Practical Graining Part 4
You’re reading novel Practical Graining Part 4 online at LightNovelFree.com. Please use the follow button to get notification about the latest chapter next time when you visit LightNovelFree.com. Use F11 button to read novel in full-screen(PC only). Drop by anytime you want to read free – fast – latest novel. It’s great if you could leave a comment, share your opinion about the new chapters, new novel with others on the internet. We’ll do our best to bring you the finest, latest novel everyday. Enjoy!
MAHOGANY STRAIGHT.]
[Ill.u.s.tration: Plate 41.
MAHOGANY MOTTLED.]
CHAPTER XI.
MAHOGANY.
This wood was a great favorite with the grainers of the last generation, and it is at present coming back to old-time popularity.
The old Honduras "feathered" mahogany is rarely seen except in old furniture, and this kind of graining is seldom called for nowadays. The modern mahogany is more straight-grained, and is generally much lighter in color, but the furniture manufacturers do not hesitate to stain the wood to any depth of color, and thus they set the pattern which the grainer must follow as regards the color. It is represented in both oil and water color, or by being partly done both ways, as in the case of walnut. The colors used are burnt sienna, burnt umber and Vand.y.k.e brown, with crimson lake for overgraining on particularly bright work.
The tools used are the same as those for walnut. No better way to imitate it will be found than first to stipple it with a thin wash of Vand.y.k.e brown in beer, much the same as for walnut, but using the flat side of the stippler or blender more than the tip, as the pores of the wood are generally longer than those of walnut. After the stippling is dry rub in the oil color, which is composed of about three-fourths burnt sienna to one-fourth burnt umber, or a little Vand.y.k.e brown may be added to the color. The dark veins are put in with the sash tool dipped in a little clear Vand.y.k.e brown, which should be mixed in a separate vessel and thinned mostly with driers, as Vand.y.k.e brown is a very slow drier. The work is then gone over with a soft cotton rag, and the color is removed where the lighter grains are to appear; the rag is also used to soften the edges of the darker streaks and to blend them into the lighter grains. The lights and shadows are made, and the whole is then lightly blended crosswise. The bristle overgrainer of the fitch tool is used to put in the finer grains, or this may be done when the oil color is dry. This is the manner in which the modern straight mahogany is most frequently imitated, but it can wholly be done in water color, using the sponge for the same purpose as the rag is used in oil.
The "feather" mahogany is best represented in water color. The centre of the feather is darkened with Vand.y.k.e brown, and the mottler or sponge is used to make the darker curves which radiate from the centre of the "feather;" then with a thin piece of stick or a piece of cardboard make the bright blaze marks that are usually seen through the centre of the feather. A small mottler or cut tool may be used for this purpose. The markings radiate from the centre outward in a curved line and across the darker veins; allow this to dry, and then lightly overgrain to bring out the effect, touching up the parts that are to appear very dark. After this is dry the hand should lightly be pa.s.sed over the work to remove any surplus color, as one coat of varnish sometimes fails to lay out on water-color work where the graining-color has freely been used. This applies to walnut and rosewood in distemper as well as to mahogany. The wood is sometimes represented in oil without first stippling, but it never looks so well. Of course the stippling may be done after the work is dry, but it makes a better appearance if done before the rubbing with oil. If it is desired to overgrain, the work, if done in oil, should be shaded in distemper, and _vice versa_. For depth and brightness, add crimson lake with a little Vand.y.k.e brown.
[Ill.u.s.tration: Plate 42.
MAHOGANY FEATHERED.]
[Ill.u.s.tration: Plate 43.
ROSEWOOD AS OUTLINED TO OVERGRAIN.]
CHAPTER XII.
ROSEWOOD.
This wood is seldom imitated in this country except on piano-legs and caskets or coffins, and then it is done in stain on the wood without first being painted. Whitewood is given two coats of logwood stain, and after that is dry the grains are put in with a bamboo brush, which is made by beating the pulp out of the ends of short strips of bamboo, leaving the harder portions of the wood, which act as bristles for applying the graining-color. Four or five strips of bamboo an inch or more wide are fastened together with wire, so that their edges interlock at the point of the brush; the brush is then dipped in the graining color, which consists of iron-filings dissolved in vinegar.
The surplus color is shaken out of the brush, and the grains are put in in the same manner as that in which an overgrainer is used in water-color. The darker veins are added with a sponge after the finer grains are put in, and the work after being grained is generally filled with rose-pink. This process can be used only on new surfaces, and is of little value to the grainer to the trade.
The ordinary way of imitating rosewood is to do it in water color, although it may be done in oil. I prefer to do it in distemper, as the work can more quickly be finished in this way. The colors used are Vand.y.k.e brown, ivory black and rose pink. The basis of the color is Vand.y.k.e brown and a little black added to it. The ivory black and the rose pink are mixed separately, and applied to the work as desired while the color is wet, carefully blending where necessary. The rose-pink is first streaked through the color and blended; then the sponge is used to remove the color and make the lighter shades. The black veins are then put in, and after the whole is dry the overgrainer and the fitch tool are used to put in the fine grains. Last of all, the edges of the dark veins are sharpened with the fitch tool, using thin black for this purpose; this final application of black may be done in oil. Care must be taken not to take too much black, or the effect will be too sombre. The natural wood is almost invariably darkened by being stained as we see it on pianos, and its beauties are obscured by so doing. When the water color is finished and dry, the hand should be lightly pa.s.sed across the work to remove any surplus color that may not thoroughly adhere, as, if not removed, it works up into the varnish, or the varnish strikes in where the graining-color is thick; and for this reason two coats of varnish are better than one coat on any dark wood that has been done wholly in water color.
In operating entirely with oil the tools are much the same as those used for water color; the bristle piped overgrainer is best for oil color. The work is done in much the same manner as with water color, using the rag where the color is to be lightened, with a little more spirits of turpentine and j.a.pan in the color than ordinarily.
The grains of rosewood are not easily copied. The wood exhibits a variety of grain second only to oak, and I think that, after oak, it is the most difficult wood to imitate, as to do it justice requires the free treatment which can be given only by a trained hand and a correct eye. The average veins are free and graceful without being set or constrained, and the grains are constantly interlocking and branching off from the main hearts.
CYPRESS-WOOD
has but recently appeared in this country as an interior finish. It is a very soft and porous wood, and is a good kind to keep out of a house, owing to its liability to shrink and swell, but occasionally we find rooms finished with it, with the exception of the doors, which the grainer is called upon to match. I am informed that cypress trees have to be girdled in the spring and killed, so that they contain but little sap when cut in the fall, as, if cut green, they would sink in the water before they could be floated to the mill. This shows how ill suited this wood is for an interior finish.
[Ill.u.s.tration: Plate 44.
ROSEWOOD AS FINISHED.]
[Ill.u.s.tration: Plate 45.
CYPRESS IN OIL.]
The grain of cypress somewhat resembles that of hard pine, but is broader in the heart and finer-grained; it also presents more contrast between the light and dark portions of the growth. The ground is slightly darker and more yellow than that used for oak. The graining-color is made of raw and burnt sienna and burnt umber, and is mixed in oil. When the color is rubbed in, the hearts are wiped out in the usual manner. A rubber comb can be used to make portions of the heart by occasionally using it in the finer portions of the wiped-out hearts, taking care that the lines made by the comb closely follow those made by hand, and that they are equally distinct, or the places where the comb has been used can readily be distinguished from the rest of the work, and they look very bad. There is but little use for the fitch tool in matching cypress; the combing is mostly fine and rather straight. The steel combs should never be used over the lines made by the rubber comb. The work may be shaded with some of the graining-color to which some black has been added, and the whole thinned with spirits.
It needs but a very thin glaze, and is ordinarily finished without shading.
CHAPTER XIII.
HARD PINE.
This wood is seldom imitated, and, although its grains are simple, they cannot be matched without taking pains. The grain of hard pine is in some respects different from that of any other wood; the growths are generally quite narrow, and are not complicated, without having many knots, and are decidedly straight, as is also the combed work. The groundwork is much the same as that for oak, being slightly more yellow. The graining-color--which is mixed in oil--is composed of raw and burnt sienna, and a little burnt umber is added. The grains are put in by first using the rag to wipe out the hearts and then pencilling in the grain, or for the lighter parts of the grain the pencilling may be omitted. The combing is done with moderately fine combs. Never go over the same place twice, as the grains of pine are always straight and never interlock, like those of oak. The work should lightly be blended lengthwise. The color used to pencil in the growths should be darker than that with which the work is rubbed in, and the blending should always be done toward the outside edge of the grain. When the work is dry it may lightly be shaded to give it depth, or slightly mottled.
Some pieces of hard pine are profusely mottled, and I have seen specimens that had the appearance of fine Hungarian ash.
[Ill.u.s.tration: Plate 46.
HARD PINE.]
WHITEWOOD.
It is seldom necessary to imitate whitewood, as the original is so cheap, and because there is as much difficulty in matching the color of the wood as that of the grains. The ground-color is about the same as that for light ash, and the graining-color can be mixed with raw sienna and raw umber, adding black or blue; or yellow ochre can be used for the basis of the color, adding raw umber and a little black for the dark streaks. The work is then put in with a fitch tool and blended softly, or a piece of pointed wood like a pencil may be used, the point being covered with a thin cotton rag, and the heart grains put in with this, taking care to have the grains subdued and not appearing prominent. The grains of whitewood generally appear sunken; they are simply outlined, and not softened with the rag.
[Ill.u.s.tration: Plate 47.
WHITEWOOD IN OIL.]
Whitewood sometimes a.s.sumes a blistered appearance peculiar to itself and somewhat like the grain of Hungarian ash. This kind of whitewood is very difficult to imitate, as the high lights are so strong and brilliant as to require touching up with the ground-color after the work is dry. This kind is seldom imitated.
CHAPTER XIV.
VARNIs.h.i.+NG OVER GRAINED WORK.
When a job of graining is finished; if it is deemed necessary to varnish it, the question arises, "What kind of varnish shall be used?"
and this is a subject on which widely different opinions prevail.
Almost every master painter has his favorite kind of varnish and is slow to accept anything contrary to his own idea of what should be used; and right here I will say that if you have something that, like the joke of the clown in the circus, has withstood the test of time, do not look farther, but "hold fast to that which is good."
Practical Graining Part 4
You're reading novel Practical Graining Part 4 online at LightNovelFree.com. You can use the follow function to bookmark your favorite novel ( Only for registered users ). If you find any errors ( broken links, can't load photos, etc.. ), Please let us know so we can fix it as soon as possible. And when you start a conversation or debate about a certain topic with other people, please do not offend them just because you don't like their opinions.
Practical Graining Part 4 summary
You're reading Practical Graining Part 4. This novel has been translated by Updating. Author: William E. Wall already has 677 views.
It's great if you read and follow any novel on our website. We promise you that we'll bring you the latest, hottest novel everyday and FREE.
LightNovelFree.com is a most smartest website for reading novel online, it can automatic resize images to fit your pc screen, even on your mobile. Experience now by using your smartphone and access to LightNovelFree.com
- Related chapter:
- Practical Graining Part 3
- Practical Graining Part 5
RECENTLY UPDATED NOVEL

I'll Be the Male Leads Sister-in-Law
I'll Be the Male Leads Sister-in-Law Chapter 548 View : 165,014
Lord of Mysteries 2: Circle of Inevitability
Lord of Mysteries 2: Circle of Inevitability Chapter 1141: Divine Kingdom View : 638,913
Quick Transmigration Cannon Fodder's Record of Counterattacks
Quick Transmigration Cannon Fodder's Record of Counterattacks Chapter 2912: Wanted Him to Experience Another Failure View : 2,899,311
Number One Dungeon Supplier
Number One Dungeon Supplier Chapter 2134 The Dashavatara (Kurma) -Part 2 View : 1,240,937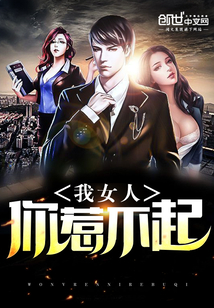