British Manufacturing Industries Part 2
You’re reading novel British Manufacturing Industries Part 2 online at LightNovelFree.com. Please use the follow button to get notification about the latest chapter next time when you visit LightNovelFree.com. Use F11 button to read novel in full-screen(PC only). Drop by anytime you want to read free – fast – latest novel. It’s great if you could leave a comment, share your opinion about the new chapters, new novel with others on the internet. We’ll do our best to bring you the finest, latest novel everyday. Enjoy!
The Belleek manufactory, in Ireland, has obtained a name for coating its glazed Parian with an iridescent l.u.s.tre, in imitation of a similar article invented by a Frenchman, M. Bianchon.
For richly decorated ornaments, the body of the Parian has been stained with success in many rich colours by Messrs. Minton, their last production in this cla.s.s being a Parian combining the red colour of the terra cotta, with the advantages of a vitrified porcelain.
Their most artistic ware is, however, their _pate sur pate_, in the production of which they have been a.s.sisted by M. Solon, an eminent artist, who left the Sevres works to establish this branch of fine art in their manufactory. To carry on this process, advantage is taken of the transparency of the Parian body with which the figures or ornaments introduced in the composition are painted, or rather modelled. As they are laid on a ground of a dark colour, the softness of the shades in the thinner parts gives to the finished pieces a particularly beautiful cameo appearance. The effect may be compared to that of the Limoges enamels, when confined to the white colour. This process has a certain connection with that of Wedgwood for making his jasper ware; but there is this difference, that in the jasper, the figures and ornaments are taken from clay moulds, and may be repeated to any extent, the talent of the artisan consisting in pressing neatly and transferring on the vases the various fragments of decoration, without destroying the sharpness of the impression, while in the _pate sur pate_ original works can only be produced by the artist, who must combine the qualifications of designer and modeller. What I say here is not in disparagement of jasper, which, considering the time of its introduction, was far in advance of anything that could be expected.
In its production the Wedgwoods never had a rival, and the models of the celebrated Josiah Wedgwood are still worked at their manufactory at Etruria, with the same success. The sulphate and carbonate of barytes were the fluxes originally used to vitrify the body of the jasper ware, and on this account it ought to be cla.s.sified with the stoneware. Parian, which may be made from purely granitic materials, has a nearer connection with porcelain.
There are three different sorts of porcelain: 1. The Chinese and j.a.panese, with which may be a.s.similated the German and French, all of them made of kaolin and felspar, sometimes with an addition of quartz.
The princ.i.p.al seat of this manufacture is now in France, with Limoges for its centre. 2. The soft porcelain, of which the most perfect type is the old Sevres, includes those of Chelsea, Bow, Worcester, and Derby. In all these the transparency, which is the distinctive feature of porcelain, is secured by the introduction of _fritt_, a mixture of sand and alkaline materials thoroughly vitrified, ground and made workable by an addition of plastic clay. The calcareous marl used at Sevres gave to the French works a superiority over the English, who could only use the clays from our southern counties. The manufacture of the soft porcelain, on account of its difficulties, is almost abandoned. 3. The English porcelain, the body of which is made, like the hard, from kaolin and Cornish stone, but differing from it by the addition of a large proportion of calcined bones. This kind is exclusively English. For the hard porcelain, the glaze is made from felspar containing a variable quant.i.ty of quartz, or, as in Germany, from quartz vitrified by an addition of gypsum, the melting of which in both cases requires a very high temperature. For the glazing of the two other cla.s.ses of porcelain, a soft, vitreous mixture containing silicate of lead and borates is used, the temperature necessary to melt these being much inferior to that required for firing the biscuit.
The most ancient porcelain is, as everyone knows, the Chinese, which, relying on the few authorities that have written on this subject, may have been in existence for two thousand years, and is said to have reached its greatest perfection towards the eleventh century of our era. The Portuguese have the credit of having been the first to introduce it in Europe, in 1520; but it is not improbable that, before they doubled the Cape of Good Hope, some specimens were brought to Europe through India and Persia. This may be inferred from the mention by ancient historians of some extraordinary white vessels, which could hardly correspond to any other kind of ware. The Portuguese and the Dutch, who were the first to explore the Chinese seas, seem to have derived a good trade from the importation of the porcelain into Europe, and, since then, the reproduction of that refined pottery was the ambition of many alchemists, who pursued their experiments in that direction with an eagerness almost equal to that wasted in the search for the philosopher's stone. For a long time, in consequence of the imperfection of their chemical knowledge, their efforts ended in failure. The only successful attempt was that of Francis II., one of the Medicis, who produced a few pieces of soft porcelain recognizable by their mark, representing the dome of Florence.
At the death of this prince, his secret was lost, and it was a long time afterwards, at the end of the seventeenth century, that John Dwight, a potter, of Fulham, in Middles.e.x, took a patent for what is curiously reported by Dr. Plot as "_the mystery of transparent earthenware commonly knowne by the name of porcelaine and Persian ware_." Made from English materials, it is probable that this was nothing better than a kind of white stoneware, possessing little of those qualities which would ent.i.tle it to the name of porcelain. Next to that in date would be the soft porcelain made at the manufactory of St. Cloud, which was said to produce, in 1698, pieces of ware considered very good imitations of the Oriental. This was the origin of the French soft porcelain, which was carried on afterwards with varied success at Chantilly, Vincennes, and other places, till it was definitely settled, in 1756, by King Louis XV. in the royal establishment of Sevres. At a corresponding period, on this side of the Channel, the efforts of our potters were varied and numerous. If we are to believe Dr. Martyn Lister, a manufactory of porcelain existed at Chelsea as far back as 1698, a fact which would establish for England a claim equal to that of France for the discovery of the soft porcelain. This is not altogether improbable, considering that there was a gla.s.s manufactory in that locality before that, and that many people had a notion that porcelain was nothing else than a gla.s.s hardened and made opaque. The managers of these gla.s.s-works may have experimented on that supposition, and the conjecture is strengthened by the fact, that pounded gla.s.s was always used at Chelsea to give the desired transparency. Good specimens are not, however, recorded before 1745, and it is probable that many of the improvements at Chelsea were realized by the Staffords.h.i.+re potters, who, two years later, went there to apply their industry. The priority in making practically good ware belongs to the works established in 1730 at Stratford-le-Bow, from which the Bow porcelain took its name. It was not perfected there, however, before 1744, when a china, softer than that made at Chelsea, and nearer to that made at Vincennes, was manufactured by a potter named Frye, originally a painter, who seems to have been the promoter and manager of these works, which at one time did not employ less than three hundred people.
Bow was celebrated for its statuettes, and it is said that several of them were modelled by Bacon, the sculptor. The successes of Bow and Chelsea were great but of short duration, for both had ceased to exist in 1775, when their utensils and moulds were sold to Mr. William Dwesbury, and carried to Derby, where this enterprising gentleman had started a manufactory as far back as 1751.
Three generations of Dwesbury continued here the traditions of Chelsea, after which time the works became the property of Robert Bloor, the last owner of repute. I am happy to say that after ceasing to exist for a great many years, this celebrated manufactory is going to be revived under the leaders.h.i.+p of Mr. E. Phillips, formerly one of the directors of the Worcester works. In that same year (1761), a man--who for his inquiring turn of mind and artistic knowledge seems to have a great likeness to Josiah Wedgwood--Johu Wall, a doctor and a chemist, began also to make porcelain at Worcester; and if Mr. Binns'
a.s.sertions are correct as regards the preparation of the fritt used in it, he must have had some knowledge of the Vincennes receipts. The Worcester works have now been celebrated for more than a century, and with them must be a.s.sociated the names of the various owners, Flight, Barr, and Chamberlain. At Caughley, in Shrops.h.i.+re, a manufactory of soft porcelain was in existence in 1756, and it was employed at one time by the proprietors of the Worcester works to a.s.sist in making ware, which was sent back to them to be decorated. The Caughley works were bought by John Rose, a pupil of Turner, the first director, and transferred to Coalport, with which the works of Nantgarw, in South Wales, were also amalgamated. These works have been in the family of John Rose until lately, when they came into the possession of M. Pew, the present owner. For softness and resistance of body, brightness of glaze, and clearness of colour, the Coalport ware is held in great esteem by those who know anything about china. At Swinton, in Yorks.h.i.+re, soft porcelain was manufactured on the property of the Marquis of Rockingham. Manufactories also existed at other places, so that the reader may here remark, that all exertions to establish the manufacture of china were made outside Staffords.h.i.+re; and if he has noticed the dates, he will also perceive that all these works were founded, when Wedgwood was too young to render any a.s.sistance. This we must say in justice to Dr. Wall, Frye, Dwesbury, and Cookworthy--whose name must not be forgotten as the discoverer of the Cornish clay, which so greatly promoted the ceramic trade of this country. William Cookworthy was a chemist and druggist, at Plymouth, a member of the Society of Friends, and a man of great respectability. Having had the opportunity of seeing some kaolin and felspar from Virginia, that an American friend had shown to him as the very material from which the Chinese porcelain was made, he recognized, several years afterwards, the same in Cornwall, and setting resolutely to work, he began to make his first trials at St. Stephens, on the property of Lord Camelford, and afterwards at Plymouth, where he remained till 1774, when Champion, a merchant of Bristol, bought his patent, and removed the works to the latter place. I must here explain that Cookworthy's ideas of the making of porcelain were correct, inasmuch as he wished to closely imitate the Chinese; consequently he had to work on different principles from those then in favour at Chelsea and other places. He wanted to produce a porcelain without fritt and with a felspathic glaze, and, in succeeding in his attempt, this energetic man is ent.i.tled to a great deal of credit, when we consider that, although the processes discovered by Bottger, in 1710, at Meyssen, for making hard porcelain, were also put in practice at Vienna, St. Petersburg, and Berlin, they were kept very secret, and it is most probable that he had no information whatever from those quarters. It would be to rob Cookworthy to admit that the hard porcelain pieces, known by the name of Lowestoft, were made in that locality. I am indeed sorry to differ in this from an eminent critic, who has taken great trouble to collect doc.u.ments in support of this opinion; but those who are in favour of it know very little about the difficulties attending the organization of such manufacture, and the quality of the materials that it requires. Besides the absence of any information respecting the place whence these materials were taken, the vast quant.i.ty of pieces which are met with is such, that it precludes the idea that they have been made in the precincts of such a small establishment. They have every feature of Chinese porcelain, and of one made in large quant.i.ties. It is most probable that, after making, or trying to make, soft porcelain for a time, the proprietors of the Lowestoft works found it more profitable to paint and decorate the foreign article, which they could easily get from Holland in the white state.
Most pieces of Cookworthy manufacture were copied from the Chinese, and are still well known by the name of Plymouth porcelain. At Bristol, Champion used the same clay to produce a softer kind of ware, and his materials began to be employed at Bow and other places. The Staffords.h.i.+re potters soon became anxious to take advantage of the discovery, and in 1777 a company was formed by Jacob Warburton to obtain a licence for their use. This was granted by Champion, but with this singular restriction--that, although they were allowed to use a certain quant.i.ty of china clay and china stone, they were not to make porcelain. This restriction, however, did not last long, and Champion himself came for a short time to Shelton to superintend some works.
Amongst the names of Warburton's a.s.sociates, we notice some well known in Staffords.h.i.+re, such as S. Hollins, of Shelton; Antony Keeling, of Tunstall; Turner, of Lane End, and a few others. To these gentlemen we must give credit for the earliest attempts to introduce the manufacture of china into the Potteries. However, their porcelain was inferior to that made at Worcester and Derby, and it is doubtful whether they would have persisted, if the matter had not been settled by Josiah Spode, the second of that name, who, by adding calcined bones to the body of the ware, made a new kind of porcelain, distinct from the hard or the soft previously made. On that account Spode deserves to be considered as the creator of the English porcelain.
There is this peculiarity in the use of bones, that the phosphate of lime which enters into their composition is not decomposed by the silicates with which it is mixed, and, as it is infusible, its admixture in the body allows the ware to stand without injury the temperature at which the felspar is vitrified. This hardening of the bones does not exclude a certain amount of transparency, and they possess, besides, a very great advantage in preventing the oxides of iron which exist in the clays, producing that brownish or imperfect transparency, noticeable in the old Derby or Worcester ware. I have already said that the adaptation of the glaze for each kind of pottery is one of the greatest difficulties that the maker has to overcome; in this case, however, there was very little, and the glazing of English porcelain may be considered as exceptionally easy. Most of the glazes which had been used for the soft porcelain could be adapted to this one, a property which was of great service when the pieces had to be decorated. I have already explained, that when paintings executed on the surface of the ware are submitted to a moderate red heat, if the glaze is soft enough to undergo an incipient fusion, the vitreous colours with which they are executed will sink into it and attain, by their incorporation, an amount of glossiness and brilliancy which cannot be got on the surface of hard glazes. This is particularly ill.u.s.trated by the old Sevres ware, which possesses this quality in the highest degree. English porcelain, well-made, has almost all the advantages of the old soft, and its making is not attended with the difficulties experienced in working a body made from fritted substances. For regular use, it is not much inferior to the hard porcelain. When this last began to be made on the Continent, people were so much prejudiced in its favour, on account of the capability of its glaze to resist the scratching of the knife, that this was thought to more than compensate for its inability to combine with the colours.
The advantage was, in fact, more apparent than real, for when hard porcelain has been long in use, it becomes as badly scratched as the English. Some people question whether it would not be desirable to revive in England the manufacture of the hard. There are many reasons against this, the princ.i.p.al being, that in case we succeeded, we should have to compete with the French and Germans, who get their labour cheaper, and have a long experience of processes altogether different from ours; and by the change we should lose the advantage of our traditions, and depend, at least for a time, on foreign labour to give a new training to our workmen. Out of the trade, few people seem to know that the price of hard porcelain is generally lower than that given for the English; and, if the experiment were made, it would be soon found that with greater risks we should produce an article of less value, and consequently less remunerative. It is true that the exports of our best china are very small, on account of its price; but with the improvement going on in the public taste, it is likely to increase, and there are signs that eventually our richest articles may find purchasers on the other side of the Atlantic.
In Europe, where the value of the various ceramic productions has been more investigated than in the other parts of the world, there is hardly an amateur who does not recognize the superiority of a soft porcelain for decorated articles, and if the English china is not, properly speaking, as soft as the old Sevres, it is certainly nearer to it than any other porcelain. This superiority is proved by the test that the various porcelains are undergoing at the present time, and which is rather decisive. We understand by this, the manner in which they have stood the dangerous compet.i.tion arising from the introduction of artistic faiences or painted majolica. While, in consequence of this, the French manufacturers have seen the production of ornamental articles in hard porcelain collapse to an incredible extent, the quant.i.ty of those made in England for similar purposes is fast increasing.
Messrs. Copeland, whose father, the late alderman, was for some time in partners.h.i.+p with Spode, occupy, in Stoke-upon-Trent, the same establishment in which that great potter carried out his improvements.
Since then, these makers have kept their rank among the princ.i.p.al leaders of the trade, and maintain their reputation for the excellence of their decoration and the beauty of their gilding. It was so far fortunate for Stoke that, although one of the smallest towns in the Potteries, it became the seat of the most important manufactories of china. It was in 1788 that Thomas Minton, who had been brought up as an engraver at the Caughley works, in Shrops.h.i.+re, and who in that capacity had been several years in the employment of Spode, founded in that town the establishment which subsequently became the property of his son, Herbert Minton. The father does not seem to have possessed these qualities which, as potter, should ent.i.tle him to a special notice; but the same cannot be said of the son, who soon after his father's death began to work in earnest to raise his manufactory to its present degree of eminence. The unceasing activity of his mind in carrying out improvements in all the branches of his trade, may be attested by one who for many years had the honour of working with him.
On every matter connected with art his ideas were sound, and his natural tact rarely failed in finding out that which was most suited to the taste of his customers. His reputation, as the most advanced potter of his time, is so well established, that I am not astonished to find others claiming a share in it, a.s.serting that it was at their suggestion, or with their a.s.sistance, that he left the old path to open the way to progress. Suggestions and advices are always freely given to a man of sociable disposition as was Herbert Minton, but he used his own judgment and discretion to test their practicability. In applying higher cla.s.s of art to his productions, he had only to follow his own inclinations, guided by that care and prudence which are inseparable from good administration. He knew how to select his a.s.sistants, and was particularly fortunate in his partners, his two nephews: Michael Hollins, who, since he left the firm of Minton, is the owner of a large tile manufactory at Stoke; and Colin Minton Campbell, his pupil and heir, who, after taking an active part in all his labours, has so successfully followed the example set by his uncle, that Minton's manufactory is now the largest in existence, and turns out the greatest variety of ware. With Minton and Copeland must be a.s.sociated the names of Messrs. Brown-Westhead, of Caulden Place; and outside Staffords.h.i.+re, the Coalport works and the Royal manufactory at Worcester. These are the princ.i.p.al producers of richly decorated china, for which the demand has greatly increased during the last few years. The greatest bulk of that ware is, however, made at Longton, one of the pottery towns which has a reputation for the cheapness of its goods; but of late a decided tendency to improve their quality and prices must be noticed among the generality of its manufacturers. Several of them, like Messrs. Ainsley, Moore, Barlow, and others, are trying to raise their goods to the same level as those of Stoke. There are about thirty-five firms in the Potteries making china, most of them for the home trade, and over five times that number making earthenware. These two hundred and thirty manufactories are spread over an area of ten square miles, comprising the towns of Hanley, Burslem, Tunstall, Longton, Fenton, Shelton, and Stoke-upon-Trent, from which the electoral borough takes its name.
These, which in a few years are likely to be amalgamated in a single town, form the district called the Potteries, containing already a population of 170,000 inhabitants engaged in the ceramic and iron trade. It has been remarked that since the foundation of Burslem, the mother town of the Potteries, the population of the district has doubled every twenty-five years, and it is easy to foresee the time when Stoke-upon-Trent will rank in importance with our largest commercial cities.
The export of porcelain is not large; but that of earthenware reaches one and a half million of pounds. This does not appear large compared with the enormous amount exported by the iron or the cotton trades, but it is satisfactory, if taken in combination with the quant.i.ty absorbed by the home trade, which represents quite as much. Our colonial trade with Australia, India, and British America is decidedly on the increase, and the same may be said as regards South America. On the contrary, our transactions with the Continent of Europe have a tendency to decrease, and to fluctuate in the case of the United States, a very important market, which, in time of prosperity, would take as much as 800,000_l._ of granite ware.
To meet the compet.i.tion of France and Germany, on one side, and the Americans on the other, great changes have taken place in the management of our works. Several processes have been improved or simplified, and large manufactories have been built on better principles. These steps were not taken too soon; for if compet.i.tion scarcely existed for our goods twenty years ago, that state of things has been much altered, and it will require a great deal of application and energy on our part, if we intend to maintain our position as the largest and best producers of pottery in the world.
It is a fact that America, which had not a single manufactory worth the name at the time of the New York Exhibition, produces now, with the a.s.sistance of British workmen, granite ware of tolerably good quality; and I have been told by an eye-witness, that no less than seventy ovens are now at work at Trenton, in New Jersey. The clays and coals used by these potters are good, and if the salaries are higher than they are in England, they find a compensation in the heavy duties which, since the war of Secession, are levied on our wares.
Our commercial intercourse with France has not much altered, and the quant.i.ty of our goods sent across the Channel may be considered small compared with the importance of this market. The French are the largest producers of hard porcelain, and they make their common earthenware quite as cheap, if not cheaper, than ours. However, if they are strong at home, they have never affected our trade abroad, except in the United States, where they send their porcelain in compet.i.tion with English granite.
At the present time, the rivalry from which we have suffered most in Germany, the North of Europe, and as far as Italy, comes from a group of establishments situated in the Rhenish provinces and that neighbourhood: at Sarreguemines, Sarrelouis, Vaudrevange, Mettlach, Maestricht, and a few other places. Built in the centre of a populous district, where labour is still very cheap, their intelligent and wealthy proprietors share in each other's business, and consequently have no inducement for lowering their prices. They seem to have given a considerable portion of their time to the study of the various processes, and they have so far succeeded, that they are a great deal more independent with regard to their men than we are. Possessing these advantages, we cannot wonder, if we have not been able to keep our hold on those markets which were the nearest to them. Besides, it is plain, that the important rise which has taken place in the price of wages and fuel, and the consequent increase in the price of our wares, has acted as an encouragement to foreign production; and perhaps it may be good policy, in future, to resist any further opportunity which might offer to increase the price of our goods. It would, however, be singular if, in the course of time, England did not derive some benefit from this compet.i.tion; she is used to close contest, and, everything considered, her position is an enviable one.
Our home trade is excellent; and if the amount of our exports does not progress so fast as we could desire, we know that we have in our commercial fleet more facilities that any other nation for sending our goods to those numerous countries where the trade of pottery is hardly established, and we rely on our honest and straightforward way of dealing, for securing new customers for English manufacture.
GLa.s.s AND SILICATES.
BY PROFESSOR FREDK. S. BARFF, M.A.
The very brilliant and useful substance, which forms the subject of this article, is said to have been discovered by the Phoenicians.
The story goes that some Phoenician merchants, while cooking their food on the sands near the seash.o.r.e, noticed that the ashes of the plant, with which they made their fire, caused some of the sand to melt and form a vitreous substance; but whether this tale be true or not, it is well known that for a long time these people made gla.s.s from the materials which were abundant on their sea and river coasts.
Gla.s.s, however, was produced long before this by the Egyptians for the beads and ornaments used in adorning their mummies, and many specimens of these are in the British Museum. It is certain also that they well knew how to make certain substances impart colour to gla.s.s for the manufacture of most of these beads. The Romans made rich goblets of ruby gla.s.s, some of which are to be seen in collections in this country, as well as urns to receive the ashes of their dead, four of which, of a green colour, are also in the British Museum. The manufacture of these vessels proves that this nation was well skilled in the arts of blowing and modelling gla.s.s; and their designs, which we are now reproducing, show that they were at least not inferior in artistic skill to those who have formed their taste in this highly civilized age. We have no record of gla.s.s being used for glazing purposes in ancient times. The Venerable Bede introduced it into this country about 674 A.D., and employed it in the adornment of church windows. Ordinary window gla.s.s was made at the works in Crutched Friars in 1557, and plate gla.s.s at the large works of the Ravenhead Plate Gla.s.s Company, near St. Helen's in Lancas.h.i.+re. About 1776, flint gla.s.s vessels were blown at the establishment in the Savoy House; and the second Duke of Buckingham brought over Venetian artists, at that time the most skilled, to make gla.s.s for mirrors, carriage windows, and other useful purposes. Their workshop was in Lambeth, and the date of their arrival in this country was 1673. The French were before us in the art of casting gla.s.s plates; and in 1688, Stewart commenced this branch of manufacture, which led to the establishment of the very famous works of St. Gobain. England has now large plate gla.s.s factories in different parts of the country, and these together yield as their weekly production at least 140,000 superficial feet of the best polished plate, or seven and a quarter millions of feet yearly. The value of plate gla.s.s made in England annually, including the rough kinds used for glazing roofs, &c., is estimated at 1,000,000_l._ France still stands very high, and her plates are extremely perfect in manufacture. St. Marie d'Oignies, in Belgium, also sends a considerable quant.i.ty of plate gla.s.s into the market. This branch of manufacture has not yet extended to America, which therefore is a large customer of Europe. Formerly, gla.s.s making was very heavily taxed in this country, and in 1812 an additional duty was placed on the manufacture of the raw material, which so greatly depressed it, that the income which the State received fell from 328,000_l._ to 183,000_l._ per annum. Moreover, large quant.i.ties of foreign gla.s.s were imported, and this too hindered the development of the industry amongst us. On the repeal of the duty, however, the trade began to increase, and has now reached very large dimensions.
Gla.s.s appears to be a mixture of silicates, the nature and chemical composition of which will be explained in a later part of this article.
The materials used are princ.i.p.ally sand, with an alkaline substance, either a salt of soda or potash and lime, though in some kinds of gla.s.s, oxide of lead takes the place of lime. Other materials are generally employed to correct impurities which may occur in the sand, and which, if present, always impart an objectionable colour to the gla.s.s.
There are two kinds of gla.s.s in ordinary use: common window gla.s.s, which may be divided into sheet, crown, and plate; and flint gla.s.s, which is used for decanters, wine-gla.s.ses, and tumblers; and, in some special forms, for ornamental stones in imitation of jewels, and also for lenses of telescopes and microscopes. The materials for making these different kinds vary somewhat, although the princ.i.p.al const.i.tuents are the same, viz. sand with some salt of soda or potash.
The scientific name for sand, or more properly for its princ.i.p.al const.i.tuent, is silica. This compound silica, or oxide of silicon, also called silicic acid, possesses properties similar to those which belong to other acids, namely, it is able, when brought into contact with bodies of an opposite character under suitable conditions, to unite with them and to form salts. Everybody knows, that if tartaric acid be added to carbonate of soda, an effervescence takes place; carbonic acid pa.s.ses off in the gaseous state, and the residue is composed of a portion of the tartaric acid, which unites with the soda, a double decomposition taking place. If silicic acid be mixed with carbonate of soda, and if the mixture be heated to a high temperature, that is, to a white heat, for some length of time, the same kind of action occurs: carbonic acid goes off, the silica or silicic acid uniting with the soda; and inasmuch as the soda salt was originally called _carbonate_ of soda, after this action, in which carbonic acid is replaced by silicic acid, it is called _silicate_ of soda. Silicic acid at the ordinary temperature of the air and in the dry state, has no action whatever upon carbonate of soda, but when heated sufficiently, the action becomes vigorous. A very interesting experiment may be performed in ill.u.s.tration of this fact in the following manner: if a mixture of carbonate of soda and carbonate of potash be heated in an ordinary fire-clay crucible, and if, when the mixture is melted, some perfectly dry sand be poured into it, effervescence will take place, owing to the expulsion of carbonic acid from the carbonate of soda and potash by means of the silicic acid. If the operation be performed in such a vessel that the carbonic acid can be collected, its presence is readily indicated by the usual tests.
This experiment can be easily made by anyone who has ordinary chemical apparatus at his command. If the mixture of carbonate of potash and carbonate of soda be melted in a small platinum crucible; and if, when melted, it be removed quickly while very hot into a tall beaker-gla.s.s, and sand be then poured into it, the escaping carbonic acid will, on account of its being heavier than air, be retained in the gla.s.s, and its presence can be recognized by its turning lime-water milky (which is, in fact, a solution of lime in water), owing to the formation of carbonate of lime produced by the carbonic acid evolved uniting with the lime dissolved in the water. A mixture of carbonate of soda and carbonate of potash is here used, because either of these salts requires a very high temperature to melt it; but when the two are heated together, the fusibility of both is increased. When sand is heated with oxide of lead (common litharge) they unite, forming a compound similar to that produced by the silica uniting with the soda, as described in the last paragraph. In the first case, a _soda_ gla.s.s is formed; in the second, a _lead_ gla.s.s is the result. If these two gla.s.ses be mixed together and melted in a crucible, and if the proportions in which they are mixed be properly adjusted, and the materials used be pure, a colourless and transparent gla.s.s will be formed, similar in appearance to that which is employed in the manufacture of decanters and tumblers. The same kind of gla.s.s may be produced by mixing all the materials in due proportions and heating them together. If, instead of oxide of lead, lime be mixed with carbonate of soda and sand, and the mixture be heated to a high temperature, a gla.s.s will be formed, in many respects similar to that of which oxide of lead is a const.i.tuent, but differing from it in several important particulars. First of all, the lead gla.s.s is highly l.u.s.trous, and has a great power of refracting light, so that, when it is cut, it presents a brilliant appearance, and by refraction readily produces the prismatic colours. This property does not belong to the gla.s.s containing lime, to anything like the same extent. Lead gla.s.s, too, is much heavier than lime gla.s.s, and is therefore unsuited to many of the purposes for which the latter is generally used, the princ.i.p.al of which is for the glazing of windows.
If, instead of oxide of lead, which is a chemical compound of lead and oxygen gas, or lime, which likewise is one of the metal calcium with oxygen, _carbonate_ of lead or of lime be used, the silicic acid will expel the carbonic acid from these substances at a high temperature, just as it does the carbonic acid from the carbonate of soda and carbonate of potash. It is necessary, for a proper understanding of the scientific part of our subject, that this fact should be borne in mind, and that the acid properties of silica should be thoroughly recognized. Formerly, carbonate of soda was used in the manufacture of ordinary window gla.s.s, but now it is found more economical to employ _sulphate_ of soda, which is a much earlier product in the manufacture of soda from common salt than the carbonate, and is therefore less expensive. Carbonic acid is what chemists call a _weak_ acid, by which is meant, that its compounds are not so firm and stable, as those which are formed by other acids with the same substances. Sulphuric acid is a strong and powerful acid, uniting very readily with the oxides of certain metals to form very stable compounds. But although this acid is chemically so powerful in its compounds, yet at a high temperature it is expelled by silicic acid, showing that this substance, so inert in its natural state and at the ordinary temperature of the air, becomes exceedingly active in expelling other acids and in forming compounds, when put under favourable conditions.
If a mixture of common sand and carbonate of soda, the carbonate of soda being in excess, be heated, a gla.s.s will be obtained which is slowly soluble in cold, readily soluble in hot water. To these compounds the name of silicate is given, so that we speak of the soda compound as silicate of soda, of the lead compound as silicate of lead, and the lime compound as silicate of lime. Silicate of soda and silicate of potash, when the alkali, that is to say, the soda or potash, is in excess, are both soluble. If a solution of one of these silicates be taken, and if carbonic acid be pa.s.sed slowly through it, after a time a gelatinous, white, flocculent substance will be formed in the liquid, and eventually precipitated. This white flocculent substance is silicic acid combined with the elements of water, and is therefore called by chemists hydrate of silica. Now this hydrate of silica is soluble in water and in hydrochloric acid; and the method by which it can be brought into solution in water will be explained, when treating fully of what are called soluble silicates and their applications.
Soluble silicates are mentioned here, in order that a more perfect understanding of the nature of silicious compounds may be obtained, by those who do not possess a scientific knowledge of chemistry. The silicic acid in the silicate of soda is precipitated or separated out by carbonic acid, and hence it appears, that an action, exactly the reverse of that which takes place at a high temperature, occurs, when the silicic acid is removed from those conditions in which it has been seen to be (chemically) so active.
Suppose that to a solution of silicate of soda or of potash a soluble salt of calcium be added--the chloride, for example, which is a compound of the metal calcium with chlorine--a double decomposition will take place; the calcium will unite with oxygen in the silicate of soda, forming lime; and this will again unite with the silicic acid, forming silicate of lime; while the chlorine will unite with the sodium, forming chloride of sodium, or common salt.
Here then, silicate of lime is obtained by a process very different from that which has already been described, namely, by the heating of lime with silica at a high temperature. The body formed in the latter case is chemically the same as that produced in the former, there being present the same weight of calcium, the same weight of oxygen, and the same weight of silicic acid in each. Again, if to a solution of silicate of soda, one containing a soluble lead salt, such as the nitrate, be added, the silicic acid will unite with the oxide of lead in the nitrate of lead, and the acid const.i.tuent of that body will unite with the oxide of sodium or soda, forming nitrate of soda. It is apparent, therefore, from these remarks, that in whatever way the substances be made to unite, the effects produced as regards chemical composition are the same. If some of the silicate of lime or silicate of lead made by precipitation be dried and heated to a high temperature in a crucible, it will melt or fuse, and form a vitreous substance. In these last cases, as in many others which will have to be alluded to, the silicates formed are not soluble in water, although silicate of lime may be partially dissolved when heated in water under extreme pressure, by which the temperature is considerably increased, and even slightly in cold water.
To ensure the production of definite silicates by the agency of heat, the materials must be mixed together in proper combining proportions; for if more of the metallic oxide is introduced than can combine chemically with the sand, it will be melted in the ma.s.s, but the excess will not form a definite compound; whereas by precipitation, the silicates formed always have, when thoroughly washed, a definite composition. This subject will be again referred to, when the manufacture of commercial gla.s.s is described.
It has been noticed that the gla.s.s found in the windows of old churches and in other places where it has been exposed to the prolonged action of the air and of moisture, has gradually become rough on its surface, and has lost to a considerable extent its transparency. This, which would be a defect in gla.s.s for the glazing of ordinary windows, where transparency is desired, is rightly regarded as a beauty in gla.s.s which is to be used for the ornamentation of windows. Many reasons have been offered in explanation of this apparently peculiar property of ancient gla.s.s; and that which appears to be correct is, that gla.s.s is a mechanical mixture of different silicates, some of which may be soluble in water, and others insoluble. The old window gla.s.s, whose manufacture will be more fully described by-and-by, was made in a less perfect manner than modern appliances enable gla.s.s manufacturers now to produce the same article, so that the silicates composing the old gla.s.s were not as intimately mixed as those used in modern gla.s.s. By the slow action of air and moisture, portions of the soluble silicates have been dissolved out, and hence we frequently find a sort of honeycomb appearance on the surface of ancient gla.s.s, as well as a thin film, which, by refraction of light, causes an opalescence when viewed by reflected light. Efforts have of late been made to produce a similar effect by employing different methods in the process of manufacture, but without complete success. The fact, however, that such changes have taken place in this less perfectly fused gla.s.s, tends to show, that if one silicate can be dissolved out, there cannot be _chemical_ union between all the silicates. If a piece of modern window gla.s.s be heated in water under pressure in a closed vessel, it will present somewhat the appearance of ancient gla.s.s, for a considerable quant.i.ty of soluble silicate will be dissolved out from it. The object in dwelling on this matter here, is to induce makers to attend more to the chemical composition of their gla.s.s, for, doubtless, much more satisfactory results would be obtained both as to the quality of the material and the cost of its production, if thoroughly scientific investigations were conducted by a competent chemist.
MANUFACTURE OF GLa.s.s.
The first object in gla.s.s making is to obtain suitable materials. The sand which is employed for window gla.s.s differs from that which is required for flint gla.s.s, in that the latter should be as pure as possible. The maker can correct the impurities in the window gla.s.s sand, provided they be not present in too great quant.i.ties; but it is far more difficult, in the case of flint gla.s.s, to chemically counteract the influence of those substances which might impair its tint. So that the manufacturer would rather pay large prices for his sand, than trust to expedients which in their application might fail, and thus cause a greater loss.
One of the princ.i.p.al and most troublesome impurities met with in sand, is iron in the form of oxide. There are two oxides of iron: one, the protoxide, which imparts a green colour to gla.s.s; and the other the peroxide, whose staining property is yellow. A very small quant.i.ty of the former will give an appreciably green tint, whereas it requires a large quant.i.ty of the peroxide to produce even a delicate yellow. In all gla.s.s making, it is found necessary to use something which will counteract the colouring properties of these two oxides. The material employed was black oxide of manganese. This is still used in certain gla.s.s-works, but from its injurious action on the fire-clay pots, a.r.s.enious acid or common white a.r.s.enic is employed to effect the same object. The chemical action in the two cases is different: the black oxide of manganese is what is termed an oxidizing agent, and gives up, at a high temperature, a portion of its oxygen to the protoxide of iron, thereby converting it into the peroxide. It thus becomes comparatively harmless, by converting a quant.i.ty of that oxide, which gives a green colour, into the other oxide, which has little or no power of colouring, except it be present in large quant.i.ties. The difficulty in using black oxide of manganese is, the exact proportioning of it to the quant.i.ty of iron present in the sand, a quant.i.ty which cannot be easily determined. If the black oxide of manganese be used in excess, some of the oxide of manganese remains unreduced, and, when this is the case, it gives a purple colour to gla.s.s. If used in exact proportions, it is reduced to an oxide which does not impart colour to gla.s.s. This may be seen in many of the old plate gla.s.s windows which were employed for glazing purposes some sixty or seventy years ago, the colour of the panes being generally purple.
Since this article was written, I have been consulted by a gla.s.s firm of eminence, as to the use of pure black oxide of manganese in the manufacture of flint gla.s.s, instead of that ordinarily supplied in commerce. The black oxide of manganese usually sold contains many other const.i.tuents besides black oxide of manganese; amongst these are iron, copper, cobalt, and alumina.
The iron, as will be seen from what has before been stated, is a decidedly objectionable ingredient to use along with the manganese.
Copper and cobalt both stain gla.s.s, the former of a bluish-green colour, while the latter makes it blue; and a small quant.i.ty of the latter has great staining power. I have thought it advisable to give a.n.a.lyses of the black oxides of manganese, and they are as follows:
Binoxide of manganese (Molecule, Mn.O_2), is found native as pyrolusite or polyanite. Appended are two a.n.a.lyses of pyrolusite containing sesquioxide of iron.
Red oxide of Manganese 870 725 Oxygen 116 98 Sesquioxide of Iron 13 42 Alumina 03 Baryta 12 Lime 03 Silica 08 14 Water 58 16 ----- ---- 1083 995
The native binoxide often contains both copper and cobalt in addition to iron; frequently to the amount of as much as 1 per cent. of copper and about 54 per cent. of cobalt.
Wad, a native binoxide of manganese, sometimes contains 5434 per cent. of iron, while nearly all the manganese ores contain more or less alumina, varying from 5 per cent. to as much as 20 per cent.
From the composition of ordinary commercial black oxide of manganese, as shown by these a.n.a.lyses, it is evident that it is better to use the pure article, and this has been found to be the case by the firm who have adopted it in lieu of commercial black oxide of manganese. I therefore strongly recommend all gla.s.s makers to try and experiment with it, for the results obtained will largely counterbalance the extra cost of the pure material; and I also much doubt whether the same injurious effects will be produced on the pots, as is the case where commercial manganese is employed.
British Manufacturing Industries Part 2
You're reading novel British Manufacturing Industries Part 2 online at LightNovelFree.com. You can use the follow function to bookmark your favorite novel ( Only for registered users ). If you find any errors ( broken links, can't load photos, etc.. ), Please let us know so we can fix it as soon as possible. And when you start a conversation or debate about a certain topic with other people, please do not offend them just because you don't like their opinions.
British Manufacturing Industries Part 2 summary
You're reading British Manufacturing Industries Part 2. This novel has been translated by Updating. Author: L. Arnoux, Professor Barff, and J. H. Pollen already has 623 views.
It's great if you read and follow any novel on our website. We promise you that we'll bring you the latest, hottest novel everyday and FREE.
LightNovelFree.com is a most smartest website for reading novel online, it can automatic resize images to fit your pc screen, even on your mobile. Experience now by using your smartphone and access to LightNovelFree.com
RECENTLY UPDATED NOVEL

The Great Mage Returns After 4000 Years
The Great Mage Returns After 4000 Years Book 2 Chapter 595 View : 526,547
I Love Destroying Worlds' Plot
I Love Destroying Worlds' Plot Chapter 1551 21.8 Fifth Violet Star - Xiu Mo View : 520,343
The Strongest War God
The Strongest War God Chapter 1394: This Path, Burying the Heaven's Favorites View : 539,749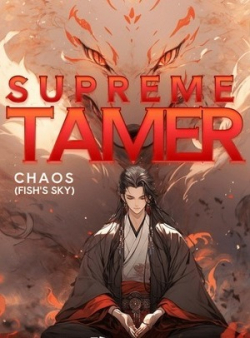
Supreme Tamer
Supreme Tamer Chapter 770: Chapter 640: Natural Disasters and Human Calamities, Crisis in Barbarian Valley View : 321,527
I'll Be the Male Leads Sister-in-Law
I'll Be the Male Leads Sister-in-Law Chapter 559 View : 191,447