Steam Turbines Part 3
You’re reading novel Steam Turbines Part 3 online at LightNovelFree.com. Please use the follow button to get notification about the latest chapter next time when you visit LightNovelFree.com. Use F11 button to read novel in full-screen(PC only). Drop by anytime you want to read free – fast – latest novel. It’s great if you could leave a comment, share your opinion about the new chapters, new novel with others on the internet. We’ll do our best to bring you the finest, latest novel everyday. Enjoy!
Any engineer who is capable of running and intelligently taking care of a reciprocating engine can run and take care of a turbine, but if he is to be anything more than a starter and stopper, it is necessary that he should know what is inside of the casing, what must be done and avoided to prevent derangement, and to keep the machine in continued and efficient operation.
In the steam turbine the steam instead of being expanded against a piston is made to expand against and to get up velocity in itself. The jet of steam is then made to impinge against vanes or to react against the moving orifice from which it issues, in either of which cases its velocity and energy are more or less completely abstracted and appropriated by the revolving member. The Parsons turbine utilizes a combination of these two methods.
[Ill.u.s.tration: FIG. 34]
Fig. 34 is a sectional view of the standard Westinghouse-Parsons single-flow turbine. A photograph of the rotor R R R is reproduced in Fig. 35, while in Fig. 36 a section of the blading is shown upon a larger scale. Between the rows of the blading upon the rotor extend similar rows of stationary blades attached to the casing or stator. The steam entering at A (Fig. 34), fills the circular s.p.a.ce surrounding the rotor and pa.s.ses first through a row of stationary blades, 1 (Fig. 37), expanding from the initial pressure P to the slightly lower pressure P{1}, and attaining by that expansion a velocity with which it is directed upon the moving blade 2. In pa.s.sing through this row of blades it is further expanded from pressure P{1} to P{2} and helps to push the moving blades along by the reaction of the force with which it issues therefrom. Impinging upon the second row of stationary blades 3, the direction of flow is diverted so as to make it impinge at a favorable angle upon the second row of revolving blades 4, and the action is continued until the steam is expanded to the pressure of the condenser or of the medium into which the turbine finally exhausts. As the expansion proceeds, the pa.s.sages are made larger by increasing the length of the blades and the diameter of the drums upon which they are carried in order to accommodate the increasing volume.
[Ill.u.s.tration: FIG. 35]
[Ill.u.s.tration: FIG. 36]
[Ill.u.s.tration: FIG. 37]
It is not necessary that the blades shall run close together, and the axial clearance, that is the s.p.a.ce lengthwise of the turbine between the revolving and the stationary blades, varies from 1/8 to 1/2 inch; but in order that there may not be excessive leakage over the tops of the blades, as shown, very much exaggerated, in Fig. 38, the radial clearance, that is, the clearance between the tops of the moving blades and the casing, and between the ends of the stationary blades and the sh.e.l.l of the rotor, must be kept down to the lowest practical amount, and varies, according to the size of the machine and length of blade, from about 0.025 to 0.125 of an inch.
[Ill.u.s.tration: FIG. 38]
In the pa.s.sage A (Fig. 34) exists the initial pressure; in the pa.s.sage B the pressure after the steam has pa.s.sed the first section or diameter of the rotor; in the pa.s.sage C after it has pa.s.sed the second section. The pressure acting upon the exposed faces of the rows of vanes would crowd the rotor to the left. They are therefore balanced by pistons or "dummies" P P P revolving with the shaft and exposing in the annular s.p.a.ces B^1 and C^1 the same areas as those of the blade sections which they are designed to balance. The same pressure is maintained in B^1 as in B, and in C^1 as in C by connecting them with equalizing pipes E E.
The third equalizing pipe connects the back or right-hand side of the largest dummy with the exhaust pa.s.sage so that the same pressure exists upon it as exists upon the exhaust end of the rotor. These dummy pistons are shown at the near end of the rotor in Fig. 35. They are grooved so as to form a labyrinth packing, the face of the casing against which they run being grooved and bra.s.s strips inserted, as shown in Fig. 39.
The dummy pistons prevent leakage from A, B^1 and C^1 to the condenser, and must, of course, run as closely as practicable to the rings in the casing, the actual clearance being from about 0.005 to 0.015 of an inch, again depending on the size of the machine.
[Ill.u.s.tration: FIG. 39]
The axial adjustment is controlled by the device shown at T in Fig. 34 and on a larger scale in Fig. 40. The thrust bearing consists of two parts, T{1} T{2}. Each consists of a cast-iron body in which are placed bra.s.s collars. These collars fit into grooves C, turned in the shaft as shown. The halves of the block are brought into position by means of screws S{1} S{2} acting on levers L{1} L{2} and mounted in the bearing pedestal and cover. The screws are provided with graduated heads which permit the respective halves of the thrust bearing to be set within one one-thousandth of an inch.
[Ill.u.s.tration: FIG. 40]
The upper screw S{2} is set so that when the rotor exerts a light pressure against it through the thrust block and lever the grooves in the balance pistons are just unable to come in contact with the dummy strips in the cylinder. The lower screw S{1} is then adjusted to permit about 0.008 to 0.010 of an inch freedom for the collar between the grooves of the thrust bearing.
These bearings are carefully adjusted before the machine leaves the shop, and to prevent either accidental or unauthorized changes of their adjustment the adjusting screw heads are locked by the method shown in Fig. 40. The screw cannot be revolved without sliding back the latch L{3}. To do this the pin P{4} must be withdrawn, for which purpose the bearing cover must be removed.
In general this adjustment should not be changed except when there has been some wear of the collars in the thrust bearing; nevertheless, it is a wise precaution to go over the adjustment at intervals. The method of doing this is as follows: The machine should have been in operation for some time so as to be well and evenly heated and should be run at a reduced speed, say 10 per cent. of the normal, during the actual operation of making the adjustment. Adjust the upper screw which, if tightened, would push the spindle away from the thrust bearing toward the exhaust. Find a position for this so that when the other screw is tightened the balance pistons can just be heard to touch, and so the least change of position inward of the upper screw will cause the contact to cease. To hear if the balance pistons are touching, a short piece of hardwood should be placed against the cylinder casing near the balance piston. If the ear is applied to the other end of the piece of wood the contact of the balance pistons can be very easily detected. The lower screw should then be loosened and the upper screw advanced from five to fifteen one-thousandths, according to the machine, at which position the latter may be considered to be set. The lower screw should then be advanced until the under half of the thrust bearing pushes the rotor against the other half of the thrust bearing, and from this position it should be pushed back ten or more one-thousandths, to give freedom for the rotor between the thrusts, and locked. A certain amount of care should be exercised in setting the dummies, to avoid straining the parts and thus obtain a false setting.
The object in view is to have the grooves of the balance pistons running as close as possible to the collars in the cylinder, but without danger of their coming in actual contact, and to allow as little freedom as possible in the thrust bearing itself, but enough to be sure that it will not heat. The turbine rotor itself has scarcely any end thrust, so that all the thrust bearing has to do is to maintain the above-prescribed adjustment.
The blades are so gaged that at all loads the rotor has a very light but positive thrust toward the running face of the dummy strips, thus maintaining the proper clearance at the dummies as determined by the setting of the proper screw adjustment.
Main Bearings
The bearings which support the rotor are shown at F F in Fig. 34 and in detail in Fig. 41. The bearing proper consists of a bra.s.s tube B with proper oil grooves. It has a dowel arm L which fits into a corresponding recess in the bearing cover and which prevents the bearing from turning.
On this tube are three concentric tubes, C D E, each fitting over the other with some clearance so that the shaft is free to move slightly in any direction. These tubes are held in place by the nut F, and this nut, in turn, is held by the small set-screw G. The bearing with the surrounding tubes is placed inside of the cast-iron sh.e.l.l A, which rests in the bearing pedestal on the block and liner H. The packing ring M prevents the leakage of oil past the bearing. Oil enters the chamber at one end of the bearing at the top and pa.s.ses through the oil grooves, lubricating the journal, and then out into the reservoir under the bearing. The oil also fills the clearance between the tubes and forms a cus.h.i.+on, which dampens any tendency to vibration.
[Ill.u.s.tration: FIG. 41]
The bearings, being supported by the blocks or "pads" H, are self-alining. Under these pads are liners 5, 10, 20, and 50 thousandths in thickness. By means of these liners the rotor may be set in its proper running position relative to the stator. This operation is quite simple. Remove the liners from under one bearing pad and place them under the opposite pad until a blade touch is obtained by turning the rotor over by hand. After a touch has been obtained on the top, bottom, and both sides, the total radial blade clearance will be known to equal the thickness of the liners transferred. The position of the rotor is then so adjusted that the radial blade clearance is equalized when the turbine is at operating temperature.
On turbines running at 1800 revolutions per minute or under, a split babbitted bearing is used, as shown in Figs. 42a and 42b. These bearings are self-alining and have the same liner adjustment as the concentric-sleeve bearings just described. Oil is supplied through a hole D in the lower liner pad, and is carried to the oil groove F through the tubes E E. The oil flows from the middle of this bearing to both ends instead of from one end to the other, as in the other type.
[Ill.u.s.tration: FIG. 42A]
[Ill.u.s.tration: FIG. 42B]
Packing Glands
Where the shaft pa.s.ses through the casing at either end it issues from a chamber in which there exists a vacuum. It is necessary to pack the shaft at these points, therefore, against the atmospheric pressure, and this is done by means of a water-gland packing W W (Fig. 34). Upon the shaft in Fig. 35, just in front of the dummy pistons, will be seen a runner of this packing gland, which runner is shown upon a larger scale and from a different direction in Fig. 43. To get into the casing the air would have to enter the guard at A (Fig. 44), pa.s.s over the projecting rings B, the function of which is to throw off any water which may be creeping along the shaft by centrifugal force into the surrounding s.p.a.ce C, whence it escapes by the drip pipe D, hence over the five rings of the labyrinth packing E and thence over the top of the revolving blade wheel, it being apparent from Fig. 43 that there is no way for the air to pa.s.s by without going up over the top of the blades; but water is admitted to the centrally grooved s.p.a.ce through the pipe shown, and is revolved with the wheel at such velocity that the pressure due to centrifugal force exceeds that of the atmosphere, so that it is impossible for the air to force the water aside and leak in over the tips of the blades, while the action of the runner in throwing the water out would relieve the pressure at the shafts and avoid the tendency of the water to leak outward through the labyrinth packing either into the vacuum or the atmosphere.
[Ill.u.s.tration: FIG. 43]
[Ill.u.s.tration: FIG. 44]
The water should come to the glands under a head of about 10 feet, or a pressure of about 5 pounds, and be connected in such a way that this pressure may be uninterruptedly maintained. Its temperature must be lower than the temperature due to the vacuum within the turbine, or it will evaporate readily and find its way into the turbine in the form of steam.
[Ill.u.s.tration: FIG. 45]
In any case a small amount of the steaming water will pa.s.s by the gland collars into the turbine, so that if the condensed steam is to be returned to the boilers the water used in the glands must be of such character that it may be safely used for feed water. But whether the water so used is to be returned to the boilers or not it should never contain an excessive amount of lime or solid matter, as a certain amount of evaporation is continually going on in the glands which will result in the deposit of scale and require frequent taking apart for cleaning.
[Ill.u.s.tration: FIG. 46]
When there is an ample supply of good, clean water the glands may be packed as in Fig. 45, the standpipe supplying the necessary head and the supply valve being opened sufficiently to maintain a small stream at the overflow. When water is expensive and the overflow must be avoided, a small float may be used as in Fig. 46, the ordinary tank used by plumbers for closets, etc., serving the purpose admirably.
When the same water that is supplied to the glands is used for the oil-cooling coils, which will be described in detail later, the coils may be attached to either of the above arrangements as shown in Fig. 47.
[Ill.u.s.tration: FIG. 47]
When the only available supply of pure water is that for the boiler feed, and the condensed steam is pumped directly back to the boiler, as shown in Fig. 48, the delivery from the condensed-water pumps may be carried to an elevation 10 feet above the axis of the glands, where a tank should be provided of sufficient capacity that the water may have time to cool considerably before being used. In most of these cases, if so desired, the oil-cooling water may come from the circulating pumps of the condenser, provided there is sufficient pressure to produce circulation, as is also shown in Fig. 48.
[Ill.u.s.tration: FIG. 48]
When the turbine is required to exhaust against a back pressure of one or two pounds a slightly different arrangement of piping must be made.
The water in this case must be allowed to circulate through the glands in order to keep the temperature below 212 degrees Fahrenheit. If this is not done the water in the glands will absorb heat from the main castings of the machine and will evaporate. This evaporation will make the glands appear as though they were leaking badly. In reality it is nothing more than the water in the glands boiling, but it is nevertheless equally objectionable. This may be overcome by the arrangement shown in Fig. 49, where two connections and valves are furnished at M and N, which drain away to any suitable tank or sewer.
These valves are open just enough to keep sufficient circulation so that there is no evaporation going on, which is evidenced by steam coming out as though the glands were leaking. These circulating valves may be used with any of the arrangements above described.
[Ill.u.s.tration: FIG. 49]
The Governor
On the right-hand end of the main shaft in Fig. 34 there will be seen a worm gear driving the governor. This is shown on a larger scale at A (Fig. 50). At the left of the worm gear is a bevel gear driving the spindle D of the governor, and at the right an eccentric which gives a vibratory motion to the lever F. The crank C upon the end of the shaft operates the oil pump. The speed of the turbine is controlled by admitting the steam in puffs of greater or less duration according to the load. The lever F, having its fulcrum in the collar surrounding the shaft, operates with each vibration of the eccentric the pilot valve.
The valve is explained in detail later.
[Ill.u.s.tration: FIG. 50]
This form of governor has been superseded by an improved type, but so many have been made that it will be well to describe its construction and adjustment. The two b.a.l.l.s W W (Fig. 50) are mounted on the ends of bell cranks N, which rest on knife edges. The other end of the bell cranks carry rollers upon which rest a plate P, which serves as a support for the governor spring S. They are also attached by links to a yoke and sleeve E which acts as a fulcrum for the lever F. The governor is regulated by means of the spring S resting on the plate P and compressed by a large nut G on the upper end of the governor spindle, which nut turns on a threaded quill J, held in place by the nut H on the end of the governor spindle and is held tight by the lock-nut K. To change the compression of the spring and thereby the speed of the turbine the lock-nut must first be loosened and the hand-nut raised to lower the speed or lowered to raise the speed as the case may be. This operation may be accomplished while the machine is either running or at rest.
The plate P rests upon ball bearings so that by simply bringing pressure to bear upon the hand-wheel, which is a part of the quill J, the spring and lock-nut may be held at rest and adjusted while the rest of the turbine remains unaffected. Another lever is mounted upon the yoke E on the pin shown at I, the other end of which is fastened to the piston of a dash-pot so as to dampen the governor against vibration. Under the yoke E will be noticed a small trigger M which is used to hold the governor in the full-load position when the turbine is at rest.
The throwing out of the weights elevates the sleeve E, carrying with it the collar C, which is spanned by the lever F upon the shaft H. The later turbines are provided with an improved form of governor operating on the same principle, but embodying several important features. First, the spindle sleeve is integral with the governor yoke, and the whole rotates about a vertical stationary spindle, so that two motions are encountered--a rotary motion and an up and down motion, according to the position taken by the governor. This spiral motion almost entirely eliminates the effect of friction of rest, and thereby enhances the sensitiveness of the governor. Second, the governor weights move outward on a parallel motion opposed directly by spring thrust, thus relieving the fulcrum entirely of spring thrust. Third, the lay shaft driving the governor oil pump and reciprocator is located underneath the main turbine shaft, so that the rotor may be readily removed without in the least disturbing the governor adjustment.
Steam Turbines Part 3
You're reading novel Steam Turbines Part 3 online at LightNovelFree.com. You can use the follow function to bookmark your favorite novel ( Only for registered users ). If you find any errors ( broken links, can't load photos, etc.. ), Please let us know so we can fix it as soon as possible. And when you start a conversation or debate about a certain topic with other people, please do not offend them just because you don't like their opinions.
Steam Turbines Part 3 summary
You're reading Steam Turbines Part 3. This novel has been translated by Updating. Author: Hubert E. Collins already has 638 views.
It's great if you read and follow any novel on our website. We promise you that we'll bring you the latest, hottest novel everyday and FREE.
LightNovelFree.com is a most smartest website for reading novel online, it can automatic resize images to fit your pc screen, even on your mobile. Experience now by using your smartphone and access to LightNovelFree.com
- Related chapter:
- Steam Turbines Part 2
- Steam Turbines Part 4
RECENTLY UPDATED NOVEL

Beauty and the Bodyguard
Beauty and the Bodyguard Chapter 11374: Chapter 11372: The Battle of the Three Kingdoms! View : 5,562,562
Springtime Farming: A Happy Wife At Home
Springtime Farming: A Happy Wife At Home Chapter 1425: Disappointment View : 516,233
I Get A Random New Occupation Every Week
I Get A Random New Occupation Every Week Chapter 2170: 2171: Into the Tiger's Den View : 1,525,560
I Swear I Don't Have A Python In My Pool
I Swear I Don't Have A Python In My Pool Chapter 1343: The Clone Becomes the Master?! View : 397,047
Online Game: I Can Use Ultimate Skills Infinitely
Online Game: I Can Use Ultimate Skills Infinitely Chapter 1371: Chu Bai's Plan View : 492,966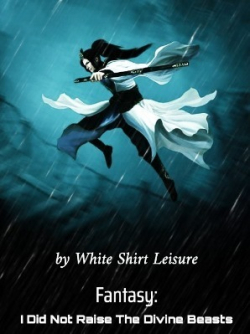
Fantasy: I Did Not Raise The Divine Beasts
Fantasy: I Did Not Raise The Divine Beasts Chapter 1123: Brother Is Here (1) View : 392,552
The Beloved and Pampered Girl
The Beloved and Pampered Girl Chapter 1040: Sorry, I Don't Think I Can Help You View : 351,219
Maximum Comprehension: Taking Care of Swords In A Sword Pavilion
Maximum Comprehension: Taking Care of Swords In A Sword Pavilion Chapter 2259: 1015, sixty years later, return to the Great Pantheon Plane View : 879,658