De Re Metallica Part 50
You’re reading novel De Re Metallica Part 50 online at LightNovelFree.com. Please use the follow button to get notification about the latest chapter next time when you visit LightNovelFree.com. Use F11 button to read novel in full-screen(PC only). Drop by anytime you want to read free – fast – latest novel. It’s great if you could leave a comment, share your opinion about the new chapters, new novel with others on the internet. We’ll do our best to bring you the finest, latest novel everyday. Enjoy!
[Ill.u.s.tration 543 (Copper Refining): A--Furnace. B--Forehearth.
C--Oblong moulds.]
The _cadmia_,[32] as it is called by us, is made from the "slags" which the master, who makes copper from "dried" cakes, draws off together with other re-melted base "slags"; for, indeed, if the copper cakes made from such "slags" are broken, the fragments are called _cadmia_; from this and yellow copper is made _caldarium_ copper in two ways. For either two parts of _cadmia_ are mixed with one of yellow copper in the blast furnaces, and melted; or, on the contrary, two parts of yellow copper with one of _cadmia_, so that the _cadmia_ and yellow copper may be well mixed; and the copper which flows down from the furnace into the forehearth is poured out with a ladle into oblong copper moulds heated beforehand. These moulds are sprinkled over with charcoal dust before the _caldarium_ copper is to be poured into them, and the same dust is sprinkled over the copper when it is poured in, lest the _cadmia_ and yellow copper should freeze before they have become well mixed. With a piece of wood the a.s.sistant cleanses each cake from the dust, when it is turned out of the mould. Then he throws it into the tub containing hot water, for the _caldarium_ copper is finer if quenched in hot water. But as I have so often made mention of the oblong copper moulds, I must now speak of them a little; they are a foot and a palm long, the inside is three palms and a digit wide at the top, and they are rounded at the bottom.
The concentrates are of two kinds--precious and base.[33] The first are obtained from the accretions of the blast furnace, when liquation cakes are made from copper and lead, or from precious liquation thorns, or from the better quality "slags," or from the best grade of concentrates, or from the sweepings and bricks of the furnaces in which exhausted liquation cakes are "dried"; all of these things are crushed and washed, as I explained in Book VIII. The base concentrates are made from accretions formed when cakes are cast from base thorns or from the worst quality of slags. The smelter who makes liquation cakes from the precious concentrates, adds to them three wheelbarrowsful of litharge and four barrowsful of hearth-lead and one of ash-coloured copper, from all of which nine or ten liquation cakes are melted out, of which five at a time are placed in the furnace in which silver-lead is liquated from copper; a _centumpondium_ of the lead which drips from these cakes contains one _uncia_ of silver. The liquation thorns are placed apart by themselves, of which one basketful is mixed with the precious thorns to be re-melted. The exhausted liquation cakes are "dried" at the same time as other good exhausted liquation cakes.
The thorns which are drawn off from the lead, when it is separated from silver in the cupellation furnace[34], and the hearth-lead which remains in the crucible in the middle part of the furnaces, together with the hearth material which has become defective and has absorbed silver-lead, are all melted together with a little slag in the blast furnaces. The lead, or rather the silver-lead, which flows from the furnace into the forehearth, is poured out into copper moulds such as are used by the refiners; a _centumpondium_ of such lead contains four _unciae_ of silver, or, if the hearth was defective, it contains more. A small portion of this material is added to the copper and lead when liquation cakes are made from them, if more were to be added the alloy would be much richer than it should be, for which reason the wise foreman of the works mixes these thorns with other precious thorns. The hearth-lead which remains in the middle of the crucible, and the hearth material which absorbs silver-lead, is mixed with other hearth-lead which remains in the cupellation furnace crucible; and yet some cakes, made rich in this manner, may be placed again in the cupellation furnaces, together with the rest of the silver-lead cakes which the refiner has made.
The inhabitants of the Carpathian Mountains, if they have an abundance of finely crushed copper[35] or lead either made from "slags," or collected from the furnace in which the exhausted liquation cakes are dried, or litharge, alloy them in various ways. The "first" alloy consists of two _centumpondia_ of lead melted out of thorns, litharge, and thorns made from hearth-lead, and of half a _centumpondium_ each of lead collected in the furnace in which exhausted liquation cakes are "dried," and of copper _minutum_, and from these are made liquation cakes; the task of the smelter is finished when he has made forty liquation cakes of this kind. The "second" alloy consists of two _centumpondia_ of litharge, of one and a quarter _centumpondia_ of de-silverized lead or lead from "slags," and of half a _centumpondium_ of lead made from thorns, and of as much copper _minutum_. The "third"
alloy consists of three _centumpondia_ of litharge and of half a _centumpondium_ each of de-silverized lead, of lead made from thorns, and of copper _minutum contusum_. Liquation cakes are made from all these alloys; the task of the smelters is finished when they have made thirty cakes.
The process by which cakes are made among the Tyrolese, from which they separate the silver-lead, I have explained in Book IX.
Silver is separated from iron in the following manner. Equal portions of iron scales and filings and of _stibium_ are thrown into an earthenware crucible which, when covered with a lid and sealed, is placed in a furnace, into which air is blown. When this has melted and again cooled, the crucible is broken; the b.u.t.ton that settles in the bottom of it, when taken out, is pounded to powder, and the same weight of lead being added, is mixed and melted in a second crucible; at last this b.u.t.ton is placed in a cupel and the lead is separated from the silver.[36]
There are a great variety of methods by which one metal is separated from other metals, and the manner in which the same are alloyed I have explained partly in the eighth book of _De Natura Fossilium_, and partly I will explain elsewhere. Now I will proceed to the remainder of my subject.
END OF BOOK XI.
FOOTNOTES:
[1] The whole of this Book is devoted to the subject of the separation of silver from copper by liquation, except pages 530-9 on copper refining, and page 544 on the separation of silver from iron. We believe a brief outline of the liquation process here will refresh the mind of the reader, and enable him to peruse the Book with more satisfaction.
The fundamental principle of the process is that if a copper-lead alloy, containing a large excess of lead, be heated in a reducing atmosphere, above the melting point of lead but below that of copper, the lead will liquate out and carry with it a large proportion of the silver. As the results are imperfect, the process cannot be carried through in one operation, and a large amount of bye-products is created which must be worked up subsequently. The process, as here described, falls into six stages. 1st, Melting the copper and lead in a blast furnace to form "liquation cakes"--that is, the "leading." If the copper contain too little silver to warrant liquation directly, then the copper is previously enriched by melting and drawing off from a settling pot the less argentiferous "tops" from the metal, liquation cakes being made from the enriched "bottoms." 2nd, Liquation of the argentiferous lead from the copper. This work was carried out in a special furnace, to which the admission of air was prevented as much as possible in order to prevent oxidation. 3rd, "Drying" the residual copper, which retained some lead, in a furnace with a free admission of air. The temperature was raised to a higher degree than in the liquation furnace, and the expelled lead was oxidized. 4th, Cupellation of the argentiferous lead.
5th, Refining of the residual copper from the "drying" furnace by oxidation of impurities and poling in a "refining furnace." 6th, Re-alloy and re-liquation of the bye-products. These consist of: _a_, "slags" from "leading"; _b_, "slags" from "drying"; _c_, "slags" from refining of the copper. All of these "slags" were mainly lead oxides, containing some cuprous oxides and silica from the furnace linings; _d_, "thorns" from liquation; _e_, "thorns" from "drying"; _f_, "thorns" from skimmings during cupellation; these were again largely lead oxides, but contained rather more copper and less silica than the "slags"; _g_, "ash-coloured copper," being scales from the "dried" copper, were cuprous oxides, containing considerable lead oxides; _h_, concentrates from furnace accretions, crushed bricks, &c.
The discussion of detailed features of the process has been reserved to notes attached to the actual text, to which the reader is referred. As to the general result of liquation, Karsten (see below) estimates the losses in the liquation of the equivalent of 100 lbs. of argentiferous copper to amount to 32-35 lbs. of lead and 5 to 6 lbs. of copper. Percy (see below) quotes results at Lautenthal in the Upper Harz for the years 1857-60, showing losses of 25% of the silver, 9.1% of the copper, and 36.37 lbs. of lead to the 100 lbs. of copper, or say, 16% of the lead; and a cost of 8 6s. per ton of copper. The theoretical considerations involved in liquation have not been satisfactorily determined. Those who may wish to pursue the subject will find repeated descriptions and much discussion in the following works, which have been freely consulted in the notes which follow upon particular features of the process. It may be mentioned that Agricola's treatment of the subject is more able than any down to the 18th century. Ercker (_Beschreibung Allerfurnemsten Mineralischen_, etc., Prague, 1574). Lohneys (_Bericht vom Bergwercken_, etc., Zellerfeldt, 1617). Schluter (_Grundlicher Unterricht von Hutte-Werken_, Braunschweig, 1738). _Karsten_ (_System der Metallurgie V._ and _Archiv fur Bergbau und Huttenwesen_, 1st series, 1825).
Berthier (_Annales des Mines_, 1825, II.). Percy (Metallurgy of Silver and Gold, London, 1880).
NOMENCLATURE.--This process held a very prominent position in German metallurgy for over four centuries, and came to have a well-defined nomenclature of its own, which has never found complete equivalents in English, our metallurgical writers to the present day adopting more or less of the German terms. Agricola apparently found no little difficulty in adapting Latin words to his purpose, but stubbornly adhered to his practice of using no German at the expense of long explanatory clauses.
The following table, prepared for convenience in translation, is reproduced. The German terms are spelled after the manner used in most English metallurgies, some of them appear in Agricola's Glossary to _De Re Metallica_.
English. Latin. German.
Blast furnace _Prima fornax_ _Schmeltzofen_
Liquation furnace _Fornax in qua argentum et _Saigernofen_ plumb.u.m ab aere secernuntur_
Drying furnace _Fornax in qua aerei panes _Darrofen_ fathiscentes torrentur_
Refining hearth _Fornax in qua panes aerei _Gaarherd_ torrefacti coquuntur_
Cupellation _Secunda fornax_, or _Treibherd_ furnace _fornax in qua plumb.u.m ab argento separatur_
Leading _Mistura_ _Frischen_
Liquating _Stillare_, or _distillare_ _Saigern_
"Drying" _Torrere_ _Darren_
Refining _Aes ex panibus torrefactis _Gaarmachen_ conficere_ Liquation cakes _Panes ex aere ac plumbo misti_ _Saigerstock_
Exhausted _Panes fathiscentes_ _Kiehnstock_, liquation cakes or _Kinstocke_
"Dried" cakes _Panes torrefacti_ _Darrlinge_
Slags from leading _Recrementa_ _Frischschlacke_ (with explanatory phrases)
Slags from drying _Recrementa_ _Darrost_ (with explanatory phrases)
Slags from refining _Recrementa_ _Gaarschlacke_ (with explanatory phrases)
Liquation thorns _Spinae_ _Saigerdorner_, (with explanatory phrases) or _Rostdorner_
Thorns from "drying" _Spinae_ _Darrsohle_ (with explanatory phrases)
Thorns from _Spinae_ _Abstrich_ cupellation (with explanatory phrases)
Silver-lead or _Stannum_ _Saigerwerk_ or liquated _saigerblei_ silver-lead
Ash-coloured copper _Aes cinereum_ _Pickschiefer_ or _schifer_
Furnace accretions _Cadmiae_ _Offenbruche_ or "accretions"
HISTORICAL NOTE.--So far as we are aware, this is the first complete discussion of this process, although it is briefly mentioned by one writer before Agricola--that is, by Biringuccio (III, 5, 8), who wrote ten years before this work was sent to the printer. His account is very incomplete, for he describes only the bare liquation, and states that the copper is re-melted with lead and re-liquated until the silver is sufficiently abstracted. He neither mentions "drying" nor any of the bye-products. In his directions the silver-lead alloy was cupelled and the copper ultimately refined, obviously by oxidation and poling, although he omits the pole. In A.D. 1150 Theophilus (p. 305, Hendrie's Trans.) describes melting lead out of copper ore, which would be a form of liquation so far as separation of these two metals is concerned, but obviously not a process for separating silver from copper. This pa.s.sage is quoted in the note on copper smelting (Note on p. 405). A process of such well-developed and complicated a character must have come from a period long before Agricola; but further than such a surmise, there appears little to be recorded. Liquation has been during the last fifty years displaced by other methods, because it was not only tedious and expensive, but the losses of metal were considerable.
[2] _Paries_,--"Part.i.tion" or "wall." The author uses this term throughout in distinction to _murus_, usually applying the latter to the walls of the building and the former to furnace walls, chimney walls, etc. In order to gain clarity, we have introduced the term "hood" in distinction to "chimney," and so far as possible refer to the _paries_ of these constructions and furnaces as "side of the furnace," "side of the hood," etc.
[4] From this point on, the construction of the roofs, in the absence of ill.u.s.tration, is hopeless of intelligent translation. The constant repet.i.tion of "_tignum_," "_tigillum_," "_trabs_," for at least fifteen different construction members becomes most hopelessly involved, especially as the author attempts to distinguish between them in a sort of "House-that-Jack-built" arrangement of explanatory clauses.
[5] In the original text this is given as the "fifth," a manifest impossibility.
[6] _Chelae_,--"claws."
[7] If Roman weights, this would be 5.6 short tons, and 7.5 tons if German _centner_ is meant.
[8] This is, no doubt, a reference to Pliny's statement (x.x.xIII, 35) regarding litharge at Puteoli. This pa.s.sage from Pliny is given in the footnote on p. 466. Puteoli was situated on the Bay of Naples.
[9] By this expression is apparently meant the "bottoms" produced in enriching copper, as described on p. 510.
[10] The details of the preparation of liquation cakes--"leading"--were matters of great concern to the old metallurgists. The size of the cakes, the proportion of silver in the original copper and in the liquated lead, the proportion of lead and silver left in the residual cakes, all had to be reached by a series of compromises among militant forces. The cakes were generally two and one-half to three and one-half inches thick and about two feet in diameter, and weighed 225 to 375 lbs.
This size was wonderfully persistent from Agricola down to modern times; and was, no doubt, based on sound experience. If the cakes were too small, they required proportionately more fuel and labour; whilst if too large, the copper began to melt before the maximum lead was liquated.
The ratio of the copper and lead was regulated by the necessity of enough copper to leave a substantial sponge ma.s.s the shape of the original cake, and not so large a proportion as to imprison the lead.
That is, if the copper be in too small proportion the cakes break down; and if in too large, then insufficient lead liquates out, and the extraction of silver decreases. Ercker (p. 106-9) insists on the equivalent of about 3 copper to 9.5 lead; Lohneys (p. 99), 3 copper to 9 or 10 lead. Schluter (p. 479, etc.) insists on a ration of 3 copper to about 11 lead. Kerl (_Handbuch Der Metallurgischen Huttenkunde_, 1855; Vol. III., p. 116) gives 3 copper to 6 to 7 parts lead. Agricola gives variable amounts of 3 parts copper to from 8 to 12 parts lead. As to the ratio of silver in the copper, or to the cakes, there does not, except the limit of payability, seem to have been any difficulty on the minimum side. On the other hand, Ercker, Lohneys, Schluter, and Karsten all contend that if the silver ran above a certain proportion, the copper would retain considerable silver. These authors give the outside ratio of silver permissible for good results in one liquation at what would be equivalent to 45 to 65 ozs. per ton of cakes, or about 190 to 250 ozs.
per ton on the original copper. It will be seen, however, that Agricola's cakes greatly exceed these values. A difficulty did arise when the copper ran low in silver, in that the liquated lead was too poor to cupel, and in such case the lead was used over again, until it became rich enough for this purpose. According to Karsten, copper containing less than an equivalent of 80 to 90 ozs. per ton could not be liquated profitably, although the Upper Harz copper, according to Kerl, containing the equivalent of about 50 ozs. per ton, was liquated at a profit. In such a case the cakes would run only 12 to 14 ozs. per ton.
It will be noticed that in the eight cases given by Agricola the copper ran from 97 to over 580 ozs. per ton, and in the description of enrichment of copper "bottoms" the original copper runs 85 ozs., and "it cannot be separated easily"; as a result, it is raised to 110 ozs. per ton before treatment. In addition to the following tabulation of the proportions here given by Agricola, the reader should refer to footnotes 15 and 17, where four more combinations are tabulated. It will be observed from this table that with the increasing richness of copper an increased proportion of lead was added, so that the products were of similar value. It has been a.s.sumed (see footnote 13 p. 509), that Roman weights are intended. It is not to be expected that metallurgical results of this period will "tie up" with the exactness of the modern operator's, and it has not been considered necessary to calculate beyond the nearest pennyweight. Where two or more values are given by the author the average has been taken.
1ST CHARGE. 2ND CHARGE. 3RD CHARGE. 4TH CHARGE.
De Re Metallica Part 50
You're reading novel De Re Metallica Part 50 online at LightNovelFree.com. You can use the follow function to bookmark your favorite novel ( Only for registered users ). If you find any errors ( broken links, can't load photos, etc.. ), Please let us know so we can fix it as soon as possible. And when you start a conversation or debate about a certain topic with other people, please do not offend them just because you don't like their opinions.
De Re Metallica Part 50 summary
You're reading De Re Metallica Part 50. This novel has been translated by Updating. Author: Georgius Agricola already has 657 views.
It's great if you read and follow any novel on our website. We promise you that we'll bring you the latest, hottest novel everyday and FREE.
LightNovelFree.com is a most smartest website for reading novel online, it can automatic resize images to fit your pc screen, even on your mobile. Experience now by using your smartphone and access to LightNovelFree.com
- Related chapter:
- De Re Metallica Part 49
- De Re Metallica Part 51
RECENTLY UPDATED NOVEL

The King of Hell's Genius Pampered Wife
The King of Hell's Genius Pampered Wife Chapter 1928: Accepted! View : 2,732,494
A Demon Lord's Tale: Dungeons, Monster Girls, and Heartwarming Bliss
A Demon Lord's Tale: Dungeons, Monster Girls, and Heartwarming Bliss Chapter 574 View : 1,365,609
Eternal Life Begins with Taking a Wife
Eternal Life Begins with Taking a Wife Chapter 1153: Mysterious Exotic Beast (1) View : 410,679
Cultivation: Start From Simplifying Martial Arts Techniques
Cultivation: Start From Simplifying Martial Arts Techniques Chapter 1092: Chapter 1048 Stepping Stone View : 621,160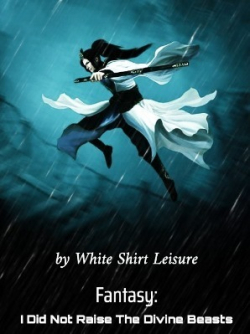
Fantasy: I Did Not Raise The Divine Beasts
Fantasy: I Did Not Raise The Divine Beasts Chapter 1111: These Are All Trash (1) View : 387,902