The Building of a Book Part 10
You’re reading novel The Building of a Book Part 10 online at LightNovelFree.com. Please use the follow button to get notification about the latest chapter next time when you visit LightNovelFree.com. Use F11 button to read novel in full-screen(PC only). Drop by anytime you want to read free – fast – latest novel. It’s great if you could leave a comment, share your opinion about the new chapters, new novel with others on the internet. We’ll do our best to bring you the finest, latest novel everyday. Enjoy!
Almost all of the maps found in text and reference books, as well as the geometrical diagrams used in mathematical and scientific works, are made by what is known as the "wax process."
This process was invented and patented by an Englishman named Palmer about 1840, shortly after the discovery of the method of making electrotype plates for printing purposes. He announced that he would furnish artists with copper plates covered with a waxlike composition on which they could make their own drawings, in a manner similar to but much simpler than the method followed by the etcher on copper.
After receiving the artist's work, the plates were to be returned to Palmer, who then made an ordinary electrotype of the engraving. A circular, issued about 1841, gives the necessary instructions for engraving, and the prices for the wax-coated plates and the subsequent electrotypes, and shows many beautiful ill.u.s.trations made by artists of that time. It was then called the "glyphographic process."
The process was first introduced into this country by a firm of printers in Buffalo, New York, and was used by them for several years for ill.u.s.trating the United States patent office reports until it was superseded upon the introduction of photo-lithography and the subsequent adoption by the government of a uniform standard for patent drawings.
This process may be described in a general way as follows: A copper plate having a highly polished surface is first blackened by the application of a weak solution of sulphuret of pota.s.sium, or other chemical which will oxidize the copper. Then a composition, made by melting together in proper proportions, beeswax, zinc-white, and paraffin, is "flowed" over the blackened surface, producing an opaque whitish engraving ground. The thickness of the wax is varied according to the subject to be engraved, but in general should not exceed that of heavy writing paper. After it has been allowed to cool with the plate lying perfectly horizontal, the wax is smoothed down to an even thickness by a steel sc.r.a.per, and the plate is then ready to receive the engraving.
Taking for an example the engraving of a map, the original copy is either photographed on the wax surface, or is transferred to it by covering the back of the copy with red chalk and tracing over every line with a steel point. The photograph, or the tracing, on the wax must not be a reversed one, as might be supposed, but should "read right." The outlines of the map are then gone over, with an engraving tool which cuts out a small channel in the wax, down to, but not into, the surface of the copper plate. The bottoms of these channels will eventually form the surface of the relief lines in the resultant electrotype plate, but now appear as dark lines against the whitish groundwork of the wax.
The engraving tools are made in different sizes, and therefore channels of varying widths at the bottoms may be cut in order to produce lines of different sizes. In cutting lines to indicate rivers,--which must be thin at the source and increase in thickness as they approach the mouth,--tools are used in graduated sizes. The first one cuts its own line of equal width for a very short distance, then another and slightly wider tool is used, the next still wider, and so on until the river line is completed. In reality a series of steps, the work is so done that the line appears to the eye to increase in width evenly and gradually from a very fine beginning to a heavy ending. The wavy lines indicating hills and mountains are made in substantially the same way. Special steel punches are pressed through the wax to the copper to show town and capital marks, and after all the lines and marks are completed, the plate is ready to receive the lettering. The name of each individual town, city, state, or river is set up in printer's type and stamped one name at a time into the wax.
The type is placed in a small tool resembling a vise, which holds it in perfect alignment and on a perfect level. Tools of various shapes are used for stamping the names in straight and curved lines. It is necessary to wet the type to prevent its adhering to the wax.
The plate is then carefully compared with the original copy and after any necessary corrections have been made it is gone over by an expert operator, who cuts out any of the channels which may have been obliterated by the burr of the wax, resulting from pressing in the names.
We now have a plate in which the lines have been cut in small channels and the names stamped with type. This is a matrix, or mould, from which an electrotype of the lines now sunken in the wax may be made in high relief for printing, but the blank portions of the wax are so thin that it is first necessary to fill in all these places on the plates with wax in order to produce a sufficiently deep electrotype plate. This is done by "building up" the plate. A small hook-shaped tool, heated over a gas jet, is used to melt small pieces of wax which are run carefully around all the names and in the s.p.a.ces between lines, thus filling up all these s.p.a.ces with a round, smooth body of wax. From this mould an ordinary electrotype is made by the method described elsewhere in this book.
All these operations require much skill and patience at every step, but the plates produced by the wax process are always much deeper and stronger than those made by any other process.
MAKING INTAGLIO PLATES
By Elmer Latham.
The method by which a photogravure plate is produced, is probably the least understood of all of the many photo-processes of reproduction.
This is chiefly on account of the difficulty of the process, which is not an easy matter to explain in detail, and also on account of the secrecy with which all plate makers guard their processes.
The reproduction of a mezzotint or line-engraved print, when made by a good photogravure process, produces in most cases a print which cannot be detected from the original. The originator of the process was probably Fox Talbot, an Englishman. The writer has seen one of his prints, made between 1855 and 1860, which was a very creditable piece of work. Dujardin of Paris took up Talbot's process, and after much modification, succeeded in developing a successful process which he is working to-day. All photogravure plate makers of the present time have more or less copied the process of Fox Talbot.
There are three different methods of making these plates known to the writer. The reader probably knows that a photogravure plate is not a relief plate, but an intaglio, and is printed on an etching-press in the same manner as an etching and requires special skill in printing on the part of the printer to produce the best results. I will give a brief explanation of the three different processes.
The first is known as the transfer process. In this process a reversed photographic negative is made from the copy, from which a positive or "transparency" is made, either by contact or in the camera. A piece of carbon paper is then coated lightly with gelatine, sensitized with b.i.+.c.hromate of pota.s.sium and allowed to dry. The paper is then placed in contact with the positive and printed in daylight until the image is imprinted on the gelatine coating of the paper, such portions of which as have received the most exposure from the action of light becoming quite insoluble. A copper plate, cleaned so that it is free from grease, is introduced into a large box into which has been blown a very finely powdered resin, which is allowed to settle somewhat before putting in the plate. The plate is allowed to remain in the box until a fine deposit of resin has settled all over it. It is then carefully removed and heated over a gas burner until the resin adheres firmly to the plate. The resin is melted only to such a point that it forms a fine grain all over the plate, leaving interstices of bare copper between. The paper, on the gelatine surface of which the picture is printed, is now placed in a tray of warm water, and the parts of the image which have had the least exposure are thereby dissolved and washed away, the image being thus fully developed on the paper. This is placed in contact with the grained plate, which has been placed in the tray of water, and firmly squeezed in contact with the plate. The paper is stripped off, leaving the gelatine film on the copper. The plate is now removed from the tray and dried, and is then ready for etching, which is accomplished by placing the plate successively in several baths of acid of different strengths until the desired results are obtained. This process gives a shallow plate, of not great wearing quality, and, as a rule, requires a great deal of work by the engraver to bring the plate up to anything like the copy.
The light tints come out very soft and smooth, but the black tones etch "flat" and lose all detail. These blacks must be put in by hand.
The poor wearing qualities of these plates make them undesirable in cases where a large edition has to be printed.
The next process is the "deposited" plate used by "Goupil" of Paris, in which copper is deposited by electricity upon a swelled gelatine film which has had a grain formed upon its surface chemically or otherwise. The deposition has to be continued until the plate has acquired the necessary thickness, which takes about three weeks; and this is a long time to wait in these days, when a publisher usually expects his order executed in ten days. These plates are practically hand made. The process gives a plate that could not possibly be used without a great deal of retouching by an expert engraver. Goupil turns out a beautiful plate, due princ.i.p.ally to his large force of engravers, one man working on a particular part of the plate, then pa.s.sing it on to another who does some other portion, and so on, until the plate is finished. In this way each engraver becomes exceedingly skilful in one thing. Line engraving is reproduced by this process exceedingly well, but such plates, like the transfer process, are shallow and give out soon in the printing.
The last process that I have to deal with is the one I am working myself. In this process the plates are made in two or more etchings, according to the requirements of the subject which is to be reproduced. This method produces a plate of great depth both in the light and black tints, and on account of the small amount of hand-work required after the plate is etched, the copy is followed very closely.
With a good positive and favorable conditions, quite frequently a plate is made upon which the retoucher needs to do no work at all, and a more faithful reproduction is made than by any of the other methods that I have mentioned. After a good positive is procured, the copper plate is cleaned, and a sensitized solution of gelatine is flowed over the plate, dried down, and then printed under the positive, with a short exposure. The plate is grained as in the transfer process, and is then etched.
This first etching, on account of the short exposure, goes over the plate in about three minutes, and is simply intended to get the light tints. The plate is again cleaned off and coated, this time in a different manner, and given a much longer exposure under the positive.
The next etching takes about three hours, which gives the blacks great depth. Comparing this with the transfer plate which has an etching of from fifteen to twenty minutes, the reason for the difference in the wearing qualities of the plate is quite evident. This process, whether used by myself or others, I feel free to say is the best one that has ever been worked, inasmuch as it gives a far more faithful reproduction than any of the others with a minimum of work by the retoucher.
Some plate makers claim to make all their plates without any retouching, which cannot be done. As I have mentioned before, occasionally a plate can be made as good as the copy without hand-work. But to say that any chemical process gives such results continually, or that a plate cannot be improved by a skilful retoucher is, to say the least, misleading. All of the different processes are very sensitive to atmospheric influences, and no small amount of chemical as well as mechanical skill is required to keep things running smoothly; and at certain times the best of operators are at a loss to remedy some slight fault that may upset things temporarily.
Photogravure making is based upon a foundation of small details, that must be looked after with the utmost care, and the neglect of any one of which means failure at the end. So it may be surmised that at times the operator has trouble of his own.
Every maker of plates, no matter which process he uses, has his individual ways of doing things, so that except in a general way no two processes are operated alike. This gives an individuality to each man's work, and an expert can easily tell one from another. For high-cla.s.s ill.u.s.trations, no other photographic process can compare with photogravure, and no doubt it will be many years before anything will be found to excel or even equal it. Much experimenting has been done with other methods, but the results have always been inferior, and I think it is safe to predict that the photogravure will always be popular.
Etchings, mezzotints, and steel engravings are still occasionally used in the ill.u.s.tration of fine books, and brief descriptions of how they are made will be of interest.
An etching is usually made on a copper plate. The plate being covered with a thin coating of wax, the artist works on it with an etching point, sketching his subject on the plate in fine lines as he would in making a pen-and-ink drawing, but cutting his lines through to the copper. The plate is then "walled in" with a high rim of wax, forming a sort of tray of the plate. Into this tray is poured a diluted solution of nitric acid, which etches, or "bites," into the uncovered lines on the plate. Some artists give a plate a short "bite," as the etching is called, for the light lines, then cover these portions of the plate with wax and give the plate successive "bites," stopping out each part as it gains its required depth. Others remove the coating and "prove" the plate by taking a print from it after each "bite,"--each of these prints being known as a "state of the plate"
and showing what is still required to be done. In the work of an etcher like Whistler the impressions of the "first state," "second state," etc., are of considerable interest, as they show the progress of the man's work, but, except as an object of interest or as a curiosity, these prints can have no real value as they are unfinished work, simply showing the various stages in the making of a work of art.
A mezzotint is also usually made on a copper plate. A texture, or groundwork, is worked on the copper plate with a tool resembling a cabinet maker's toothed plane iron, except it is rounded at the end.
The teeth are very fine, ranging from forty to one hundred and twenty to the inch in different tools. This tool is called a "Bercier," or "rocker." The rounded edge allows the tool to be rocked across the plate, the rocking motion causing the teeth to form indentations in the copper. The rocking has to be continued until the surface of the plate is completely covered, and it then presents an appearance like velvet. Rocking in from forty to sixty directions is necessary to cover the plate properly. The durability of a mezzotint plate depends entirely upon the pressure put upon the rocker, and the depth to which it penetrates the copper. After the ground is thus laid, the outline is sketched in on the rocked surface, which takes the pencil easily, and then with steel sc.r.a.pers and burnishers the light and middle tints are worked down, leaving undisturbed the portions of the surface where the strongest blacks are to be. From time to time, a print is taken from the plate, to note the progress of the work, which advances slowly to the finish. On account of the length of time necessary for the laying of the ground and the sc.r.a.ping of the plate, many artists hesitate to attempt mezzotint plates. There are very few men in this country to-day who do mezzotint engraving, which, considering the results to be obtained, seems somewhat surprising.
For flesh tones, drapery, and landscapes it has no equal. The velvety richness of the blacks, the beautiful gradations of the middle tones, and the extreme delicacy of the light tints give the artist a power of expression not obtainable by any other method of engraving. Besides this, as the engraving is done on the bare copper, the artist can see at all times the progress of his work without having to take off the wax ground as he must in making an etching. This is a great advantage, for as the effect of each stroke can be plainly seen on the plate, the element of uncertainty which always attends the production of an etching is entirely eliminated, and it is then simply a question of skill with the sc.r.a.per. The difficulty of obtaining rockers is one great drawback. I doubt if one could be obtained in New York to-day.
The teeth have to be very accurately cut, and a perfect tool has a value to an engraver that cannot well be estimated. The lack of demand has prevented their manufacture in this country, but they could be made here by any fine tool maker.
Steel engravings are still used to some extent in this country, although only in portrait work. A wax ground is laid on the plate as in etching. A tracing is made from the photograph, from which the picture is to be made, and is then transferred to the wax ground. The engraver then follows the lines of the tracing with an etching point, the hair, head, and outline of the features being gone over carefully.
Then the plate is etched with weak nitric acid. If the face is to be "stippled," it is covered with fine dots made by a graver directly on the surface of the metal after the plate has been etched and the wax cleaned off. If the face is to be a mezzotint, that part of the work is all rocked over, and then sc.r.a.ped down within the etched outline, when the flesh is modelled as in a regular mezzotint. The drapery, background, etc., is usually done by a ruling machine with fine or coa.r.s.e, waved or straight lines, as the texture may require. These lines are ruled through a coating of wax, and then, by etching and stopping out, the required results are obtained.
This method of engraving is also giving place to process work, and in a few years more the steel engraved portrait will probably be a thing of the past.
PRINTING INTAGLIO PLATES
By George W. H. Ritchie.
The method of printing etchings, mezzotint, and other intaglio plates is the same to-day as it was in the time of Rembrandt and Durer. The modern inventor has found no way to economize time, labor, or expense in the work--excepting that in the case of postage stamps, bond certificates, and similar plates, which are printed in vast quant.i.ties, the work has been adapted to the steam press.
In the olden time the engraver, or etcher, himself was to a considerable extent his own printer. He worked at engraving his plate until he needed a proof to show him how the work was progressing. Then he printed, or "pulled," a proof and resumed his work, taking proofs from time to time until he had completed the plate to his satisfaction. Then, if only a small edition was required, he printed it. Proofs taken during the making of a plate are known by plate engravers and printers as the "states" of a plate, and it is due to the whim of the etcher, the softness of the copper, and the wearing of the plate in printing that we have prints representing many "states"
of a single plate which might otherwise have had but one state, thus depriving one modern print collector of the privilege of discovering in his proof three hairs more or less in a donkey's tail than his rival finds in another proof, which makes the former's more valuable by several hundred pounds.
One form of press is used for all manner of intaglio plate printing.
It consists of a framework supporting two heavy iron rollers, between which moves a flat iron travelling plank, or bed, and on this bed the plate to be printed is laid. The pressure of the rollers is regulated by screws at each end of the top roller, which is covered with two or three pieces of thick felt. This top roller is revolved by handles and the bed moves along with it under the pressure of the roller. At one side of the press stands a rectangular box, or "stove," made of iron, or having an iron top. The top is heated by gas and on it the printer puts his plate while inking and wiping it. The heat thins the ink as it is applied, allowing it to be worked freely and to be "lifted"
easily by the paper.
The ink is made of fine bone dust, vegetable or other form of carbon, which has been carefully cleansed from foreign matter and ground to the necessary fineness in combination with burned linseed oil. Its strength and consistency should be varied according to the plate which is in hand, and the color also may be varied to suit the character of the plate by the addition of pigments.
The paper used in plate printing may be one of several kinds, but the usual variety is a fine white paper free from spots and imperfections which might mar the appearance of the finished print. This paper is made either by hand or machinery of selected bleached cotton rags, and has a soft, spongy surface which yields readily under the pressure of the plate. Before it can be used the paper is moistened and allowed to stand for from one to twelve hours, or even longer, until it becomes evenly and thoroughly dampened,--but not wet,--so that it will more readily force itself into the lines of the plate and take therefrom and hold the ink.
Before printing a photogravure, mezzotint, or other engraved plate the printer must first carefully examine it to see that it has no scratches, and that no dried ink remains in the lines from the last printing, and, in fact, that there are none of the many possible impedimenta which might prevent the production of a perfect print. The plate being in proper condition, it is then thoroughly cleansed with turpentine or benzine, all traces of which must be carefully wiped from the surface before the ink is applied. The plate is then laid on the heated iron box or "stove" until it has become thoroughly warmed.
The surface of the plate is covered with ink, put on by means of an ink-roller, or perhaps the old-fas.h.i.+oned dauber, and the ink is thoroughly worked into the lines or depressions in the plate. After this the ink on the flat surface of the plate is entirely removed by wiping with rags. The printer's hand, which has become more or less covered with ink from the rags, is then pa.s.sed over a piece of chalk, or gilder's white, and lightly rubbed over the surface of the plate, to remove the last vestige of the ink, leaving a highly polished flat surface with the incised lines or depressions filled with ink to the level of the surface.
The plate is then ready for printing and is placed on the bed of the press, a sheet of dampened paper laid upon it, and both are then run between the rollers of the press. As the top roller is encased in soft blankets, the soft, dampened paper is forced into the ink-filled lines of the plate, and when the paper is removed the ink clings to it and shows an exact impression of the engraving. This entire process must be repeated for each print made from an intaglio plate.
While the printing of a steel engraving or photogravure is a more or less mechanical operation, the printing of an etching--and "dry points" may be included--is oftentimes as much of an art as the actual etching of the plate. The two styles of printing may be compared to two kinds of fis.h.i.+ng,--that of fis.h.i.+ng for flounders with a drop line, from a flat-bottomed boat at low tide when one must just sit tight until one has a bite, and then haul in the fish, bait up, drop the line and wait again, as against that of angling for trout on an early spring day, dropping the fly in a likely spot without success at the first cast, persevering until rewarded by a rise and then by the sport of playing the fish, giving him line and reeling him in as about he circles and finally is landed. A good one, perchance, but the sport was in landing him. So it is with printing an etching. There is the opportunity to play with, and work hard over, a plate. Perhaps the etcher has not, for reasons only known to himself, put in the plate all that can be shown in the print by ordinary printing. The printer actually has to interpret in his printing the etcher's meaning, for the which, as a rule, he gets "more kicks than ha'pence," and in the end wishes he had stuck to plain plate printing as far as the profit is concerned.
In the process of printing an etching, the printer first covers the plate with ink and then wipes it with the rags, and, if necessary, with the hand. It depends entirely upon the etched work of the plate as to how it must be wiped, and it rests with the printer to prepare a proof which is satisfactory to the etcher. The plate is wiped "closely" where the high lights are required or a tint (a thin coating of ink) left over certain portions where it needs to be darker. After this the plate is "retroussed," which is accomplished by pa.s.sing a very soft piece of fine muslin, or a "badger blender,"--a soft brush used by artists,--delicately over the work in the plate and drawing the ink up and over the edges of the lines. This softens and broadens the lines and gives a very rich effect, and, if continued sufficiently, fills the s.p.a.ces between the lines and produces an almost black effect. All this work is varied according to the wishes of the etcher. A plate that left the etcher's hand a mere skeleton may be made to produce a print which is a thing of life. The possibilities of an etching in the hands of a skilful printer are almost limitless; the effects can vary with every impression, each showing a new picture. His processes are as interesting as those of the etcher himself, and it is within his capabilities to transform an etching from a broad daylight effect into a moonlight scene, including the moon, by judiciously, or injudiciously, inking and wiping the plate.
The Building of a Book Part 10
You're reading novel The Building of a Book Part 10 online at LightNovelFree.com. You can use the follow function to bookmark your favorite novel ( Only for registered users ). If you find any errors ( broken links, can't load photos, etc.. ), Please let us know so we can fix it as soon as possible. And when you start a conversation or debate about a certain topic with other people, please do not offend them just because you don't like their opinions.
The Building of a Book Part 10 summary
You're reading The Building of a Book Part 10. This novel has been translated by Updating. Author: Theodore Low De Vinne and Frederick H. Hitchcock already has 576 views.
It's great if you read and follow any novel on our website. We promise you that we'll bring you the latest, hottest novel everyday and FREE.
LightNovelFree.com is a most smartest website for reading novel online, it can automatic resize images to fit your pc screen, even on your mobile. Experience now by using your smartphone and access to LightNovelFree.com
- Related chapter:
- The Building of a Book Part 9
- The Building of a Book Part 11
RECENTLY UPDATED NOVEL
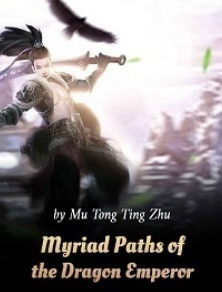
Myriad Paths of the Dragon Emperor
Myriad Paths of the Dragon Emperor Chapter 3127-chaotic battle View : 1,685,064
Madam's Identities Shocks The Entire City Again
Madam's Identities Shocks The Entire City Again Chapter 3509: Master Wang Isn't To Be Someone Not To Be Trifled With (1) View : 2,737,620
Complete Martial Arts Attributes
Complete Martial Arts Attributes Chapter 3007: Blood God Curse! View : 2,950,753
Hi, My Sweet Lil Moe Wife!
Hi, My Sweet Lil Moe Wife! Chapter 2404: She doesn't look like her biological mother View : 551,662
Spending My Retirement In A Game
Spending My Retirement In A Game Chapter 922 Aggressive Map-Making View : 1,197,171