Steam Engines Part 3
You’re reading novel Steam Engines Part 3 online at LightNovelFree.com. Please use the follow button to get notification about the latest chapter next time when you visit LightNovelFree.com. Use F11 button to read novel in full-screen(PC only). Drop by anytime you want to read free – fast – latest novel. It’s great if you could leave a comment, share your opinion about the new chapters, new novel with others on the internet. We’ll do our best to bring you the finest, latest novel everyday. Enjoy!
[Ill.u.s.tration: Figs. 23 to 26. Action of Corliss Valve Gear]
The action of the steam or admission valves is best explained by reference to Figs. 23 to 26. Referring to Fig. 23, _A_ is a bell-crank which turns loosely upon the valve stem _V_. The lower left-hand extension of _A_ carries the grab hook _H_, while the upper extension is connected with the wrist-plate as indicated. Ordinarily the hook _H_ is pressed inward by the spring _S_, so that the longer arm of the hook is always pressed against the knock-off cam _C_. The cam _C_ also turns upon the valve stem _V_ and is connected with the governor by means of a reach rod as indicated in Fig. 23 and shown in Fig. 22. The drop lever _B_ is keyed to the valve stem _V_, and is connected with the dash pot by a rod as indicated by the dotted line. This is also shown in Fig. 22.
The end of the drop lever carries a steel block (shown shaded in Fig.
23), which engages with the grab hook _H_.
When in operation, the bell-crank is rotated in the direction of the arrow by the action of the wrist-plate and connecting-rod. As the bell-crank rotates, the grab hook engages the steel block at the end of the drop lever _B_ and lifts it, thus causing the valve to open, and to remain so until the bell-crank has advanced so far that the longer arm of the grab hook _H_ is pressed outward by the projection on the knock-off cam, as shown in Fig. 24. The drop lever now being released, the valve is quickly closed by the suction of the dash pot, which pulls the lever down to its original position by means of the rod previously mentioned.
[Ill.u.s.tration: Fig. 27. Governor for Corliss Engine]
The governor operates by changing the point of cut-off through the action of the cam _C_. With the cam in the position shown in Fig. 25, cut-off occurs earlier than in Fig. 24. Should the cam be turned in the opposite direction (clockwise), cut-off would take place later. A detailed view of the complete valve mechanism described is shown a.s.sembled in Fig. 26, with each part properly named. A detail of the governor is shown in Fig. 27. An increase in speed causes the revolving b.a.l.l.s _BB_ to swing outward, thus raising the weight _W_ and the sleeve _S_. This in turn operates the lever _L_ through rod _R_ and a bell-crank attachment, as shown in the right-hand view. An upward and downward movement of the b.a.l.l.s, due to a change in speed of the engine, swings the lever _L_ backward and forward as shown by the full and dotted lines. The ends of this lever are attached by means of reach-rods to the knock-off cams, this being shown more clearly in Fig. 22. The connections between the lever _L_ and cam _C_ are such that a raising of the b.a.l.l.s, due to increased speed, will reduce the cut-off and thus slow down the engine. On the other hand, a falling of the b.a.l.l.s will lengthen the cut-off through the same mechanism.
[Ill.u.s.tration: Fig. 28. Dash-pot for Corliss Engine]
[Ill.u.s.tration: Figs. 29 and 30. Plan and Longitudinal Section of Adjustable Piston]
Mention has already been made of the dash pot which is used to close the valve suddenly after being released from the grab hook. The dash-pot rod is shown in Fig. 26, and indicated by dotted lines in Figs. 23 to 25. A detailed view of one form of dash pot is shown in Fig. 28. When the valve is opened, the rod attached to lever _B_, Figs. 23 and 24, raises the piston _P_, Fig. 28, and a partial vacuum is formed beneath it which draws the piston and connecting rod down by suction as soon as the lever _B_ is released, and thus closes the valve suddenly and without shock.
The strength of the suction and the air cus.h.i.+on for this piston are regulated by the inlet and outlet valves shown on the sides of the dash pot.
Engine Details
Figs. 29 to 37 show various engine details, and ill.u.s.trate in a simple way some of the more important principles involved in steam engine design.
[Ill.u.s.tration: Fig. 31. A Typical Cross-head]
[Ill.u.s.tration: Figs. 32 and 33. Methods Commonly Used for Taking Up Wear in a Connecting-rod]
A partial cross-section of an adjustable piston is shown in Fig. 29, and a longitudinal section of the same piston in Fig. 30. The princ.i.p.al feature to be emphasized is the method of automatic expansion employed to take up any wear and keep the piston tight. In setting up the piston a hand adjustment is made of the outer sleeve or ring _R_ by means of the set-screws _AA_. Ring _R_ is made in several sections, so that it may be expanded in the form of a true circle. Further tightness is secured without undue friction by means of the packing ring _P_ which fits in a groove in _R_ and is forced lightly against the walls of the cylinder by a number of coil springs, one of which is shown at _S_. As the cylinder and piston become worn, screws _A_ are adjusted from time to time, and the fine adjustment for tightness is cared for by the packing ring _P_ and the coil springs _S_.
The points to be brought out in connection with the cross-head are the methods of alignment and adjustment. A typical cross-head is shown in cross and longitudinal sections in Fig. 31. Alignment in a straight line, longitudinally, is secured by the cylindrical form of the bearing surfaces or shoes, shown at _S_. These are sometimes made V-shaped in order to secure the same result. The wear on a cross-head comes on the surfaces _S_, and is taken up by the use of screw wedges _W_, shown in the longitudinal section. As the sliding surfaces become worn, the wedges are forced in slightly by s.c.r.e.w.i.n.g in the set-screws and clamping them in place by means of the check-nuts.
[Ill.u.s.tration: Fig. 34. Outboard Bearing for Corliss Type Engine]
[Ill.u.s.tration: Fig. 35. Inner Bearing and Bed of Corliss Engine]
The method commonly employed in taking up the wear in a connecting-rod is shown in Figs. 32 and 33. The wear at the wrist-pin is taken by the so called bra.s.ses, shown at _B_ in the ill.u.s.trations. The inner bra.s.s, in both cases, fits in a suitable groove, and is held stationary when once in place. The outer bra.s.s is adjustable, being forced toward the wrist-pin by a sliding wedge which is operated by one or more set-screws. In Fig. 32 the wedge is held in a vertical position, and is adjusted by two screws as shown. The arrangement made use of in Fig. 33 has the wedge pa.s.sing through the rod in a horizontal position, and adjusted by means of a single screw, as shown in the lower view. With the arrangements shown, tightening up the bra.s.ses shortens the length of the rod. In practice the wedges at each end of the rod are so placed that tightening one shortens the rod, and tightening the other lengthens it, the total effect being to keep the connecting-rod at its original length.
A common form of outboard bearing for an engine of the slow-speed or Corliss type is ill.u.s.trated in Fig. 34. The various adjustments for alignment and for taking up wear are the important points considered in this case. The plate _B_ is fastened to the stone foundation by anchor bolts not shown. Sidewise movement is secured by loosening the bolts _C_, which pa.s.s through slots in the bearing, and adjusting by means of the screws _S_. Vertical adjustment is obtained by use of the wedge _W_, which is forced in by the screw _A_, as required. The inner bearing and bed piece of a heavy duty Corliss engine is shown in Fig. 35. The bearing in this case is made up of four sections, so arranged that either horizontal or vertical adjustment may be secured by the use of adjusting screws and check-nuts.
Engines of the slide-valve type are usually provided either with a fly-ball throttling governor, or a shaft governor. A common form of throttling governor is shown in Fig. 36. As the speed increases the b.a.l.l.s _W_ are thrown outward by the action of the centrifugal force, and being attached to arms hinged above them, any outward movement causes them to rise. This operates the spindle _S_, which, in turn, partially closes the balanced valve in body _B_, thus cutting down the steam supply delivered to the engine. The action of a throttling governor upon the work diagram of an engine is shown in Fig. 38. Let the full line represent the form of the diagram with the engine working at full load.
Now, if a part of the load be thrown off, the engine will speed up slightly, causing the governor to act as described, thus bringing the admission and expansion lines into the lower positions, as shown in dotted lines.
[Ill.u.s.tration: Fig. 36. Common Form of Throttling Governor]
The shaft governor is used almost universally on high-speed engines, and is shown in one form in Fig. 37. It consists, in this case, of two weights _W_, hinged to the spokes of the wheel near the circ.u.mference by means of suitable arms. Attached to the arms, as shown, are coil springs _C_. The ends of the arms beyond the weights are connected by means of levers _L_ to the eccentric disk. When the engine speeds up, the weights tend to swing outward toward the rim of the wheel, the amount of the movement being regulated by the tension of the springs _C_. As the arms move outward, the levers at the ends turn the eccentric disk on the shaft, the effect of which is to change the angle of advance and shorten the cut-off. When the speed falls below the normal, the weights move toward the center and the cut-off is lengthened. The effect of this form of governor on the diagram is shown in Fig. 39. The full line represents the diagram at full load, and the dotted line when the engine is under-loaded.
[Ill.u.s.tration: Fig. 37. Shaft Governor for High-speed Engine]
CHAPTER IV
STEAM ENGINE ECONOMY
Under the general heading of steam engine economy, such items as cylinder condensation, steam consumption, efficiency, ratio of expansion, under- and over-loading, condensing, etc., are treated.
The princ.i.p.al waste of steam in the operation of an engine is due to condensation during the first part of the stroke. This condensation is due to the fact that during expansion and exhaust the cylinder walls and head and the piston are in contact with comparatively cool steam, and, therefore, give up a considerable amount of heat. When fresh steam is admitted at a high temperature, it immediately gives up sufficient heat to raise the cylinder walls to a temperature approximating that of the entering steam. This results in the condensation of a certain amount of steam, the quant.i.ty depending upon the time allowed for the transfer of heat, the area of exposed surface, and the temperature of the cylinder walls. During the period of expansion the temperature falls rapidly, and the steam being wet, absorbs a large amount of heat. After the exhaust valve opens, the drop in pressure allows the moisture that has collected on the cylinder walls to evaporate into steam, so that during the exhaust period but little heat is transferred. With the admission of fresh steam at boiler pressure, a mist is condensed on the cylinder walls, which greatly increases the rapidity with which heat is absorbed.
The amount of heat lost through cylinder condensation is best shown by a practical ill.u.s.tration. One horsepower is equal to 33,000 foot-pounds of work per minute, or 33,000 60 = 1,980,000 foot-pounds per hour. This is equivalent to 1,980,000 778 = 2,550 heat units. The latent heat of steam at 90 pounds gage pressure is 881 heat units. Hence, 2,250 881 = 2.9 pounds of steam at 90 pounds pressure is required per horsepower, provided there is no loss of steam, and all of the contained heat is changed into useful work. As a matter of fact, from 30 to 35 pounds of steam are required in the average simple non-condensing high-speed engine.
There are three remedies which are used to reduce the amount of cylinder condensation. The first to be used was called steam jacketing, and consisted in surrounding the cylinder with a layer of high-pressure steam, the idea being to keep the inner walls up to a temperature nearly equal to that of the incoming steam. This arrangement is but little used at the present time, owing both to the expense of operation and to its ineffectiveness as compared with other methods.
The second remedy is the use of superheated steam. It has been stated that the transfer of heat takes place much more rapidly when the interior surfaces are covered with a coating of moisture or mist.
Superheated steam has a temperature considerably above the point of saturation at the given pressure; hence, it is possible to cool it a certain amount before condensation begins. This has the effect of reducing the transfer of heat for a short period following admission, and this is the time that condensation takes place most rapidly under ordinary conditions with saturated steam. This, in fact, is the princ.i.p.al advantage derived from the use of superheated steam, although it is also lighter for a given volume, and therefore, a less weight of steam is required, to fill the cylinder up to the point of cut-off. The economical degree of superheating is considered to be that which will prevent the condensation of any steam on the walls of the cylinder up to the point of cut-off, thus keeping them at all times free from moisture.
The objections to superheated steam are its cutting effect in the pa.s.sages through which it flows, and the difficulty experienced in lubricating the valves and cylinder at such a high temperature. The third and most effective remedy for condensation losses is that known as compounding, which will be treated under a separate heading in the following.
Multiple Expansion Engines
It has been explained that cylinder condensation is due princ.i.p.ally to the change in temperature of the interior surfaces of the cylinder, caused by the variation in temperature of the steam at initial and exhaust pressures. Therefore, if the temperature range be divided between two cylinders which are operated in series, the steam condensed in the first or high pressure cylinder will be re-evaporated and pa.s.sed into the low-pressure cylinder as steam, where it will again be condensed and re-evaporated as it pa.s.ses into the exhaust pipe.
Theoretically, this should reduce the condensation loss by one-half, and if three cylinders are used, the loss should be only one-third of that in a simple engine. In actual practice the saving is not as great as this, but with the proper relation between the cylinders, these results are approximated.
Engines in which expansion takes place in two stages are called compound engines. When three stages are employed, they are called triple expansion engines. Compounding adds to the first cost of an engine, and also to the friction, so that in determining the most economical number of cylinders to employ, the actual relation between the condensation loss and the increased cost of the engine and the friction loss, must be considered. In the case of power plant work, it is now the practice to use compound engines for the large sizes, while triple expansion engines are more commonly employed in pumping stations. Many designs of multiple expansion engines are provided with chambers between the cylinders, called receivers. In engines of this type the exhaust is frequently reheated in the receivers by means of bra.s.s coils containing live steam.
In the case of a cross-compound engine, a receiver is always used. In the tandem design it is often omitted, the piping between the two cylinders being made to answer the purpose.
The ratio of cylinder volumes in compound engines varies with different makers. The usual practice is to make the volume of the low-pressure cylinder from 2.5 to 3 times that of the high-pressure. The total ratio of expansion in a multiple expansion engine is the product of the ratios in each cylinder. For example, if the ratio of expansion is 4 in each cylinder in a compound engine, the total ratio will be 4 4 = 16. The effect of a triple-expansion engine is sometimes obtained in a measure by making the volume of the low-pressure cylinder of a compound engine 6 or 7 times that of the high-pressure. This arrangement produces a considerable drop in pressure at the end of the high-pressure stroke, with the result of throwing a considerable increase of work on the high-pressure cylinder without increasing its ratio of expansion, and at the same time securing a large total ratio of expansion in the engine.
In the case of vertical engines, the low-pressure cylinder is sometimes divided into two parts in order to reduce the size of cylinder and piston. In this arrangement a receiver of larger size than usual is employed, and the low-pressure cranks are often set at an angle with each other.
Another advantage gained by compounding is the possibility to expand the steam to a greater extent than can be done in a single cylinder engine, thus utilizing, as useful work, a greater proportion of the heat contained in the steam. This also makes it possible to employ higher initial pressures, in which there is a still further saving, because of the comparatively small amount of fuel required to raise the pressure from that of the common practice of 80 or 90 pounds for simple engines, to 120 to 140 pounds, which is entirely practical in the case of compound engines. With triple expansion, initial pressures of 180 pounds or more may be used to advantage. The gain from compounding may amount to about 15 per cent over simple condensing engines, taking steam at the same initial pressure. When compound condensing engines are compared with simple non-condensing engines, the gain in economy may run from 30 to 40 per cent.
TABLE IV. STEAM CONSUMPTION OF ENGINES
+-------------------------+--------------------------------+ Pounds of Steam per Indicated Horsepower per Hour Kind of Engine +----------------+---------------+ Non-condensing Condensing +-------------------------+----------------+---------------+ { High-speed 32 24 Simple { Medium-speed 30 23 { Corliss 28 22 { High-speed 26 20 Compound { Medium-speed 25 19 { Corliss 24 18 +-------------------------+----------------+---------------+
Steam Consumption and Ratio of Expansion
The steam consumption is commonly called the _water rate_, and is expressed in pounds of dry steam required per indicated horsepower per hour. This quant.i.ty varies widely in different types of engines, and also in engines of the same kind working under different conditions. The water rate depends upon the "cylinder losses," which are due princ.i.p.ally to condensation, although the effects of clearance, radiation from cylinder and steam chest, and leakage around valves and piston, form a part of the total loss. Table IV gives the average water rate of different types of engines working at full load.
The most economical ratio of expansion depends largely upon the type of the engine. In the case of simple engines, the ratio is limited to 4 or 5 on account of excessive cylinder condensation in case of larger ratios. This limits the initial pressure to an average of about 90 pounds for engines of this type. In the case of compound engines, a ratio of from 8 to 10 is commonly employed to advantage, while with triple-expansion engines, ratios of 12 to 15 are found to give good results.
[Ill.u.s.tration: Fig. 38. Action of Throttling Governor on Indicator Diagram]
[Ill.u.s.tration: Fig. 39. Effect of Shaft Governor on Indicator Diagram]
[Ill.u.s.tration: Fig. 40. Increasing Power of Engine by Condensing]
Steam Engines Part 3
You're reading novel Steam Engines Part 3 online at LightNovelFree.com. You can use the follow function to bookmark your favorite novel ( Only for registered users ). If you find any errors ( broken links, can't load photos, etc.. ), Please let us know so we can fix it as soon as possible. And when you start a conversation or debate about a certain topic with other people, please do not offend them just because you don't like their opinions.
Steam Engines Part 3 summary
You're reading Steam Engines Part 3. This novel has been translated by Updating. Author: Anonymous already has 672 views.
It's great if you read and follow any novel on our website. We promise you that we'll bring you the latest, hottest novel everyday and FREE.
LightNovelFree.com is a most smartest website for reading novel online, it can automatic resize images to fit your pc screen, even on your mobile. Experience now by using your smartphone and access to LightNovelFree.com
- Related chapter:
- Steam Engines Part 2
- Steam Engines Part 4
RECENTLY UPDATED NOVEL

Epic Of Ice Dragon: Reborn As An Ice Dragon With A System
Epic Of Ice Dragon: Reborn As An Ice Dragon With A System Chapter 1946: Unexpected Outcome! View : 569,354
The Strongest War God
The Strongest War God Chapter 1340: Braydon Pretends to be the Little Fool View : 498,157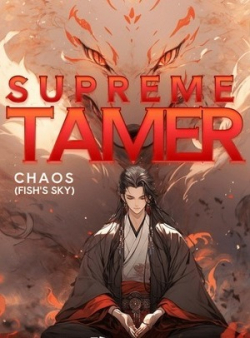
Supreme Tamer
Supreme Tamer Chapter 716: Chapter 586: Wanxiang City, Location of the Defecting Girl View : 297,920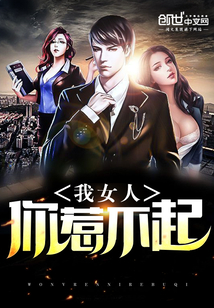