De Re Metallica Part 52
You’re reading novel De Re Metallica Part 52 online at LightNovelFree.com. Please use the follow button to get notification about the latest chapter next time when you visit LightNovelFree.com. Use F11 button to read novel in full-screen(PC only). Drop by anytime you want to read free – fast – latest novel. It’s great if you could leave a comment, share your opinion about the new chapters, new novel with others on the internet. We’ll do our best to bring you the finest, latest novel everyday. Enjoy!
liquation cakes per ton
Weight of liquation 169.4 lbs.
thorns
Average value of 18 ozs.
the liquation 4dwts.
thorns per ton
Extraction of 71% silver into the liquated lead
[18] For the liquation it was necessary to maintain a reducing atmosphere, otherwise the lead would oxidize; this was secured by keeping the cakes well covered with charcoal and by preventing the entrance of air as much as possible. Moreover, it was necessary to preserve a fairly even temperature. The proportions of copper and lead in the three liquation products vary considerably, depending upon the method of conducting the process and the original proportions. From the authors consulted (see note p. 492) an average would be about as follows:--The residual copper--exhausted liquation cakes--ran from 25 to 33% lead; the liquated lead from 2 to 3% copper; and the liquation thorns, which were largely oxidized, contained about 15% copper oxides, 80% lead oxides, together with impurities, such as antimony, a.r.s.enic, etc. The proportions of the various products would obviously depend upon the care in conducting the operation; too high temperature and the admission of air would increase the copper melted and oxidize more lead, and thus increase the liquation thorns. There are insufficient data in Agricola to adduce conclusions as to the actual ratios produced. The results given for the 6th charge (note 17, p. 512) would indicate about 30% lead in the residual copper, and would indicate that the original charge was divided into about 24% of residual copper, 18% of liquation thorns, and 57% of liquated lead. This, however, was an unusually large proportion of liquation thorns, some of the authors giving instances of as low as 5%.
[19] The first instance given, of 44 _centumpondia_ (3,109 lbs.) lead and one _centumpondium_ (70.6 lbs.) copper, would indicate that the liquated lead contained 2.2% copper. The second, of 46 _centumpondia_ (3,250 lbs.) lead and 1-1/2 _centumpondia_ copper (106 lbs.), would indicate 3% copper; and in the third, 120 _centumpondia_ (8,478 lbs.) lead and six copper (424 lbs.) would show 4.76% copper. This charge of 120 _centumpondia_ in the cupellation furnace would normally make more than 110 _centumpondia_ of litharge and 30 of hearth-lead, _i.e._, saturated furnace bottoms. The copper would be largely found in the silver-lead "which does not melt," at the margin of the crucible. These skimmings are afterward referred to as "thorns." It is difficult to understand what is meant by the expression that the silver which is in the copper is mixed with the remaining (_reliquo_) silver. The coppery skimmings from the cupellation furnace are referred to again in Note 28, p. 539.
[20] A further amount of lead could be obtained in the first liquation, but a higher temperature is necessary, which was more economical to secure in the "drying" furnace. Therefore, the "drying" was really an extension of liquation; but as air was admitted the lead and copper melted out were oxidized. The products were the final residual copper, called by Agricola the "dried" copper, together with lead and copper oxides, called by him the "slags," and the scale of copper and lead oxides termed by him the "ash-coloured copper." The German metallurgists distinguished two kinds of slag: the first and princ.i.p.al one, the _darrost_, and the second the _darrsohle_, this latter differing only in that it contained more impurities from the floor of the furnace, and remained behind until the furnace cooled. Agricola possibly refers to these as "more liquation thorns," because in describing the treatment of the bye-products he refers to thorns from the process, whereas in the description of "drying" he usually refers to "slags." A number of a.n.a.lyses of these products, given by Karsten, show the "dried" copper to contain from 82.7 to 90.6% copper, and from 9.4 to 17.3% lead; the "slag" to contain 76.5 to 85.1% lead oxide, and from 4.1 to 7.8% cuprous oxide, with 9 to 13% silica from the furnace bottoms, together with some other impurities; the "ash-coloured copper" to contain about 60% cuprous oxide and 30% lead oxide, with some metallic copper and minor impurities. An average of proportions given by various authors shows, roughly, that out of 100 _centners_ of "exhausted" liquation cakes, containing about 70% copper and 30% lead, there were about 63 _centners_ of "dried" copper, 38 _centners_ of "slag," and 6-1/2 _centners_ of "ash-coloured copper." According to Karsten, the process fell into stages; first, at low temperature some metallic lead appeared; second, during an increasing temperature for over 14 to 15 hours the slags ran out; third, there was a period of four hours of lower temperature to allow time for the lead to diffuse from the interior of the cakes; and fourth, during a period of eight hours the temperature was again increased. In fact, the latter portion of the process ended with the economic limit between leaving some lead in the copper and driving too much copper into the "slags." Agricola gives the silver contents of the "dried" copper as 3 _drachmae_ to 1 _centumpondium_, or equal to about 9 ozs. per ton; and a.s.suming that the copper finally recovered from the bye-products ran no higher, then the first four charges (see note on p.
506) would show a reduction in the silver values of from 95 to 97%; the 7th and 8th charges (note on p. 512) of about 90%.
[21] If Roman weights, this would equal from 6,360 lbs. to 7,066 lbs.
[22] One half _uncia_, or three _drachmae_ of silver would equal either 12 ozs. or 9 ozs. per ton. If we a.s.sume the values given for residual copper in the first four charges (note p. 506) of 34 ozs., this would mean an extraction of, roughly, 65% of the silver from the exhausted liquation cakes.
[23] See note 29, p. 540.
[24]
a.s.suming Roman weights: 2 _centumpondia_ = 141.3 lbs.
2-1/2 " = 176.6 "
3 " = 211.9 "
3-1/2 " = 248.2 "
6 " = 423.9 "
[25] This description of refining copper in an open hearth by oxidation with a blast and "poling"--the _gaarmachen_ of the Germans--is so accurate, and the process is so little changed in some parts of Saxony, that it might have been written in the 20th century instead of the 16th.
The best account of the old practice in Saxony after Agricola is to be found in Schluter's _Hutte Werken_ (Braunschweig, 1738, Chap. CXVIII.).
The process has largely been displaced by electrolytic methods, but is still in use in most refineries as a step in electrolytic work. It may be unnecessary to repeat that the process is one of subjecting the molten ma.s.s of impure metal to a strong and continuous blast, and as a result, not only are the impurities to a considerable extent directly oxidized and taken off as a slag, but also a considerable amount of copper is turned into cuprous oxide. This cuprous oxide mostly melts and diffuses through the metallic copper, and readily parting with its oxygen to the impurities further facilitates their complete oxidation.
The blast is continued until the impurities are practically eliminated, and at this stage the molten metal contains a great deal of dissolved cuprous oxide, which must be reduced. This is done by introducing a billet of green wood ("poling"), the dry distillation of which generates large quant.i.ties of gases, which reduce the oxide. The state of the metal is even to-day in some localities tested by dipping into it the point of an iron rod; if it be at the proper state the adhering copper has a net-like appearance, should be easily loosened from the rod by dipping in water, is of a reddish-copper colour and should be quite pliable; if the metal is not yet refined, the sample is thick, smooth, and detachable with difficulty; if over-refined, it is thick and brittle. By allowing water to run on to the surface of the molten metal, thin cakes are successively formed and taken off. These cakes were the article known to commerce over several centuries as "rosetta copper."
The first few cakes are discarded as containing impurities or slag, and if the metal be of good quality the cakes are thin and of a red colour.
Their colour and thinness, therefore, become a criterion of purity. The cover of charcoal or charcoal dust maintained upon the surface of the metal tended to r.e.t.a.r.d oxidation, but prevented volatilization and helped to secure the impurities as a slag instead. Karsten (_Archiv._, 1st series, p. 46) gives several a.n.a.lyses of the slag from refining "dried" copper, showing it to contain from 51.7 to 67.4% lead oxide, 6.2 to 19.2% cuprous oxide, and 21.4 to 23.9 silica (from the furnace bottoms), with minor quant.i.ties of iron, antimony, etc. The "bubbles"
referred to by Agricola were apparently the shower of copper globules which takes place upon the evolution of sulphur dioxide, due to the reaction of the cuprous oxide upon any remaining sulphide of copper when the ma.s.s begins to cool.
HISTORICAL NOTE.--It is impossible to say how the Ancients refined copper, beyond the fact that they often re-smelted it. Such notes as we can find are set out in the note on copper smelting (note 42, p. 402).
The first authentic reference to poling is in Theophilus (1150 to 1200 A.D., Hendrie's translation, p. 313), which shows a very good understanding of this method of refining copper:--"Of the Purification of Copper. Take an iron dish of the size you wish, and line it inside and out with clay strongly beaten and mixed, and it is carefully dried.
Then place it before a forge upon the coals, so that when the bellows act upon it the wind may issue partly within and partly above it, and not below it. And very small coals being placed round it, place the copper in it equally, and add over it a heap of coals. When by blowing a long time this has become melted, uncover it and cast immediately fine ashes of coals over it, and stir it with a thin and dry piece of wood as if mixing it, and you will directly see the burnt lead adhere to these ashes like a glue, which being cast out again superpose coals, and blowing for a long time, as at first, again uncover it, and then do as you did before. You do this until at length by cooking it you can withdraw the lead entirely. Then pour it over the mould which you have prepared for this, and you will thus prove if it be pure. Hold it with the pincers, glowing as it is, before it has become cold, and strike it with a large hammer strongly over the anvil, and if it be broken or split you must liquefy it anew as before. If, however, it should remain sound, you will cool it in water, and you cook other (copper) in the same manner." Biringuccio (III, 8) in 1540 describes the process briefly, but omits the poling, an essential in the production of malleable copper.
[26] _Pompholyx_ and _spodos_ were impure zinc oxides (see note 26, p.
394).
The copper flowers were no doubt cupric oxide. They were used by the Ancients for medicinal purposes. Dioscorides (V, 48) says: "Of flowers of copper, which some call the sc.r.a.pings of old nails, the best is friable; it is gold-coloured when rubbed, is like millet in shape and size, is moderately bright, and somewhat astringent. It should not be mixed with copper filings, with which it is often adulterated. But this deception is easily detected, for when bitten in the teeth the filings are malleable. It (the flowers) is made when the copper fused in a furnace has run into the receptacle through the spout pertaining to it, for then the workmen engaged in this trade cleanse it from dirt and pour clear water over it in order to cool it; from this sudden condensation the copper spits and throws out the aforesaid flowers." Pliny (x.x.xIV, 24) says: "The flower, too, of copper (_aeris flos_) is used in medicine.
This is made by fusing copper, and then removing it to another furnace, where the repeated blast makes the metal separate into small scales like millet, known as flowers. These scales also fall off when the cakes of metal are cooled in water; they become red, too, like the scales of copper known as '_lepis_,' by use of which the flowers of copper are adulterated, it being also sold for it. These are made when hammering the nails that are made from the cakes of copper. All these methods are carried on in the works of Cyprus; the difference between these substances is that the _squamae_ (copper scales) are detached from hammering the cakes, while the flower falls off spontaneously." Agricola (_De Nat. Fos._, p. 352) notes that "flowers of copper (_flos aeris_) have the same properties as 'roasted copper.'"
[27] It seems scarcely necessary to discuss in detail the complicated "flow scheme" of the various minor bye-products. They are all re-introduced into the liquation circuit, and thereby are created other bye-products of the same kind _ad infinitum_. Further notes are given on:--
Liquation thorns Note 28.
Slags " 30.
Ash-coloured copper " 29.
Concentrates " 33.
_Cadmia_ " 32.
There are no data given, either by Agricola or the later authors, which allow satisfactory calculation of the relative quant.i.ties of these products. A rough estimate from the data given in previous notes would indicate that in one liquation only about 70% of the original copper came out as refined copper, and that about 70% of the original lead would go to the cupellation furnace, _i.e._, about 30% of the original metal sent to the blast furnace would go into the "thorns," "slags," and "ash-coloured copper." The ultimate losses were very great, as given before (p. 491), they probably amounted to 25% of the silver, 9% copper, and 16% of the lead.
[28] There were the following cla.s.ses of thorns:--
1st. From liquation.
2nd. From drying.
3rd. From cupellation.
In a general way, according to the later authors, they were largely lead oxide, and contained from 5% to 20% cuprous oxide. If a calculation be made backward from the products given as the result of the charge described, it would appear that in this case they must have contained at least one-fifth copper. The silver in these liquation cakes would run about 24 ozs. per ton, in the liquated lead about 36 ozs. per ton, and in the liquation thorns 24 ozs. per ton. The extraction into the liquated lead would be about 80% of the silver.
[29] The "ash-coloured copper" is a cuprous oxide, containing some 3% lead oxide; and if Agricola means they contained two _unciae_ of silver to the _centumpondium_, then they ran about 48 ozs. per ton, and would contain much more silver than the ma.s.s.
[30] There are three princ.i.p.al "slags" mentioned--
1st. Slag from "leading."
2nd. Slag from "drying."
3rd. Slag from refining the copper.
From the a.n.a.lyses quoted by various authors these ran from 52% to 85% lead oxide, 5% to 30% cuprous oxide, and considerable silica from the furnace bottoms. They were reduced in the main into liquation cakes, although Agricola mentions instances of the metal reduced from "slags"
being taken directly to the "drying" furnace. Such liquation cakes would run very low in silver, and at the values given only averaged 12 ozs.
per ton; therefore the liquated lead running the same value as the cakes, or less than half that of the "poor" lead mentioned in Note 17, p. 512, could not have been cupelled directly.
[31] See Note 16, p. 511, for discussion of yellow and _caldarium_ copper.
[32] This _cadmia_ is given in the Glossary and the German translation as _kobelt_. A discussion of this substance is given in the note on p.
112; and it is sufficient to state here that in Agricola's time the metal cobalt was unknown, and the substances designated _cadmia_ and _cobaltum_ were a.r.s.enical-cobalt-zinc minerals. A metal made from "slag"
from refining, together with "base" thorns, would be very impure; for the latter, according to the paragraph on concentrates a little later on, would contain the furnace accretions, and would thus be undoubtedly zincky. It is just possible that the term _kobelt_ was used by the German smelters at this time in the sense of an epithet--"black devil"
(see Note 21, p. 214).
[33] It is somewhat difficult to see exactly the meaning of base (_vile_) and precious (_preciosum_) in this connection. While "base"
could mean impure, "precious" could hardly mean pure, and while "precious" could mean high value in silver, the reverse does not seem entirely _apropos_. It is possible that "bad" and "good" would be more appropriate terms.
[34] The skimmings from the molten lead in the early stages of cupellation have been discussed in Note 28, p. 539. They are probably called thorns here because of the large amount of copper in them. The lead from liquation would contain 2% to 3% of copper, and this would be largely recovered in these skimmings, although there would be some copper in the furnace bottoms--hearth-lead--and the litharge. These "thorns" are apparently fairly rich, four _unciae_ to the _centumpondium_ being equivalent to about 97 ozs. per ton, and they are only added to low-grade liquation material.
[35] _Particulis aeris tusi_. Unless this be the fine concentrates from crus.h.i.+ng the material mentioned, we are unable to explain the expression.
[36] This operation would bring down a b.u.t.ton of antimony under an iron matte, by de-sulphurizing the antimony. It would seem scarcely necessary to add lead before cupellation. This process is given in an a.s.say method, in the _Probierbuchlein_ (folio 31) 50 years before _De Re Metallica_: "How to separate silver from iron: Take that silver which is in iron _plechen_ (_plachmal_), pulverize it finely, take the same iron or _plec_ one part, _spiesglasz_ (antimony sulphide) one part, leave them to melt in a crucible placed in a closed _windtofen_. When it is melted, let it cool, break the crucible, chip off the b.u.t.ton that is in the bottom, and melt it in a crucible with as much lead. Then break the crucible, and seek from the b.u.t.ton in the cupel, and you will find what silver it contains."
De Re Metallica Part 52
You're reading novel De Re Metallica Part 52 online at LightNovelFree.com. You can use the follow function to bookmark your favorite novel ( Only for registered users ). If you find any errors ( broken links, can't load photos, etc.. ), Please let us know so we can fix it as soon as possible. And when you start a conversation or debate about a certain topic with other people, please do not offend them just because you don't like their opinions.
De Re Metallica Part 52 summary
You're reading De Re Metallica Part 52. This novel has been translated by Updating. Author: Georgius Agricola already has 652 views.
It's great if you read and follow any novel on our website. We promise you that we'll bring you the latest, hottest novel everyday and FREE.
LightNovelFree.com is a most smartest website for reading novel online, it can automatic resize images to fit your pc screen, even on your mobile. Experience now by using your smartphone and access to LightNovelFree.com
- Related chapter:
- De Re Metallica Part 51
- De Re Metallica Part 53
RECENTLY UPDATED NOVEL

The King of Hell's Genius Pampered Wife
The King of Hell's Genius Pampered Wife Chapter 1928: Accepted! View : 2,732,510
A Demon Lord's Tale: Dungeons, Monster Girls, and Heartwarming Bliss
A Demon Lord's Tale: Dungeons, Monster Girls, and Heartwarming Bliss Chapter 574 View : 1,365,615
Eternal Life Begins with Taking a Wife
Eternal Life Begins with Taking a Wife Chapter 1153: Mysterious Exotic Beast (1) View : 410,703
Cultivation: Start From Simplifying Martial Arts Techniques
Cultivation: Start From Simplifying Martial Arts Techniques Chapter 1092: Chapter 1048 Stepping Stone View : 621,173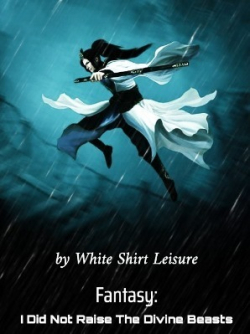
Fantasy: I Did Not Raise The Divine Beasts
Fantasy: I Did Not Raise The Divine Beasts Chapter 1111: These Are All Trash (1) View : 387,915