De Re Metallica Part 38
You’re reading novel De Re Metallica Part 38 online at LightNovelFree.com. Please use the follow button to get notification about the latest chapter next time when you visit LightNovelFree.com. Use F11 button to read novel in full-screen(PC only). Drop by anytime you want to read free – fast – latest novel. It’s great if you could leave a comment, share your opinion about the new chapters, new novel with others on the internet. We’ll do our best to bring you the finest, latest novel everyday. Enjoy!
Or else one _libra_ of the concentrates from was.h.i.+ng pyrites, or other stones to which gold adheres, is mixed with half a _libra_ of salt, half a _libra_ of argol, a third of a _libra_ of gla.s.s-galls, a sixth of a _libra_ of gold or silver slags, and a _sicilicus_ of copper. The crucible into which these are put, after it has been covered with a lid, is sealed with lute and placed in a small furnace that is provided with small holes through which the air is drawn in, and then it is heated until it turns red and the substances put in have alloyed; this should take place within four or five hours. The alloy having cooled, it is again crushed to powder and a pound of litharge is added to it; then it is heated again in another crucible until it melts. The b.u.t.ton is taken out, purged of slag, and placed in a cupel, where the gold is separated from the lead.
Or to a _libra_ of the powder prepared from such metalliferous concentrates, is added a _libra_ each of salt, of saltpetre, of argol, and of gla.s.s-galls, and it is heated until it melts. When cooled and crushed, it is washed, then to it is added a _libra_ of silver, a third of copper filings, a sixth of litharge, and it is likewise heated again until it melts. After the b.u.t.ton has been purged of slag, it is put into the cupel, and the gold and silver are separated from the lead; the gold is parted from the silver with _aqua valens_. Or else a _libra_ of the powder prepared from such metalliferous concentrates, a quarter of a _libra_ of copper filings, and two _librae_ of that second powder[32]
which fuses ores, are heated until they melt. The mixture when cooled is again reduced to powder, roasted and washed, and in this manner a blue powder is obtained. Of this, and silver, and that second powder which fuses ores, a _libra_ each are taken, together with three _librae_ of lead, and a quarter of a _libra_ of copper, and they are heated together until they melt; then the b.u.t.ton is treated as before. Or else a _libra_ of the powder prepared from such metalliferous concentrates, half a _libra_ of saltpetre, and a quarter of a _libra_ of salt are heated until they melt. The alloy when cooled is again crushed to powder, one _libra_ of which is absorbed by four pounds of molten silver. Or else a _libra_ of the powder made from that kind of concentrates, together with a _libra_ of sulphur, a _libra_ and a half of salt, a third of a _libra_ of salt made from argol, and a third of a _libra_ of copper resolved into powder with sulphur, are heated until they melt. Afterward the lead is re-melted, and the gold is separated from the other metals. Or else a _libra_ of the powder of this kind of concentrates, together with two _librae_ of salt, half a _libra_ of sulphur, and one _libra_ of litharge, are heated, and from these the gold is melted out. By these and similar methods concentrates containing gold, if there be a small quant.i.ty of them or if they are very rich, can be smelted outside the blast furnace.
If there be much of them and they are poor, then they are smelted in the blast furnace, especially the ore which is not crushed to powder, and particularly when the gold mines yield an abundance of it[33]. The gold concentrates mixed with litharge and hearth-lead, to which are added iron-scales, are smelted in the blast furnace whose tap-hole is intermittently closed, or else in the first or the second furnaces in which the tap-hole is always open. In this manner an alloy of gold and lead is obtained which is put into the cupellation furnace. Two parts of roasted pyrites or _cadmia_ which contain gold, are put with one part of unroasted, and are smelted together in the third furnace whose tap-hole is always open, and are made into cakes. When these cakes have been repeatedly roasted, they are re-smelted in the furnace whose tap-hole is temporarily closed, or in one of the two others whose tap-holes are always open. In this manner the lead absorbs the gold, whether pure or argentiferous or cupriferous, and the alloy is taken to the cupellation furnace. Pyrites, or other gold ore which is mixed with much material that is consumed by fire and flies out of the furnace, is melted with stone from which iron is melted, if this is at hand. Six parts of such pyrites, or of gold ore reduced to powder and sifted, four of stone from which iron is made, likewise crushed, and three of slaked lime, are mixed together and moistened with water; to these are added two and a half parts of the cakes which contain some copper, together with one and a half parts of slag. A basketful of fragments of the cakes is thrown into the furnace, then the mixture of other things, and then the slag.
Now when the middle part of the forehearth is filled with the molten material which runs down from the furnace, the slags are first skimmed off, and then the cakes made of pyrites; afterward the alloy of copper, gold and silver, which settles at the bottom, is taken out. The cakes are gently roasted and re-smelted with lead, and made into cakes, which are carried to other works. The alloy of copper, gold, and silver is not roasted, but is re-melted again in a crucible with an equal portion of lead. Cakes are also made much richer in copper and gold than those I spoke of. In order that the alloy of gold and silver may be made richer, to eighteen _librae_ of it are added forty-eight _librae_ of crude ore, three _librae_ of the stone from which iron is made, and three-quarters of a _libra_ of the cakes made from pyrites, and mixed with lead, all are heated together in the crucible until they melt. When the slag and the cakes melted from pyrites have been skimmed off, the alloy is carried to other furnaces.
There now follows silver, of which the native silver or the lumps of _rudis_ silver[34] obtained from the mines are not smelted in the blast furnaces, but in small iron pans, of which I will speak at the proper place; these lumps are heated and thrown into molten silver-lead alloy in the cupellation furnace when the silver is being separated from the lead, and refined. The tiny flakes or tiny lumps of silver adhering to stones or marble or rocks, or again the same little lumps mixed with earth, or silver not pure enough, should be smelted in the furnace of which the tap-hole is only closed for a short time, together with cakes melted from pyrites, with silver slags, and with stones which easily fuse in fire of the second order.
In order that particles of silver should not fly away[35] from the lumps of ore consisting of minute threads of pure silver and twigs of native silver, they are enclosed in a pot, and are placed in the same furnace where the rest of the silver ores are being smelted. Some people smelt lumps of native silver not sufficiently pure, in pots or triangular crucibles, whose lids are sealed with lute. They do not place these pots in the blast furnace, but arrange them in the a.s.say furnace into which the draught of the air blows through small holes. To one part of the native silver they add three parts of powdered litharge, as many parts of hearth-lead, half a part of galena[36], and a small quant.i.ty of salt and iron-scales. The alloy which settles at the bottom of the other substances in the pot is carried to the cupellation furnace, and the slags are re-melted with the other silver slags. They crush under the stamps and wash the pots or crucibles to which silver-lead alloy or slags adhere, and having collected the concentrates they smelt them together with the slags. This method of smelting _rudis_ silver, if there is a small quant.i.ty of it, is the best, because the smallest portion of silver does not fly out of the pot or the crucible, and get lost.
If bis.m.u.th ore or antimony ore or lead ore[37] contains silver, it is smelted with the other ores of silver; likewise galena or pyrites, if there is a small amount of it. If there be much galena, whether it contain a large or a small amount of silver, it is smelted separately from the others; which process I will explain a little further on.
Because lead and copper ores and their metals have much in common with silver ores, it is fitting that I should say a great deal concerning them, both now and later on. Also in the same manner, pyrites are smelted separately if there be much of them. To three parts of roasted lead or copper ore and one part of crude ore, are added concentrates if they were made by was.h.i.+ng the same ore, together with slags, and all are put in the third furnace whose tap-hole is always open. Cakes are made from this charge, which, when they have been quenched with water, are roasted. Of these roasted cakes generally four parts are again mixed with one part of crude pyrites and re-melted in the same furnace. Cakes are again made from this charge, and if there is a large amount of copper in these cakes, copper is made immediately after they have been roasted and re-melted; if there is little copper in the cakes they are also roasted, but they are re-smelted with a little soft slag. In this method the molten lead in the forehearth absorbs the silver. From the pyritic material which floats on the top of the forehearth are made cakes for the third time, and from them when they have been roasted and re-smelted is made copper. Similarly, three parts of roasted _cadmia_[38] in which there is silver, are mixed with one part of crude pyrites, together with slag, and this charge is smelted and cakes are made from it; these cakes having been roasted are re-smelted in the same furnace. By this method the lead contained in the forehearth absorbs the silver, and the silver-lead is taken to the cupellation furnace. Crude quartz and stones which easily fuse in fire of the third order, together with other ores in which there is a small amount of silver, ought to be mixed with crude roasted pyrites or _cadmia_, because the roasted cakes of pyrites or _cadmia_ cannot be profitably smelted separately. In a similar manner earths which contain little silver are mixed with the same; but if pyrites and _cadmia_ are not available to the smelter, he smelts such silver ores and earths with litharge, hearth-lead, slags, and stones which easily melt in the fire. The concentrates[39]
originating from the was.h.i.+ng of _rudis_ silver, after first being roasted[40] until they melt, are smelted with mixed litharge and hearth-lead, or else, after being moistened with water, they are smelted with cakes made from pyrites and _cadmia_. By neither of these methods do (the concentrates) fall back in the furnace, or fly out of it, driven by the blast of the bellows and the agitation of the fire. If the concentrates originated from galena they are smelted with it after having been roasted; and if from pyrites, then with pyrites.
Pure copper ore, whether it is its own colour or is tinged with chrysocolla or azure, and copper glance, or grey or black _rudis_ copper, is smelted in a furnace of which the tap-hole is closed for a very short time, or else is always open[41]. If there is a large amount of silver in the ore it is run into the forehearth, and the greater part of the silver is absorbed by the molten lead, and the remainder is sold with the copper to the proprietor of the works in which silver is parted from copper[42]. If there is a small amount of silver in the ore, no lead is put into the forehearth to absorb the silver, and the above-mentioned proprietors buy it in with the copper; if there be no silver, copper is made direct. If such copper ore contains some minerals which do not easily melt, as pyrites or _cadmia metallica fossilis_[43], or stone from which iron is melted, then crude pyrites which easily fuse are added to it, together with slag. From this charge, when smelted, they make cakes; and from these, when they have been roasted as much as is necessary and re-smelted, the copper is made. But if there be some silver in the cakes, for which an outlay of lead has to be made, then it is first run into the forehearth, and the molten lead absorbs the silver.
Indeed, _rudis_ copper ore of inferior quality, whether ash-coloured or purple, blackish and occasionally in parts blue, is smelted in the first furnace whose tap-hole is always open. This is the method of the Tyrolese. To as much _rudis_ copper ore as will fill eighteen vessels, each of which holds almost as much as seven Roman _moduli_[44], the first smelter--for there are three--adds three cartloads of lead slags, one cartload of schist, one fifth of a _centumpondium_ of stones which easily fuse in the fire, besides a small quant.i.ty of concentrates collected from copper slag and accretions, all of which he smelts for the s.p.a.ce of twelve hours, and from which he makes six _centumpondia_ of primary cakes and one-half of a _centumpondium_ of alloy. One half of the latter consists of copper and silver, and it settles to the bottom of the forehearth. In every _centumpondium_ of the cakes there is half a _libra_ of silver and sometimes half an _uncia_ besides; in the half of a _centumpondium_ of the alloy there is a _bes_ or three-quarters of silver. In this way every week, if the work is for six days, thirty-six _centumpondia_ of cakes are made and three _centumpondia_ of alloy, in all of which there is often almost twenty-four _librae_ of silver. The second smelter separates from the primary cakes the greater part of the silver by absorbing it in lead. To eighteen _centumpondia_ of cakes made from crude copper ore, he adds twelve _centumpondia_ of hearth-lead and litharge, three _centumpondia_ of stones from which lead is smelted, five _centumpondia_ of hard cakes rich in silver, and two _centumpondia_ of exhausted liquation cakes[45]; he adds besides, some of the slags resulting from smelting crude copper, together with a small quant.i.ty of concentrates made from accretions, all of which he melts for the s.p.a.ce of twelve hours, and makes eighteen _centumpondia_ of secondary cakes, and twelve _centumpondia_ of copper-lead-silver alloy; in each _centumpondium_ of the latter there is half a _libra_ of silver. After he has taken off the cakes with a hooked bar, he pours the alloy out into copper or iron moulds; by this method they make four cakes of alloy, which are carried to the works in which silver is parted from copper. On the following day, the same smelter, taking eighteen _centumpondia_ of the secondary cakes, again adds twelve _centumpondia_ of hearth-lead and litharge, three _centumpondia_ of stones from which lead is smelted, five _centumpondia_ of hard cakes rich in silver, together with slags from the smelting of the primary cakes, and with concentrates washed from the accretions which are usually made at that time. This charge is likewise smelted for the s.p.a.ce of twelve hours, and he makes as many as thirteen _centumpondia_ of tertiary cakes and eleven _centumpondia_ of copper-lead-silver alloy, each _centumpondium_ of which contains one-third of a _libra_ and half an _uncia_ of silver.
When he has skimmed off the tertiary cakes with a hooked bar, the alloy is poured into copper moulds, and by this method four cakes of alloy are made, which, like the preceding four cakes of alloy, are carried to the works in which silver is parted from copper. By this method the second smelter makes primary cakes on alternate days and secondary cakes on the intermediate days. The third smelter takes eleven cartloads of the tertiary cakes and adds to them three cartloads of hard cakes poor in silver, together with the slag from smelting the secondary cakes, and the concentrates from the accretions which are usually made at that time. From this charge when smelted, he makes twenty _centumpondia_ of quaternary cakes, which are called "hard cakes," and also fifteen _centumpondia_ of those "hard cakes rich in silver," each _centumpondium_ of which contains a third of a _libra_ of silver. These latter cakes the second smelter, as I said before, adds to the primary and secondary cakes when he re-melts them. In the same way, from eleven cartloads of quaternary cakes thrice roasted, he makes the "final"
cakes, of which one _centumpondium_ contains only half an _uncia_ of silver. In this operation he also makes fifteen _centumpondia_ of "hard cakes poor in silver," in each _centumpondium_ of which is a sixth of a _libra_ of silver. These hard cakes the third smelter, as I have said, adds to the tertiary cakes when he re-smelts them, while from the "final" cakes, thrice roasted and re-smelted, is made black copper[46].
The _rudis_ copper from which pure copper is made, if it contains little silver or if it does not easily melt, is first smelted in the third furnace of which the tap-hole is always open; and from this are made cakes, which after being seven times roasted are re-smelted, and from these copper is melted out; the cakes of copper are carried to a furnace of another kind, in which they are melted for the third time, in order that in the copper "bottoms" there may be more silver, while in the "tops" there may be less, which process is explained in Book XI.
Pyrites, when they contain not only copper, but also silver, are smelted in the manner I described when I treated of ores of silver. But if they are poor in silver, and if the copper which is melted out of them cannot easily be treated, they are smelted according to the method which I last explained.
Finally, the copper schists containing bitumen or sulphur are roasted, and then smelted with stones which easily fuse in a fire of the second order, and are made into cakes, on the top of which the slags float.
From these cakes, usually roasted seven times and re-melted, are melted out slags and two kinds of cakes; one kind is of copper and occupies the bottom of the crucible, and these are sold to the proprietors of the works in which silver is parted from copper; the other kind of cakes are usually re-melted with primary cakes. If the schist contains but a small amount of copper, it is burned, crushed under the stamps, washed and sieved, and the concentrates obtained from it are melted down; from this are made cakes from which, when roasted, copper is made. If either chrysocolla or azure, or yellow or black earth containing copper and silver, adheres to the schist, it is not washed, but is crushed and smelted with stones which easily fuse in fire of the second order.
Lead ore, whether it be _molybdaena_[47], pyrites, (galena?) or stone from which it is melted, is often smelted in a special furnace, of which I have spoken above, but no less often in the third furnace of which the tap-hole is always open. The hearth and forehearth are made from powder containing a small portion of iron hammer-scales; iron slag forms the princ.i.p.al flux for such ores; both of these the expert smelters consider useful and to the owner's advantage, because it is the nature of iron to attract lead. If it is _molybdaena_ or the stone from which lead is smelted, then the lead runs down from the furnace into the forehearth, and when the slags have been skimmed off, the lead is poured out with a ladle. If pyrites are smelted, the first to flow from the furnace into the forehearth, as may be seen at Goslar, is a white molten substance, injurious and noxious to silver, for it consumes it. For this reason the slags which float on the top having been skimmed off, this substance is poured out; or if it hardens, then it is taken out with a hooked bar; and the walls of the furnace exude the same substance[48]. Then the _stannum_ runs out of the furnace into the forehearth; this is an alloy of lead and silver. From the silver-lead alloy they first skim off the slags, not rarely white, as some pyrites[49] are, and afterward they skim off the cakes of pyrites, if there are any. In these cakes there is usually some copper; but since there is usually but a very small quant.i.ty, and as the forest charcoal is not abundant, no copper is made from them. From the silver-lead poured into iron moulds they likewise make cakes; when these cakes have been melted in the cupellation furnace, the silver is parted from the lead, because part of the lead is transformed into litharge and part into hearth-lead, from which in the blast furnace on re-melting they make de-silverized lead, for in this lead each _centumpondium_ contains only a _drachma_ of silver, when before the silver was parted from it each _centumpondium_ contained more or less than three _unciae_ of silver[50].
The little black stones[51] and others from which tin is made, are smelted in their own kind of furnace, which should be narrower than the other furnaces, that there may be only the small fire which is necessary for this ore. These furnaces are higher, that the height may compensate for the narrowness and make them of almost the same capacity as the other furnaces. At the top, in front, they are closed and on the other side they are open, where there are steps, because they cannot have the steps in front on account of the forehearth; the smelters ascend by these steps to put the tin-stone into the furnace. The hearth of the furnace is not made of powdered earth and charcoal, but on the floor of the works are placed sandstones which are not too hard; these are set on a slight slope, and are two and three-quarters feet long, the same number of feet wide, and two feet thick, for the thicker they are the longer they last in the fire. Around them is constructed a rectangular furnace eight or nine feet high, of broad sandstones, or of those common substances which by nature are composed of diverse materials[52]. On the inside the furnace is everywhere evenly covered with lute. The upper part of the interior is two feet long and one foot wide, but below it is not so long and wide. Above it are two hood-walls, between which the fumes ascend from the furnace into the dust chamber, and through this they escape by a narrow opening in the roof. The sandstones are sloped at the bed of the furnace, so that the tin melted from the tin-stone may flow through the tap-hole of the furnace into the forehearth.[53]
As there is no need for the smelters to have a fierce fire, it is not necessary to place the nozzles of the bellows in bronze or iron pipes, but only through a hole in the furnace wall. They place the bellows higher at the back so that the blast from the nozzles may blow straight toward the tap-hole of the furnace. That it may not be too fierce, the nozzles are wide, for if the fire were fiercer, tin could not be melted out from the tin-stone, as it would be consumed and turned into ashes.
Near the steps is a hollowed stone, in which is placed the tin-stone to be smelted; as often as the smelter throws into the furnace an iron shovel-ful of this tin-stone, he puts on charcoal that was first put into a vat and washed with water to be cleansed from the grit and small stones which adhere to it, lest they melt at the same time as the tin-stone and obstruct the tap-hole and impede the flow of tin from the furnace. The tap-hole of the furnace is always open; in front of it is a forehearth a little more than half a foot deep, three-quarters of two feet long and one foot wide; this is lined with lute, and the tin from the tap-hole flows into it. On one side of the forehearth is a low wall, three-quarters of a foot wider and one foot longer than the forehearth, on which lies charcoal powder. On the other side the floor of the building slopes, so that the slags may conveniently run down and be carried away. As soon as the tin begins to run from the tap-hole of the furnace into the forehearth, the smelter sc.r.a.pes down some of the powdered charcoal into it from the wall, so that the slags may be separated from the hot metal, and so that it may be covered, lest any part of it, being very hot, should fly away with the fumes. If after the slag has been skimmed off, the powder does not cover up the whole of the tin, the smelter draws a little more charcoal off the wall with a sc.r.a.per. After he has opened the tap-hole of the forehearth with a tapping-bar, in order that the tin can flow into the tapping-pot, likewise smeared with lute, he again closes the tap-hole with pure lute or lute mixed with powdered charcoal. The smelter, if he be diligent and experienced, has brooms at hand with which he sweeps down the walls above the furnace; to these walls and to the dust chamber minute tin-stones sometimes adhere with part of the fumes. If he be not sufficiently experienced in these matters and has melted at the same time all of the tin-stone,--which is commonly of three sizes, large, medium, and very small,--not a little waste of the proprietor's tin results; because, before the large or the medium sizes have melted, the small have either been burnt up in the furnace, or else, flying up from it, they not only adhere to the walls but also fall in the dust chamber.
The owner of the works has the sweepings by right from the owner of the ore. For the above reasons the most experienced smelter melts them down separately; indeed, he melts the very small size in a wider furnace, the medium in a medium-sized furnace, and the largest size in the narrowest furnace. When he melts down the small size he uses a gentle blast from the bellows, with the medium-sized a moderate one, with the large size a violent blast; and when he smelts the first size he needs a slow fire, for the second a medium one, and for the third a fierce one; yet he uses a much less fierce fire than when he smelts the ores of gold, silver, or copper. When the workmen have spent three consecutive days and nights in this work, as is usual, they have finished their labours; in this time they are able to melt out a large weight of small sized tin-stone which melts quickly, but less of the large ones which melt slowly, and a moderate quant.i.ty of the medium-sized which holds the middle course.
Those who do not smelt the tin-stone in furnaces made sometimes wide, sometimes medium, or sometimes narrow, in order that great loss should not be occasioned, throw in first the smallest size, then the medium, then the large size, and finally those which are not quite pure; and the blast of the bellows is altered as required. In order that the tin-stone thrown into the furnace should not roll off from the large charcoal into the forehearth before the tin is melted out of it, the smelter uses small charcoal; first some of this moistened with water is placed in the furnace, and then he frequently repeats this succession of charcoal and tin-stone.
The tin-stone, collected from material which during the summer was washed in a ditch through which a stream was diverted, and during the winter was screened on a perforated iron plate, is smelted in a furnace a palm wider than that in which the fine tin-stone dug out of the earth is smelted. For the smelting of these, a more vigorous blast of the bellows and a fiercer fire is needed than for the smelting of the large tin-stone. Whichever kind of tin-stone is being smelted, if the tin first flows from the furnace, much of it is made, and if slags first flow from the furnace, then only a little. It happens that the tin-stone is mixed with the slags when it is either less pure or ferruginous--that is, not enough roasted--and is imperfect when put into the furnace, or when it has been put in in a larger quant.i.ty than was necessary; then, although it may be pure and melt easily, the ore either runs out of the furnace at the same time, mixed with the slags, or else it settles so firmly at the bottom of the furnace that the operation of smelting being necessarily interrupted, the furnace freezes up.
[Ill.u.s.tration 415 (Tin smelting Furnaces): A--Furnace. B--Its tap-hole.
C--Forehearth. D--Its tap-hole. E--Slags. F--Sc.r.a.per. G--Dipping-pot.
H--Walls of the chimney. I--Broom. K--Copper plate. L--Latticework bars.
M--Iron seal or die. N--Hammer.]
The tap-hole of the forehearth is opened and the tin is diverted into the dipping-pot, and as often as the slags flow down the sloping floor of the building they are skimmed off with a rabble; as soon as the tin has run out of the forehearth, the tap-hole is again closed up with lute mixed with powdered charcoal. Glowing coals are put in the dipping-pot so that the tin, after it has run out, should not get chilled. If the metal is so impure that nothing can be made from it, the material which has run out is made into cakes to be re-smelted in the hearth, of which I shall have something to say later; if the metal is pure, it is poured immediately upon thick copper plates, at first in straight lines and then transversely over these to make a lattice. Each of these lattice bars is impressed with an iron die; if the tin was melted out of ore excavated from mines, then one stamp only, namely, that of the Magistrate, is usually imprinted, but if it is made from tin-stone collected on the ground after was.h.i.+ng, then it is impressed with two seals, one the Magistrate's and the other a fork which the washers use.
Generally, three of this kind of lattice bars are beaten and amalgamated into one ma.s.s with a wooden mallet.
The slags that are skimmed off are afterward thrown with an iron shovel into a small trough hollowed from a tree, and are cleansed from charcoal by agitation; when taken out they are broken up with a square iron mallet, and then they are re-melted with the fine tin-stone next smelted. There are some who crush the slags three times under wet stamps and re-melt them three times; if a large quant.i.ty of this be smelted while still wet, little tin is melted from it, because the slag, soon melted again, flows from the furnace into the forehearth. Under the wet stamps are also crushed the lute and broken rock with which such furnaces are lined, and also the accretions, which often contain fine tin-stone, either not melted or half-melted, and also prills of tin. The tin-stone not yet melted runs out through the screen into a trough, and is washed in the same way as tin-stone, while the partly melted and the prills of tin are taken from the mortar-box and washed in the sieve on which not very minute particles remain, and thence to the canvas strake.
The soot which adheres to that part of the chimney which emits the smoke, also often contains very fine tin-stone which flies from the furnace with the fumes, and this is washed in the strake which I have just mentioned, and in other sluices. The prills of tin and the partly melted tin-stone that are contained in the lute and broken rock with which the furnace is lined, and in the remnants of the tin from the forehearth and the dipping-pot, are smelted together with the tin-stone.
When tin-stone has been smelted for three days and as many nights in a furnace prepared as I have said above, some little particles of the rock from which the furnace is constructed become loosened by the fire and fall down; and then the bellows being taken away, the furnace is broken through at the back, and the accretions are first chipped off with hammers, and afterward the whole of the interior of the furnace is re-fitted with the prepared sandstone, and again evenly lined with lute.
The sandstone placed on the bed of the furnace, if it has become faulty, is taken out, and another is laid down in its place; those rocks which are too large the smelter chips off and fits with a sharp pick.
[Ill.u.s.tration 417 (Tin smelting Furnaces): A--Furnaces. B--Forehearths.
C--Their tap-holes. D--Dipping-pots. E--Pillars. F--Dust-chamber.
G--Window. H--Chimneys. I--Tub in which the coals are washed.]
Some build two furnaces against the wall just like those I have described, and above them build a vaulted ceiling supported by the wall and by four pillars. Through holes in the vaulted ceiling the fumes from the furnaces ascend into a dust chamber, similar to the one described before, except that there is a window on each side and there is no door.
The smelters, when they have to clear away the flue-dust, mount by the steps at the side of the furnaces, and climb by ladders into the dust chamber through the apertures in the vaulted ceilings over the furnaces.
They then remove the flue-dust from everywhere and collect it in baskets, which are pa.s.sed from one to the other and emptied. This dust chamber differs from the other described, in the fact that the chimneys, of which it has two, are not dissimilar to those of a house; they receive the fumes which, being unable to escape through the upper part of the chamber, are turned back and re-ascend and release the tin; thus the tin set free by the fire and turned to ash, and the little tin-stones which fly up with the fumes, remain in the dust chamber or else adhere to copper plates in the chimney.
[Ill.u.s.tration 418 (Refining Tin): A--Hearths. B--Dipping-pots. C--Wood.
D--Cakes. E--Ladle. F--Copper plate. G--Lattice-shaped bars. H--Iron dies. I--Wooden mallet. K--Ma.s.s of tin bars. L--Shovel.]
If the tin is so impure that it cracks when struck with the hammer, it is not immediately made into lattice-like bars, but into the cakes which I have spoken of before, and these are refined by melting again on a hearth. This hearth consists of sandstones, which slope toward the centre and a little toward a dipping-pot; at their joints they are covered with lute. Dry logs are arranged on each side, alternately upright and lengthwise, and more closely in the middle; on this wood are placed five or six cakes of tin which all together weigh about six _centumpondia_; the wood having been kindled, the tin drips down and flows continuously into the dipping-pot which is on the floor. The impure tin sinks to the bottom of this dipping-pot and the pure tin floats on the top; then both are ladled out by the master, who first takes out the pure tin, and by pouring it over thick plates of copper makes lattice-like bars. Afterward he takes out the impure tin from which he makes cakes; he discriminates between them, when he ladles and pours, by the ease or difficulty of the flow. One _centumpondium_ of the lattice-like bars sells for more than a _centumpondium_ of cakes, for the price of the former exceeds the price of the latter by a gold coin[54]. These lattice-like bars are lighter than the others, and when five of them are pounded and amalgamated with a wooden mallet, a ma.s.s is made which is stamped with an iron die. There are some who do not make a dipping-pot on the floor for the tin to run into, but in the hearth itself; out of this the master, having removed the charcoal, ladles the tin and pours it over the copper-plate. The dross which adheres to the wood and the charcoal, having been collected, is re-smelted in the furnace.
[Ill.u.s.tration 419 (Blast Furnaces): A--Furnace. B--Bellows. C--Iron Disc. D--Nozzle. E--Wooden Disc. F--Blow-hole. G--Handle. H--Haft.
I--Hoops. K--Ma.s.ses of tin.]
Some of the Lusitanians melt tin from tin-stone in small furnaces. They use round bellows made of leather, of which the fore end is a round iron disc and the rear end a disc of wood; in a hole in the former is fixed the nozzle, in the middle of the latter the blow-hole. Above this is the handle or haft, which draws open the round bellows and lets in the air, or compresses it and drives the air out. Between the discs are several iron hoops to which the leather is fastened, making such folds as are to be seen in paper lanterns that are folded together. Since this kind of bellows does not give a vigorous blast, because they are drawn apart and compressed slowly, the smelter is not able during a whole day to smelt much more than half a _centumpondium_ of tin.
[Ill.u.s.tration 422 (Iron smelting Furnaces): A--Hearth. B--Heap.
C--Slag-vent. D--Iron ma.s.s. E--Wooden mallets. F--Hammer. G--Anvil.]
Very good iron ore is smelted[55] in a furnace almost like the cupellation furnace. The hearth is three and a half feet high, and five feet long and wide; in the centre of it is a crucible a foot deep and one and a half feet wide, but it may be deeper or shallower, wider or narrower, according to whether more or less ore is to be made into iron.
A certain quant.i.ty of iron ore is given to the master, out of which he may smelt either much or little iron. He being about to expend his skill and labour on this matter, first throws charcoal into the crucible, and sprinkles over it an iron shovel-ful of crushed iron ore mixed with unslaked lime. Then he repeatedly throws on charcoal and sprinkles it with ore, and continues this until he has slowly built up a heap; it melts when the charcoal has been kindled and the fire violently stimulated by the blast of the bellows, which are skilfully fixed in a pipe. He is able to complete this work sometimes in eight hours, sometimes in ten; and again sometimes in twelve. In order that the heat of the fire should not burn his face, he covers it entirely with a cap, in which, however, there are holes through which he may see and breathe.
At the side of the hearth is a bar which he raises as often as is necessary, when the bellows blow too violent a blast, or when he adds more ore and charcoal. He also uses the bar to draw off the slags, or to open or close the gates of the sluice, through which the waters flow down on to the wheel which turns the axle that compresses the bellows.
In this sensible way, iron is melted out and a ma.s.s weighing two or three _centumpondia_ may be made, providing the iron ore was rich. When this is done the master opens the slag-vent with the tapping-bar, and when all has run out he allows the iron ma.s.s to cool. Afterward he and his a.s.sistant stir the iron with the bar, and then in order to chip off the slags which had until then adhered to it, and to condense and flatten it, they take it down from the furnace to the floor, and beat it with large wooden mallets having slender handles five feet long.
Thereupon it is immediately placed on the anvil, and repeatedly beaten by the large iron hammer that is raised by the cams of an axle turned by a water-wheel. Not long afterward it is taken up with tongs and placed under the same hammer, and cut up with a sharp iron into four, five, or six pieces, according to whether it is large or small. These pieces, after they have been re-heated in the blacksmith's forge and again placed on the anvil, are shaped by the smith into square bars or into ploughshares or tyres, but mainly into bars. Four, six, or eight of these bars weigh one-fifth of a _centumpondium_, and from these they make various implements. During the blows from the hammer by which it is shaped by the smith, a youth pours water with a ladle on to the glowing iron, and this is why the blows make such a loud sound that they may be heard a long distance from the works. The ma.s.ses, if they remain and settle in the crucible of the furnace in which the iron is smelted, become hard iron which can only be hammered with difficulty, and from these they make the iron-shod heads for the stamps, and such-like very hard articles.
[Ill.u.s.tration 424 (Iron smelting Furnaces): A--Furnace. B--Stairs.
C--Ore. D--Charcoal.]
But to iron ore which is cupriferous, or which when heated[56] melts with difficulty, it is necessary for us to give a fiercer fire and more labour; because not only must we separate the parts of it in which there is metal from those in which there is no metal, and break it up by dry stamps, but we must also roast it, so that the other metals and noxious juices may be exhaled; and we must wash it, so that the lighter parts may be separated from it. Such ores are smelted in a furnace similar to the blast furnace, but much wider and higher, so that it may hold a great quant.i.ty of ore and much charcoal; mounting the stairs at the side of the furnace, the smelters fill it partly with fragments of ore not larger than nuts, and partly with charcoal; and from this kind of ore once or twice smelted they make iron which is suitable for re-heating in the blacksmith's forge, after it is flattened out with the large iron hammer and cut into pieces with the sharp iron.
[Ill.u.s.tration 425 (Steel making Furnaces): A--Forge. B--Bellows.
C--Tongs. D--Hammer. E--Cold stream.]
By skill with fire and fluxes is made that kind of iron from which steel is made, which the Greeks call [Greek: stomoma]. Iron should be selected which is easy to melt, is hard and malleable. Now although iron may be smelted from ore which contains other metals, yet it is then either soft or brittle; such (iron) must be broken up into small pieces when it is hot, and then mixed with crushed stone which melts. Then a crucible is made in the hearth of the smith's furnace, from the same moistened powder from which are made the forehearths in front of the furnaces in which ores of gold or silver are smelted; the width of this crucible is about one and a half feet and the depth one foot. The bellows are so placed that the blast may be blown through the nozzle into the middle of the crucible. Then the whole of the crucible is filled with the best charcoal, and it is surrounded by fragments of rock to hold in place the pieces of iron and the superimposed charcoal. As soon as all the charcoal is kindled and the crucible is glowing, a blast is blown from the bellows and the master pours in gradually as much of the mixture of iron and flux as he wishes. Into the middle of this, when it is melted, he puts four iron ma.s.ses each weighing thirty pounds, and heats them for five or six hours in a fierce fire; he frequently stirs the melted iron with a bar, so that the small pores in each ma.s.s absorb the minute particles, and these particles by their own strength consume and expand the thick particles of the ma.s.ses, which they render soft and similar to dough. Afterward the master, aided by his a.s.sistant, takes out a ma.s.s with the tongs and places it on the anvil, where it is pounded by the hammer which is alternately raised and dropped by means of the water-wheel; then, without delay, while it is still hot, he throws it into water and tempers it; when it is tempered, he places it again on the anvil, and breaks it with a blow from the same hammer. Then at once examining the fragments, he decides whether the iron in some part or other, or as a whole, appears to be dense and changed into steel; if so, he seizes one ma.s.s after another with the tongs, and taking them out he breaks them into pieces. Afterward he heats the mixture up again, and adds a portion afresh to take the place of that which has been absorbed by the ma.s.ses. This restores the energy of that which is left, and the pieces of the ma.s.ses are again put back into the crucible and made purer. Each of these, after having been heated, is seized with the tongs, put under the hammer and shaped into a bar. While they are still glowing, he at once throws them into the very coldest nearby running water, and in this manner, being suddenly condensed, they are changed into pure steel, which is much harder and whiter than iron.
The ores of the other metals are not smelted in furnaces. Quicksilver ores and also antimony are melted in pots, and bis.m.u.th in troughs.
[Ill.u.s.tration 427 (Quicksilver distillation Furnaces): A--Hearth.
B--Poles. C--Hearth without fire in which the pots are placed. D--Rocks.
E--Rows of pots. F--Upper pots. G--Lower pots.]
I will first speak of quicksilver. This is collected when found in pools formed from the outpourings of the veins and stringers; it is cleansed with vinegar and salt, and then it is poured into canvas or soft leather, through which, when squeezed and compressed, the quicksilver runs out into a pot or pan. The ore of quicksilver is reduced in double or single pots. If in double pots, then the upper one is of a shape not very dissimilar to the gla.s.s ampullas used by doctors, but they taper downward toward the bottom, and the lower ones are little pots similar to those in which men and women make cheese, but both are larger than these; it is necessary to sink the lower pots up to the rims in earth, sand, or ashes. The ore, broken up into small pieces is put into the upper pots; these having been entirely closed up with moss, are placed upside down in the openings of the lower pots, where they are joined with lute, lest the quicksilver which takes refuge in them should be exhaled. There are some who, after the pots have been buried, do not fear to leave them uncemented, and who boast that they are able to produce no less weight of quicksilver than those who do cement them, but nevertheless cementing with lute is the greatest protection against exhalation. In this manner seven hundred pairs of pots are set together in the ground or on a hearth. They must be surrounded on all sides with a mixture consisting of crushed earth and charcoal, in such a way that the upper pots protrude to a height of a palm above it. On both sides of the hearth rocks are first laid, and upon them poles, across which the workmen place other poles transversely; these poles do not touch the pots, nevertheless the fire heats the quicksilver, which fleeing from the heat is forced to run down through the moss into the lower pots. If the ore is being reduced in the upper pots, it flees from them, wherever there is an exit, into the lower pots, but if the ore on the contrary is put in the lower pots the quicksilver rises into the upper pot or into the operculum, which, together with the gourd-shaped vessels, are cemented to the upper pots.
De Re Metallica Part 38
You're reading novel De Re Metallica Part 38 online at LightNovelFree.com. You can use the follow function to bookmark your favorite novel ( Only for registered users ). If you find any errors ( broken links, can't load photos, etc.. ), Please let us know so we can fix it as soon as possible. And when you start a conversation or debate about a certain topic with other people, please do not offend them just because you don't like their opinions.
De Re Metallica Part 38 summary
You're reading De Re Metallica Part 38. This novel has been translated by Updating. Author: Georgius Agricola already has 686 views.
It's great if you read and follow any novel on our website. We promise you that we'll bring you the latest, hottest novel everyday and FREE.
LightNovelFree.com is a most smartest website for reading novel online, it can automatic resize images to fit your pc screen, even on your mobile. Experience now by using your smartphone and access to LightNovelFree.com
- Related chapter:
- De Re Metallica Part 37
- De Re Metallica Part 39
RECENTLY UPDATED NOVEL

The King of Hell's Genius Pampered Wife
The King of Hell's Genius Pampered Wife Chapter 1928: Accepted! View : 2,732,481
A Demon Lord's Tale: Dungeons, Monster Girls, and Heartwarming Bliss
A Demon Lord's Tale: Dungeons, Monster Girls, and Heartwarming Bliss Chapter 574 View : 1,365,608
Eternal Life Begins with Taking a Wife
Eternal Life Begins with Taking a Wife Chapter 1153: Mysterious Exotic Beast (1) View : 410,651
Cultivation: Start From Simplifying Martial Arts Techniques
Cultivation: Start From Simplifying Martial Arts Techniques Chapter 1092: Chapter 1048 Stepping Stone View : 621,142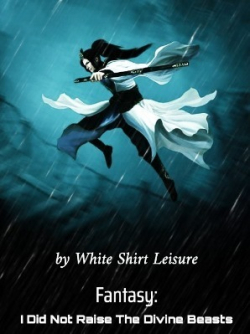
Fantasy: I Did Not Raise The Divine Beasts
Fantasy: I Did Not Raise The Divine Beasts Chapter 1111: These Are All Trash (1) View : 387,886