The Repairing & Restoration of Violins Part 12
You’re reading novel The Repairing & Restoration of Violins Part 12 online at LightNovelFree.com. Please use the follow button to get notification about the latest chapter next time when you visit LightNovelFree.com. Use F11 button to read novel in full-screen(PC only). Drop by anytime you want to read free – fast – latest novel. It’s great if you could leave a comment, share your opinion about the new chapters, new novel with others on the internet. We’ll do our best to bring you the finest, latest novel everyday. Enjoy!
Cramps are used of sufficient width for reaching over the border at each end and quite on to the end of the bar. James, after his repeated trials as to the closeness of the relation of the curve of the bar to that of the table, takes it to the chief as commanded, who expresses his satisfaction and orders the completing process to be gone through.
The curved surface of the bar is wetted and some glue placed along, the part of the table with which it is to be in contact is also wetted, but not much. After a few minutes for the glue to soak in, the final glueing is done along the course on the table and the curved course of the bar; the latter is then placed in position and first one cramp at one end is fixed, then the other; the s.c.r.e.w.i.n.g down is very gently done, James, from experience, knowing just how much and no more. The hard brown paper between the cramps and their padded or corked ends prevents any injury to the varnish.
For the central and adjacent portions of the bar to be pressed, James uses at times wooden cramps with a longer reach, and treating all parts of the bar with gentle but sufficient pressure, being meanwhile careful that the pressure is not directed on one side but direct downwards; he knows that if this is not strictly attended to, the bar will be twisted and when dry, or even finished, will not appear straight but curved along its course.
James having seen that this part of the operation has proceeded satisfactorily, places the table away to dry, and when so, the cramps are removed and the table examined by the chief. All being a.s.sumed to be satisfactory, James is told to go on with the shaping down of the bar, which is done with a chisel held with the bevel downwards, this being safer and less likely to slip.
This having been done to the curving desired by the chief, the gla.s.s-papering to a nice even surface and finish is proceeded with, and the operation may be said to be completed.
We now come to the closing down of the upper table. This last is a final process that when done clumsily, hurriedly, or in many ways improperly, has been the cause of much damage, if not positive destruction, to many good or valuable works of the great masters and others.
Before deciding upon the precise moment for this important stage of repairing, there should be a most careful investigation of the condition of the whole of the interior of the instrument.
Without this there is the possibility of fine splinters of wood, or cracks, being left unattended to that may announce themselves when all is supposed to be in readiness for the bow, by a jarring, or, when the bow is applied, by a buzzing which will take all the knowledge, experience and guessing, perhaps more, that can be brought to bear upon the matter without any practical result, excepting perhaps that of the necessity of re-opening.
If found out before closing down, neighbouring parts should be rigidly examined, as a slight, almost invisible fracture, will, on testing, be frequently found to be much more extensive than was at first suspected.
Gentle tappings may be tried and testings of resistance to bending at the same, keeping the light at right angles to enable the slightest opening or fracture to show itself and be at once placed under treatment.
When every test proves the instrument to be sound and ready for closing up, preparations may be commenced.
There is probably no one of the different details of repairing that gives more evidence than this of the kind of workman engaged upon it.
It may almost be said that this is rarely done as it ought to be in the manner that can be described as being good in every way for the purpose, and neatly done.
The bad manner of closing has been, more frequently than any other, the means of putting the whole instrument out of order, gradually distorting, if not actually bringing it to ruin as a work of art, and to destruction as a means of producing good musical sounds.
Judging by the ways adopted by many inferior grades of repairers, professional and amateur, the closing down of the upper table is thought to be a trifling matter and simply that of pa.s.sing some glue on a brush rapidly round where the ribs are to come into contact with the table, clapping it down, placing the cramps round, s.c.r.e.w.i.n.g them tight, and, if the weather is cold, acting with more rapidity.
Ten minutes may be said to be the average time that this performance takes, and in the majority of cases is thought to be a good one.
But not so by a really competent, painstaking repairer. From his view this operation is to be one of the most cautiously conducted ones in the whole series of joinings in connection with the repairing or constructing of the violin.
As with other processes, there is more than one way of doing a thing and that well.
I recollect in early days being acquainted with an exceeding dexterous amateur in cabinet making, the princ.i.p.al part of whose furniture, in a large house, was his own individual and unaided workmans.h.i.+p. He also combined with this the making of violins, and of them I have a recollection of their exceedingly neat workmans.h.i.+p, being, in fact, ahead in that respect of many professional makers of the time. I often received from him hints as to the best methods of overcoming many little mechanical difficulties.
Once I was telling him about the dexterous manipulation required in fixing accurately and swiftly the upper table. There was the difficulty of getting perhaps the two end parts in position and fixing with sufficient rapidity before the glue had stiffened or set at the other parts.
He asked me why I wanted "to do this all at once, instead of a part at a time? He never did it."
He then proceeded to show me that the glue might be applied to the two end blocks and the corresponding parts of the table that were to be affixed, and these cramped exactly and with comparative ease, in their proper position. This being done, a very thin worn table knife could be used for working in glue at the other parts and the cramping down proceeded with as before.
Another way suggested itself to me some time after, which in careful hands would be still more adapted for accurate fitting. It is as follows:--Having seen that the opposing surfaces or parts that are to be affixed to each other are quite level, fit each other, have been cleaned and are free from any oiliness or greasy particles, the glue is neatly brushed round the parts requiring it, both upper table and ribs being treated. The corner and end blocks, if new, will require more than one coating, and these to be allowed to dry, as the end of the grain is very absorbent.
a.s.suming that the glue is sufficient in quant.i.ty all round, it may be allowed to dry.
The upper table can now be tested for a good fit by laying it, and noticing whether the marginal projection over the ribs is regular or not; in some instances a little humouring or averaging of this projection has to be made, especially when the instrument is very old, and bears evidence of much trouble under the hands of repairers of different degrees of skill, experience and patience.
This being found satisfactory, a slight brus.h.i.+ng of thin glue over the upper and lower end blocks will be enough before placing the table in position and cramping them down.
For the other parts the thin knife will be sufficient, wetted and worked between, the cramps being applied as before.
This way of closing up dispenses with all cause for hurry. The exact amount of glue can be calculated without danger of over-loading, and the next necessary opening for repairs can be effected without the least risk of damage to the margin of the upper table. By this method there is no occasion for wiping superfluous glue from underneath the over-lapping edge, as there will not be any perceptible, or, indeed, present, when tidily done.
Sufficient time being allowed for drying--a little longer for the end blocks, these being more hidden and slowly affected by the atmosphere--the cramps may be removed.
As a final process, the varnis.h.i.+ng over the parts that have been repaired may be touched upon.
The success of this so much depends upon the natural talent of the operator for matching colours and mixing of different gums for obtaining as close as possible resemblance to the surrounding work, that any hard and fast rules concerning it cannot be laid down.
An alcoholic mixture is almost invariably used for the covering of raw repairs, time scarcely ever being available for the use of an oil varnish.
The most commonly used basis is a lac varnish. The ease with which this is dissolved and manipulated is a temptation to use it at times when it would be the least desirable for the imitation of old varnish. One great fault in connection with it is its retaining a glare on the surface when hardened, and the undesirable aspect is given of polished spots where repairs have been going on. There is only one way of counteracting this--by mixing other gums or resins that have less or but little glare when hard. Those of a very astringent quality should be avoided, as when dry their pulling power or contraction is very great, and a cracked surface not at all like the rich fused appearance of many of the old masters, but dry and uninteresting, will make itself too evident.
By a carefully-calculated mixture of soft and hard gums, with a little transparent colouring matter when necessary, a very good if not highly successful imitation of the surrounding work can be accomplished, such as will prevent the repair "catching the eye" too soon, for it must do so eventually when hunted for. The density of colouring and thickness of the princ.i.p.al component parts must always be studied, as the same depth of tint by a very thin layer as that of a thick one will not have the same effect, and one or the other, when making a contrast with the adjacent old surface, will be conspicuous as a failure.
A few hints may be acceptable as to material and the management of it.
We will a.s.sume, for instance, that a portion of the upper table of a rather deep brown-red old master has been repaired, and a slice of comparatively light coloured or new wood has been inserted as a necessity, the grain as a matter of course having been matched to the best of the ability of the repairer.
The first step taken will be that of putting a nice clean even surface over the fresh wood, and in such a manner, that on pa.s.sing the hand or finger over it, no lumps, edges, or rough spots are felt. Having brushed the dust or powdered wood away, the colour of the wood will have to be lowered or subdued, otherwise the whiteness will obtrude itself and stare through any carefully selected varnish. This, for good effect, will be found advisable with the repairing of any old instrument.
The precautions to be taken at this stage are respecting the quality or disposition of the stain (as we may call it). The stains ordinarily sold for colouring wood are quite useless for present purposes, as they are absorbed between the threads, leaving these by contrast very light and the reverse of what is desirable.
A very weak solution in water of b.i.+.c.hromate of potash will lower the colour sufficiently for most purposes, and when quite dry the wood will (having swelled with the moisture) require the fine gla.s.s-papering again, after which, the next stage can be proceeded with.
The solution of nitric acid in water should be avoided, as, although giving a fairly good lowering of the tint, it destroys the soft parts of the wood, and, further, causes an odour that may cause annoyance to the musician and suspicion to the expert.
Another solution may be recommended, that of the black liquorice, which is a transparent brown, and naturally hard. Judgment will have to be exercised in the management of either of the above solutions that they are not put on too heavily.
The staining being effected, a slight coat of a diluted or light tint of the upper or deeply coloured varnish may be painted over and left to dry.
If time is not an important item for consideration, a turpentine varnish may be applied.
An excellent first colouring can be effected with the transparent preparation of gamboge. This material has for long, perhaps always, been in request for coloured varnish, as it can be used with (after due preparation) either alcohol, turpentine or oil. If dissolved in the last, the drying will take so long as to be practically useless to the repairer. The turpentine solution is more rapid, but not sufficiently so for the restorer under ordinary circ.u.mstances.
It will be therefore plain that an alcoholic solution of gums or resins will have to be relied on for obtaining the best results when time is limited.
The solution of gamboge in alcohol is, when used alone, too weak or insufficient in body; it is therefore advisable to incorporate with it some other material of a resinous or gummy nature, but such as will not impair the transparency. Among the most useful are the bleached or white sh.e.l.lac. This, as it leaves the manufactory, is not always in a condition for immediate use by the restorer; it should be washed in water and then dried well, pounded up and placed in a bottle with about four-fifths of alcohol; after remaining in solution for some days the clear portion can be poured into another bottle and retained for use.
This, when used alone in its colourless condition, will possibly have, when dry, too much glare upon its surface, but the colouring matters put into it may oppose this sufficiently.
The use of a little gum guac.u.m in solution will be found occasionally advantageous; this gum is fairly hard and will lower the colour and prevent too much of an approach to gaudiness, that is, if a highly coloured varnish has been found necessary. When it is desirable to dispense with lac of any kind in the varnish, other materials can be found that will perhaps answer the purpose as well, if not better; a solution of benzoin has no colour sufficient in itself and therefore may be used as a priming or mixing with the gamboge or with dragon's blood if that is desirable; the latter, like the gamboge, requires something to give it body.
Dragon's blood will soon let the operator know that its power of colouring to a staring degree will require suppression. To lessen its strength the following may be taken as an excellent means, and will reduce the violence _ad libitum_. With a lighted candle, wax for preference, smoke a piece of clean gla.s.s, and with a camel hair brush remove the black and stir it carefully with the coloured varnish. Care must be taken that too large a quant.i.ty is not put in, or an unpleasant tone, even blackness, will be the result.
With regard to the strength of the red, the same precautions must be taken: on comparing the varnish of a very red old master of Italy, say a Landolphi, with some made with a fairly strong solution of resin and dragon's blood, the violence of colour in the latter will be very apparent. At a little distance off the old master will look very modest while the other will seem coa.r.s.e and vulgar.
For softening purposes a very small quant.i.ty of gum thrus may be used, too much will result in tackiness.
The Repairing & Restoration of Violins Part 12
You're reading novel The Repairing & Restoration of Violins Part 12 online at LightNovelFree.com. You can use the follow function to bookmark your favorite novel ( Only for registered users ). If you find any errors ( broken links, can't load photos, etc.. ), Please let us know so we can fix it as soon as possible. And when you start a conversation or debate about a certain topic with other people, please do not offend them just because you don't like their opinions.
The Repairing & Restoration of Violins Part 12 summary
You're reading The Repairing & Restoration of Violins Part 12. This novel has been translated by Updating. Author: Horace Petherick already has 850 views.
It's great if you read and follow any novel on our website. We promise you that we'll bring you the latest, hottest novel everyday and FREE.
LightNovelFree.com is a most smartest website for reading novel online, it can automatic resize images to fit your pc screen, even on your mobile. Experience now by using your smartphone and access to LightNovelFree.com
- Related chapter:
- The Repairing & Restoration of Violins Part 11
- The Repairing & Restoration of Violins Part 13
RECENTLY UPDATED NOVEL

People Found Out About The Base I Built On the Moon
People Found Out About The Base I Built On the Moon Chapter 1023: Chapter 131 Luo Feng City_2 View : 368,735
Cultivation: Start From Simplifying Martial Arts Techniques
Cultivation: Start From Simplifying Martial Arts Techniques Chapter 1140: Chapter 1096: Walking Leisurely in the Courtyard View : 651,676
The Yun Family's Ninth Child Is An Imp!
The Yun Family's Ninth Child Is An Imp! Chapter 6425: wait a minute View : 2,292,575
Heaven Extinction Martial Emperor
Heaven Extinction Martial Emperor Chapter 1160: Myriad bone devil body (1) View : 387,616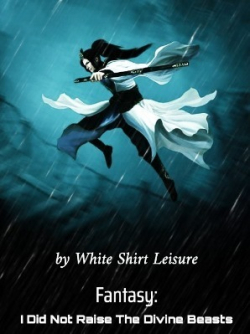