Inventions in the Century Part 32
You’re reading novel Inventions in the Century Part 32 online at LightNovelFree.com. Please use the follow button to get notification about the latest chapter next time when you visit LightNovelFree.com. Use F11 button to read novel in full-screen(PC only). Drop by anytime you want to read free – fast – latest novel. It’s great if you could leave a comment, share your opinion about the new chapters, new novel with others on the internet. We’ll do our best to bring you the finest, latest novel everyday. Enjoy!
The old method of burning wood, or soft coal, or charcoal at the bottom of a small old-fas.h.i.+oned cylindrical fire brick kiln attended to by hand, and heating the articles of pottery arranged on shelves in the chamber above, is done away with to a great extent in large manufactories for the making of stone and earthenware--although still followed in many porcelain kilns.
Inventions in the line of pottery kilns have received the aid of woman.
Susan Frackelton of the United States invented a portable kiln for firing pottery and porcelain, for which she obtained a patent in 1886.
As in drying clay for brick, so in drying clay for porcelain and pottery generally, great improvements have been made in the drying of the clay, and other materials to be mixed therewith. A great step was taken to aid drying by the invention of the _filter press_, in which the materials, after they are mixed and while still wet, are subjected to such pressure that all surplus water is removed and all air squeezed out, by which the inclosure of air bubbles in the clay is prevented.
Despairing of excelling the China porcelain, although French investigators having alleged their discovery of such methods, modern inventors have contented themselves in inventing new methods and compositions. Charles Aoisseau, the potter of Tours, born in 1796, rediscovered and revived the art of Palissy. About 1842, Thomas Battam of England invented the method of imitating marble and other statuary by a composition of silica, alumina, soda, and traces of lime, magnesia, and iron, reducing it to liquid form and pouring it into plaster moulds, forming the figure or group. His plaster casts soon became famous. In the use of materials the aid of chemists was had in finding the proper ingredients to fuse with sand to produce the best forms of common and fine _Faience_.
_Porcelain Moulding_, and its accompanying ornamentation and the use of apparatus for moulding by compression and by exhaustion of the air has become since that time a great industry.
_Porcelain Colours._--Chemists also aided in discovering what metallic ingredients could best be used when mixed with the clay and sand to produce the desired colours. As soon as a new metal was discovered, it was tested to find, among other things, what vitrifiable colour it would produce. In the production of metallic glazes, the oxides generally are employed. The colours are usually applied to ware when it is in its unglazed or _biscuit_ form. In the _biscuit_ or _bisque_ form pottery is bibulous, the prepared glaze sinks into its pores and when burned forms a vitreous coating.
The application of oil colours and designs to ware before baking by the "bat" system of printing originated in the eighteenth and was perfected in the nineteenth century. It consists of impressing oil pictures on a bat of glue and then pressing the bat on to the porous unbaked clay or porcelain which transferred the colours. This was another revolution in the art.
One manner for ages of applying colours to ware is first to reduce the mixture to a liquid form, called "slip," and then, if the Chinese method is followed, to dip the colour up on the end of a hollow bamboo rod, which end is covered with wire gauze, then by blowing through the rod the colour was sprayed or deposited on the ware. Another method is the use of a brush and comb. The brush being dipped into the coloured matter, the comb is pa.s.sed over the brush in such manner as to cause the paint to spatter the object with fine drops or particles. A very recent method, by which the beautiful background and blended colours of the celebrated Rookwood pottery of Cincinnati, Ohio, have become distinguished, consists in laying the colour upon the ware in a cloud or sheet of almost imperceptible mist by the use of an air atomiser blown by the operator. By the use of this simple instrument, the laying on a single colour, or the delicate blending and shadings of two or more colours in very beautiful effects is easily produced.
This use of the atomiser commenced in 1884, and was claimed as the invention of a lady, Miss Laura Fry, who obtained a patent for thus blowing the atomised spray colouring matter on pottery in 1889; but it was held by the courts that she was antic.i.p.ated by experiments of others, and by descriptions in previous patents of the spraying of paint on other objects by compressed air apparatus known as the air brush.
However, this introduction of the use of the atomiser caused quite a revolution in the art of applying colours to pottery in the forming of backgrounds.
Enamelled ware is no longer confined to pottery. About 1878 Niedringhaus in the United States began to enamel sheet iron by the application of glaze and iron oxide, giving such articles a granite appearance; and since then metallic cooking vessels, bath tubs, etc., have been converted in appearance into the finest earthenware and porcelain, and far more durable, beautiful and useful than the plain metal alone for such purposes.
When we remember that for many centuries, wood and pewter, and to some extent crude earthenware, were the materials from which the dishes of the great bulk of the human family were made, as well as their table and mantel ornaments, and compare them in character and plenteousness with the table and other ware of even the poorest character of to-day, we can appreciate how much has been done in this direction to help the human family by modern inventions.
_Artificial Stone._--The world as yet has not so far exhausted its supply of stone and marble as to compel a resort to artificial productions on a great scale, and yet to meet the demands of those localities wherein the natural supplies of good building stones and marble are very scarce, necessitating when used a long and expensive transportation, methods have been adopted by which, at comparatively small cost, fine imitations of the best stones and marbles have been produced, having all the durable and artistic qualities of the originals, as for the most part, they are composed of the same materials as the stone and marbles themselves.
The characteristic backgrounds, the veins and shadowings, and the soft colours of various marbles have been quite successfully imitated by treating dehydrated gypsum with various colouring solutions. Sand stones have been moulded or pressed from the same ingredients, and with either smooth or undressed faces. When necessary the mixture is coloured, to resemble precisely the original stones.
One of the improvements in the manufacture and use of modern _cements_ and artificial stones consists in their application to the making of streets and sidewalks. Neat, smooth, hard, beautiful pavements are now taking the place everywhere of the unsatisfactory gravel, wood, and brick pavements of former days. We know that the Romans and other ancient peoples had their hydraulic cements, and the plaster on some of their walls stands to-day to attest its good quality. Modern inventors have turned their attention in recent years to the production of machines to grind, crush, mix and set the materials, and to apply them to large wall surfaces, in place of hand labour. _Ready-made plaster_ of a fine quality is now manufactured in great quant.i.ties. It needs only the addition of a little water to reduce it to a condition for use; and a machine operated by compressed air may be had for spreading it quickly over the lath work of wood or sheet metal, slats, or over rough cement ceilings and walls.
_Gla.s.s._--The Sister of Pottery is Gla.s.s. It may have been an accidental discovery, occurring when men made fire upon a sandy knoll or beach, that fire could melt and fuse sand and ashes, or sand and lime, or sand and soda or some other alkali, and with which may also have been mixed some particles of iron, or lead, or manganese, or alumina to produce that hard, l.u.s.trous, vitreous, brittle article that we call _gla.s.s_.
But who invented the method of blowing the viscid ma.s.s into form on the end of a hollow tube? Who invented the scissors and shears for cutting and tr.i.m.m.i.n.g it when soft? Or the use of the diamond, or its dust, for polis.h.i.+ng it when hard? History is silent on these points. The tablets of the most ancient days of Egypt, yet recovered, show gla.s.s blowers at work at their trade--and the names of the first and original inventors are buried in oblivion. Each age has handed down to us from many countries specimens of gla.s.s ware which will compare favourably in beauty and finish with any that can be made to-day.
Yet with the knowledge of making gla.s.s of the finest description existing for centuries, it is strange that its manufacture was not extended to supply the wants of mankind, to which its use now seems so indispensable. And yet as late as the sixteenth and seventeenth centuries gla.s.s windows were found only in the houses of the wealthy, in the churches and palaces, and gla.s.s mirrors were unknown except to the rich, as curiosities, and as aids to the scientists in the early days of telescopy. Poor people used oiled paper, isingla.s.s, thinly shaved leather, resembling parchment, and thin sheets of soft pale crystalised stone known as talc, and soapstone.
The nineteenth century has been characterised as the scientific century of gla.s.s, and the term commercial, may well be added to that designation.
Its commercial importance and the advancement in its manufacture during the first half of the century is ill.u.s.trated in the fact that the Crystal Palace of the London Industrial Exhibition of 1851, although containing nearly 900,000 square feet of gla.s.s, was furnished by a single firm, Messrs. Chance & Co. of London, without materially delaying their other orders. In addition to scientific discoveries, the manufacture of gla.s.s in England received a great impetus by the removal of onerous excise duties which had been imposed on its manufacture.
The princ.i.p.al improvements in the art of gla.s.s-making effected during the nineteenth century may be summarised as follows:
First, Materials.--By the investigations of chemists and practical trials it was learned what particular effect was produced by the old ingredients employed, and it was found that the colours and qualities of gla.s.s, such as clearness, strength, tenacity, purity, etc., could be greatly modified and improved by the addition to the sand of certain new ingredients. By a.n.a.lysis it was learned what different metallic oxides should be employed to produce different colours. This knowledge before was either preserved in secrecy, or accidentally or empirically practised, or unknown. Thus it was learned and established that lime hardens the gla.s.s and adds to its l.u.s.tre; that the use of ordinary ingredients, the silicates of lime, magnesia, iron, soda and potash, in their impure form, will produce the coa.r.s.er kinds of gla.s.s, such as that of which green bottles are made; that silicates of soda and lime give the common window gla.s.s and French plate; that the beautiful varieties of Bohemian gla.s.s are chiefly a silicate of potash and lime; that crystal or flint gla.s.s, so called because formerly pulverised flints were used in making it, can be made of a suitable combination of pota.s.sia plumbic silicate; that the plumbic oxide greatly increases its transparency, brilliancy, and refractive power; that _paste_--that form of gla.s.s from which imitations of diamonds are cut, may be produced by adding a large proportion of the oxide of lead; that by the addition of a trace of ferric oxide or uranic acid the yellow topaz can be had; that by subst.i.tuting cobaltic oxide the brilliant blue sapphire is produced; that cuperic oxide will give the emerald, gold oxide the ruby, manganic oxide the royal purple, and a mixture of cobaltic and manganic oxides the rich black onyx.
Professor Faraday as early as 1824 had noticed a change in colour gradually produced in gla.s.s containing oxide of manganese by exposure to the rays of the sun. This observation induced an American gentleman, Mr.
Thomas Gaffield, a merchant of Boston, to further experiment in this direction. His experiments commenced in 1863, and he subjected eighty different kinds of gla.s.s, coloured and uncoloured, and manufactured in many different countries, to this exposure of the sun's rays. He found that not only gla.s.s having manganese as an element, but nearly every species of gla.s.s, was so affected, some in shorter and some in longer times; that this discoloration was not due to the heat rays of the sun, but to its actinic rays; and that the original colour of the gla.s.s could be reproduced by reheating the same.
Mr. Gaffield also extended his experiments to ascertain the power of different coloured gla.s.ses to transmit the actinic or chemical rays, and found that blue would transmit the most and red and orange the least.
Others proceeded on lines of investigation in ascertaining the best materials to be employed in gla.s.s-making in producing the clearest and most permanent uncoloured light; the best coloured lights for desired purposes; gla.s.ses having the best effects on the growth of plants; and the best cla.s.s for refracting, dispersing and transmitting both natural lights and those great modern artificial lights, gas and electricity.
Another ill.u.s.tration of modern scientific investigation and success in gla.s.s-making materials is seen at the celebrated German gla.s.s works at Jena under the management of Professors Ernst Abbe and Dr. Schott, commenced in 1881. They, too, found that many substances had each its own peculiar effect in the refraction and dispersion of light, and introduced no fewer than twenty-eight new substances in gla.s.s making.
Their special work was the production of gla.s.s for the finest scientific and optical purposes, and the highest grades of commercial gla.s.s. They have originated over one hundred new kinds of gla.s.s. Their lenses for telescopes and microscopes and photographic cameras, and gla.s.s and prisms, and for all chemical and other scientific work, have a worldwide reputation.
So that in materials of composition the old days in which there were substantially but two varieties of gla.s.s--the old-fas.h.i.+oned standard crown, and flint gla.s.s--have pa.s.sed away.
_Methods._--The revolution in the production of gla.s.s has been greatly aided also by new methods of treatment of the old as well as the new materials. For instance, the application of the Siemens regenerative furnace, already alluded to in referring to pottery, in place of old-fas.h.i.+oned kilns, and by which the amount of smoke is greatly diminished, fuel saved, and the colour of the gla.s.s improved. Pots are used containing the materials to be melted and not heated in the presence of the burning fuel, but by the heated gases in separate compartments.
Another process is that of M. de la Bastie, added to by others, of toughening gla.s.s by plunging it while hot and pasty and after it has been shaped, annealed, and reheated, into a bath of grease, whereby the rapid cooling and the grease changes its molecular condition so that it is less dense, resists breaking to a greater degree, and presents no sharp edges when broken.
Another process is that of making plate gla.s.s by the cylinder process--rolling it into large sheets.
Other processes are those for producing hollow ware by pressing in moulds; for decorating; for surface enamelling of sheet gla.s.s whereby beautiful lace patterns are transferred from the woven or netted fabric itself by using it as a stencil to distribute upon the surface the pulverised enamel, which is afterwards burned on; of producing _iridescent_ gla.s.s in which is exhibited the lights and shadows of delicate soap bubble colours by the throwing against the surface of hydrochloric acid under pressure, or the fumes of other materials volatilised in a reheating furnace.
Then there is Dode's process for platinising gla.s.s, by which a reflecting mirror is produced without silvering or otherwise coating its back, by first applying a thin coating of platinic choride mixed with an oil to the surface of the gla.s.s and heating the same, by which the mirror reflects from its front face. The platinum film is so thin that the pencil and hand of a draughtsman may be seen through it, the object to be copied being seen by reflection.
Again there is the process of making _gla.s.s wool or silk_--which is gla.s.s drawn out into such extremely fine threads that it may be used for all purposes of silk threads in the making of fabrics for decorative purposes and in some more useful purposes, such as the filtration of water and other liquids.
We have already had occasion to refer to Tilghman's sand blast in describing pneumatic apparatus. In gla.s.s manufacture the process is used in etching on gla.s.s designs of every kind, both simple and intricate.
The sand forced by steam, or by compressed air on the exposed portions of the gla.s.s on which the design rests, will cut the same deeply, or most delicately, as the hand and eye of the operator may direct.
_Machines._--In addition to the new styles of furnaces, moulds and melting, and rolling mills to which we have alluded, mention may be made of annealing and cooling ovens, by which latter the gla.s.s is greatly improved by being allowed to gradually cool. A large number of instruments have been invented for special purposes, such as for making the beautiful expensive cut gla.s.s, which is flint gla.s.s ground by wheels of iron, stone, and emery into the desired designs, while water is being applied, and then polished by wheels of wood, and pumice, or rottenstone; for grinding and polis.h.i.+ng gla.s.s for lenses; and for polis.h.i.+ng and finis.h.i.+ng plate gla.s.s; for applying gla.s.s lining to metal pipes, tubes, etc.; for the delicate engraving of gla.s.s by small revolving copper disks, varying in size from the diameter of a cent down to one-fifteenth of an inch, cutting the finest blade of gra.s.s, a tiny bud, the downy wing of an insect, or the faint shadow of an exquisite eyebrow.
_Cameo_ cutting and incrustation; porcelain electroplating and moulding apparatus, and apparatus for making porcelain plates before drying and burning, may be added to the list.
It would be a much longer list to enumerate the various objects made of gla.s.s unknown or not in common use in former generations. The reader must call to mind or imagine any article which he thinks desirable to be made from or covered with this l.u.s.trous indestructible material, or any practicable form of instrument for the transmission of light, and it is quite likely he will find it already at hand in shops or instruments in factories ready for its making.
_Rubber--Goodyear._
The rubber tree, whether in India with its immense trunk towering above all its fellows and wearing a lofty crown, hundreds of feet in circ.u.mference, of mixed green and yellow blossoms; or in South America, more slender and shorter but still beautiful in cl.u.s.tered leaves and flowers on its long, loosely pendent branches; or in Africa, still more slender and growing as a giant creeper upon the highest trees along the water courses, hiding its struggling support and festooning the whole forest with its glossy dark green leaves, sweetly scented, pure white, star-like flowers, and its orange-like fruit--yields from its veins a milk which man has converted into one of the most useful articles of the century.
The modes of treating this milky juice varies among the natives of the several countries where the trees abound. In Africa they cut or strip the bark, and as the milk oozes out the natives catch and smear it thickly over their limbs and bodies, and when it dries pull it off and cut it into blocks for transportation. In Brazil the juice is collected in clay vessels and smoked and dried in a smouldering fire of palm nuts, which gives the material its dark brown appearance. They mould the softened rubber over clay patterns in the form of shoes, jars, vases, tubes, etc., and as they are sticky they carry them separated on poles to the large towns and sea ports and sell them in this condition. It was some such articles that first attracted the attention of Europeans, who during the eighteenth century called the attention of their countrymen to them.
It was in 1736 that La Condamine described rubber to the French Academy.
He afterward resided in the valley of the Amazon ten years, and then he and MM. Herissent, Macquer, and Grossat, again by their writings and experiments interested the scientific and commercial world in the matter.
In 1770 Dr. Priestley published the fact that this rubber had become notable for rubbing out pencil marks, bits of it being sold for a high price for that purpose. About 1797, some Englishman began to make water-proof varnish from it, and to take out patents for the same. This was as far as the art had advanced in caoutchouc, or rubber, in the eighteenth century.
In 1819 Mr. Mackintosh, of Glasgow, began experimenting with the oil of naphtha obtained from gas works as a solvent for India rubber; and so successfully that he made a water-proof varnish which was applied to fabrics, took out his patent in England in 1823, and thus was started the celebrated "Mackintoshes."
In 1825 Thomas C. Wales, a merchant of Boston, conceived the idea of sending American boot and shoe lasts to Brazil for use in place of their clay models. This soon resulted in sending great quant.i.ties of rubber overshoes to Europe and America.
The importation of rubber and the manufacture of water-proof garments and articles therefrom now rapidly increased in those countries. But nothing that could be done would prevent the rubber from getting soft in summer and hard and brittle in the winter. Something was needed to render the rubber insensible to the changes of temperature.
For fifty years, ever since the manufacturers and inventors of Europe and America had learned of the water-proof character of rubber, they had been striving to find something to overcome this difficulty. Finally it became the lot of one man to supply the want. His name was Charles Goodyear.
Born with the century, in New Haven, Connecticut, and receiving but a public school education, he engaged with his father in the hardware business in Philadelphia. This proving a failure, he, in 1830, turned his attention to the improvement of rubber goods. He became almost a fanatic on the subject--going from place to place clad in rubber fabrics, talking about it to merchants, mechanics, scientists, chemists, anybody that would listen, making his experiments constantly; deeply in debt on account of his own and his father's business failures, thrown into jail for debt for months, continuing his experiments there with philosophical, good-natured persistence; out of jail steeped to his lips in poverty; his family suffering for the necessaries of life; selling the school books of his children for material to continue his work, and taking a patent in 1835 for a rubber cement, which did not help him much. Finding that nitric acid improved the quality of the rubber by removing its adhesiveness, he introduced this process, which met with great favour, was applied generally to the manufacture of overshoes, and helped his condition. But his trials and troubles continued. Finally one Nathaniel Haywood suggested the use of sulphurous acid gas, and this was found an improvement; but still the rubber would get hard in winter, and although not so soft in summer, yet the odour was offensive. Yet by the use of this improvement he was enabled to raise more money to get Haywood a patent for it, while he became its owner. In the midst of his further troubles, and while experimenting with the sulphur mixed with rubber he found by accidental burning or partly melting of the two together on a stove, that the part in which the sulphur was embedded was hard and inelastic, and that the part least impregnated with the sulphur was proportionately softer and more elastic. At last the great secret was discovered!
And now at this later day, when $50,000,000 worth of rubber goods are made annually in the United States alone, the whole immense business is still divided into but two cla.s.ses--hard and soft--hard or vulcanized like that called "ebonite," or soft, it may be, as a delicate wafer. And these qualities depend on and vary as a greater or less amount of sulphur is used, as described in the patents of Goodyear, commencing with his French patent of 1844.
Inventions in the Century Part 32
You're reading novel Inventions in the Century Part 32 online at LightNovelFree.com. You can use the follow function to bookmark your favorite novel ( Only for registered users ). If you find any errors ( broken links, can't load photos, etc.. ), Please let us know so we can fix it as soon as possible. And when you start a conversation or debate about a certain topic with other people, please do not offend them just because you don't like their opinions.
Inventions in the Century Part 32 summary
You're reading Inventions in the Century Part 32. This novel has been translated by Updating. Author: William Henry Doolittle already has 691 views.
It's great if you read and follow any novel on our website. We promise you that we'll bring you the latest, hottest novel everyday and FREE.
LightNovelFree.com is a most smartest website for reading novel online, it can automatic resize images to fit your pc screen, even on your mobile. Experience now by using your smartphone and access to LightNovelFree.com
- Related chapter:
- Inventions in the Century Part 31
- Inventions in the Century Part 33
RECENTLY UPDATED NOVEL
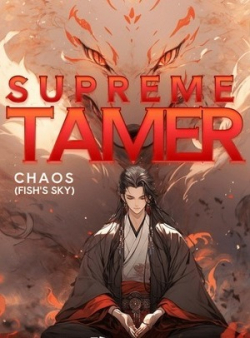
Supreme Tamer
Supreme Tamer Chapter 768: Chapter 638: 30,000 People, Must Be Silenced Completely View : 320,157
Infinite Mana In The Apocalypse
Infinite Mana In The Apocalypse Chapter 3498 Entanglements! IV View : 4,896,145
I Love Destroying Worlds' Plot
I Love Destroying Worlds' Plot Chapter 1545 21.2 Back to Vearth - False Brother View : 519,389
The Grand Secretary's Pampered Wife
The Grand Secretary's Pampered Wife Chapter 767.2: Truth of the Past Revealed View : 633,609
Complete Martial Arts Attributes
Complete Martial Arts Attributes Chapter 3004: Blood God Altar! Blood God Array! (2) View : 2,948,955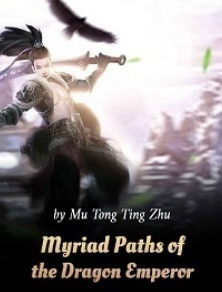
Myriad Paths of the Dragon Emperor
Myriad Paths of the Dragon Emperor Chapter 3123: The third Prince, jiujue mu View : 1,682,685