Aviation Engines Part 29
You’re reading novel Aviation Engines Part 29 online at LightNovelFree.com. Please use the follow button to get notification about the latest chapter next time when you visit LightNovelFree.com. Use F11 button to read novel in full-screen(PC only). Drop by anytime you want to read free – fast – latest novel. It’s great if you could leave a comment, share your opinion about the new chapters, new novel with others on the internet. We’ll do our best to bring you the finest, latest novel everyday. Enjoy!
The form of caliper shown at B is an outside caliper. Those at C and D are special forms for inside and outside work, the former being used, if desired, as a divider, while the latter may be employed for measuring the walls of tubing. The calipers at E are simple forms, having a friction joint to distinguish them from the spring calipers shown at B, C and D. In order to permit of ready adjustment of a spring caliper, a split nut as shown at G is sometimes used. A solid nut caliper can only be adjusted by s.c.r.e.w.i.n.g the nut in or out on the screw, which may be a tedious process if the caliper is to be set from one extreme to the other several times in succession. With a slip nut as shown at G it is possible to slip it from one end of the thread to the other without turning it, and of locking it in place at any desired point by simply allowing the caliper leg to come in contact with it. The method of adjusting a spring caliper is shown at Fig. 174, H.
Among the most common of the machinist's tools are those used for linear measurements. The usual forms are shown in group, Fig. 175. The most common tool, which is widely known, is the carpenter's folding two-foot rule or the yardstick. While these are very convenient for taking measurements where great accuracy is not required, the machinist must work much more accurately than the carpenter, and the standard steel scale which is shown at D, is a popular tool for the machinist. The steel scale is in reality a graduated straight edge and forms an important part of various measuring tools. These are made of high grade steel and vary from 1 to 48 inches in length. They are carefully hardened in order to preserve the graduations, and all surfaces and edges are accurately ground to insure absolute parallelism. The graduations on the high grade scales are produced with a special device known as a dividing engine, but on cheaper scales, etching suffices to provide a fairly accurate graduation. The steel scales may be very thin and flexible, or may be about an eighth of an inch thick on the twelve-inch size, which is that commonly used with combination squares, protractors and other tools of that nature. The repairman's scale should be graduated both with the English system, in which the inches are divided into eighths, sixteenths, thirty-secondths and sixty-fourths, and also in the metric system, divided into millimeters and centimeters. Some machinists use scales graduated in tenths, twentieths, fiftieths and hundredths. This is not as good a system of graduation as the more conventional one first described.
[Ill.u.s.tration: Fig. 175.--Measuring Appliances for the Machinist and Floor Man.]
Some steel scales are provided with a slot or groove cut the entire length on one side and about the center of the scales. This permits the attachment of various fittings such as the protractor head, which enables the machinist to measure angles, or in addition the heads convert the scale into a square or a tool permitting the accurate bisecting of pieces of circular section. Two scales are sometimes joined together to form a right angle, such as shown at Fig. 175, C. This is known as a square and is very valuable in ascertaining the truth of vertical pieces that are supposed to form a right angle with a base piece.
The Vernier is a device for reading finer divisions on a scale than those into which the scale is divided. Sixty-fourths of an inch are about the finest division that can be read accurately with the naked eye. When fine work is necessary a Vernier is employed. This consists essentially of two rules so graduated that the true scale has each inch divided into ten equal parts, the upper or Vernier portion has ten divisions occupying the same s.p.a.ce as nine of the divisions of the true scale. It is evident, therefore, that one of the divisions of the Vernier is equal to nine-tenths of one of those on the true scale. If the Vernier scale is moved to the right so that the graduations marked "1" shall coincide, it will have moved one-tenth of a division on the scale or one-hundredth of an inch. When the graduations numbered 5 coincide the Vernier will have moved five-hundredths of an inch; when the lines marked 0 and 10 coincide, the Vernier will have moved nine-hundredths of an inch, and when 10 on the Vernier comes opposite 10 on the scales, the upper rule will have moved ten-hundredths of an inch, or the whole of one division on the scale. By this means the scale, though it may be graduated only to tenths of an inch, may be accurately set at points with positions expressed in hundredths of an inch. When graduated to read in thousandths, the true scale is divided into fifty parts and the Vernier into twenty parts. Each division of the Vernier is therefore equal to nineteen-twentieths of one of the true scale. If the Vernier be moved so the lines of the first division coincide, it will have moved one-twentieth of one-fiftieth, or .001 inch. The Vernier principle can be readily grasped by studying the section of the Vernier scale and true scale shown at Fig. 176, A.
[Ill.u.s.tration: Fig. 176.--At Left, Special Form of Vernier Caliper for Measuring Gear Teeth; at Right, Micrometer for Accurate Internal Measurements.]
The caliper scale which is shown at Fig. 175, A, permits of taking the over-all dimension of any parts that will go between the jaws. This scale can be adjusted very accurately by means of a fine thread screw attached to a movable jaw and the divisions may be divided by eye into two parts if one sixty-fourth is the smallest of the divisions. A line is indicated on the movable jaw and coincides with the graduations on the scale. As will be apparent, if the line does not coincide exactly with one of the graduations it will be at some point between the lines and the true measurement may be approximated without trouble.
A group of various other measuring tools of value to the machinist is shown at Fig. 177. The small scale at A is termed a "center gauge,"
because it can be used to test the truth of the taper of either a male or female lathe center. The two smaller nicks, or v's, indicate the shape of a standard thread, and may be used as a guide for grinding the point of a thread-cutting tool. The cross level which is shown at B is of marked utility in erecting, as it will indicate absolutely if the piece it is used to test is level. It will indicate if the piece is level along its width as well as its length.
[Ill.u.s.tration: Fig. 177.--Measuring Appliances of Value in Airplane Repair Work.]
A very simple attachment for use with a scale that enables the machinist to scribe lines along the length of a cylindrical piece is shown at Fig.
177, C. These are merely small wedge-shaped clamps having an angular face to rest upon the bars. The thread pitch gauge which is shown at Fig. 177, D, is an excellent pocket tool for the mechanic, as it is often necessary to determine without loss of time the pitch of the thread on a bolt or in a nut. This consists of a number of leaves having serrations on one edge corresponding to the standard thread it is to be used in measuring. The tool shown gives all pitches up to 48 threads per inch. The leaves may be folded in out of the way when not in use, and their shape admits of their being used in any position without the remainder of the set interfering with the one in use. The fine pitch gauges have slim, tapering leaves of the correct shape to be used in finding the pitch of small nuts. As the tool is round when the leaves are folded back out of the way, it is an excellent pocket tool, as there are no sharp corners to wear out the pocket. Practical application of a Vernier having measuring heads of special form for measuring gear teeth is shown at Fig. 176, A. As the action of this tool has been previously explained, it will not be necessary to describe it further.
MICROMETER CALIPERS AND THEIR USE
Where great accuracy is necessary in taking measurements the micrometer caliper, which in the simple form will measure easily .001 inch (one-thousandth part of an inch) and when fitted with a Vernier that will measure .0001 inch (one ten-thousandth part of an inch), is used.
The micrometer may be of the caliper form for measuring outside diameters or it may be of the form shown at Fig. 176, B, for measuring internal diameters. The operation of both forms is identical except that the internal micrometer is placed inside of the bore to be measured while the external form is used just the same as a caliper. The form outlined will measure from one and one-half to six and a half inches as extension points are provided to increase the range of the instrument.
The screw has a movement of one-half inch and a hardened anvil is placed in the end of the thimble in order to prevent undue wear at that point.
The extension points or rods are accurately made in standard lengths and are screwed into the body of the instrument instead of being pushed in, this insuring firmness and accuracy. Two forms of micrometers for external measurements are shown at Fig. 178. The top one is graduated to read in thousandths of an inch, while the lower one is graduated to indicate hundredths of a millimeter. The mechanical principle involved in the construction of a micrometer is that of a screw free to move in a fixed nut. An opening to receive the work to be measured is provided by the backward movement of the thimble which turns the screw and the size of the opening is indicated by the graduations on the barrel.
[Ill.u.s.tration: Fig. 178.--Standard Forms of Micrometer Caliper for External Measurements.]
The article to be measured is placed between the anvil and spindle, the frame being held stationary while the thimble is revolved by the thumb and finger. The pitch of the screw thread on the concealed part of the spindle is 40 to an inch. One complete revolution of the spindle, therefore, moves it longitudinally one-fortieth, or twenty-five thousandths of an inch. As will be evident from the development of the scale on the barrel of the inch micrometer, the sleeve is marked with forty lines to the inch, each of these lines indicating twenty-five thousandths. The thimble has a beveled edge which is graduated into twenty-five parts. When the instrument is closed the graduation on the beveled edge of the thimble marked 0 should correspond to the 0 line on the barrel. If the micrometer is rotated one full turn the opening between the spindle and anvil will be .025 inch. If the thimble is turned only one graduation, or one twenty-fifth of a revolution, the opening between the spindle and anvil will be increased only by .001 inch (one-thousandth of an inch).
As many of the dimensions of the airplane parts, especially of those of foreign manufacture or such parts as ball and roller bearings, are based on the metric system, the competent repairman should possess both inch and metric micrometers in order to avoid continual reference to a table of metric equivalents. With a metric micrometer there are fifty graduations on the barrel, these representing .01 of a millimeter, or approximately .004 inch. One full turn of the barrel means an increase of half a millimeter, or .50 mm. (fifty one-hundredths). As it takes two turns to augment the s.p.a.ce between the anvil and the stem by increments of one millimeter, it will be evident that it would not be difficult to divide the s.p.a.ces on the metric micrometer thimble in halves by the eye, and thus the average workman can measure to .0002 inch plus or minus without difficulty. As set in the ill.u.s.tration, the metric micrometers show a s.p.a.ce of 13.5 mm., or about one millimeter more than half an inch. The inch micrometer shown is set to five-tenths or five hundred one-thousandths or one-half inch. A little study of the foregoing matter will make it easy to understand the action of either the inch or metric micrometer.
Both of the micrometers shown have a small knurled k.n.o.b at the end of the barrel. This controls the ratchet stop, which is a device that permits a ratchet to slip by a pawl when more than a certain amount of pressure is applied, thereby preventing the measuring spindle from turning further and perhaps springing the instrument. A simple rule that can be easily memorized for reading the inch micrometer is to multiply the number of vertical divisions on the sleeve by 25 and add to that the number of divisions on the bevel of the thimble reading from the zero to the line which coincides with the horizontal line on the sleeve. For example: if there are ten divisions visible on the sleeve, multiply this number by 25, then add the number of divisions shown on the bevel of the thimble, which is 10. The micrometer is therefore opened 10 25 equals 250 plus 10 equals 260 thousandths.
Micrometers are made in many sizes, ranging from those having a maximum opening of one inch to special large forms that will measure forty or more inches. While it is not to be expected that the repairman will have use for the big sizes, if a caliper having a maximum opening of six inches is provided with a number of extension rods enabling one to measure smaller objects, practically all of the measuring needed in repairing engine parts can be made accurately. Two or three smaller micrometers having a maximum range of two or three inches will also be found valuable, as most of the measurements will be made with these tools which will be much easier to handle than the larger sizes.
TYPICAL TOOL OUTFITS
The equipment of tools necessary for repairing airplane engines depends entirely upon the type of the power plant and while the common hand tools can be used on all forms, the work is always facilitated by having special tools adapted for reaching the nuts and screws that would be hard to reach otherwise. Special spanners and socket wrenches are very desirable. Then again, the nature of the work to be performed must be taken into consideration. Rebuilding or overhauling an engine calls for considerably more tools than are furnished for making field repairs or minor adjustments. A complete set of tools supplied to men working on Curtiss OX-2 engines and JN-4 training biplanes is shown at Fig. 179.
The tools are placed in a special box provided with a hinged cover and are arranged in the systematic manner outlined. The various tools and supplies shown are: A, hacksaw blades; B, special socket wrenches for engine bolts and nuts; C, ball pein hammers, four sizes; D, five a.s.sorted sizes of screw drivers ranging from very long for heavy work to short and small for fine work; E, seven pairs of pliers including combination in three sizes, two pairs of cutting pliers and one round nose; F, two split pin extractors and spreaders; G, wrench set including three adjustable monkey wrenches, one Stillson or pipe wrench, five sizes adjustable end wrenches and ten double end S wrenches; H, set of files, including flat, three cornered and half round; I, file brush; J, chisel and drift pin; K, three small punches or drifts; L, hacksaw frame; M, soldering copper; N, special spanners for propeller retaining nuts; O, special spanners; P, socket wrenches, long handle; Q, long handle, stiff bristle brushes for cleaning motor; R, gasoline blow torch; S, hand drill; T, spools of safety wire; U, flash lamp; V, special puller and castle wrenches; W, oil can; X, large adjustable monkey wrench; Y, washer and gasket cutter; Z, ball of heavy twine. In addition to the tools, various supplies, such as soldering acid, solder, sh.e.l.lac, valve grinding compound, bolts and nuts, split pins, washers, wood screws, etc., are provided.
[Ill.u.s.tration: Fig. 179.--Special Tools for Maintaining Curtiss OX-2 Motor Used in Curtiss JN-4 Training Biplane.]
SPECIAL HALL-SCOTT TOOLS
NO. TOOL DIRECTIONS FOR USE 1 Engine hoisting hook, 6-cylinder Hook under cam-shaft housing, when hoisting engine.
2 Engine hoisting hook, 4-cylinder Hook under cam-shaft housing, when hoisting engine.
3 Water plug wrench For use on water plugs on top and end of cylinders.
4 Vertical shaft f.l.a.n.g.e puller For pulling lower pinion shaft f.l.a.n.g.e from shaft. (Used on A-5 and A-7 engines only.) 5 Oil gun For general lubrication use.
6 Magneto gear puller For pulling magneto gears from magneto shaft.
7 Socket wrench, 1/4" A.L.A.M. For use on bolts and nuts on crank cases.
8 Socket wrench, 1/4" A.L.A.M For use on crank cases and magneto gear housings.
9 Socket wrench, 1/4" A.L.A.M. For use on magneto gear housings.
10 Socket wrench, 3/8" standard For bolts and nuts which fasten magnetos to crank-case.
11 Socket wrench, 1/4" A.L.A.M. For use on magneto gear housings.
12 Vertical shaft gear puller For removing water pump and magneto drive gear.
13 Brace and facing cutter For facing lugs on cylinders for cylinder hold down stud washers.
14 Handle for brace Use with brace.
15 Valve grinding brace For grinding in valves.
16 Socket wrench base, 3/8" A.L.A.M. For thrust bearing cap screws.
17 Brace and facing cutter, 5/16" For facing lugs on rocker arm A.L.A.M. covers.
18 Valve grinding screw driver For grinding in valves.
19 Valve spring tool For putting on and taking off valve springs.
20 Block-valve spring tool For use with valve spring tool.
21 Socket wrench, 5/8" A.L.A.M. For main bearing nuts.
22 Socket wrench, 1/4" A.L.A.M. For use on cam-shaft housing.
23 Socket wrench, 5/16" A.L.A.M. For cam-shaft housing hold down stud nuts.
24 Socket wrench, 1/2" A.L.A.M. For cylinder hold down stud nuts.
25 Socket wrench, 5/16" A.L.A.M. For carburetor and water pump bolts and nuts.
26 Socket wrench, 5/16" A.L.A.M. For carburetor and water pump bolts and nuts.
27 Socket wrench For use on carburetor jets.
28 Magneto screw driver For general magneto use.
29 Bra.s.s bar, 1" diameter 7" long For driving piston pins from pistons.
30 Hack saw For general use.
31 Oil can For cam-shaft housing lubrication.
32 Gasoline or distillate can For priming or other use.
33 Oil can For magneto gear lubrication.
34 Sh.e.l.lac can For rubber hose connections and gaskets.
35 Magneto cleaner For use on magnetos.
36 Clamps For holding cylinder hold down studs, when fitting main bearings.
37 Piston guards For use in pistons, when out of engine, to protect them.
38 Screw driver For general use.
39 Vertical shaft clamps For clamping vertical shaft f.l.a.n.g.es, when timing engine.
40 Thrust adjusting nut wrench For adjusting propeller thrust bearing.
41 Stuffing box spanner wrench For adjusting stuffing box nut on vertical shaft.
42 Water pump spanner wrench For adjusting water pump stuffing nut.
43 Wrench For use on cylinder relief c.o.c.ks and cylinder priming c.o.c.ks.
44 Hose clamp wrench For use on hose clamps.
45 Sc.r.a.per For cleaning piston ring grooves on pistons.
46 Crank-shaft nut wrench For adjusting crank-shaft nut.
47 Spark-plug wrench For putting in and taking out spark-plugs in cylinders.
48 Timing disc (single disc) For use on crank-shaft to time engine.
Specify type motor disc should be made for. If double disc is required, specify the two types of motors the disc is to be made for. Double disc.
Aviation Engines Part 29
You're reading novel Aviation Engines Part 29 online at LightNovelFree.com. You can use the follow function to bookmark your favorite novel ( Only for registered users ). If you find any errors ( broken links, can't load photos, etc.. ), Please let us know so we can fix it as soon as possible. And when you start a conversation or debate about a certain topic with other people, please do not offend them just because you don't like their opinions.
Aviation Engines Part 29 summary
You're reading Aviation Engines Part 29. This novel has been translated by Updating. Author: Victor Wilfred Page already has 693 views.
It's great if you read and follow any novel on our website. We promise you that we'll bring you the latest, hottest novel everyday and FREE.
LightNovelFree.com is a most smartest website for reading novel online, it can automatic resize images to fit your pc screen, even on your mobile. Experience now by using your smartphone and access to LightNovelFree.com
- Related chapter:
- Aviation Engines Part 28
- Aviation Engines Part 30
RECENTLY UPDATED NOVEL
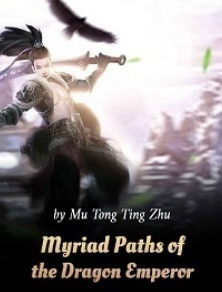
Myriad Paths of the Dragon Emperor
Myriad Paths of the Dragon Emperor Chapter 3091: Sinister intentions View : 1,659,797
The Grand Secretary's Pampered Wife
The Grand Secretary's Pampered Wife Chapter 763.1: Overbearing Robbery! View : 617,402
Madam's Identities Shocks The Entire City Again
Madam's Identities Shocks The Entire City Again Chapter 3489: A Sir Who Claims to Be From Continent M Is Looking For You View : 2,719,077