The Working of Steel Part 19
You’re reading novel The Working of Steel Part 19 online at LightNovelFree.com. Please use the follow button to get notification about the latest chapter next time when you visit LightNovelFree.com. Use F11 button to read novel in full-screen(PC only). Drop by anytime you want to read free – fast – latest novel. It’s great if you could leave a comment, share your opinion about the new chapters, new novel with others on the internet. We’ll do our best to bring you the finest, latest novel everyday. Enjoy!
[Ill.u.s.tration: FIG. 75.--Peg withdrawn after cooling to 760C. The increased amount of free ferrite arranges itself about the crystals as envelopes.]
[Ill.u.s.tration: FIG. 76.-Peg withdrawn after cooling to 740C.]
[Ill.u.s.tration: FIG. 77.--Peg withdrawn after cooling to 670C.
(magnified 800 diameters). Just at this moment the lamination of pearlite, which now occupied its original area, was taking place.
In some parts the lamination was perfect, in other parts the iron and iron-carbide were still dissolved in each other.]
[Ill.u.s.tration: FIG. 78.--Any peg withdrawn after 670C. on cooling (magnified 100 diameters).]
[Ill.u.s.tration: FIG. 79.--Structure of overheated steel before (left) and after refining (right).]
CHAPTER IX
HARDENING CARBON STEEL FOR TOOLS
For years the toolmaker had full sway in regard to make of steel wanted for shop tools, he generally made his own designs, hardened, tempered, ground and usually set up the machine where it was to be used and tested it.
Most of us remember the toolmaker during the sewing machine period when interchangeable tools were beginning to find their way; rather cautiously at first. The bicycle era was the real beginning of tool making from a manufacturing standpoint, when interchangeable tools for rapid production were called for and toolmakers were in great demand. Even then, jigs, and fixtures were of the toolmaker's own design, who practically built every part of it from start to finish.
The old way, however, had to be changed. Instead of the toolmaker starting his work from cutting off the stock in the old hack saw, a place for cutting off stock was provided. If, for instance, a forming tool was wanted, the toolmaker was given the master tool to make while an apprentice roughed out the cutter. The toolmaker, however, reserved the hardening process for himself. That was one of the particular operations that the old toolmaker refused to give up. It seemed preposterous to think for a minute that any one else could possibly do that particular job without spoiling the tools, or at least warp it out of shape (most of us did not grind holes in cutters 15 to 20 years ago); or a hundred or more things might happen unless the toolmaker did his own hardening and tempering.
That so many remarkably good tools were made at that time is still a wonder to many, when we consider that the large shop had from 30 to 40 different men, all using their own secret compounds, heating to suit eyesight, no matter if the day was bright or dark, and then tempering to color. But the day of the old toolmaker has changed.
Now a tool is designed by a tool designer, O.K.'d, and then a print goes to the foreman of the tool department, who specifies the size and gets the steel from the cutting-off department. After finis.h.i.+ng the machine work it goes to the hardening room, and this is the problem we shall now take up in detail.
THE MODERN HARDENING ROOM.--A hardening room of today means a very different place from the dirty, dark smithshop in the corner with the open coal forge. There, when we wanted to be somewhat particular, we sometimes shoveled the coal cinders to one side and piled a great pile of charcoal on the forge. We now have a complete equipment; a gas- or oil-heating furnace, good running water, several sizes of lead pots, and an oil tank large enough to hold a barrel of oil. By running water, we mean a large tank with overflow pipes giving a constant supply. The ordinary hardening room equipment should consist of:
Gas or oil m.u.f.fle furnace for hardening.
Gas or oil forge furnace.
A good size gas or oil furnace for annealing and case-hardening.
A gas or oil furnace to hold lead pots.
Oil tempering tank, gas- or oil-heated.
Pressure blower.
Large oil tank to hold at least a barrel of oil.
Big water tank with screen trays connected with large pipe from bottom with overflow.
Straightening press.
The furnace should be connected with pyrometers and tempering tank with a thermometer.
Beside all this you need a good man. It does not make much difference how completely the hardening department is fitted up, if you expect good work, a small percentage of loss and to be able to tackle anything that comes along, you must have a good man, one who understands the difference between low- and high-carbon steel, who knows when particular care must be exercised on particular work. In other words, a man who knows how his work should be done, and has the intelligence to follow directions on treatments of steel on which he has had no experience.
Jewelers' tools, especially for silversmith's work, probably have to stand the greatest punishment of any all-steel tools and to make a spoon die so hard that it will not sink under a blow from an 1,800-lb. hammer with a 4-ft. drop, and still not crack, demands careful treatment.
To harden such dies, first cover the impression on the die with paste made from bone dust or lampblack and oil. Place face down in an iron box partly filled with crushed charcoal, leaving back of die uncovered so that the heat can be seen at all times. Heat slowly in furnace to a good cherry red. The heat depends on the quality and the a.n.a.lysis of steel and the recommended actions of the steel maker should be carefully followed. When withdrawn from the fire the die should be quenched as shown in Fig. 80 with the face of die down and the back a short distance out of the water.
When the back is black, immerse all over.
[Ill.u.s.tration: FIG. 80.--Quenching a die, face down.]
If such a tank is not at hand, it would pay to rig one up at once, although a barrel of brine may be used, or the back of the die may be first immersed to a depth of about 1/2 in. When the piece is immersed, hold die on an angle as in Fig. 81.
[Ill.u.s.tration: FIG. 81.--Hold die at angle to quench.]
This is for the purpose of expelling all steam bubbles as they form in contact with hot steel. We are aware of the fact that a great many toolmakers in jewelry shops still cling to the overhead bath, as in Fig. 82, but more broken pieces and more dies with soft spots are due to this method than to all the others combined, as the water strikes one spot in force, contracting the surface so much faster than the rest of the die that the results are the same as if an uneven heating had been given the steel.
TAKE TIME FOR HARDENING.--Uneven heating and poor quenching has caused loss of many very valuable dies, and it certainly seems that when a firm spends from $75 to $450 in cutting a die that a few hours could be spared for proper hardening. But the usual feeling is that a tool must be hurried as soon as the hardener gets it, and if a burst die is the result from either uneven or overheated steel and quenching same without judgment, the steel gets the blame.
[Ill.u.s.tration: FIG. 82.--An obsolete method.]
Give the steel a chance to heat properly, mix a little common sense with "your 30 years experience on the other fellows steel." Remember that high-carbon steel hardens at a lower heat than low-carbon steel, and quench when at the right heat in the two above ways, and 99 per cent of the trouble will vanish.
When a die flies to pieces in quenching, don't rush to the superintendent with a "poor-steel" story, but find out first why it broke so that the salesman who sold it will not be able to harden piece after piece from the same bar satisfactorily. If you find a "cold short," commonly called "a pipe," you can lay the blame on the steelmaker. If it is a case of overheating and quenching when too hot, you will find a coa.r.s.e grain with many bright spots like crystals to the hardening depth. If uneven heating is the cause, you will find a wider margin of hardening depth on one side than on the other, or find the coa.r.s.e grain from over-heating on one side while on the other you will find a close grain, which may be just right. If you find any other faults than a "pipe,"
or are not able to harden deep enough, then take the blame like a man and send for information. The different steel salesmen are good fellows and most of them know a thing or two about their own business.
For much work a cooling bath at from 50 to 75F. is very good both for small hobs, dies, cutter plates or plungers. Some work will harden best in a barrel of brine, but in running cold water, splendid results will be obtained. Cutter plates should always be dipped corner first and if any have stripper holes, they should first be plugged with asbestos or fire clay cement.
In general it may be said that the best hardening temperature for carbon steel is the lowest temperature at which it will harden properly.
CARBON IN TOOL STEEL
Carbon tool steel, or "tool steel" as it is commonly called, usually contains from 80 to 125 points (or from 0.80 to 1.25 per cent) of carbon, and none of the alloys which go to make up the high speed steels. This was formerly known also as crucible or "cast"
steel, or crucible cast steel, from the way in which it was made.
This was before the days of steel castings. The advent of these caused so much confusion that the term was soon dropped. When we say "tool steel," we nearly always refer to carbon-tool steel, high-speed steel being usually designated by that name.
For many purposes carbon-steel cutters are still found best, although where a large amount of material is to be removed at a rapid rate, it has given way to high-speed steels.
CARBON STEELS FOR DIFFERENT TOOLS
All users of tool steels should carefully study the different qualities of the steels they handle. Different uses requires different kinds of steel for best results, and for the purpose of designating different steels some makers have adopted the two terms "temper," and "quality,"
to distinguish between them.
In this case temper refers to the amount of carbon which is combined with the iron to make the metal into a steel. The quality means the absence of phosphorous, sulphur and other impurities, these depending on the ores and the methods of treatment.
Steel makers have various ways of designating carbon steels for different purposes. Some of these systems involve the use of numbers, that of the Latrobe Steel Company being given herewith. It will be noted that the numbers are based on 20 points of carbon per unit. The names given the different tempers are also of interest.
Other makers use different numbers.
The temper list follows:
LATROBE TEMPER LIST OF CARBON TOOL STEELS No. 3 temper 0.60 to 0.69 per cent carbon No. 3-1/2 temper 0.70 to 0.79 per cent carbon No. 4 temper 0.80 to 0.89 per cent carbon No. 4-1/2 temper 0.90 to 0.99 pet cent carbon No. 5 temper 1.00 to 1.09 per cent carbon No. 5-1/2 temper 1.10 to 1.19 per cent carbon No. 6 temper 1.20 to 1.29 per cent carbon No. 6-1/2 temper 1.30 to 1.39 per cent carbon No. 7 temper 1.40 to 1.49 per cent carbon
USES OF THE VARIOUS TEMPERS OF CARBON TOOL STEEL
DIE TEMPER.--No. 3: All kinds of dies for deep stamping, pressing and drop forgings. Mining drills to harden only. Easily weldable.
SMITHS' TOOL TEMPER.--No. 3-1/2: Large punches, minting and rivet dies, nailmakers' tools, hammers, hot and cold sets, snaps and boilermakers' tools, various smiths' tools, large shear blades, double-handed chisels, caulking tools, heading dies, masons' tools and tools for general welding purposes.
SHEAR BLADE TEMPER.--No. 4: Punches, large taps, s.c.r.e.w.i.n.g dies, shear blades, table cutlery, circular and long saws, heading dies.
Weldable.
The Working of Steel Part 19
You're reading novel The Working of Steel Part 19 online at LightNovelFree.com. You can use the follow function to bookmark your favorite novel ( Only for registered users ). If you find any errors ( broken links, can't load photos, etc.. ), Please let us know so we can fix it as soon as possible. And when you start a conversation or debate about a certain topic with other people, please do not offend them just because you don't like their opinions.
The Working of Steel Part 19 summary
You're reading The Working of Steel Part 19. This novel has been translated by Updating. Author: Fred H. Colvin and K. A. Juthe already has 638 views.
It's great if you read and follow any novel on our website. We promise you that we'll bring you the latest, hottest novel everyday and FREE.
LightNovelFree.com is a most smartest website for reading novel online, it can automatic resize images to fit your pc screen, even on your mobile. Experience now by using your smartphone and access to LightNovelFree.com
- Related chapter:
- The Working of Steel Part 18
- The Working of Steel Part 20
RECENTLY UPDATED NOVEL

General, Your Wife Is Requesting Your Return Home For Farming
General, Your Wife Is Requesting Your Return Home For Farming Chapter 1458: Chapter 1206 (1): Untitled View : 694,529
My Girlfriend is a Zombie
My Girlfriend is a Zombie Chapter 829: Our Goal is to Tire Him Out! View : 2,285,366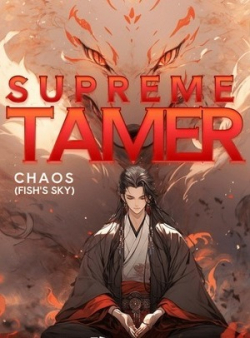
Supreme Tamer
Supreme Tamer Chapter 690: Chapter 559: Battle of the Three Great Main Pets View : 276,629
Trash of the Count's Family
Trash of the Count's Family Book 2: Chapter 249: Lunacy, Worship. And the Way (11) View : 813,070
Super Insane Doctor of the Goddess
Super Insane Doctor of the Goddess Chapter 1020: The Power of a True Dragon! View : 303,260