Diggers in the Earth Part 3
You’re reading novel Diggers in the Earth Part 3 online at LightNovelFree.com. Please use the follow button to get notification about the latest chapter next time when you visit LightNovelFree.com. Use F11 button to read novel in full-screen(PC only). Drop by anytime you want to read free – fast – latest novel. It’s great if you could leave a comment, share your opinion about the new chapters, new novel with others on the internet. We’ll do our best to bring you the finest, latest novel everyday. Enjoy!
If you look on the back of the spoon, you will perhaps see "Rogers Bros. 1846." These men were the first silvermakers in this country to plate tableware by electricity. To make a spoon, they formed one out of iron or copper and made sure that it was perfectly clean. Then across a bath of silver cyanide, pota.s.sium cyanide, and water they laid two metal rods, and from these they hung a spoon at one end and a plate of silver at the other. These rods were connected with the two poles of a battery. The electrical current pa.s.sed through them, released the silver from the silver cyanide, and this was deposited upon the spoon. The cyanide that had lost its silver took enough more from the silver plate to make up. The amount of silver on the spoon depends upon the length of time it remains in the bath. It is weighed before plating and again afterwards, to make sure that the proper amount of silver has been deposited upon it. On the back of many plated articles you will see the words "Triple plate" or "Quadruple plate." If the article has been made by a reliable firm, this means that the triple plate it manufactures contains three times as much silver as "single plate," and that quadruple plate contains four times as much. A piece of silver looks just as well if it has stayed in the bath only a few minutes, but of course it has taken on so little silver that this will soon wear off and show the cheaper metal.
A large amount of silver is used for coins. When the United States needs dollars, half-dollars, quarters, and dimes, notice is given and offers are called for, stating the quant.i.ty for sale and its price.
When it is delivered, it is first of all "a.s.sayed"; that is, tested to find out how nearly pure it is and how much it is worth. Next it is refined, or purified from other metals, mixed with a little copper to harden it, then melted again and poured into moulds to make bars. If dollars are to be made, the bar is made thinner by pa.s.sing it between heavy rollers, and blanks for dollars are cut out with a die. These blanks are weighed and every one that is too heavy or too light is put back to be melted over again. Thus far these dollars are only round, smooth pieces of metal. They must be milled to give them a rough edge, and they must be stamped. For stamping, the piece of metal is placed between two dies, one above and one below, and these close upon it with a force of one hundred and fifty tons. Every part of the process of manufacturing money is carried on with the utmost care. The places where coins are made are called "mints." The United States has four; the oldest is in Philadelphia, and there are branch mints in San Francisco, New Orleans, and Denver. Coins minted in Philadelphia have no distinguis.h.i.+ng mark; but coins minted in San Francisco are marked with a tiny "S"; if minted in New Orleans, with an "O"; and if in Denver, with a "D."
VII
IRON, THE EVERYDAY METAL
Did you ever realize that your food and clothes, your books, and the house in which you live all depend upon iron? Vegetables, grains, and fruits are cultivated with iron tools; fish are caught with iron hooks, and many iron articles are used in the care and sale of meat.
Clothes are woven on iron looms, sewed with iron needles, and fastened together with b.u.t.tons containing iron. Books are printed and bound by iron machines, and sometimes written with iron pens or on iron typewriters. Houses are put together with nails; and indeed, there is hardly an article in use that could be made as well or as easily if iron was not plenty. If you were making a world and wanted to give the people the most useful metal possible, the gift would have to be iron; and the wisest thing you could do would be to put it everywhere, but in such forms that the people would have to use their brains to make it of service.
This is just the way with the iron in our world. Wherever you see a bank of red sand or red clay or a little brook which leaves a red mark on the ground as it flows, there is iron. Iron is in most soils, in red bricks, in garnets, in ripening apples, and even in your own blood. It forms one twentieth part of the crust of the earth. Iron dissolves in water if you give it time enough. If you leave a steel tool out of doors on a wet night, it will rust; that is, some of the iron will unite with the oxygen of the water. This is rather inconvenient, and yet in another way this dissolving is a great benefit. Through the millions of years that are past, the oxygen of the rain has dissolved the iron in the hills and has worked it down, so that now it is in great beds of ore or in rich "pockets" that are often of generous size. One of them, which is now being mined in Minnesota, is more than two miles long, half a mile wide, and of great thickness. The rains are still at work was.h.i.+ng down iron from the hills. They carry the tiny particles along as easily as possible until they come upon limestone. Then, almost as if it was frightened, the brook drops its iron and runs away as fast as it can. Sometimes it flows into a pond or bog in which are certain minute plants or animals that act as limestone does, and the particles of iron fall to the bottom of the pond. In colonial days much of the iron worked in America was taken from these deposits. One kind of iron is of special interest because it comes directly from the sky, and falls in the shape of stones called "meteorites," some of which weigh many tons. In some of the old fables about wonderful heroes, the stories sometimes declare that the swords with which they accomplished their deeds of prowess fell straight from the heavens, which probably means that they were made of meteoric iron. Fortunately for the people and their homes, meteorites are not common, but every large museum has specimens of them.
It is not especially difficult to make iron if you have the ore, a charcoal fire in a little oven of stones, and a pair of bellows. Put on layers of charcoal alternating with layers of ore, blow the bellows, and by and by you will have a lump of iron. It is not really melted, but it can be pounded and worked. This is called the "Catalan method," because the people of Catalonia in Spain made iron in this way. It is still used by the natives of the interior of Africa. But if all the iron was made by this method, it would be far more costly than gold. The man who makes iron in these days must have an immense "blast furnace," perhaps one hundred feet high, a real "pillar of fire." Into this furnace are dropped ma.s.ses of ore, and with it c.o.ke to make it hotter and limestone to carry off the silica slag, or worthless part.
To increase the heat, blasts of hot air are blown into the bottom of the furnace. This air is heated by pa.s.sing it through great steel cylinders as high as the furnace. The fuel used is nothing more than the gases which come out at the top of the furnace.
The slag is so much lighter than iron that when the ore is melted the slag floats on top just as oil floats on water, and can be drained out of the furnace through a higher opening than that through which the iron flows. The slag tap is open most of the time, but the iron tap is opened only once in about six hours. It is a magnificent sight when a furnace is "tapped" and the stream of iron drawn off. Imagine a great shed, dark and gloomy, with many workmen hurrying about to make ready for what is to come. The floor is of sand and slopes down from the furnace. Through the center of this floor runs a long ditch straight from the furnace to the end of the shed. Opening from it on both sides are many smaller ditches; and connecting with these are little gravelike depressions two or three feet long and as close together as can be. These are called "pigs." When the time has come, the workmen gather about the furnace, and with a long bar they drill into the hard-baked clay of the tapping hole. Suddenly it breaks, and with a rush and a roar the crimson flood of molten iron gushes out. It flows down the trench into the ditches, then into the pigs, till their whole pattern is marked out in glowing iron. Now the blast begins to drive great beautiful sparks through the tapping hole. This means that the molten iron is exhausted. The blast is turned off, and the "mud-gun"
is brought into position and shoots b.a.l.l.s of clay into the tapping hole to close it for another melting, or "drive." The crimson pigs become rose-red, darken, and turn gray. The men play streams of water over them and the building is filled with vapor. As soon as the pigs are cool enough, they are carted away and piled up outside the building.
In some iron works moulds of pressed steel carried on an endless chain are used instead of sand floors. The chain carries them past the mouth of a trough full of melted iron. They are filled, borne under water to be cooled, and then dropped upon cars. A first-cla.s.s machine can make twenty pigs a minute.
[Ill.u.s.tration: IN THE STEEL FOUNDRY
It is a dangerous business to visit a steel mill. Tremendous kettles travel overhead on huge cranes, hot metal flows from unexpected places, and there is a constant glow and steam and roar everywhere to confuse the unwary.]
Most of the iron made in blast furnaces is turned into steel. Steel has been made for centuries, but until a few years ago the process was slow and costly. A workman's steel tools were treasures, and a good jackknife was a valuable article. Railroads were using iron rails.
They soon wore out, but at the suggestion to use steel, the presidents of the roads would have exclaimed, "Steel, indeed! We might as well use silver!" Trains needed to be longer and heavier, but iron rails and bridges could not stand the strain. Land in cities was becoming more valuable; higher buildings were needed, but stone was too expensive. Everywhere there was a call for a metal that should be strong and cheap. Iron was plentiful, but steel was dear. A cheaper method of making iron into steel was needed; and whenever there is pressing need of an invention, it is almost sure to come. Before long, what is known as the "Bessemer process" was invented. One great difficulty in the manufacture of steel was to leave just the right amount of carbon in the iron. Bessemer simply took it all out, and then put back exactly what was needed. Molten iron, tons and tons of it, is run into an immense pear-shaped vessel called a "converter."
Fierce blasts of air are forced in from below. These unite with the carbon and destroy it. There is a roar, a clatter, and a clang.
Terrible flames of glowing red shoot up. Suddenly they change from red to yellow, then to white; and this is the signal that the carbon has been burned out. The enormously heavy converter is so perfectly poised that a child can move it. The workmen now tilt it and drop in whatever carbon is needed. The molten steel is poured into square moulds, forming ma.s.ses called "blooms," and is carried away. More iron is put into the converter, and the work begins again.
The Bessemer process makes enormous ma.s.ses of steel and makes it very cheaply; but it has one fault--it is too quick. The converter roars away for a few minutes, till the carbon and other impurities are burned out; and the men have no control over the operation. In what is called the "open-hearth" process, pig iron, sc.r.a.p iron, and ore are melted together with whatever other substances may be needed to make the particular kind of steel desired. This process takes much longer than the Bessemer, but it can be controlled. Open-hearth steel is more h.o.m.ogeneous,--that is, more nearly alike all the way through,--and is better for some purposes, while for others the Bessemer is preferred.
Steel is hard and strong, but it has two faults. A steel bar will stand a very heavy blow and not break, but if it is struck gently many thousand times, it sometimes crystallizes and may snap. A steel rail may carry a train for years and then may crystallize and break and cause a wreck. Inventors are at work discovering alloys to prevent this crystallization. The second fault of steel is that it rusts and loses its strength. That is why an iron bridge or fence must be kept painted to protect it from the moisture in the air.
If all the iron that is in use should suddenly disappear, did you ever think what would happen? Houses, churches, skysc.r.a.pers, and bridges would fall to the ground. Railroad trains, automobiles, and carriages would become heaps of rubbish. s.h.i.+ps would fall apart and become only scattered planks floating on the surface of the water. Clocks and watches would become empty cases. There would be no machines for manufacturing or for agriculture, not even a spade to dig a garden.
Everybody would be out of work. If you wish to see how it would seem, try for an hour to use nothing that is of iron or has been made by using iron.
VIII
OUR GOOD FRIEND COPPER
Where did rocks come from?
Some were deposited in water, like limestone and like the shale and sandstone that lie over the strata of coal. Others were made by fire, and were thrown up in a melted state from the interior of the earth.
Such rocks are the Giant's Causeway in Ireland and the Palisades of the Hudson River. They are called "igneous" rocks, from the Latin word _ignis_ meaning "fire."
When the igneous rocks were thrown up to the surface of the earth, they brought various metals with them. How the metals happened to be there ready to be brought up, no one knows. Some people think they were dissolved in water and then deposited; others think that electricity had something to do with their formation. However that may be, metals were brought up with the igneous rocks, and one of these metals is copper.
Now, to one who did not know how to work iron, copper was indeed a wonderful treasure, for it made very good knives and spoons. The people who lived in this country long before the Indians came understood how to use it, and after a while the Indians themselves found out its value. They did not trouble themselves to dig for it; they simply picked it up from the ground, good pure metal in lumps; and with stones for hammers they beat it into knives.
There was only one place in what is now the United States where they could do this, and that was in northern Michigan. A long point of land stretches out into Lake Superior as if it was trying to see what could be found there. Just beyond its reach is Isle Royal; and in these two places there was plenty of copper, enough for the Indians, enough for the people who have come after them, and enough for a great many more.
One piece of copper which the Indians did not pick up, and the United States Government did, is the famous Ontonagon Boulder, so called because it was found near the Ontonagon River. It weighs more than three tons. The Indians would have been glad to make use of it, but it was too hard for their tools, and so they are said to have wors.h.i.+ped it as a G.o.d. It is now in the National Museum in Was.h.i.+ngton.
The lumps of copper, such as those which delighted the hearts of the Indians, are known to-day as "barrel" copper, because they are of a good size to be dropped into barrels and carried away for smelting.
The great boulders which the Indians could not use are called "ma.s.s"
copper. Sometimes they weigh as much as five hundred tons. The copper in them is almost pure, and a big boulder is worth perhaps $200,000.
Nevertheless, the mine-owners do not rejoice when they come upon such a ma.s.s in their digging, for it cannot be either dug or blasted, and has to be cut away with chisels of chilled steel. Now, a mine may be wonderfully rich in metal, but if working it costs too much, then another mine with less metal but more easily worked will pay better.
So it is with these great ma.s.ses of copper. They are interesting to study and they look well in museums, but they do not pay so well as the "stamp" copper which is found in humble little bits in the gangue, or the rock of the vein, and has to be pounded in a stamp mill. This gangue is dug out and broken up as in mines of other metals. The copper is much heavier than the rock, so it is easy to get rid of the worthless gangue by means of a flow of water. The gangue of the Michigan mines is exceedingly hard, but the stamps are so powerful that one can crush five hundred tons in less than twenty-four hours.
Some copper can be taken out of the mortars at once, but the rest of the broken gangue is fed to jigs, or screens, which are kept under jets of water. The water is thrown up from below and the lighter rock is tossed away, while the heavier copper falls through the tiny holes in the screens.
[Ill.u.s.tration: IN A COPPER SMELTER
The men are pouring hot copper into moulds for castings.]
After the ore has been through all these experiences, it comes out looking like dark-colored sand or coa.r.s.e brown sugar. It is not interesting, and no one who saw it for the first time would ever fancy that it was going to turn into something beautiful. It is dumped into freight cars and trundled off to the smelting furnaces. But however uninteresting it looks, it is well worth while to follow these cars to see what happens to it at the smelters. First of all, even before it goes into the smelting furnace, it must be roasted. There is usually sulphur combined with the copper, and roasting will get rid of much of it. In some places this is done by building up a great heap of ore with a little wood. The wood is kindled, and by the time it has burned out, the sulphur in the ore has begun to burn, and in a good-sized heap it will continue to burn for perhaps two months.
Such a heap is a good thing to keep away from, for the fumes of sulphur are very disagreeable. Indeed, they will kill trees and other growing things wherever the wind may carry them, even several miles away. The managers of mines of copper as well as of gold and silver have learned to economize; and it has been found that instead of letting these fumes go into the air, they may be made to pa.s.s through acid chambers lined with zinc and full of water. The water holds the fumes, and can be used in making sulphuric acid.
After the ore has been roasted, it is put into the furnace for smelting. If you should make an oven and put into it a mixture of wood and roasted copper, that would be a smelting furnace. Set the wood on fire, pump in air to make the flame hot, and if your furnace could be made hot enough,--that is, 2300 F., or about eleven times as hot as boiling water,--you could smelt copper. Of course the furnace of a real smelting factory will hold tons and tons of copper ore and has all sorts of improvements, but after all it is in principle only an oven with wood and ore and draft. Another sort of furnace, which is better for some kinds of ore, has a grate for the fire and a bed above it for the copper.
Imagine an enormous furnace holding between two and three hundred tons of metal and burning with such a terrific heat that by contrast boiling water would seem cool and comfortable. Suddenly, while you stand looking at it, but a long way off, a door flies open and the most beautiful cascade--only it is not a waterfall, but a _copper_ fall--pours out. It looks like red, red gold, rich and wonderful, with little flames of red and blue dancing over it. It might almost be one of the fire-breathing dragons of the old story-books; and if it should get loose, it would devour whomever it touched far quicker than any dragon. It hardly seems as if any one could manage such a monster; but it looks easy, after you have seen it done. An enormous horizontal wheel revolves slowly. On its edge are moulds shaped like bricks, but much larger. On the hub of the wheel a workman sits to direct the filling of these. A set of them is filled, and moves on, and others take their place. When they are partly cooled, another workman, at the farther side of the wheel, pries them out of the mould and drops them into water. Then by the aid of the fingers of a machine and those of men, they are loaded upon cars.
In copper there is often some gold and silver. The precious metals do not make the copper any better, and if they can be separated from it, they are well worth the trouble. This is done by electricity. It is so successful that the metallurgists are hoping soon to take a long step ahead and by means of electricity to produce refined copper directly from the ore. Indeed, this has been done already in the laboratories, but before the managers of mines can employ the method, a way of making it less expensive must be discovered.
No mine that wastes anything is as well managed as it might be; and superintendents are constantly on the watch for cheaper methods and for ways to make the refuse matter of use. Even the scoria, or slag from the furnaces, has been found to be good for something, and now it is made into a coa.r.s.e sort of brick that for certain rough uses is of value. By the way, the shaft of a copper mine, the Red Jacket, has shown itself of use in a manner that no one expected, namely, it helps to prove that the earth turns around. This shaft is the deepest mining shaft in the world, and when you get into the cage, you go down a full mile toward the center of the earth. If you drop any article into the shaft, it always strikes the east side before reaching the bottom. The only way to explain this is that the earth turns toward the east.
Copper mixed with zinc forms bra.s.s, which is harder than copper alone.
It tarnishes, though not so easily as copper; but a coat of varnish will protect it till the varnish wears off. A good way to find out the many uses of bra.s.s and to see how valuable they are is to go along the street and through a house and make a list. On the street you will see signs, harness buckles, and b.u.t.tons, everywhere. Look on the automobiles and fire engines for a fine display of bra.s.s, polished and s.h.i.+ning. In the house you will find bra.s.s bedsteads, curtain rods, faucets, pipes, drawerpulls, candlesticks, gas and electric fixtures, lamps, the works of clocks and watches, and scores of other things.
You will not have any idea how many they are till you begin to count.
Copper mixed with tin forms bronze. Go into a hardware store and look at the samples of bronze outside of each drawer, and you will be surprised that there are so many. Bronze does not change even when in the open air for ages. That is one reason why it has always been so much used for statues. There are two strange facts about this mixture.
One is that bronze is harder than either copper or tin. The other is that if you mix one pint of melted copper with one pint of tin, the mixture will be less than a quart. Just why these things are so, no one is quite certain. Mathematics declares that the whole is equal to the sum of its parts; but in this one case the whole seems to be less than the sum of its parts.
Another reason why bronze is so much used for statues is that the castings are smooth. I once went to a foundry to have a bra.s.s ornament shaped somewhat like a cone made for a clock. The foundryman formed a mould in clay and poured the melted bra.s.s into it. When it had cooled, the mould was broken off and the ornament taken out; but it was of no use because it was so full of little hollows that it could not be made smooth without cutting away a great deal of it. The man had to try three times before he succeeded in making one that could be polished.
If it had been made of bronze, there would have been no trouble, because bronze, hard as it is after it cools, flows when it is melted almost as easily as mola.s.ses and fills every little nook and corner of the mould.
A famous Latin poet named Horace, who lived two thousand years ago, wrote of his poems, "I have reared a monument more lasting than bronze"; and he was right, for few statues have endured from his day to ours, but his poems are still read and admired.
Bells are made of bronze, about three quarters copper and one quarter tin. It is thought that much copper gives a deep, full tone, and that much tin with, sometimes, zinc makes the tone sharp. The age of a bell has something to do with its sound being rich and mellow; but the bellmaker has even more, for he must understand not only how to cast it, but also how to tune it. If you tap a large bell, it will, if properly tuned, sound a clear note. Tap it just on the curve of the top, and it will give a note exactly one octave above the first. If the note of the bell is too low, it can be made higher by cutting away a little from the inner rim. If it is too high, it can be made lower by filing on the inside a little above the rim. Many of the old bells contain the gifts of silver and gold which were thrown in by people who watched their founding. The most famous bell in the United States is the "Liberty Bell" of Independence Hall, in Philadelphia, which rang when Independence was adopted by Congress. This was founded in England long before the Revolution and later was melted and founded again in the United States.
It would not be easy to get on without bra.s.s and bronze; but even these alloys are not so necessary as copper by itself. It is so strong that it is used in boiler tubes of locomotives, as roofing for buildings and railroad coaches, in the great pans and vats of the sugar factories and refineries. A copper ore called "malachite," which shows many shades of green, beautifully blended and mingled, is used for the tops of tables. Wooden s.h.i.+ps are often "copper-bottomed"; that is, sheets of copper are nailed to that part of the hull which is under water in order to prevent barnacles from making their homes on it, and so lessening the speed of the vessel.
Diggers in the Earth Part 3
You're reading novel Diggers in the Earth Part 3 online at LightNovelFree.com. You can use the follow function to bookmark your favorite novel ( Only for registered users ). If you find any errors ( broken links, can't load photos, etc.. ), Please let us know so we can fix it as soon as possible. And when you start a conversation or debate about a certain topic with other people, please do not offend them just because you don't like their opinions.
Diggers in the Earth Part 3 summary
You're reading Diggers in the Earth Part 3. This novel has been translated by Updating. Author: Eva March Tappan already has 661 views.
It's great if you read and follow any novel on our website. We promise you that we'll bring you the latest, hottest novel everyday and FREE.
LightNovelFree.com is a most smartest website for reading novel online, it can automatic resize images to fit your pc screen, even on your mobile. Experience now by using your smartphone and access to LightNovelFree.com
- Related chapter:
- Diggers in the Earth Part 2
- Diggers in the Earth Part 4
RECENTLY UPDATED NOVEL

Global Game: AFK In The Zombie Apocalypse Game
Global Game: AFK In The Zombie Apocalypse Game Chapter 2700 Upgrade Completed View : 3,149,404
Nine Star Hegemon Body Arts
Nine Star Hegemon Body Arts Chapter 5670 Dragon Devours Golden Python View : 8,868,113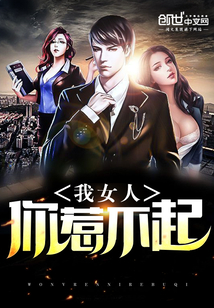
You Cannot Afford To Offend My Woman
You Cannot Afford To Offend My Woman Chapter 1261 (Showdown) View : 1,830,190
Reincarnated As a Fox With System
Reincarnated As a Fox With System Chapter 918: First Step of Escape Plan! View : 531,771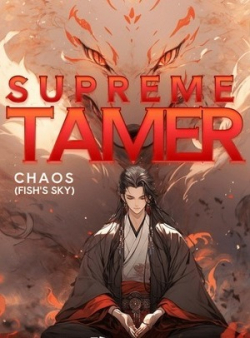
Supreme Tamer
Supreme Tamer Chapter 768: Chapter 638: 30,000 People, Must Be Silenced Completely View : 320,308