The Grantville Gazette - Volume 6 Part 21
You’re reading novel The Grantville Gazette - Volume 6 Part 21 online at LightNovelFree.com. Please use the follow button to get notification about the latest chapter next time when you visit LightNovelFree.com. Use F11 button to read novel in full-screen(PC only). Drop by anytime you want to read free – fast – latest novel. It’s great if you could leave a comment, share your opinion about the new chapters, new novel with others on the internet. We’ll do our best to bring you the finest, latest novel everyday. Enjoy!
The 1911 Encyclopedia Britannica is at http://1911encyclopedia.org/ The story of the @ symbol is at http://www.atsymbol.com/history.htm
A good place for looking up the origin of phrases is "The Phrase Finder"- http://www.phrases.org.uk/
The Koran virgins controversy-http://www.iht.com/articles/532570.html
Bouncing Back: Bringing Rubber to Grantville
by Iver P. Cooper
Chemistry Professor Joe Schwarcz writes, "It's hard to fight an effective war without rubber.
Fan belts, gaskets, gas masks, and tires are critical to the war effort." While he had modern warfare in mind, Grantville's war machines-modified cars and trucks-need rubber to remain functional. In 1633, Quentin Underwood insisted that "developing a rubber industry should be a top priority."
Rubber has myriad useful properties. Its most unique feature is elasticity, which allows it to be used as a shock absorber. Because of its toughness, articles made of rubber have good abrasion resistance. Rubber is also impermeable to gases and liquids. Finally, it is an electrical insulator. Rubber is used in hundreds of automobile parts; the apt slogan of the B.F. Goodrich Company was, "Everything in Rubber."
In the old timeline, synthetic rubber accounted for about 60% of all rubber consumed.
Synthetic rubber is not an option within, say, a decade or two of the Ring of Fire. Even though we know, from the encyclopedias, that the secret is to co-polymerize butadiene and styrene (or acrylonitrile), where exactly are the butadiene and styrene coming from? Well, we can make butadiene from alcohol, or from petroleum ingredients like butane or butylene. To make styrene, we need ethyl benzene.
Schwarcz comments that the process which the Germans used to make Buna-S rubber (the butadiene-styrene copolymer) "was not a simple business." You need the right catalyst, the right emulsifier, and so on. This detailed process information probably isn't in the Grantville library system.
Even if we knew exactly what to do, to handle the chemicals, we need steel and gla.s.s, both of which are going to be expensive to make. And for the raw materials, we have to appropriately process coal or petroleum. All in all, the obstacles are numerous and formidable. Once they are surmounted, the synthetic rubber industry will still have to compete with other industries for key materials (coal tar, petroleum, etc.) and skilled workers.
Prospective Natural Rubber Sources Our immediate source of rubber will be sc.r.a.p (see "Rubber Reclaiming," below). However, even with reclaiming, we will eventually run out of rubber. So we need to find natural rubber, and quickly.
Natural rubber is found in latex, a sticky liquid exuded from wounds by certain plants. It is not sap, although non-botanists may confuse the two. There are several encyclopedias available in Grantville, and from them, one can compile a seemingly impressive list (see Appendix 1) of possible rubber sources. However, we need to know where to look and what kind of plant to look for. The best prospects fall into three categories: (1) New World Tropical Rubber Plants: the Para Rubber Tree/Hevea brasiliensis (Amazon and Guianas), the Ceara Rubber Tree/Manihot glaziovii (northeast Brazil), and the Castilla Rubber Tree/Castilla elastica (Mexico to Peru).
(2) Old World Tropical Rubber Plants: the Lagos Rubber Tree/Funtumia elastica (West Africa), the a.s.sam Rubber Tree/Ficus elastica (Asia), and various rubber vines (Africa and Asia).
(3) Temperate Latex-Producing Plants included in the Ring of Fire or commonplace in Europe: milkweed and goldenrod in particular.
For each of those rubber sources, we have both a written description, and some kind of useful ill.u.s.tration (its overall form, its leaves, its flowers (if any), its seeds, and so forth).
There are also some borderline prospects: the Pernambuco Rubber Tree/Hancornia speciosa, Guayule/Parthenium argentatum and Russian dandelion/Taraxac.u.m kok-saghyz, which are of interest mainly because they can be grown outside a tropical rainforest. In the case of Hancornia and Guayule, the encyclopedias offer only a written description, but there are ill.u.s.trations and a range map for Guayule in a 1981 National Geographic article. For Russian dandelion, there is just the prayer (which will be answered) that it resembles the common dandelion.
Knowing Where to Search The 1911 Encyclopedia Britannica and the Encyclopedia Americana name where wild rubber occurs, by country (e.g., Mexico) or even just by region (e.g., Africa). Obviously, it is more useful to know that it occurs in a small country like Liberia than in a large country like Brazil.
Collier's Encyclopedia and the World Book Encyclopedia have maps showing more specifically where wild rubber and plantation rubber are found. There is also useful information in the economic maps of the Hammond Citation Atlas. However, these maps must be used with caution.
First of all, they show the current range of the rubber trees. The wild rubber may be available, in 1632, from a wider area, and the plantation rubber may be cultivatable in locations other than those shown on the map.
Secondly, they don't distinguish one kind of wild rubber from another, and the ranges do overlap. A given site in the marked region in Africa could be native to the tree Funtumia elastica, or to one or more of the many rubber vines which Africa possesses. Likewise, Castilla elastica and Hevea guianensis are both found in northern South America. So what this means is that 1632 characters should keep an open mind when they look for latex-producing plants.
In any event, knowing where to search is not enough. You have to be able to carry out the search successfully. This has two components: being able to identify the rubber plant (see next section), and being able to survive the journey (see "The Geopolitics of Foreign Rubber," below).
The latter section also provides more detailed information on where the plants can be found or cultivated.
Identifying the Rubber Plant Once we are in the right area, we can hire native guides, show them pictures (and latex or rubber samples), and ask them to guide us to where the trees are located. Or we can stumble around the rainforests ourselves, if we are nervous about the native att.i.tude to European visitors.
Appendix 1 lists the descriptive information that is available for each of the known rubber sources. I am not going to quote the actual text, since it is readily available in libraries or on the internet.
However, I think it fair to warn you that the plant life of the rainforest is very diverse, and it is possible to be deceived by a closely related species that is a poor producer. For example, in Brazil, the leading rubber tree, Hevea brasiliensis, may be confused with Hevea spruceana (just to complicate matters further, there are interspecies crosses in the coastal regions), and in West Africa, those seeking Funtumia elastica may be misled into tapping Funtumia africana (the False Rubber Tree).(Polhamus, 36, 65; Christy, 78-9) * * *
The Aztecs of Mexico and the Maya of the Yucatan and Central America used Castilla rubber for footgear, headgear, game b.a.l.l.s, and incense (s.h.i.+drowitz, 2-5, 372-3). Because the rubber of this tree was used and even traded by the indios of Latin America, we don't actually need to be able to describe the tree in order to locate it. Chances are that if our agents go to the local markets in the correct general area, the Indians will know something about it.
Another special case is presented by the Indian Rubber Tree, Ficus elastica. This is one plant we don't have to journey far to find; it is a popular house plant, and I would be astounded if there were no specimens in Grantville.
The story of how Francois Fresnau found the Hevea brasiliensis tree in French Guiana is an interesting one, because the techniques he used could be adapted to finding any rubber tree whose latex production is already known to the natives. Fresnau was quite fortunate to succeed-albeit after a fourteen year search-because H. brasiliensis is rare in Guiana. (There is another rubber tree that is more common there, called Hevea guianensis, which was identified in 1764).
Although he was a military engineer, a.s.signed to the fort of Cayenne, he had been asked to keep his eyes open for exotic plants that might be of interest to the Royal Gardens. Fresnau was especially anxious to find Guianese specimens of the elastic resin-producing Syringe Tree of Portuguese Brazil. However, the natives he bribed with "gewgaws" and gin all told him, "Nimati"
("I don't know").
Then, by chance, Fresnau returned from a fis.h.i.+ng trip on a boat crewed by Naurague Indians from Mayacare in Brazil. He showed them rubber articles, and they immediately realized which tree Fresnau was seeking. Because of his commitments, Fresnau could not travel to Mayacare, but he was resourceful enough to persuade them to make him clay models of the fruit and leaves of the Syringe Tree. He paid the Naurague for their troubles with liquor, salt and other presents.
Fresnau showed the clay models to native hunters and French colonial officials in various parts of Guiana and was told that the trees he sought were to be found on the banks of the Matarani River. He brought his Naurague Indians to the site, and they confirmed that the trees were of the correct species. (Schidrowitz, 14-22)
Rubber Collection Technology There are two basic techniques of gathering rubber. First of all, we can make a small wound in the bark of the tree, and collect the latex that flows out, without killing off the tree. This is called tapping.
Secondly, we can cut down the rubber tree, or chop up the rubber shrub, vine or weed, and extract all of its rubber content. This may result in a large, quick return, but it is obviously wasteful (especially if the rubber source is a tree with a long maturation period).
Appendix 2 lists the standard collection technologies for each of the rubber sources that were singled out previously as hot prospects, as well as for a few borderline cases. It also gives the expected productivity on a per tree and per acre basis. If land is cheap, and labor expensive, then it may be more important to determine the productivity per tapper.
Rubber Tapping At least 95% of all of the rubber produced today comes from the latex tubes of the Para Rubber Tree, Hevea brasiliensis. There is good reason for this. Latex can be repeatedly extracted from Hevea without killing the tree, the latex has a high rubber content, and the rubber itself is of excellent quality. A single tap produces only 56 grams of latex, but the tree can endure 150 tappings in a single year (EA).
The original method of gathering Hevea latex was both inefficient and destructive. The tree was nicked repeatedly, and latex bled from the injured areas (Dean, 10). EA says that the tapping that "inevitably resulted had led to the death" of the tapped tree.
Thanks to the work of Henry Ridley in Malaya in 1890-1910, it was recognized that it was better, from the point of view of long-term productivity, to make a single cut, position a cup underneath, and return later to collect the latex. It was also desirable to allow the tree to "rest"
periodically. Finally, the cuts must be made with care to avoid the cambium layer. If the latter is penetrated, the trees will toughen their trunks, which will make further tapping more onerous.
If we want our collectors to follow these improved practices-which are described and ill.u.s.trated in several of the encyclopedias-we will have to go with them to the trees and show them the proper technique. Moreover, if we want to make sure that they adhere to our instructions, we will have to make inspections from time to time.
In 1911, when the Encyclopedia Britannica, 11th ed. (EB11) was published, several different Para Rubber tapping methods were in use, and it was not yet known which would prove to be the best. The oldest was the V-system, in which V's were cut on the base of the tree, and a collection cup placed at the vertex of each. The width of each V was not more than one-quarter of the circ.u.mference of the tree. The V-system can be seen on two of the trees in the photo of Fig. 12.
The V-system had already been largely replaced by the herringbone system, which is depicted in Fig. 2. In essence, there is a central collection channel which leads down to a single collection cup. This main channel is fed by alternating tributaries, diagonals cut at a 45 degree angle.
The third method mentioned in the EB11 is the spiral system, which was then considered to be experimental. It involves making a series of spiral cuts, but the text does not elaborate on where the cuts start and end, how wide they are, how far apart they are s.p.a.ced, and so forth. We can only judge this from the end result, which can be seen on three of the trees in the photo of Fig. 12. This shows spiral bands of cut bark, separated from each other by an unmarred region which is perhaps one-half to one-third the width of the cut bands. If I understand the system correctly, the cuts will ultimately be extended into this region, too, until the entire lower trunk has been sliced.
The cuts were, whichever the system used, made by means of "small knives and p.r.i.c.kers,"
rather than machetes. In other words, by 1911 it was already recognized that the cuts should be no deeper than the latex-bearing layer.
The modern Hevea tapping method is a derivative of the spiral system; there is a diagram in the World Book Encyclopedia (WBE). The tapping of a virgin trunk begins with a single diagonal cut, starting four feet above the ground. It is angled downward, at what looks like a 30 degree angle (this is confirmed by the modern EB), and reaches halfway around the trunk. For the next tap, a parallel groove is cut just below the one before it. As this process continues, a "tapping panel," a diagonal band of scored bark, is created. (The cup is hung at the base of the fresh cut.) After three or four years, the tapping panel reaches the ground, and a new panel is started on the other side of the trunk. By the time this panel is completed, the originally tapped side has healed.
For photos of tapping panels, see the modern EB and Collier's Encyclopedia (CE).
According to CE, the tapping should begin early in the morning. The WBE mentions that some plantations tap a tree every other day ("1T1R"), while others tap it for 15 consecutive days and then let the tree rest for 15 consecutive days ("15T15R"). CE says that the 15T15R method produces provides much greater amounts of latex than the other.
The Encyclopedia Americana (EA) entry provides more information about the cut itself. It is one twenty-fifth of an inch wide, and only one-quarter to one-half inch deep. However, EA suggests a cut that is only one-third, not one-half, the circ.u.mference of the trunk; hence, this approach contemplates carving three successive tapping panels into the trunk. In addition, the tapping panels contemplated by EA are only six inches high. (One tapping panel is thus the result of 150 tapping cuts, which presumably occurred over 300 calendar days.) * * *
The only encyclopedia to provide any information concerning the standard methods of tapping the other rubber trees is EB11, and it must be remembered that the methods it advocates may not be optimal. For collecting the Castilla elastica latex, the EB11 recommends a simple spiral cut at a 45 degree angle. The Funtumia elastica latex was collected using the "herringbone"
system. Pernambuco or Mangabeira Rubber (Hancornia speciosa) was obtained by making eight shallow, oblique cuts around the trunk, then allowing the latex to drip into cups.
The problem with the Ceara rubber tree (Manihot glaziovii) is that the latex flows very slowly. Hence, the latex allowed to coagulate on the tree, and the coagulate is then pulled off in strings. Some of the latex will drip down, and large leaves are laid down in advance to collect it.
(EB11).
Tapping methods will affect labor efficiency. For Hevea, just one cut is made per tree per day; a plantation worker can tap 250-400 trees in a day. In contrast, a Castilla must be hacked repeatedly, because the latex-bearing cells are not connected; as a result, the same worker could tap only 20 or 50 Castilla trees daily. (Polhamus 264; Treadwell, 32)
Rubber Harvesting In some cases, the latex cannot be tapped; the plant must be harvested and the latex recovered from the dead plant material.
If the plant can produce a rubber crop every year, then the main objection to this procedure is the labor cost involved in harvesting. The harvesting of milkweed and goldenrod are discussed below, in their own sections, while guayule and Russian dandelion are relegated to Appendices.
Latex is produced by several different African (and Asian) species of vines. To extract the rubber, the vine must be cut down, and unfortunately, when the price of rubber was high, this encouraged over-exploitation. The EB11 notes that the southern Sudan was "nearly entirely denuded." In consequence, the authorities in the French Sudan, the Congo, and in German Africa adopted regulations which limited when and how the vines could be tapped, and also required replanting. As the EB11 notes, these edicts can only be enforced "at considerable expense."
Library research in Grantville will reveal some information on how to extract the guayule rubber. EA says that 3- to 5- year old shrubs are shredded. The recommended collecting technique is to mow off just the top, so that the same plant can be harvested repeatedly. The latex is leached out of the plant material with hot water.
CE, on the other hand, says that the rubber is found in all parts except the leaves. It suggests that the collected plant material be "cured" (that is, left outside to ferment), chopped up, and macerated in water, after which the rubber is skimmed off the surface.
Latex Processing The latex of the Para Rubber Tree is said to be about 41% rubber and 55% water (EB11); CE says 27%/70% and 36%/60%, respectively, for four and ten year old trees.
Hevea latex can be stabilized by the addition of ammonia or sodium sulfite (CE), and then concentrated (much like separating cream from milk) for s.h.i.+pping. Rubber gloves and toy balloons are made by dipping molds into latex and then allowing the acquired layer to dry. This is usually done several times, to increase the thickness of the rubber, and then the dipped article is removed from the mold. However, most latex is coagulated into rubber at or near the collection site, and only later shaped into a final product.
The Hevea latex is unstable; the rubber will gradually separate from the water, a process called "coagulation." This can be expedited by addition of an acid, since Hevea latex is alkaline.
Crude Hevea plantation rubber was typically 94.6% rubber, 2.66% resin, 1.75% protein, 0.14% ash, and 0.85% water.
Grantville's only source of information concerning the handling of latex from other rubber trees is the EB11.
Castilla latex has the advantage that the rubber can be separated from the water by centrifugation. However, the standard processing method is to strain the "milk" through a wire sieve, add an alkaline plant juice (the Castilla latex is acidic) to cause coagulation, flatten out the coagulum to remove water bubbles, and then let the material dry for a few weeks.
In Africa, there was the curious practice of letting the Funtumia latex sit for half a month, covered with palm leaves, in a hollowed-out tree trunk. The trunk absorbs the water component, leaving the rubber behind. Another approach is to dilute the latex with water, and then heat it to coagulate the rubber. The Africans also employ plant-derived coagulating agents, but the bare reference to "Bauhinia leaves" is not likely to be of much use to us.
Perhaps the most important characteristic of Funtumia latex is not mentioned by the Grantville sources; it is very stable (Polhamus, 264). The same is true, to a lesser degree, of Castilla latex (102) and Ficus latex (264).
A number of natural latexes have a high resin content, and, if the resin is not removed, the rubber will be considered inferior. In 1911, solvent extraction of the resin was considered commercially impracticable, but that of course is very dependent on the price of the solvent as well as on the price difference between high resin and low resin rubber. EB11 shows that Ceara, Castilla and Ficus rubbers have average resin contents of 10.04%, 12.42%, and 11.8%, respectively.
Guayule rubber has a substantially higher resin content. According to CE, it is 20-25% for rubber extracted from the wild shrub, and about 16% in the case of the cultivated varieties. EA gives the resin content as 13-18%. It acknowledges that solvents have been used commercially to extract the resin, but does not provide particulars. The EB11 entry for "resin" says that it is "mostly soluble in alcohol, essential oils, ether and hot fatty oils." Curiously, CE states that the resin content is actually advantageous "as an aid to processing" when guayule rubber is blended with Hevea rubber.
Rubber Processing A general problem with natural rubbers is the presence, inadvertent or deliberate, of gross impurities (dirt, chips of wood, leaf material, etc.) Such defects can be mitigated by filtering the latex (see above) and by was.h.i.+ng the rubber.
The rubber initially conforms to the shape of the collecting cup and is called a biscuit. The spongy ma.s.s of rubber is washed (with hot or cold water) as it is pa.s.sed between grooved rollers (EB11, Fig. 8), producing ribbed sheet. CE suggests use of a series of rollers, with progressively finer corrugations. It was then hung to dry. If a smokehouse is used, the product is called smoked sheet. Or it can be dried without resort to smoking, producing crepe rubber. The rubber can be softened with heat and compressed into blocks.
Additional shaping may be carried out in factories. After softening (if necessary), the rubber may be calendered (rolled), molded or extruded. By suitable incorporation of air, sponge and foam rubber can be formed. (WBE) The rubber is warmed or masticated to soften it. The masticating machine (EB11, fig. 8) kneads the rubber, and, as this is happening, any desired additional ingredients (e.g., sulfur, carbon black, fillers, anti-aging compounds, colors, and oils), are mixed in. The rubber can then be softened further by heat and pressed into molds. One type of masticator, the rubber mill, has two rollers rotating inward, but at slightly different speeds. A more advanced masticator, the Banbury mixer, has rotating blades. (EA) The last step in the preparation of commercial rubber is vulcanization, since the vulcanized rubber cannot be further shaped. Without this treatment, rubber is an unsatisfactory material; it is brittle when cold and sticky or gooey when hot. Goodyear overcame these problems with his vulcanization process. In vulcanized rubber, the polyisoprene chains are cross-linked by disulfide bonds. Several methods of achieving vulcanization are described in EB11. In one, the rubber is immersed in molten sulfur for an hour or so at 140 deg. C. In another, the rubber is placed in a lead chamber with chloride of sulfur. In a third, it is cooked with a solution of calcium polysulfide at 140 deg. C. The use of excess sulfur or heat results in a hard, inelastic rubber (ebonite).
The Microsoft Encarta CD, which is probably available in Grantville, mentions that vulcanization can be accelerated with aniline and thiocarbanilide.
Rubberized cloth can be prepared by dissolving the rubber in one of its solvents ("carbon bisulphide, benzol and mineral naphtha, carbon tetrachloride, and chloroform") and then using the solution to coat the fabric. The original MacIntosh process used naphtha.
The Logistics of Rubber Collection Most rubber plants require a tropical climate. Once these plants have been located, we have four choices. First, we can simply trade with the natives for it. Second, we can go out into the hinterland and collect the latex from wild plants ourselves. Third, we can establish local rubber plantations. Finally, we can collect the seed (or other propagatable plant materials) and cultivate the plant elsewhere. This could be at a different tropical location (presumably, one more advantageous to USE), or in greenhouses back home.
All of the high-ranking rubber sources listed at the beginning of this essay have been cultivated, at least on an experimental basis. Most have also been transplanted, at least for trial purposes, to another part of the world, e.g., Hevea, Castilla and Manihot to Asia and Africa, Funtumia to Trinidad (Christy, 237) and Asia (EB11), Guayule to the Soviet Union, and the Russian dandelion to the USA.
However, because Hevea is the most important source of natural rubber, it behooves us to take a closer look at why plantations in Asia and Africa have supplanted the collection of wild rubber in Brazil.
Collecting Wild Hevea Rubber In our timeline, Brazil was not an important source of rubber after 1920. That is because the British successfully transplanted Hevea brasiliensis to Asia. The wild Brazilian rubber was unable to compete with the plantation rubber because its collection was too labor intensive.
There are limits to how much rubber can be collected from wild Hevea trees. They are widely dispersed in the rainforest, usually only two or three trees per hectare (Dean 10). The trees had to be found, and then connecting paths had to be created by hacking through the dense rainforest vegetation with a machete. Usually, a single tapper would clear two or three trails of 60 to 150 trees each. (Dean, 36-37) The tapper traversed one trail each day. In contrast, on a Hevea plantation, one tapper might process 400 trees in a single day (EA). Large-scale collection of wild rubber was limited by the labor supply. The Amazon jungles were thinly settled, so workers had to be brought in from elsewhere. These strangers were vulnerable to the many diseases and other pitfalls of life in the Amazon, and labor turnover was high. Even in 1907, "each ton cost five lives" (Dean, 44).
In the lower Amazon, and on the coast, where rubber trees were more accessible, yields declined substantially (from ten to two pounds of rubber per tree per year), as a result of overtapping (Brown, 104). The overtapping was evident by 1853, just eight years after the vulcanization process expanded the rubber market (Coates, 58-9). This forced collectors to go deeper into the Amazon, increasing provisioning costs.
In southeast Asia, plantations reduced labor costs, because a single worker could tap more trees in a day. Logically, the Brazilians should have started their own plantations. Unfortunately, even though it is native to the region, and hence well adapted to the local soil and climate, Hevea brasiliensis cannot be successfully cultivated in plantations in Latin America. The Microsoft Encarta Encyclopedia on CD in its "rubber" essay contains these fateful words: "About 99 percent of plantation rubber comes from southeastern Asia. Attempts to establish significant rubber plantations in the tropical zone of the western hemisphere have failed because of widespread tree loss as a result of a leaf blight." (More information about the attempts to establish Hevea plantations in Latin America appears in Appendix 3.) Even without the South American Leaf Blight, it is doubtful that Brazilian plantations would be compet.i.tive with southeast Asian ones. In the early 1900's, the daily cost of labor and provisions in the Orient was perhaps one eighth of that in Brazil (Akers).
The Grantville Gazette - Volume 6 Part 21
You're reading novel The Grantville Gazette - Volume 6 Part 21 online at LightNovelFree.com. You can use the follow function to bookmark your favorite novel ( Only for registered users ). If you find any errors ( broken links, can't load photos, etc.. ), Please let us know so we can fix it as soon as possible. And when you start a conversation or debate about a certain topic with other people, please do not offend them just because you don't like their opinions.
The Grantville Gazette - Volume 6 Part 21 summary
You're reading The Grantville Gazette - Volume 6 Part 21. This novel has been translated by Updating. Author: Eric Flint already has 698 views.
It's great if you read and follow any novel on our website. We promise you that we'll bring you the latest, hottest novel everyday and FREE.
LightNovelFree.com is a most smartest website for reading novel online, it can automatic resize images to fit your pc screen, even on your mobile. Experience now by using your smartphone and access to LightNovelFree.com
RECENTLY UPDATED NOVEL

Warning : Providence the Beauty is Driven to Villainy
Warning : Providence the Beauty is Driven to Villainy Chapter 1275: She is in the same boat as love (22)_1 View : 322,659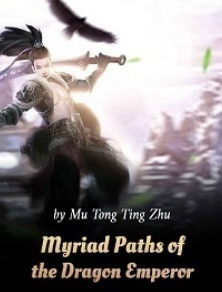
Myriad Paths of the Dragon Emperor
Myriad Paths of the Dragon Emperor Chapter 2976-killing a God King in succession View : 1,532,075
Complete Martial Arts Attributes
Complete Martial Arts Attributes Chapter 2877: No Way Of Escape? Hei Tian! Destruction Of The Void Speckle Great Array! (4) View : 2,830,880
The Beloved and Pampered Girl
The Beloved and Pampered Girl Chapter The 954th Inexpressible Embarrassment! View : 305,351
People Found Out About The Base I Built On the Moon
People Found Out About The Base I Built On the Moon Chapter 900: Chapter 107 Titan Star_6 View : 311,559
I Get A Random New Occupation Every Week
I Get A Random New Occupation Every Week Chapter 2086: Ning Che's Gentleness View : 1,429,685
World Dominating Empress Physician
World Dominating Empress Physician Chapter 2485: The heaven collapsing earth shattering trio reunited (1) View : 619,451