The Jute Industry: From Seed to Finished Cloth Part 4
You’re reading novel The Jute Industry: From Seed to Finished Cloth Part 4 online at LightNovelFree.com. Please use the follow button to get notification about the latest chapter next time when you visit LightNovelFree.com. Use F11 button to read novel in full-screen(PC only). Drop by anytime you want to read free – fast – latest novel. It’s great if you could leave a comment, share your opinion about the new chapters, new novel with others on the internet. We’ll do our best to bring you the finest, latest novel everyday. Enjoy!
CHAPTER IX. THE ROVING FRAME
The process of doubling ends with the last drawing frame, but there still remains a process by means of which the drafting of the slivers and the parallelization of the fibres are continued. And, in addition to these important functions, two other equally important operations are conducted simultaneously, viz., that of imparting to the drawn out sliver a slight twist to form what is known as a "rove" or roving, and that of winding the rove on to a large rove bobbin ready for the actual spinning frame.
The machine in which this multiple process is performed is termed a "roving frame." Such machines are made in various sizes, and with different types of faller mechanism, but each machine is provided for the manipulation of two rows of bobbins, and, of course, with two rows of spindles and flyers. These two rows of spindles, flyers, and rove bobbin supports are shown clearly in Fig. 18, which represents a spiral roving frame made by Messrs. Douglas Fraser & Sons, Ltd., Arbroath.
Each circular bobbin support is provided with pins rising from the upper face of the disc, and these pins serve to enter holes in the f.l.a.n.g.e of the bobbin and thus to drive the bobbin. The discs or bobbin supports are situated in holes in the "lifter rail" or "builder rail" or simply the "builder"; the vertical spindles pa.s.s through the centre of the discs, each spindle being provided with a "flyer," and finally a number of plates rest upon the tops of the spindles.
[Ill.u.s.tration: FIG. 18 ROVING FRAME _By Permission of Messrs.
Douglas Fraser & Sons, Ltd_.]
A roving machine at work is shown in Fig. 19, and it will be seen that the twisted sliver or rove on emerging from the drawing rollers pa.s.ses obliquely to the top of the spindle, through a guide eye, then between the channel-shaped bend at the upper part of the flyer, round the flyer arm, through an eye at the extreme end of either of the flyer arms, and finally on to the bobbin. Each bobbin has its own sliver can (occasionally two), and the sliver pa.s.ses from this can between the sides of the sliver guide, between the retaining rollers, then amongst the gill pins of the fallers and between the drawing (also the delivery) rollers. Here the sliver terminates because the rotary action of the flyer imparts a little twist and causes the material to a.s.sume a somewhat circular sectional form.
From this point, the path followed to the bobbin is that described above.
As in all the preceding machines, the delivery speed of the sliver is constant and is represented by the surface speed of the periphery of the delivery rollers, this speed approximates to about 20 yards per minute. The spindles and their flyers are also driven at a constant speed, because in all cases we have--
spindle speed = delivery x twist.
There is thus a constant length of yarn to be wound on the rove bobbin per minute, and the speed of the bobbin, which is driven independently of the spindle and flyer, is constant for any one series of rove coils on the bobbin. The speed of the bobbin differs, however, for each complete layer of rove, simply because the effective diameter of the material on the bobbin changes with the beginning of each new layer.
The eyes of the flyers always rotate in the same horizontal plane, and hence the rove always pa.s.ses to the bobbins at the same height from any fixed point. The bobbins, however, are raised gradually by the builder during the formation of each layer from the top of the bobbin to the bottom, and lowered gradually by the builder during the formation of each layer from bottom to top. In other words, the travel of the builder is represented by the distance between the inner faces of the f.l.a.n.g.es of the rove bobbin.
[Ill.u.s.tration: FIG. 19 ROVING FRAME FAIRBAIRN'S ROVING FRAME IN WORK]
Since every complete layer of rove is wound on the bobbin in virtue of the joint action of the spindle and flyer, the rotating bobbin, and the builder, each complete traverse of the latter increases the combined diameter of the rove and bobbin shaft by two diameters of the rove. It is therefore necessary to impart an intermittent and variable speed to the bobbin. The mechanism by means of which this desirable and necessary speed is given to the bobbin const.i.tutes one of the most elegant groups of mechanical parts which obtains in textile machinery. Some idea of the intricacy of the mechanism, as well as its value and importance to the industry, may be gathered from the fact that a considerable number of textile and mechanical experts struggled with the problem for years; indeed 50 years elapsed before an efficient and suitable group of mechanical parts was evolved for performing the function.
The above group of mechanical parts is known as "the differential motion," and the difficulties in constructing its suitable gearing arose from the fact that the speed of the rove pa.s.sing on to the various diameters must be maintained throughout, and must coincide with the delivery of yarn from the rollers, so that the attenuated but slightly twisted sliver can be wound on to the bobbin without strain or stretch. The varying motion is regulated and obtained by a drive, either from friction plates or from cones, and the whole gear is interesting, instructive--and sometimes bewildering--two distinct motions, a constant one and a variable one, are conveyed to the bobbins from the driving shaft of the machine.
The machine ill.u.s.trated in Fig. 18 is of special design, and the whole train of gear, with the exception of a small train of wheels to the retaining roller, is placed at the pulley end--that nearest the observer. The gear wheels are, as shown, efficiently guarded, and provision is made to start or stop the machine from any position on both sides. The machine is adapted for building 10 in. X 5 in.
bobbins, i.e. 10 in. between the f.l.a.n.g.es and 5 in. outside diameter, and provided with either 56 or 64 spindles, the ill.u.s.tration showing part of a machine and approximately 48 spindles.
The machines for rove (roving frames) are designated by the size of the bobbin upon which the rove is wound, e.g. 10 in. x 5 in. frame, and so on; this means that the f.l.a.n.g.es of the bobbin are 10 in.
apart and 5 in. in diameter, and hence the traverse of the builder would be 10 in. The 10 in. x 5 in. bobbin is the standard size for the ordinary run of yarns, but 9 in. x 4-1/2 in. bobbins are used for the roves from which finer yarns are spun. When the finished yarn appears in the form of rove (often termed spinning direct), as is the case for heavier sizes or thick yarns, 8 in. x 4 in. bobbins are largely used.
Provision is made on each roving frame for changing the size of rove so as to accommodate it for the subsequent process of spinning and according to the count of the required yarn; the parts involved in these changes are those which affect the draft gearing, the twist gearing, and the builder gearing in conjunction with the automatic index wheel which acts on the whole of the regulating motion.
CHAPTER X. SPINNING
The final machine used in the conversion of rove to the size of yarn required is termed the spinning frame. The actual process of spinning is performed in this machine, and, although the whole routine of the conversion of fibre into yarn often goes under the name of spinning, it is obvious that a considerable number of processes are involved, and an immense amount of work has to be done before the actual process of spinning is attempted. The nomenclature is due to custom dating back to prehistoric times when the conversion of fibre to yarn was conducted by much simpler apparatus than it is at present; the established name to denote this conversion of fibre to yarn now refers only to one of a large number of important processes, each one of which is as important and necessary as the actual operation of spinning.
A photographical reproduction of a large spinning flat in one of the Indian jute mills appears in Fig. 20, showing particularly the wide "pa.s.s" between two long rows of spinning frames, and the method adopted of driving all the frames from a long line shaft. Spinning frames are usually double-sided, and each side may contain any practicable number of spindles; 64 to 80 spindles per side are common numbers.
[Ill.u.s.tration: FIG 20. AN INDIAN SPINNING FLAT]
The rove bobbins, several of which are clearly seen in Fig. 20, are brought from the roving frame and placed on the iron pegs of a creel (often called a hake) near the top of the spinning frame-actually above all moving parts of the machine. Each rove bobbin is free to rotate on its own peg as the rove from it is drawn downwards by the retaining rollers. The final drafting of the material takes place in this frame, and a considerable amount of twist is imparted to the drawn out material; the latter, now in the desired form and size of yarn, is wound simultaneously on to a suitable size and form of spinning bobbin.
When the rove emerges from the retaining rollers it is pa.s.sed over a "breast-plate," and then is entered into the wide part of the conductor; it then leaves by the narrow part of the conductor by means of which part the rove is guided to the nip of the drawing rollers, The rove is, of course, drafted or drawn out between the retaining and drawing rollers according to the draft required, and the fibrous material, now in thread size is placed in a slot of the "thread-plate," then round the top of the flyer, round one of the arms of the flyer, through the eye or palm at the end of the flyer arm and on to the spinning bobbin. The latter is raised and lowered as in the roving frame by a builder motion, so that the yarn may be distributed over the full range between the ends or f.l.a.n.g.es.
Each spindle is driven separately by means of a tape or band which pa.s.ses partially round the driving cylinder and the driven whorl of the spindle, and a constant relation obtains between the delivery of the yarn and the speed of the spindle during the operation of spinning any fixed count or type of yarn. In this connection, the parts resemble those in the roving frame, but from this point the functions of the two frames differ. The yarn has certainly to be wound upon the bobbin and at the same rate as it is delivered from the drawing or delivery rollers, but in the spinning frame the bobbin, which rotates on the spindle, is not driven positively, as in the roving frame, by wheel gearing; each spinning bobbin is actually driven by the yarn being pulled round by the arm of the flyer and just sufficient resistance is offered by the pressure or tension of the "temper band" and weight. The temper band is simply a piece of leather or hemp twine to which is attached a weight, and the other end of the leather or twine is attached to the builder rail.
[Ill.u.s.tration: FIG. 21 A LINE OF SPINNING FRAMES]
The front part of the builder rail is provided with grooves into one of which the temper-band is placed so that the band itself is in contact with a groove near the base of the bobbin f.l.a.n.g.e. A varying amount of resistance or tension on the bobbin is required in virtue of the varying size of the partially-filled bobbin, and this is obtained by placing the temper-band successively in different groves in the builder so that it will embrace a gradually increasing arc of the spinning bobbin, and thus impart a heavier drag or tension.
The spinning frames in Fig. 20 are arranged with the ends of the frame parallel to the pa.s.s, whereas the end frames in Fig. 21 are at right angles to the pa.s.s, and hence an excellent view of the chief parts is presented. The full rove bobbins are seen distinctly on the pegs of the creel in the upper part of the figure, and the rove yarns from these bobbins pa.s.s downwards, as already described, until they ultimately enter the eyes of the flyer arms to be directed to and wound upon the spinning bobbins. The flyers--at one time termed throstles--are clearly visible a little above the row of temper weights. The chief parts for raising the builder--cam lever, adjustable rod, chain and wheel--are ill.u.s.trated at the end of the frame nearest the observer.
CHAPTER XI. TWISTING AND REELING
In regard to cloth manufacture, most yarns are utilized in the form they leave the spinning frame, that is, as single yarns. On the other hand, for certain branches of the trade, weaving included, it is necessary to take two, three, or more of these single yarns and to combine them by a process technically termed twisting, and sometimes "doubling" when two single yarns only are combined.
Although the commonest method, so far as weaving requirements go, is to twist two single yarns together to make a compound yarn, it is not uncommon to combine a much higher number, indeed, sixteen or more single yarns are often united for special purposes, but, when this number is exceeded, the operation comes under the heading of twines, ropes and the like. The twist or twine thus formed will have the number of yarns regulated by the levelness and strength required for the finished product. The same operation is conducted in the making of strands for cordage, but when a number of these twines are laid-up or twisted together, the name cord or rope is used to distinguish them.[1]
[Footnote 1: See _Cordage and Cordage Hemp and Fibres_, by T.
Woodhouse and P. Kilgour.]
When two or three threads are united by twisting, the operation can be conducted in a twisting frame which differs little from a ordinary spinning frame, and hence need not be described. There may be, however, appliances embodying some system of automatic stop motion to bring the individual spindles to rest if one thread out of any group which are being combined happens to break. When several threads have to be twisted together, special types of twisting frames are employed; these special machines are termed "tube twisters,"
and the individual threads pa.s.s through holes suitably placed in a plate or disc before they reach the tube.
More or less elaborate methods of combining yarns are occasionally adopted, but the reader is advised to consult the above-mentioned work on Cordage and similar literature for detailed information.
When the yarn leaves the spinning frame, or the twisting frame, it is made up according to requirements, and the general operations which follow spinning and twisting are,--reeling, cop-winding, roll or spool winding, mill warping or link warping. The type or cla.s.s of yarn, the purpose for which the yarn is to be used, or the equipment of the manufacturer, determines which of these methods should be used previous to despatching the yarn.
_Reeling_. Reeling is a comparatively simple operation, consisting solely of winding the yarns from the spinning or twisting bobbins on to a wide swift or reel of a suitable width and of a fixed diameter, or rather circ.u.mference. Indeed, the circ.u.mference of the reel was fixed by an Act of Convention of Estates, dating as far back as 1665 and as under:
"That no linen yarn be exported under the pain of confiscation, half to the King and half to the attacher."
"That linen yarn be sold by weight and that no reel be shorter than _ten quarters_."
The same size of reel has been adopted for all jute yarns. All such yarns which are to be dyed, bleached, or otherwise treated must be reeled in order that the liquor may easily penetrate the threads which are obviously in a loose state. There are systems of dyeing and bleaching yarns in cop, roll or beam form, but these are not employed much in the jute industry. Large quant.i.ties of jute yarns intended for export are reeled, partly because bundles form suitable bales for transport, and partly because of the varied operations and sizes of apparatus which obtain in foreign countries.
YARN TABLE FOR JUTE YARNS
90 inches, or 2-1/2 yards = 1 thread, or the circ.u.mference of the reel 120 threads or 300 yards = 1 cut (or lea) 2 cuts or 600 yards = 1 heer 12 cuts or 3,600 yards = 1 standard hank 48 cuts or 14,400 yards = 1 spyndle
Since jute yarns are comparatively thick, it is only the very finest yarns which contain 12 cuts per hank. The bulk of the yarn is made up into 6-cut hanks. If the yarn should be extra thick, even 6 cuts are too many to be combined, and one finds groups of 4 cuts, 3 cuts, 2 cuts, and even 1 cut. A convenient name for any group less than 12 cuts is a "mill-hank," because the number used is simply one of convenience to enable the mill-hank to be satisfactorily placed on the swift in the winding frame.
The reeling operation is useful in that it enables one to measure the length of the yarn; indeed, the operation of reeling, or forming the yarn into cuts and hanks, has always been used as the method of designating the count, grist or number of the yarn. We have already seen that the count of jute yarn is determined by the weight in lbs.
of one spyndle (14,400 yds.).
For 8 lb. per spyndle yarn, and for other yarns of about the same count, it is usual to have provision for 24 spinning bobbins on the reel. As the reel rotates, the yarn from these 24 bobbins is wound round, say,
The Jute Industry: From Seed to Finished Cloth Part 4
You're reading novel The Jute Industry: From Seed to Finished Cloth Part 4 online at LightNovelFree.com. You can use the follow function to bookmark your favorite novel ( Only for registered users ). If you find any errors ( broken links, can't load photos, etc.. ), Please let us know so we can fix it as soon as possible. And when you start a conversation or debate about a certain topic with other people, please do not offend them just because you don't like their opinions.
The Jute Industry: From Seed to Finished Cloth Part 4 summary
You're reading The Jute Industry: From Seed to Finished Cloth Part 4. This novel has been translated by Updating. Author: Kilgour and Woodhouse already has 658 views.
It's great if you read and follow any novel on our website. We promise you that we'll bring you the latest, hottest novel everyday and FREE.
LightNovelFree.com is a most smartest website for reading novel online, it can automatic resize images to fit your pc screen, even on your mobile. Experience now by using your smartphone and access to LightNovelFree.com
- Related chapter:
- The Jute Industry: From Seed to Finished Cloth Part 3
- The Jute Industry: From Seed to Finished Cloth Part 5
RECENTLY UPDATED NOVEL

The Death Mage Who Doesn't Want a Fourth Time
The Death Mage Who Doesn't Want a Fourth Time Chapter 376: The future of the now-enclosed Sauron Duchy View : 322,104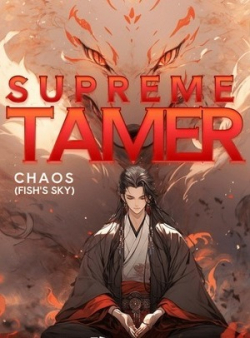
Supreme Tamer
Supreme Tamer Chapter 704: Chapter 573: Xia Guanghan, Unable to Escape Death View : 288,969
Super Insane Doctor of the Goddess
Super Insane Doctor of the Goddess Chapter 1036: Are You Qualified? Are You Worthy? View : 312,032
Best Delinquent Wife's Order: Rise Again, Hubby
Best Delinquent Wife's Order: Rise Again, Hubby Chapter 1054: Riding the Wind and Asking the Moon (139) View : 311,493