Seasoning of Wood Part 16
You’re reading novel Seasoning of Wood Part 16 online at LightNovelFree.com. Please use the follow button to get notification about the latest chapter next time when you visit LightNovelFree.com. Use F11 button to read novel in full-screen(PC only). Drop by anytime you want to read free – fast – latest novel. It’s great if you could leave a comment, share your opinion about the new chapters, new novel with others on the internet. We’ll do our best to bring you the finest, latest novel everyday. Enjoy!
In the first place, it should be borne in mind that it is the heat which produces evaporation and not the air nor any mysterious property a.s.signed to a "vacuum."
For every pound of water evaporated at ordinary temperatures approximately 1,000 British thermal units of heat are used up, or "become latent," as it is called. This is true whether the evaporation takes place in a vacuum or under a moderate air pressure. If this heat is not supplied from an outside source it must be supplied by the water itself (or the material being dried), the temperature of which will consequently fall until the surrounding s.p.a.ce becomes saturated with vapor at a pressure corresponding to the temperature which the water has reached; evaporation will then cease. The pressure of the vapor in a s.p.a.ce saturated with water vapor increases rapidly with increase of temperature. At a so-called vacuum of 28 inches, which is about the limit in commercial operations, and in reality signifies an actual pressure of 2 inches of mercury column, the s.p.a.ce will be saturated with vapor at 101 degrees Fahrenheit. Consequently, no evaporation will take place in such a vacuum unless the water be warmer than 101 degrees Fahrenheit, provided there is no air leakage.
The qualification in regard to air is necessary, for the sake of exactness, for the following reason: In any given s.p.a.ce the total actual pressure is made up of the combined pressures of all the gases present. If the total pressure ("vacuum") is 2 inches, and there is no air present, it is all produced by the water vapor (which saturates the s.p.a.ce at 101 degrees Fahrenheit); but if some air is present and the total pressure is still maintained at 2 inches, then there must be less vapor present, since the air is producing part of the pressure and the s.p.a.ce is no longer saturated at the given temperature.
Consequently further evaporation may occur, with a corresponding lowering of the temperature of the water, until a balance is again reached. Without further explanation it is easy to see that but little water can be evaporated by a vacuum alone without addition of heat, and that the prevalent idea that a vacuum can of itself produce evaporation is a fallacy. If heat be supplied to the water, however, either by conduction or radiation, evaporation will take place in direct proportion to the amount of heat supplied, so long as the pressure is kept down by the vacuum pump.
At 30 inches of mercury pressure (one atmosphere) the s.p.a.ce becomes saturated with vapor and equilibrium is established at 212 degrees Fahrenheit. If heat be now supplied to the water, however, evaporation will take place in proportion to the amount of heat supplied, so long as the pressure remains that of one atmosphere, just as in the case of the vacuum. Evaporation in this condition, where the vapor pressure at the temperature of the water is equal to the gas pressure on the water, is commonly called "boiling," and the saturated vapor entirely displaces the air under continuous operation. Whenever the s.p.a.ce is not saturated with vapor, whether air is present or not, evaporation will take place, by boiling if no air be present or by diffusion under the presence of air, until an equilibrium between temperature and vapor pressure is resumed.
Relative humidity is simply the ratio of the actual vapor pressure present in a given s.p.a.ce to the vapor pressure when the s.p.a.ce is saturated with vapor at the given temperature. It matters not whether air be present or not. One hundred per cent humidity means that the s.p.a.ce contains all the vapor which it can hold at the given temperature--it is saturated. Thus at 100 per cent humidity and 212 degrees Fahrenheit the s.p.a.ce is saturated, and since the pressure of saturated vapor at this temperature is one atmosphere, no air can be present under these conditions. If, however, the total pressure at this temperature were 20 pounds (5 pounds gauge), then it would mean that there was 5 pounds air pressure present in addition to the vapor, yet the s.p.a.ce would still be saturated at the given temperature.
Again, if the temperature were 101 degrees Fahrenheit, the pressure of saturated vapor would be only 1 pound, and the additional pressure of 14 pounds, if the total pressure were atmospheric, would be made up of air. In order to have no air present and the s.p.a.ce still saturated at 101 degrees Fahrenheit, the total pressure must be reduced to 1 pound by a vacuum pump. Fifty per cent relative humidity, therefore, signifies that only half the amount of vapor required to saturate the s.p.a.ce at the given temperature is present. Thus at 212 degrees Fahrenheit temperature the vapor pressure would only be 7-1/2 pounds (vacuum of 15 inches gauge). If the total pressure were atmospheric, then the additional 7-1/2 pounds would be simply air.
"Live steam" is simply water-saturated vapor at a pressure usually above atmospheric. We may just as truly have live steam at pressures less than atmospheric, at a vacuum of 28 inches for instance. Only in the latter case its temperature would be lower, _viz._, 101 degrees Fahrenheit.
Superheated steam is nothing more than water vapor at a relative humidity less than saturation, but is usually considered at pressures above atmospheric, and in the absence of air. The atmosphere at, say, 50 per cent relative humidity really contains superheated steam or vapor, the only difference being that it is at a lower temperature and pressure than we are accustomed to think of in speaking of superheated steam, and it has air mixed with it to make up the deficiency in pressure below the atmosphere.
Two things should now be clear; that evaporation is produced by heat and that the presence or absence of air does not influence the amount of evaporation. It does, however, influence the rate of evaporation, which is r.e.t.a.r.ded by the presence of air. The main things influencing evaporation are, first, the quant.i.ty of heat supplied and, second, the relative humidity of the immediately surrounding s.p.a.ce.
Drying by Superheated Steam
What this term really signifies is simply water vapor in the absence of air in a condition of less than saturation. Kilns of this type are, properly speaking, vapor kilns, and usually operate at atmospheric pressure, but may be used at greater pressures or at less pressures.
As stated before, the vapor present in the air at any humidity less than saturation is really "superheated steam," only at a lower pressure than is ordinarily understood by this term, and mixed with air. The main argument in favor of this process seems to be based on the idea that steam is moist heat. This is true, however, only when the steam is near saturation. When it is superheated it is just as dry as air containing the same relative humidity. For instance, steam at atmospheric pressure and heated to 248 degrees Fahrenheit has a relative humidity of only 50 per cent and is just as dry as air containing the same humidity. If heated to 306 degrees Fahrenheit, its relative humidity is reduced to 20 per cent; that is to say, the ratio of its actual vapor pressure (one atmosphere) to the pressure of saturated vapor at this temperature (five atmospheres) is 1:5, or 20 per cent. Superheated vapor in the absence of air, however, parts with its heat with great rapidity and finally becomes saturated when it has lost all of its ability to cause evaporation. In this respect it is more moist than air when it comes in contact with bodies which are at a lower temperature. When saturated steam is used to heat the lumber it can raise the temperature of the latter to its own temperature, but cannot produce evaporation unless, indeed, the pressure is varied.
Only by the heat supplied above the temperature of saturation can evaporation be produced.
Impregnation Methods
Methods of partially overcoming the shrinkage by impregnation of the cell walls with organic materials closely allied to the wood substance itself are in use. In one of these which has been patented, sugar is used as the impregnating material, which is subsequently hardened or "caramelized" by heating. Experiments which the United States Forest Service has made substantiate the claims that the sugar does greatly reduce the shrinkage of the wood; but the use of impregnation processes is determined rather from a financial economic standpoint than by the physical result obtained.
Another process consists in pa.s.sing a current of electricity through the wet boards or through the green logs before sawing. It is said that the ligno cellulose and the sap are thus transformed by electrolysis, and that the wood subsequently dries more rapidly.
Preliminary Treatments
In many dry kiln operations, especially where the kilns are not designed for treatments with very moist air, the wood is allowed to air-season from several months to a year or more before running it into the dry kiln. In this way the surface dries below its fibre-saturation point and becomes hardened or "set" and the subsequent shrinkage is not so great. Moreover, there is less danger of surface checking in the kiln, since the surface has already pa.s.sed the danger point. Many woods, however, check severely in air-drying or case-harden in the air. It is thought that such woods can be satisfactorily handled in a humidity-regulated kiln direct from the saw.
Preliminary steaming is frequently used to moisten the surface if case-hardened, and to heat the lumber through to the center before drying begins. This is sometimes done in a separate chamber, but more often in a compartment of the kiln itself, part.i.tioned off by means of a curtain which can be raised or lowered as circ.u.mstances require.
This steaming is usually conducted at atmospheric pressure and frequently condensed steam is used at temperatures far below 212 degrees Fahrenheit. In a humidity-regulated kiln this preliminary treatment may be omitted, since nearly saturated conditions can be maintained and graduated as the drying progresses.
Recently the process of steaming at pressures up to 20 pounds gauge in a cylinder for short periods of time, varying from 5 to 20 minutes, is being advocated in the United States. The truck load is run into the cylinder, steamed, and then taken directly out into the air. It may subsequently be placed in the dry kiln if further drying is desired.
The self-contained heat of the wood evaporates considerable moisture, and the sudden drying of the boards causes the shrinkage to be reduced slightly in some cases. Such short periods of steaming under 20 pounds pressure do not appear to injure the wood mechanically, although they do darken the color appreciably, especially of the sapwood of the species having a light-colored sap, as black walnut (_Juglans nigra_) and red gum (_Liquidamber styraciflua_). Longer periods of steaming have been found to weaken the wood. There is a great difference in the effect on different species, however.
Soaking wood for a long time before drying has been practised, but experiments indicate that no particularly beneficial results, from the drying standpoint, are attained thereby. In fact, in some species containing sugars and allied substances it is probably detrimental from the shrinkage standpoint. If soaked in boiling water some species shrink and warp more than if dried without this treatment.
In general, it may be said that, except possibly for short-period steaming as described above, steaming and soaking hardwoods at temperatures of 212 degrees Fahrenheit or over should be avoided if possible.
It is the old saying that wood put into water shortly after it is felled, and left in water for a year or more, will be perfectly seasoned after a short subsequent exposure to the air. For this reason rivermen maintain that timber is made better by rafting. Herzenstein says: "Floating the timber down rivers helps to wash out the sap, and hence must be considered as favorable to its preservation, the more so as it enables it to absorb more preservative."
Wood which has been buried in swamps is eagerly sought after by carpenters and joiners, because it has lost all tendency to warp and twist. When first taken from the swamp the long-immersed logs are very much heavier than water, but they dry with great rapidity. A cypress log from the Mississippi Delta, which two men could barely handle at the time it was taken out some years ago, has dried out so much since then that to-day one man can lift it with ease. White cedar telegraph poles are said to remain floating in the water of the Great Lakes sometimes for several years before they are set in lines and to last better than freshly cut poles.
It is very probable that immersion for long periods in water does materially hasten subsequent seasoning. The tannins, resins, alb.u.minous materials, etc., which are deposited in the cell walls of the fibres of green wood, and which prevent rapid evaporation of the water, undergo changes when under water, probably due to the action of bacteria which live without air, and in the course of time many of these substances are leached out of the wood. The cells thereby become more and more permeable to water, and when the wood is finally brought into the air the water escapes very rapidly and very evenly.
Herzenstein's statement that wood prepared by immersion and subsequent drying will absorb more preservative, and that with greater rapidity, is certainly borne out by experience in the United States.
It is sometimes claimed that all seasoning preparatory to treatment with a substance like tar oil might be done away with by putting the green wood into a cylinder with the oil and heating to 225 degrees Fahrenheit, thus driving the water off in the form of steam, after which the tar oil would readily penetrate into the wood. This is the basis of the so-called "Curtiss process" of timber treatment. Without going into any discussion of this method of creosoting, it may be said that the same objection made for steaming holds here. In order to get a temperature of 212 degrees Fahrenheit in the center of the treated wood, the outside temperature would have to be raised so high that the strength of the wood might be seriously injured.
A company on the Pacific coast which treats red fir piling a.s.serts that it avoids this danger by leaving the green timber in the tar oil at a temperature which never exceeds 225 degrees Fahrenheit for from five to twelve hours, until there is no further evidence of water vapor coming out of the wood. The tar oil is then run out, and a vacuum is created for about an hour, after which the oil is run in again and is kept in the cylinders under 100 pounds pressure for from ten to twelve hours, until the required amount of absorption has been reached (about 12 pounds per cubic foot).
Out-of-door Seasoning
The most effective seasoning is without doubt that obtained by the uniform, slow drying which takes place in properly constructed piles outdoors, under exposure to the winds and the sun. Lumber has always been seasoned in this way, which is still the best for ordinary purposes.
It is probable for the sake of economy, air-drying will be eliminated in the drying process of the future without loss to the quality of the product, but as yet no effective method has been discovered whereby this may be accomplished, because nature performs certain functions in air-drying that cannot be duplicated by artificial means. Because of this, hardwoods, as a rule, cannot be successfully kiln-dried green or direct from the saw, and must receive a certain amount of preliminary air-drying before being placed in a dry kiln.
The present methods of air-seasoning in use have been determined by long experience, and are probably as good as they could be made for present conditions. But the same care has not up to this time been given to the seasoning of such timber as ties, bridge material, posts, telegraph and telephone poles, etc. These have sometimes been piled more or less intelligently, but in the majority of cases their value has been too low to make it seem worth while to pile with reference to anything beyond convenience in handling.
In piling material for air-seasoning, one should utilize high, dry ground when possible, and see that the foundations are high enough off the ground, so that there is proper air circulation through the bottom of the piles, and also that the piles are far enough apart so that the air may circulate freely through and around them.
It is air circulation that is desired in all cases of drying, both in dry kilns and out-of-doors, and not suns.h.i.+ne; that is, not the sun s.h.i.+ning directly upon the material. The ends also should be protected from the sun, and everything possible done to induce a free circulation of air, and to keep the foundations free from all plant growth.
Naturally, the heavier the material to be dried, the more difficulty is experienced from checking, which has its most active time in the spring when the sap is rising. In fact the main period of danger in material checking comes with the March winds and the April showers, and not infrequently in the South it occurs earlier than that. In other words, as soon as the sap begins to rise, the timber shows signs of checking, and that is the time to take extra precautions by careful piling and protection from the sun. When the hot days of summer arrive the tendency to check is not so bad, but stock will sour from the heat, stain from the sap, mildew from moisture, and fall a prey to wood-destroying insects.
It has been proven in a general way that wood will season more slowly in winter than in summer, and also that the water content during various months varies. In the spring the drying-out of wood cut in October and November will take place more rapidly.
SECTION XI
KILN-DRYING OF WOOD
Advantages of Kiln-drying over Air-drying
Some of the advantages of kiln-drying to be secured over air-drying in addition to reducing the s.h.i.+pping weight and lessening quant.i.ty of stock are the following:
1. Less material lost.
2. Better quality of product.
3. Prevention of sap stain and mould.
4. Fixation of gums and resins.
5. Reduction of hygroscopicity.
This reduction in the tendency to take up moisture means a reduction in the "working" of the material which, even though slight, is of importance.
The problem of drying wood in the best manner divides itself into two distinct parts, one of which is entirely concerned with the behavior of the wood itself and the physical phenomena involved, while the other part has to do with the control of the drying process.
Physical Conditions governing the Drying of Wood
Seasoning of Wood Part 16
You're reading novel Seasoning of Wood Part 16 online at LightNovelFree.com. You can use the follow function to bookmark your favorite novel ( Only for registered users ). If you find any errors ( broken links, can't load photos, etc.. ), Please let us know so we can fix it as soon as possible. And when you start a conversation or debate about a certain topic with other people, please do not offend them just because you don't like their opinions.
Seasoning of Wood Part 16 summary
You're reading Seasoning of Wood Part 16. This novel has been translated by Updating. Author: Joseph B. Wagner already has 585 views.
It's great if you read and follow any novel on our website. We promise you that we'll bring you the latest, hottest novel everyday and FREE.
LightNovelFree.com is a most smartest website for reading novel online, it can automatic resize images to fit your pc screen, even on your mobile. Experience now by using your smartphone and access to LightNovelFree.com
- Related chapter:
- Seasoning of Wood Part 15
- Seasoning of Wood Part 17
RECENTLY UPDATED NOVEL

Rebirth of the Nameless Immortal God
Rebirth of the Nameless Immortal God Chapter 2261 Diligently View : 301,769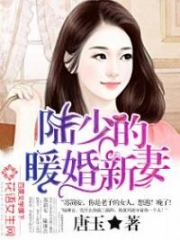
A Warm Wedding and A New Bride of Young Master Lu
A Warm Wedding and A New Bride of Young Master Lu Chapter 1295 View : 2,165,983
He Is Warmer Than Time
He Is Warmer Than Time Chapter 1965: Chapter 2025 -the answer is obvious View : 215,959
Master Pei's Wife is a Devil Concubine
Master Pei's Wife is a Devil Concubine Chapter 989: Su Ji Seizes the Underground Market! View : 216,765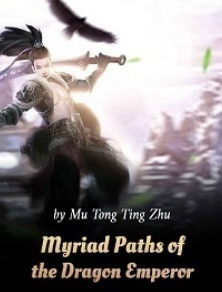
Myriad Paths of the Dragon Emperor
Myriad Paths of the Dragon Emperor Chapter 2313: The challenge begins View : 781,061
Following a Hundred Years of Cultivation, I'm dying Before I Got Cheats
Following a Hundred Years of Cultivation, I'm dying Before I Got Cheats Chapter 590: The State of the Eastern End's Cultivation View : 110,795
After Her Divorce, She Escaped With A Strong Man To Farm
After Her Divorce, She Escaped With A Strong Man To Farm Chapter 684: Hundred Flower Garden View : 141,631
I Woke My Vegetative Husband up at Our Wedding Night!
I Woke My Vegetative Husband up at Our Wedding Night! Chapter 1035: Are You Going to Harm Qian Qian Like This? View : 269,906