Practical Graining Part 6
You’re reading novel Practical Graining Part 6 online at LightNovelFree.com. Please use the follow button to get notification about the latest chapter next time when you visit LightNovelFree.com. Use F11 button to read novel in full-screen(PC only). Drop by anytime you want to read free – fast – latest novel. It’s great if you could leave a comment, share your opinion about the new chapters, new novel with others on the internet. We’ll do our best to bring you the finest, latest novel everyday. Enjoy!
[Ill.u.s.tration: FIG. 24.]
The piped bristle or fitch hair overgrainer (Fig. 4) may be used in oil or in distemper for representing ash, walnut, cherry, mahogany, etc.; for maple it may be used as an overgrainer. For overgraining any wood in distemper there is no better tool than the plain bristle overgrainer (Fig. 5) the bristles being separated into cl.u.s.ters with a bone comb after charging the brush with color.
[Ill.u.s.tration: FIG. 25.]
[Ill.u.s.tration: FIG. 26.]
The badger blender (Fig. 6) is used for all graining done in distemper and is sometimes used for oil work, a similar brush made of bristles is sometimes used for marbling. The flat bristle brush used for applying the graining color is the only blender necessary for oil work.
The castellated or knotted overgrainer (Figs. 7, 8 and 9) is used for graining in distemper work, which has previously been grained in oil.
The plain overgrainer (Figs. 10, 11 and 12) may be used for shading in distemper or for graining maple.
Mottlers or cutters made of bristles (Figs. 13, 14, 15, 16, 17) are for use for distemper color in graining maple, mahogany, etc.
The angular cutter (Fig. 17) is used for taking out the high lights in mahogany.
The waved mottler (Fig. 18) is used for representing maple, mahogany or satinwood in distemper.
Camel's-hair mottlers or cutters (Figs. 19 and 20) are used for very fine work on maple, etc., but the bristle brushes answer all practical purposes.
The serrated mottler or marbler (Fig. 21) is used for maple or satinwood in distemper or for marbling.
For applying distemper color a tin bound bristle graining brush (Fig.
22) is excellent, it should be about 1/2 an inch thick.
The bristle stippler (Fig. 23) is used for walnut or for mahogany in distemper.
The fitch or sable piped overgrainer (Fig. 24) is used in distemper for maple, satinwood or other delicate work.
The check roller is used for putting in the pores of oak and the dark streaks or lines in the hearts, and is used to best advantage in distemper. A well charged mottler supplies the color. The mottler is laid against the edges of the wheels, and by revolving the roller the color is transferred to the work. A guard of tin may be soldered to the mottler so that it fits the handle of the roller, being held in place by the thumb.
One or two flat fres...o...b..istle liners (Figs. 25 and 26) No. 1 and 2 for putting in hearts, veins, etc., and one or two tin bound sash tools complete the list of all tools necessary for use, and any wood that grows may be represented by using the tools mentioned.
CHAPTER XVII.
PATENT GRAINING MACHINES.
Various devices other than those usually employed--brushes, combs, etc.--have been invented for representing the grains of wood, and some of these machines are excellent, and are so constructed that by properly using them a very good imitation of wood may be obtained. The majority of them, however, seem to have been invented for the express purpose of being sold to gullible painters. The work done by such machines bears but little resemblance to the grain of any wood, and the only merit they possess is their boasted "ease of manipulation." It would seem that the majority of the patent pads, rollers, etc., now in use were designed by persons totally unfamiliar with the various woods which they claim their machines can represent; they bear the same relation to good handwork as the schoolboy's drawing of a house bears to that of an architect. The quality of the work seems to be immaterial if it can rapidly be executed; and if there are plenty of knots in the pattern, so much the better. It is of no consequence what wood it is supposed to represent, so long as it pleases the eye of the painter, and he will often purchase at an exorbitant price that which is practically useless for ordinary housework.
I have before me a circular containing some photographic ill.u.s.trations of the work done by a patent roller process; and if any wood ever grew that bears a resemblance to the ill.u.s.trations, I am ignorant of its name. Aniline colors are the means employed to represent the grains, and the process is designed to obviate the necessity of first painting the work, as the color is directly applied by the roller, without the wood being prepared in any way. It is claimed that any shadows or grains existing in the wood will only add to the beauty of the finished work. This will be news to the intelligent workman. The circular says nothing about how to use the rollers on painted work, so I presume it is worthless except for new work, and nearly so for that; for the painter who attempts to represent wood in the manner described will find that in the end it costs as much as though he had employed a skilful workman; and when the job is finished, he will have but a poor imitation of wood.
So far as I am aware, the oldest machine for representing the graining of wood is the Mason pad, which consists of a convex pad with handles at either end. The face of the pad is made of a rubber composition, on which are engraved the grains, the pad being about two feet in length.
The graining-color is applied to the work, and while wet the pad is pressed against it, thus removing sufficient color to show the grain.
This process is now seldom used; the composition of which the face of the pad is made hardens in cold weather and in hot weather it is inclined to run together, and great care must be taken to avoid defacing the pad.
The objection common to all roller processes or machines is that they do the same work over and over again, which is contrary to what we find in nature, as the grains are always different from one another, so that it would require an endless variety of patterns to do such work as is done by any first-cla.s.s grainer.
Another method for the rapid imitation of wood is found in stencil-plates, which consist of thin sheets of bra.s.s so constructed that when laid against the panel to be grained they leave no mark until a cloth is pa.s.sed over the plate, when the graining-color exposed by the stencil is rubbed off, thus making the grains. This sort of work looks much better than that done by any of the pads or rollers, but is open to the same objection--viz., repet.i.tion.
Another process is operated by having rolls with leather or composition surface, with the grains cut thereon; after the graining-color has been applied to the work, the rollers are pa.s.sed over it, thus removing the color wherever the roller touches. As a rule, the work done by this process is not very distinct, nor is it particularly clean. Very large rollers have to be used in order to grain a panel four feet long, as the work will seldom join without showing the joints; and while a door was being grained in this manner (with joints in the panels), a skilful workman could do one by hand and in a much better manner.
The best work that I have ever seen, not done by hand, was by means of a composition roller with a smooth surface; it can be used only for the imitation of porous woods, as chestnut, ash and walnut, and is useless for oak, cherry or any of the close-grained woods. The work can first be stippled in distemper, and when dry rubbed in lightly in oil; or the roller can be applied directly to the stippled work or to the groundwork, and afterwards stippled if necessary. It is requisite to procure several pieces of the wood to be imitated, smoothed carefully with the pores open; then directly apply the graining-color and with the composition roller go over the wood, taking the color from the pores and applying it directly to the work by transfer. If carefully done, you have an exact duplicate of the grain of the real wood, and no man can do better work than this; but, in order to grain a room or a house in this manner, it is necessary to have a great variety of pieces of porous wood, and to use each piece only for imitating the wood of which it is composed.
The gransorbian is another transfer process, by which the grains are produced as follows: The graining-color is applied in the usual manner, and heavy absorptive paper on which the grain of the wood to be imitated is impressed is laid against the wet color; a roller with a smooth surface is pa.s.sed over the paper, using considerable force, so that the color is absorbed into the paper wherever it is pressed against the work by the roller. The paper can be used several times before it becomes useless through becoming saturated with color, but, being cheap, it is an inexpensive manner of doing fair to good work.
All depends on the man who makes the patterns, as, if they are not true to nature, the effect is very bad, and some of the samples that I have seen are very poor imitations of the grain of any wood. I should judge that the paper is produced by applying the pulp to a block of wood on which the pattern to be produced is engraved, using considerable pressure to force the pulp into the carved work. The plain work is done with combs in the usual manner.
Another transfer process is the transfer paper. The grain is printed on paper similar to the best wall-paper, and is transferred to the groundwork by pressure after first wetting the back of the paper and allowing time for the water thoroughly to soften the printed color. The surface of the groundwork must first be damped in order to receive the moist color from the paper. Two or three impressions may be obtained from each wetting of the paper. Some of the work done by this process is excellent, and approaches very near the work done by the smooth transfer roller, but the majority of the paper is printed from blocks or cylinders, designed not by nature, but by man, and are unworthy of comparison with those printed from nature.
There are various processes other than handwork, but the above are the princ.i.p.al methods employed.
The first-cla.s.s grainer has nothing to fear from any of the foregoing processes, for while some were being used the work could be done in the old way, and equally well, provided the workmen were at all skilful. I have never seen any work that can excel fine handwork, as there is more grace and variety in such work than there is in any done by any other methods. When the services of a grainer cannot be obtained, machine processes may answer for ordinary work or for small work, such as ice-chests, pails, etc., but the chief objection I have to them is that they claim too much, and the average painter who buys the process is deceived, because he is told that any wood can be imitated by this or that machine, when such is not the case.
CHAPTER XVIII.
IMITATIONS OF CARVED WORK, MOULDINGS, ETC., BY GRAINING.
In imitating carved work, mouldings, etc. in graining color, more than ordinary ability is required in order to succeed in deceiving people; and this kind of work should not be attempted unless there is ample time for its proper execution, nor should its use be contemplated for too exposed positions, as if not thoroughly done it is an eyesore to the intelligent beholder, but if done in a recessed doorway or other suitable place, inside or outside, it enhances the value of the work if it agrees with the general style of the architecture or of the surroundings. Mouldings or raised panels are often imitated on front doors where the real article would never be placed by an intelligent carpenter, owing to the shape of the door; hence it would be displaying poor judgment to place the imitation where the real article ought to find no place. It is wonderful how a thorough grainer can transform a plastered wall into one apparently sheathed or wainscoted, and I have seen doors so perfectly imitated that persons would grasp at the k.n.o.b in attempting to open a door that was grained on a plastered wall.
Imitations of carved figures, scrolls and game-birds are favored by some workmen, and are very effective if well done; as a rule such work should be seen in a subdued light to render the deception more complete.
[Ill.u.s.tration]
Practical Graining Part 6
You're reading novel Practical Graining Part 6 online at LightNovelFree.com. You can use the follow function to bookmark your favorite novel ( Only for registered users ). If you find any errors ( broken links, can't load photos, etc.. ), Please let us know so we can fix it as soon as possible. And when you start a conversation or debate about a certain topic with other people, please do not offend them just because you don't like their opinions.
Practical Graining Part 6 summary
You're reading Practical Graining Part 6. This novel has been translated by Updating. Author: William E. Wall already has 816 views.
It's great if you read and follow any novel on our website. We promise you that we'll bring you the latest, hottest novel everyday and FREE.
LightNovelFree.com is a most smartest website for reading novel online, it can automatic resize images to fit your pc screen, even on your mobile. Experience now by using your smartphone and access to LightNovelFree.com
- Related chapter:
- Practical Graining Part 5
RECENTLY UPDATED NOVEL

Lord of Mysteries 2: Circle of Inevitability
Lord of Mysteries 2: Circle of Inevitability Chapter 1141: Divine Kingdom View : 638,892
Quick Transmigration Cannon Fodder's Record of Counterattacks
Quick Transmigration Cannon Fodder's Record of Counterattacks Chapter 2912: Wanted Him to Experience Another Failure View : 2,899,255
Number One Dungeon Supplier
Number One Dungeon Supplier Chapter 2134 The Dashavatara (Kurma) -Part 2 View : 1,240,915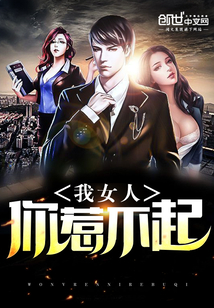