Gas and Oil Engines, Simply Explained Part 4
You’re reading novel Gas and Oil Engines, Simply Explained Part 4 online at LightNovelFree.com. Please use the follow button to get notification about the latest chapter next time when you visit LightNovelFree.com. Use F11 button to read novel in full-screen(PC only). Drop by anytime you want to read free – fast – latest novel. It’s great if you could leave a comment, share your opinion about the new chapters, new novel with others on the internet. We’ll do our best to bring you the finest, latest novel everyday. Enjoy!
Referring again to fig. 26, this gas or governor cam may be set out, and the keyway marked on the same principle as already described for the air and exhaust valves. An end view of the three cams keyed up on the side shaft is given in fig. 40A. In small engines it is convenient to have the air and exhaust cams made in one casting, when one key only will be required. On some engines, instead of employing a movable roller or valve lever, the exhaust cam is fitted on side shaft with a "feather"--_i.e._, a headless key--and the cam being capable of longitudinal movement, such movement being controlled by a small lever or handle, called the half-compression lever.
[Ill.u.s.tration: FIG. 40.]
[Ill.u.s.tration: FIG. 40A.]
Having once thoroughly grasped the important part the cams play in the working of the engine, it will be an easy matter to adjust the valve settings, and to keep them adjusted correctly. The effect of a wrong setting will then be strikingly apparent. On small engines a separate cam to operate the gas valve is not a necessity; and the practice of fitting the gas valve spindle (or the p.e.c.k.e.r, the effect would be the same) with a device for increasing or diminis.h.i.+ng its length, is also unnecessary and unsound.
The wear on a well-designed gas valve operating mechanism is practically nil; and even if there was wear, the effect would be to cause the valve to open a trifle later and close sooner than it would otherwise, _i.e._, it would remain open a shorter time during each charging stroke. This in turn (other conditions remaining the same) would give us a weaker mixture; and although too weak a mixture is preferable to a too rich one, we should have to adopt some means of increasing the richness of the mixture; otherwise the maximum power of the engine would soon be seen to diminish.
To get the mixture normal again we must either enlarge the gas inlet or cut down the air-supply somewhat, and so keep the proportions the same.
That is to say, the quality of the mixture is dependent upon the relative dimension of the gas and air inlets. We know by actual trial that if at the completion of the charging stroke the pressure in the cylinder is approximately that of the atmosphere, better results are obtained than when the pressure is considerably below that of the atmosphere. Thus, the larger we make the inlet ports (but still retaining correct relative dimensions) the more readily will the mixture be drawn into the cylinder as the piston moves forward, tending to create a vacuum. Of the two courses open to us to retain a good mixture it is preferable to open out the gas-supply, for by cutting down the air-supply, and sucking the gas in, due to the partial vacuum being formed, we should be keeping the proportions correct at the expense of reducing the total volume of the explosive mixture (more strictly speaking, the density of the charge) admitted to the cylinder.
Under normal conditions it is not necessary to create a high vacuum to suck the gas into the cylinder, but it is as well to understand what results we would tend to produce, did we work on these lines. Of course, with small high-speed engines fitted with suction air valve, the vacuum is higher than it would be in slow-speed engines with mechanically operated valves. If we take an extreme case as an example, where, to get any gas to speak of into the cylinder the air-supply would have to be cut down or throttled to an abnormal extent, we will realise at once that such a small quant.i.ty of both air and gas would have been drawn in, and consequently the mixture would be so rarefied that on the compression stroke the pressure would possibly be extremely low and totally inadequate to produce efficient working. Moreover, working at such a high vacuum as this would not only prevent us obtaining a normal explosion in the cylinder, but would upset the working of the exhaust valve. The latter being held down on its seat during the suction stroke by means of a spiral spring would be lifted off its seat by suction (the partial vacuum in the cylinder), and any burnt gases which happened to be hanging about in the exhaust port or pipe would be drawn into the cylinder again, and tend to damp the ensuing explosion. Too early closing of the exhaust should be avoided almost as rigorously as too late. The latter will affect the working in a similar way to the exhaust being lifted on the charging stroke by suction; on the other hand, if it closes too soon, the entire volume of burnt gases will not have been swept out of the cylinder, and the effect will again be to damp the following explosion.
The gas valve opens just after the crank is above the back centre and closes just before the front centre is reached, that is, opening a little after the air valve and closing a shade before it, thus every particle of gas is used in the cylinder, due to a draught of air being drawn in after the gas valve has been closed.
The settings of the valve being of primary importance, no matter what size engine we are dealing with, and being also the most confusing matter for anyone unacquainted with gas engines to grasp, it will not be out of place to suggest a simple method of checking these settings.
Let us begin by pulling the fly-wheel round backwards until we feel the piston is on the compression stroke, then from this point--the crank being about 45 above the front centre--pull the wheel round until the crank is in the position for the exhaust opening (see fig. 28). In this position there should be but the _slightest_ play in the exhaust lever, showing that the valve is _just_ on point of opening; and by keeping one's hand on the lever whilst the fly-wheel is pulled round _very slowly_ (it is a good plan to get some one else to do the pulling round), it is possible to ascertain the precise point at which the valve opens. Next pull round till the crank is in the position for the air valve opening, and observe that it is set correctly. Then go on to a trifle above the back centre, where the exhaust valve should close, and so on till the opening and closing of each valve has been checked. It will be noticed that the air, and sometimes the gas, valve opens before the exhaust closes. This overlap is necessary; and it will be found that the smaller the engine and the higher the speed the greater this overlap will be to obtain good results, although a good deal of individual judgment must be used in settling the exact amount of overlap, as the requisite amount may, to get the best results, vary in different engines of precisely the same dimensions and type.
When dealing with engines which have no separate gas valve--the gas being admitted with the air, which is sometimes the case with very small engines--the above notes referring to the gas setting independently, will, of course, not hold good.
It may be mentioned with regard to the lump on the opening side of the exhaust cam, that this if overdone is found to be detrimental on large engines, and even on small ones. If it is too large, it will cause both exhaust valve and seat to become burnt and pitted, due to the surface being exposed to the exceedingly high temperature of the expanding gases. If it is too large, it is equivalent to opening the exhaust valve too early, and the effect is the same, viz., a waste of power and damage to the valve and its seat.
[Ill.u.s.tration: FIG. 43.]
[Ill.u.s.tration: FIG. 44.--Brake Testing.]
The method of grinding in the valves to their seats with emery powder and oil is so well known that no further description is needed here. We give, however, in fig. 43 a sketch showing a very expeditious way of dealing with very badly worn or burnt seats. The sketch explains itself.
Such a tool is readily made; even the cutter could be turned and filed up to shape and then hardened at home. By lightly tapping in the taper cotter pin little by little, sufficient pressure is put on the cutter to make it an easy matter to completely re-face an old seat or form a new one. A T-wrench or "tommy" can be used to work the cutter spindle. The lower part of the latter must be the same diameter as the existing valve spindle; the bush acts as a guide; and as the bevel of the cutter should be the same as that of the valve, a very little grinding in with emery powder is required to finish the job off.
In fig. 44 we give a diagram showing the method of testing for Brake H.P. of engine, as it is frequently interesting to make such a simple test after any alterations or adjustments have been made.
Two spring balances and a rope or cord (according to the size of the engine), fitted with a few wood blocks as shown in section, fig. 44, to keep the rope on the rim of fly-wheel, is all that is required for this test. The following formula may be used for arriving at the B.H.P.:--
B.H.P. = (S1 - S2) 3.14 x D x R / 33000
S1 = Reading in lbs. of spring balance No. 1.
S2 = Reading in lbs. of spring balance No. 2.
D = Diameter of fly-wheel and diameter of brake rope in feet.
R = Revolutions of fly-wheel per minute.
As 3.14 x D / 33000 will always remain the same for any given engine and gear, we may call that expression C; then the B.H.P. may be written--
B.H.P. = (S1 - S2) C R
CHAPTER VIII
OIL ENGINES
The small oil engine is practically the same as the gas engine, with the addition of a vaporiser for converting the oil into gas, or vapour, to be exploded in the cylinder; consequently the one may be converted into the other in many cases without much trouble. The difficulty of producing an efficient oil engine lies princ.i.p.ally in devising a satisfactory and reliable vapouriser--one which will work equally well under all loads. The heat supplied to the chamber must be sufficient to vaporise the oil, but not great enough to decompose it. There are various methods of vaporising the oil, and many types of vaporisers are employed to attain the same end. There are some in which a charge of oil is drawn by suction into a hot chamber in which it is converted into vapour and at the same time mixed with a small quant.i.ty of hot air; this rich mixture is then pa.s.sed into the combustion chamber of the engine, in the same manner as coal-gas would be, where it is further diluted with more air drawn in through the air valve. Other arrangements cause a jet of oil to be injected into a chamber containing hot air, in the form of spray, which immediately converts the oil into vapour, and is then pa.s.sed into the cylinder, compressed, and fired. Then, again, we can pump oil through a spraying nipple into the vapouriser (which is kept at a suitable temperature) whilst the cylinder is being filled with air on the suction stroke. On the following compression stroke the air is driven into the vapouriser, which communicates with the cylinder through a narrow neck, and mixes intimately with the oil vapour.
Gradually, as the pressure rises, due to compression, the charge becomes more and more explosive, until at the completion of this stroke it has attained the proper proportions of air and oil vapour, and is fired by the temperature of the vapouriser and that caused by a high compression; that is, the charge is fired automatically; and once the engine is running, no heating lamp is required to keep the vapouriser at the correct temperature. It is necessary, however, to raise it to the workable temperature at starting. This is known as the Hornsby-Akroyd method.
Capel's arrangement is also simple and efficient, and has the additional advantage of being capable of being fitted to their existing gas engines, the conversion being made in a very short time. This vapouriser consists primarily of a tubular casting A, on the outside of which are formed a series of vertical ribs, shown in plan, fig. 46, running to within a short distance of the f.l.a.n.g.e at one end, as shown in the section, fig. 45, thus providing an annular s.p.a.ce C between the upper ends of the ribs and the f.l.a.n.g.e. This casting is enclosed by an outer casing B, which fits well over the inner tube. It has also a number of small holes drilled near the lower end communicating with the channels between the ribs. Thus it will be seen that when the gas valve is opened and suction takes place, air is drawn in through these holes, pa.s.ses up into the annular s.p.a.ce C below the top f.l.a.n.g.e, from there travels to the opposite side of vapouriser, and mixes with the oil which is also being drawn in through a small nipper at N, fig. 45. Both then pa.s.s between a series of pegs, where they become thoroughly mixed, and finally pa.s.s on to the inlet valve V, fig. 47, and so into the cylinder, where the complete charge is mixed up and compressed and fired in the usual manner. Iron ignition tubes may be used, and one heating lamp serves a double purpose in keeping the tube and vapouriser hot at the same time.
This lamp is fed by means of a pump actuated from the side shaft. The plunger of the pump is loaded with a spiral spring, which may be adjusted to give any desired pressure, and is kept constant and steady by means of an air vessel. This pump is shown in fig. 48. It is actuated by means of a rod and lever from the side shaft of engine. The plunger P works in a barrel B, which is carried by a small reservoir R, the latter being in communication with the main oil tank by means of the pipe H.
[Ill.u.s.tration: FIG. 46.]
[Ill.u.s.tration: FIG. 45.]
[Ill.u.s.tration: FIG. 47.]
[Ill.u.s.tration: FIG. 48.]
[Ill.u.s.tration: FIG. 49.]
[Ill.u.s.tration: FIG. 50.]
[Ill.u.s.tration: FIG. 51.]
The plunger is loaded with a spiral spring, and has a ball valve, as shown. Intermediate between this small reservoir and the main oil tank is another set of valves, shown in fig. 49. It will be seen that the suction of the pump will draw the oil up, the small and lower ball valve, of course, allowing it to pa.s.s freely. On the down stroke the lower valve will be automatically closed, and the oil will be put under pressure, this being determined by the load on the plunger valve, which is adjustable by means of the screw S, fig. 48. When the required pressure in the pipe P, figs. 45 and 49, has been attained, the plunger valve lifts on each stroke and the surplus oil flows through the plunger into the small reservoir R. The latter is at about the same level as another still smaller reservoir M (shown in figs. 47 and 50), a flow of oil being established between the two by means of a pipe Q (see figs. 48 and 50). In the reservoir R is fitted an overflow pipe, so that the oil cannot rise beyond a certain level; hence the head of oil in the smaller one M is always constant. On the suction stroke a partial vacuum is formed in the engine cylinder, consequently the pressure in the vapouriser drops somewhat below that of the atmosphere, and this small difference in pressure is enough to cause the oil to rise in the small pa.s.sage X, fig. 45, beyond its normal level, and overflow into the vapourising chamber, as previously described. The valve or nipper N is shown open in the diagram, fig. 45, and all that is required to stop the engine when running is to drop the small handle L, fig. 45, when the valve will close, due to the spring S. The air vessel shown in fig. 49 is in communication with the pipe leading to the blow lamp. A pressure gauge can also be fitted, although it is not in any way a necessity.
The ratchet wheel and pawl shown in fig. 48 are part of the lubricator.
The wheel drives a bra.s.s or gun-metal plug, producing an intermittent rotary motion. The plug has a small hole in its periphery, which becomes filled with oil when it is at the upper part of its travel, and empties the oil out into a discharge pipe T, when it is inverted, and is then led away and applied to the piston at the required spot. Fig. 51 shows this arrangement in section.
Gas and Oil Engines, Simply Explained Part 4
You're reading novel Gas and Oil Engines, Simply Explained Part 4 online at LightNovelFree.com. You can use the follow function to bookmark your favorite novel ( Only for registered users ). If you find any errors ( broken links, can't load photos, etc.. ), Please let us know so we can fix it as soon as possible. And when you start a conversation or debate about a certain topic with other people, please do not offend them just because you don't like their opinions.
Gas and Oil Engines, Simply Explained Part 4 summary
You're reading Gas and Oil Engines, Simply Explained Part 4. This novel has been translated by Updating. Author: Walter C. Runciman already has 818 views.
It's great if you read and follow any novel on our website. We promise you that we'll bring you the latest, hottest novel everyday and FREE.
LightNovelFree.com is a most smartest website for reading novel online, it can automatic resize images to fit your pc screen, even on your mobile. Experience now by using your smartphone and access to LightNovelFree.com
- Related chapter:
- Gas and Oil Engines, Simply Explained Part 3
RECENTLY UPDATED NOVEL

Cultivation Online
Cultivation Online Chapter 1775 Successor of the Cultivation Tower View : 1,851,187
After Transmigrating, The Fat Wife Made A Comeback!
After Transmigrating, The Fat Wife Made A Comeback! Chapter 2362: The Day of the Wedding Banquet View : 2,149,897
The Grand Secretary's Pampered Wife
The Grand Secretary's Pampered Wife Chapter 753.1: The King Returns! View : 591,530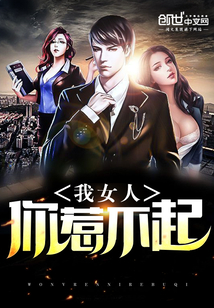
You Cannot Afford To Offend My Woman
You Cannot Afford To Offend My Woman Chapter 1234 (Too Chaotic) View : 1,789,700