On Laboratory Arts Part 13
You’re reading novel On Laboratory Arts Part 13 online at LightNovelFree.com. Please use the follow button to get notification about the latest chapter next time when you visit LightNovelFree.com. Use F11 button to read novel in full-screen(PC only). Drop by anytime you want to read free – fast – latest novel. It’s great if you could leave a comment, share your opinion about the new chapters, new novel with others on the internet. We’ll do our best to bring you the finest, latest novel everyday. Enjoy!
-- 63. Centering.
When a lens is ground and polished it will almost always happen that the axis of revolution of its cylindrical edge is inclined to the axis of revolution of its curved surfaces. Since in practice lenses have to be adjusted by their edges, it is generally necessary to adjust the edge to a cylinder about the axis of figure of the active surfaces.
This is best done on a lathe with a hollow mandrel.. The lens is chucked on a chuck with a central aperture--generally by means of pitch or Regnault's mastic, or "centering" cement for small lenses--and a cross wire is fixed in the axis of revolution of the lathe, and is illuminated by a lamp. This cross wire is observed by an eye-piece (with cross wires only in the case of a convex lens, or a telescope similarly furnished in the case of a concave lens), also placed in the axis of rotation of the lathe.
Both cross wires are thus in the axis of revolution of the mandrel, and the distant one (B in the figure) is viewed through the lens and referred to the fixed cross wires at A. In general, as the lathe is rotated by turning the mandrel the image of the illuminated cross wires will be observed to rotate also. The lens is adjusted until the image remains steady on rotating the mandrel and it is to give time for this operation that a slow-setting cement is recommended. When the image remains stationary we know that the optical centre of the lens is in the axis of revolution, and that this axis is normal to both lens surfaces, i.e. is the princ.i.p.al axis of the lens, or axis of figure.
Fig. 54.
A much readier method, and one, in general, good enough for most purposes, is to put a candle on the end of the lathe-bed where the back centre generally is, and observe the images of the flame by reflection from both the lens surfaces. This method is very handy with small lenses; the mandrel is turned, and the lens adjusted by hand till the images are immovable. In both cases, of course, the edge of the lens is turned or ground till it is truly circular, the position of the lens remaining undisturbed on the chuck. If the edge gauge has been properly used in the earlier stages of figuring, it will be found that very little turning or grinding is requisite to produce a true centering.
The particular defect due to want of centering in a lens may be observed by using it as the objective of a telescope, and observing a star slightly out of focus. The interference fringes will not be concentric circles unless the lens is properly centred. I ought to say that I have not looked into the theory of this, but have merely taken it as a generally admitted fact. The diseases of lenses and the modes of treating them are dealt with in a book by Messrs. Cook of York, ent.i.tled On the Adjustment and Testing of Telescopic Objectives.
The final process of figuring will be dealt with later on (-- -- 66 and 67), as it applies not only to lenses but to mirrors, prisms, etc. If the instructions given have been carefully carried out on a 2-inch lens, it should perform fairly well, and possibly perfectly, without any further adjustment of the gla.s.s.
-- 64. Preparation of Small Lenses, where great Accuracy is not of the first Importance.
Such lenses may generally be made out of bits of good plate or sheet gla.s.s, and are of constant use in the physical laboratory. They may be purchased so cheaply, however, that only those who have the misfortune to work in out-of-the-way places need be driven to make them.
Suitable gla.s.s having been obtained and the curves calculated from the index of refraction, as obtained by any of the ordinary methods applicable to plates (the microscope method, in general, is quite good enough), squares circ.u.mscribing the desired circles are cut out by the help of a diamond. [Footnote: Glazebrook and Shaw's Practical Physics, p. 383 (4th ed.).] The squares are roughly snipped by means of a pair of pliers or spectacle-maker's shanks. The rough circles are then mounted on the end of a bra.s.s or iron rod of rather greater diameter than the finished lenses are to possess. This mounting is best done by centering cement.
The discs are then dressed circular on a grindstone, the rod serving both as a gauge and handle. A sufficient number of these discs having been prepared, a pair of bra.s.s tools of the form shown in the sketch (Fig. 55), and of about the proper radius of curvature, are made.
One of these tools is used as a support for the gla.s.s discs.
Fig. 55.
A compa.s.s being set to scribe circles of the same diameter as the gla.s.s discs, centre marks are made on the surface of the appropriate tool, circles are drawn on this, and facets are filed or milled (for which the spiral head of the milling machine is excellent). In the case of concave supporting surfaces, i.e. in making concave lenses, I apprehend filing would be difficult, and the facets would have to be made by a rose cutter or mill; but if the discs are fairly round, then, in fact, no facets are required.
The facets being ready, the gla.s.s discs are cemented to them by centering cement, which may be used quite generally for small lenses.
When the cutting of facets has been omitted on a concave surface, the best cement is hard pitch. The grinding tool is generally rather larger than the nest of lenses. Coa.r.s.e and fine grinding is accomplished wholly on the lathe--the tool being rotated at a fair speed (see infra), and the nest of lenses moved about by its handle so as to grind all parts equally. It must, of course, be held anywhere except "dead on," for then the part round the axis would not get ground; this inoperative portion of the rotating tool must therefore be allowed to distribute its incapable efforts evenly over the nest of lenses.
Polis.h.i.+ng is accomplished by means of the grinding tool, coated with paper and rouge as before; or the tool may be coated with very thin cloth and used with rouge as before--in this case the polis.h.i.+ng goes on fastest when the surface of the cloth is distinctly damp. In working by this method, each grade of emery need only be applied from five to ten minutes. The gla.s.s does not appear to get scratched when the emery is changed, provided everything is well washed. A good polish may be got in an hour. The lathe is run as for turning bra.s.s of the same diameter as the tool.
One side of the lenses being thus prepared, they are reversed, and the process gone through for the other side in a precisely similar manner.
[Footnote: Unless the radius of curvature is very short and the lenses also convex, there is no necessity to recess the facets, provided hard pitch is used as the cement. See note on hard pitch.] To save trouble, it is usual, to make such lenses of equal curvature on both faces; but of course this is a matter of taste.
Fig. 56.
For very common work, bits of good plate gla.s.s are employed, and the manufacturer's surface treated as flat (Fig. 56). In this way plano-convex lenses are easily and cheaply made. Finally the lenses have to be centred, an essential operation in this case. This is easily done by the reflection method--the edge being turned off by the file and kerosene and the centering cement being used in making the preliminary adjustment on the chuck. I presume a lens made in this way is worth about a s.h.i.+lling, so that laboratory manufacture is not very remunerative. Fig. 56 shows the method of mounting small lenses for lathe grinding, when only one lens is required. The tool is generally rotated in the lathe and the lens held against it.
-- 65. Preparing Small Mirrors for Galvanometers.
To get good mirrors for galvanometers, I have found the best plan is to grind and polish a large number together, on a disc perhaps 8 or 10 inches in diameter. I was led to this after inspecting and rejecting four ounces of microscope cover slips, a most wearisome process. That regular cover slips should be few and far between is not unlikely, seeing that they are made (by one eminent firm at least) simply by "pot" blowing a huge thin bulb, and then smas.h.i.+ng it on the floor and selecting the fragments. As in the case of large mirrors, it is of course only necessary to grind one side of the gla.s.s, theoretically at all events. The objections to this course are:
(1) A silver surface cannot, in my experience, be polished externally (on a minute object like a cover slip) to be anything like so bright as the silver surface next the gla.s.s; and,
(2) if one side only is ground, it will be found that the little mirror hopelessly loses its figure directly it is detached from the support on which it has been worked. Consequently, I recommend that these small mirrors should be ground and polished on both sides--enough may be made at one operation to last for a very long time.
A slate back is prepared of the same radius of curvature as it is desired to impart to the mirrors. Bits of thin sheet gla.s.s are then ground circular as described in the last section and cemented to this surface by the smallest quant.i.ty of clean archangel pitch, allowed to cool slowly and even to rest for a day before the work is proceeded with. The whole surface is then ground and polished as before.
The mirrors are now reversed, when they ought to nearly fit the tool (a.s.suming that flats are being made, and the fellow tool in all other cases), and are recemented by pitch to the appropriate backing ground, and polished. If very excellent results are required, these processes may be preceded by a preliminary rough grinding of one surface, so that the little discs will "sit" exactly on the tool surface, and not run the risk of being strained by capillary forces in the pitch. We have always found this necessary for really good results.
On removing such mirrors from the backing, they generally, more or less lose their figure, becoming (in general fairly uniformly) more concave or convex. About 5 per cent of the mirrors thus prepared will be found almost perfect if the work has been well done, and the rest will probably be very fair, unless the diameter is very large as compared with the thickness. The best way of grinding and polis.h.i.+ng such large surfaces (nests 10 inches in diameter) is on a grinding machine, such as will be described below. The polis.h.i.+ng is best done by means of paper, as before described.
Having occasion to require hitherto unapproached lightness and optical accuracy in such mirrors, I got my a.s.sistant to try making them of fused quartz, slices being cut by a diamond wheel from a rod of that material. Chips of natural quartz were also obtained from broken "pebble" spectacles, and these were worked at the same time. The resulting mirrors were certainly superior to the best we could make from gla.s.s, but the labour of grinding was greater, and the labour of polis.h.i.+ng less, than in the latter case. The pebble fragments gave practically as good mirrors as the fused slices. For the future it will be better always to make galvanometer mirrors from quartz crystals. These may be easily sliced, as will be described in -- 74.
The slices are dressed on a grindstone according to instructions already given for small lenses.
The silvering of these mirrors is a point of great importance. After trying nearly every formula published, we have settled down to the following.
A solution of pure crystallised nitrate of silver in distilled water is made up to a strength of 125 grams of the salt per litre. This forms the stock solution and is kept in a dark bottle.
Let the volume of silvering liquor required in any operation be denoted by 4 v. The liquor is prepared as follows:
I. Measure out a volume v of the stock solution of silver nitrate, and calculate the weight of salt which it contains; let this be w.
In another vessel dissolve pure Roch.e.l.le salt to the amount of 2.6 w, and make up the solution to the volume v. These two solutions are to be mixed together at a temperature of 55 C, the vessels with their contents being heated to this temperature on the water bath. After mixing the liquids the temperature is to be kept approximately constant for five minutes, after which the liquor may be cooled. The white precipitate which first forms will become gray or black and very dense as the liquid cools. If it does not, the liquor must be reheated to 55 C, and kept at that temperature for a few minutes and then again allowed to cool. The solution is in good order when all the precipitate is dense and gray or black and the liquor clear. The blacker and denser the precipitate the better is the solution. The liquor is decanted and filtered from the precipitate and brought up to the volume 2 v by addition of some of the wash water.
II. Measure out a volume 0.118 v of the stock solution into a separate vessel, and add to it a 5 per cent solution of ammonium hydrate, with proper precautions, so that the precipitate at first formed is all but redissolved after vigorous shaking. It is very important that this condition should be exactly attained. Therefore add the latter part of the ammonia very carefully. Make up the volume to 2 v.
Mix the solutions I. and II. in a separate vessel and pour the mixture into the depositing vessel. The surface to be silvered should face downwards, and lie just beneath the free surface of the liquid.
Bubbles must of course be removed.
The silver deposit obtained in this manner is exceedingly white and, bright on the surface next to the gla.s.s, but the back is mat and requires polis.h.i.+ng.
The detail of the process described above was worked out in my laboratory by Mr. A. Pollock, to whom my thanks are due.
This process gives good deposits when the solutions are freshly prepared, but the ammonia solution will not keep; The surfaces to be silvered require to be absolutely clean. The process is a.s.sisted by a summer temperature, say 70 Fahr, and possibly by the action of light. Six or seven hours at least are required for a good deposit; a good plan is to leave the mirrors in the bath all night. On removal from the bath the mirrors require to be well washed, and allowed to dry thoroughly in sun heat for several hours before they are touched.
Care should be taken not to pull the mirrors out of shape when they are mounted for the bath. A single drop of varnish or paint (a mere speck) on the centre will suffice to hold them. The back of the deposit requires to be varnished or painted as a rule to preserve the silver. All paints and varnishes thus applied tend to spoil the figure by expanding or contracting. On the whole, I think boiled linseed oil and white or red lead--white or red paint in fact--is less deleterious than other things I have tried. Sh.e.l.lac varnish is the worst.
Of course, the best mirror can be easily spoiled by bad mounting. I have tried a great number of methods and can recommend as fairly successful the following:- A little pure white lead, i.e. bought as pure as a chemical--not as a paint--is mixed with an equal quant.i.ty of red lead and made into a paste with a little linseed oil. I say a paste, not putty. A trace of this is then worked on to the back of the mirror at the centre as nearly as may be, and to this is attached the support. The only objection to this is that nearly a week is required for the paste to set. If people must use sh.e.l.lac let it be remembered that it will go on changing its shape for months after it has cooled (whether it has been dissolved in alcohol or not).
-- 66. Preparation of Large Mirrors or Lenses for Telescopes.
So much has been written on this subject by astronomers, generally in the English Mechanic and in the Philosophical Transactions for 1840, that it might be thought nothing could be added. I will only say here that the processes already described apply perfectly to this case; but of course I only refer to silver on gla.s.s mirrors. For any size over 6 inches in diameter, the process of grinding and polis.h.i.+ng by hand, particularly the latter, will probably be found to involve too much labour, and a machine will be required. A description of a modification of Mr. Nasmyth's machine--as made by my a.s.sistant, Mr.
Cook--will be found below.
There is no difficulty in constructing or working such a machine, and considered as an all round appliance, it possesses solid advantages over the simple double pulley and crank arrangement, which, however, from its simplicity deserves a note. Two pulleys, A and B, of about 18 inches diameter by 4 inches on the face, are arranged to rotate about vertical axes, and belted together. The shaft of one of these pulleys is driven by a belt in any convenient manner. Each pulley is provided on its upper surface with a crank of adjustable length carrying a vertical crank-pin.
Each crank-pin pa.s.ses through a 3"X 2" wooden rod, say 3' 6" long, and these rods are pinned together at their farther extremities, and this pin carries the grinding or polis.h.i.+ng tool, or rather engages loosely with the back of this tool which lies below the rod. It is clear that if the pulleys are of commensurable diameters, and are rigidly connected--say by belting which neither stretches nor slips--the polis.h.i.+ng tool will describe a closed curve. If, however, the belt is arranged to slip slightly, or if the pulleys are of incommensurable diameters, the curve traced out by the grinding tool will be very complex, and in the case of the ratio of the diameters being incommensurable, will always remain open; for polis.h.i.+ng purposes the consummation to be wished.
Mirror surfaces are ground spherical, the reduction to parabolic form being attained in the process of polis.h.i.+ng. A very interesting account of the practice of dealing with very large lenses will be found in Nature, May 1886, or the Journal of the Society of Arts, same date (I presume), by Sir Howard Grubb. The author considers that the final adjustment of surfaces by "figuring"--of which more anon--is an art which cannot be learned by inspection, any more than a man could learn to paint by watching an artist. This is, no doubt, the case to some extent; still, a person wis.h.i.+ng to learn how to figure a lens could not do better than take Sir Howard at his word, and spend a month at his works. Meanwhile the following remarks must suffice; it is not likely that anybody to whom these notes will be of service would embark on such large work as is contemplated by Sir Howard Grubb.
Fig. 57.
Description of Polis.h.i.+ng Machine. Power is applied through belting to the speed cone A. By means of a bevel pinion rotation is communicated to the wheel D, which is of solid metal and carries a T-slot, C. A pedestal forming a crank-pin can be clamped so as to have any desired radius of motion by the screw E. A train of wheels E F G H K (ordinary cast lathe change wheels) communicate any desired ratio of motion to the tool-holder, which simply consists of two pins projecting vertically downwards from the spokes of wheel K.
These pins form a fork, and each p.r.o.ng engages in a corresponding hole in the back of the slate-grinding tool (not shown in figure). The connection with the tool is purposely loose. The wheel E, of course, cannot rotate about the crank-pin D. Provision for changing the ratio of tool rotation is achieved by mounting the wheels composing the train on pins capable of sliding along a long slot in the bar supporting them. The farther end of this bar is caused to oscillate to and fro very slowly by means of an additional crank-pin S and crank-shaft, the projecting face of the bed-plate W being placed so as to allow V to slide about easily and smoothly.
Motion is communicated to this part of the system by means of gears at 0 and P, and a belt working from P to Q.
Thus the vertical shaft R is set in motion and communicates by gears with S. A pulley placed on the axle of the wheel carrying the crank-pin S gives a slow rotation to the work which is mounted on the table M. A small but important feature is the tray L below the gear K. This prevents dirt falling from the teeth of the wheel on to the work. The motion of S is of course very much less than of B--say 100 times less. The work can be conveniently adjusted as to height by means of the screw N.
On Laboratory Arts Part 13
You're reading novel On Laboratory Arts Part 13 online at LightNovelFree.com. You can use the follow function to bookmark your favorite novel ( Only for registered users ). If you find any errors ( broken links, can't load photos, etc.. ), Please let us know so we can fix it as soon as possible. And when you start a conversation or debate about a certain topic with other people, please do not offend them just because you don't like their opinions.
On Laboratory Arts Part 13 summary
You're reading On Laboratory Arts Part 13. This novel has been translated by Updating. Author: Richard Threlfall already has 550 views.
It's great if you read and follow any novel on our website. We promise you that we'll bring you the latest, hottest novel everyday and FREE.
LightNovelFree.com is a most smartest website for reading novel online, it can automatic resize images to fit your pc screen, even on your mobile. Experience now by using your smartphone and access to LightNovelFree.com
- Related chapter:
- On Laboratory Arts Part 12
- On Laboratory Arts Part 14
RECENTLY UPDATED NOVEL

Heaven Extinction Martial Emperor
Heaven Extinction Martial Emperor Chapter 1123: To whom will the deer die (1) View : 370,669
Following a Hundred Years of Cultivation, I'm dying Before I Got Cheats
Following a Hundred Years of Cultivation, I'm dying Before I Got Cheats Chapter 1154: Successful Pill Refinement, Beginning Seclusion (Part 1) View : 452,294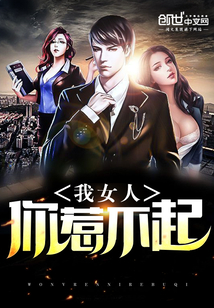
You Cannot Afford To Offend My Woman
You Cannot Afford To Offend My Woman Chapter 1262 (This Deity Has Long Seen Through Everything) View : 1,831,017
I Have A City In An Alternate World
I Have A City In An Alternate World Chapter 4022: The might of the human race! 1! View : 1,313,216
The King of Hell's Genius Pampered Wife
The King of Hell's Genius Pampered Wife Chapter 1933: I Surrender View : 2,739,193
Beauty and the Bodyguard
Beauty and the Bodyguard Chapter 11376: Chapter 11374: The Battle of the Three Kingdoms! View : 5,563,590