Pottery, for Artists Craftsmen & Teachers Part 3
You’re reading novel Pottery, for Artists Craftsmen & Teachers Part 3 online at LightNovelFree.com. Please use the follow button to get notification about the latest chapter next time when you visit LightNovelFree.com. Use F11 button to read novel in full-screen(PC only). Drop by anytime you want to read free – fast – latest novel. It’s great if you could leave a comment, share your opinion about the new chapters, new novel with others on the internet. We’ll do our best to bring you the finest, latest novel everyday. Enjoy!
Moulds having moderately wide mouths enable the potter to press his shapes instead of cast them. This method in expert hands is even quicker than casting and has the advantage of imparting a st.u.r.dier look to large shapes. Pressing is also resorted to for those shapes to which it would be difficult for the slip to obtain free access.
[Ill.u.s.tration: FIG. 18--ROLLING OUT CLAY.]
For the ordinary three-piece mould the procedure would be thus: The clay, well wedged and quite plastic, is rolled out as described in Jigger and Jolley work, to a suitable thickness. (Fig. 18.) b.u.t.ter cloth or fine linen will do instead of leather to roll the clay on. The insides of the three parts of the mould are sponged and pieces of the thin rolled clay roughly cut to fit them. These pieces are now fitted and well applied to the three parts by dabbing with the damp sponge. A soft close-textured sponge, or a soft felt dabber, is best for this operation. When closely setting, the edges are trimmed and given a slight bevel. The top is cut straight. Then the mould is a.s.sembled and firmly tied. Some of the waste clay is rolled into thin _ropes_. With the bevelled edges slightly moistened, these ropes are firmly wedged into the two side junctions and round the base. Where the mouth is large enough for the insertion of the hand this is not a difficult operation. If it be narrow, the two halves of the mould may be tied up and the joints welded together before they are a.s.sembled on the base. A coil of clay can then be placed on the edge of the base just clear of the two sides which are now fitted over and tied up. Then a stick sponge is used to join up the base to the sides. (Fig.
19.) After a little while the shape is fit to be removed and is finished in the usual way.
Nothing can rival large thrown shapes for vigour or variety, but unfortunately they are not always within reach of even the good craftsman.
Then this method offers the least objectionable subst.i.tute for them and in clever hands is capable of many fine results.
The following method is used to mould handles or simple applied ornament.
Handles, feet, masks, etc., are usually pressed and stuck on the dry shape with slip. To mould them some skill is necessary if the press is to be quite accurate and free from twist or ugly seams.
[Ill.u.s.tration: FIG. 19--SECTION OF A MOULD. STICK-SPONGE WELDING BASE TO SIDES.]
One way, when the handle or foot is symmetrical, is to cut the model exactly in half. This must be done when the model is tough enough to handle without bending or distorting it. One half is laid cut side down upon a sheet of gla.s.s, and surrounded at a convenient distance with clay walls. Plaster is now poured on to form one half of the mould, and allowed to set. It is then removed and the smooth surface joggled and claywashed (brushed over with claywater). The other half is then very carefully applied to the half still embedded in the mould, the walls built round and the other part of the mould cast. Then all is trimmed up and a groove run round the form as shown. (Fig. 20.) For pressing, the form is well filled with clay and the two halves of the mould strongly pressed together. Any surplus clay will squeeze into the groove and when tough enough to remove the whole is "fettled" and finished before drying and sticking up.
[Ill.u.s.tration: FIG. 20--HALF OF MOULD FOR PRESSING HANDLE.]
With care and practice this method is possible: Build walls and pour in enough plaster to form one half of the mould. Before it stiffens, very carefully press in the handle or ornament just up to the halfway line and allow to set. Joggle, claywash, and cast the second half. Finally, when the object is of any size, clay walls may be used as described in the chapter on Figurines.
CHAPTER V
JIGGER AND JOLLEY WORK
"Earth I am, et is most trwe, desdan me not, for so ar you."
--From an old platter.
Dishes, platters, and to some extent bowls, are usually made on a _Jigger and Jolley_. The jigger has a revolving head, fitted to receive moulds.
The jolley has a pivoted arm to which different profiles may be clamped.
In factories these things are complicated and go by power, but in a studio where the output of platters and dishes is likely to be limited something simple will do. Where the wheel is strong, well-hung, and fitted with a removable head, a contrivance as shown at Fig. 21 can be fitted by any carpenter, that should serve all purposes.
The vertical supports of the jolley arm should be quite rigid. The arm itself must so pivot that the face of any profile screwed onto it will cross the head of the jigger, or wheel if one be used, through the centre.
In other words, the cutting profile must form a diagonal of the circular head. Then, too, it must be hung at a height sufficient to allow a fairly thick block of plaster being used for a mould.
[Ill.u.s.tration: FIG. 21--MAKING A DISH.]
When making these moulds, the slotted wheel head or the jigger head is removed and soaped or oiled. Then a circular block of plaster is cast to fit. This may be done with the aid of a roll of linoleum, much in the way described in casting. The paper cone will, of course, be replaced by the wheel head, bedded face up in clay. This plaster block has to be moulded to the exact size of the dish or plaque required. To do this a profile of zinc is necessary. The true section of the dish is drawn full size, and profiles giving one half of the back and front are traced on a stout sheet of zinc. The zinc is roughly cut to shape with shears and then finished with a file to a chisel edge (see cut). The two profiles are then firmly backed with shaped wooden forms, slotted to screw onto the arm of the jolley. The profile giving the _face_ of the plaque is securely adjusted in a horizontal position, the inner point, giving the centre of the platter, being exactly over the centre of the jigger head. The plaster block, which should be turned down before it sets hard, is s.h.i.+pped back into position, the jigger revolved and the profile gradually pressed down until the true section is obtained, _i.e._ when the profile is exactly horizontal again. The mould is now removed, trimmed at the sides if necessary, and set apart to dry. It is then ready to use. The mould is slipped into position and revolved to insure even rotation. Then the profile giving the back of the platter screwed onto the arm and both adjusted until the stop allows the profile to rest at just that distance from the mould required by the thickness of the platter. (Fig. 22.)
[Ill.u.s.tration: FIG. 22--PROFILE IN POSITION ABOVE PLATE MOULD.]
The arm is then swung clear of the mould, which is well sponged with water to receive the clay. This is carefully wedged and then rolled out or batted flat on a piece of leather until it is a little thicker than the thickest part of the platter (see Fig. 23). The slab so made is smoothed with a palette knife, taken up, leather and all, slapped onto the mould, clay side down, and the leather removed. The clay is now well dabbed down with a wet sponge or dabber, to take out all wrinkles, pressed firmly onto the mould and the waste cut off.
[Ill.u.s.tration: FIG. 23--CUTTING EDGE OF PROFILE.]
Now the jigger or head is set spinning, the jolley pulled over it, and the profile gently pressed into the clay. Water is used freely to prevent the profile sticking, and as it becomes clogged the clay is removed. The turning is continued until the profile comes to a stop on the rest. Holes that may appear should be filled up before the finish, at which time the surface should present a smooth unscratched appearance. The shape is allowed to dry on the mould until tough enough to be slipped face down onto a perfectly flat slab dusted with fine sand or flint to prevent sticking. In this position it is left to dry, when the edges are nicely trimmed with fine sandpaper.
For bowls the process is similar, but the mould here gives the outside and the profile the inside as in cut. (Fig. 24.) If made on the outside, they split before they can be removed. With small bowls the clay is wedged and a lump pressed into the mould by hand. With large bowls requiring a deep foot this must be turned separately and stuck on after the bowl is removed from the mould.
[Ill.u.s.tration: FIG. 24--BOWL.]
Where a jigger and jolley is not available, plates and bowls may be duplicated as follows: Place the plate bottom up on a well-soaped surface or a piece of gla.s.s. Should the plate not lie quite flat, caulk the apertures with clay, then all round and distant one and one half inches from the rim, build clay walls, or fix a containing band of linoleum, of sufficient height to allow plaster being poured in an inch and a half above the base or foot of the model. Mix fairly stiff plaster and pour in.
Let it set, and then remove walls and the model. This gives a mould of the reverse of the plate or bowl. The mould is thoroughly dried before using and then sponged with clean water. Clay of the desired thickness is then rolled out as described and applied to the mould and dabbed flat with a sponge or dabber. The finish is imparted with the fingers and the surplus at edges trimmed with a knife. When tough, the press is slipped out and reversed to dry on a piece of sanded gla.s.s. Where there is a rim to the plate or bowl, this should be filled in cleanly with clay before the whole is pressed. It is of course impossible to mould thus bowls that possess a deep or under-cut foot.
[Ill.u.s.tration: FIG. 25--PLATE MOULDED TO GIVE BACK.]
[Ill.u.s.tration: FIG. 26--MOULD. TO GIVE FACE OF PLATE.]
[Ill.u.s.tration: THE KICK WHEEL.]
[Ill.u.s.tration: Egypt. B.C. 2000 ANCIENT EGYPTIAN POTTER.]
CHAPTER VI
THROWN SHAPES
"The lyf so short, the craft so longe to learne."
--CHAUCER.
The wheel is the true fountain head of all beautiful shapes, and the student who would become a potter cannot get "on the wheel" too soon.
Throwing, sometimes _spinning_, is the term applied to the making of shapes on the wheel. Interesting and really fine pots may be built or cast, but the ultimate appeal rests with the thrown shape.
Unfortunately, a complete mastery of throwing is not to be gained by a few spasmodic wrestles with the wheel. It comes only with long hours of concentrated effort. Having watched an accomplished thrower and seen the full round shapes rise so easily between his dexterous fingers, it is with a severe shock that one realizes at the first attempt the skill and practice that will be required before such a desirable proficiency is attained.
The best kind of wheel is the kick wheel shown in the ill.u.s.tration. With this the feet, hands, and head work in harmony, accelerating or r.e.t.a.r.ding the motions as required. It is a not distant relation of the earliest wheel, which was a heavy head on a short shaft, pivoted in a stone socket.
Set spinning by hand, it was kept revolving some time by its own momentum.
This form of wheel is used even to this day in the near and far East.
Its first development was a secondary wheel and driving band turned by hand. This led to the wheel shown in the frontispiece and to the kick wheel and again on to the factory wheel. This in its turn is being superseded by the steam wheel, which gears onto a running band, the foot being used to start, stop, and regulate the speed. The two last named were introduced with the idea of accelerating the production rather than the improvement of the shapes. No doubt the now primitive kick wheel, much as used by the potters of the Renaissance, will be found good enough for us.
The tools required for throwing, after the wheel itself is secured, are as follows: a thin copper wire twisted between two bits of wood, a p.r.i.c.ker, a fine soft sponge, another bit of sponge tied to a stick, one or two modelling tools and a rib (see Fig. 27).
[Ill.u.s.tration: FIG. 27--1, "Rib"; 2, Modelling Tools; 3, p.r.i.c.ker; 4, Sponge; 5, Wire; 6, 7, and 8, Shaving Tools; 9, Leather. THROWING & SHAVING TOOLS.]
The clay is first knocked up into shape ready for the throwing. To do this it is _wedged_, a fair-sized piece being taken in both hands and thrown violently down on the bench, cut across, and smashed together again. This process is repeated until all air bubbles are expelled. This is ascertained by cutting with a wire. The finger is then pa.s.sed across the surface to tell if it is well together, and not hard and soft in streaks.
If, as must happen in a small pottery, the clay is out of condition, it is best remedied by cutting it with the wire into thin slabs, piling them criss-cross and then wedging the ma.s.s. If still streaky, it can be quickly tempered, piece by piece. A double handful is torn across, wedged together at a different angle between the hands, re-torn, and re-wedged, until hard and soft are welded indistinguishably together.
This thorough wedging is essential, as with beginners a small lump or bubble will usually be sufficient to bring about the collapse of the shape.
Pottery, for Artists Craftsmen & Teachers Part 3
You're reading novel Pottery, for Artists Craftsmen & Teachers Part 3 online at LightNovelFree.com. You can use the follow function to bookmark your favorite novel ( Only for registered users ). If you find any errors ( broken links, can't load photos, etc.. ), Please let us know so we can fix it as soon as possible. And when you start a conversation or debate about a certain topic with other people, please do not offend them just because you don't like their opinions.
Pottery, for Artists Craftsmen & Teachers Part 3 summary
You're reading Pottery, for Artists Craftsmen & Teachers Part 3. This novel has been translated by Updating. Author: George J. Cox already has 686 views.
It's great if you read and follow any novel on our website. We promise you that we'll bring you the latest, hottest novel everyday and FREE.
LightNovelFree.com is a most smartest website for reading novel online, it can automatic resize images to fit your pc screen, even on your mobile. Experience now by using your smartphone and access to LightNovelFree.com
- Related chapter:
- Pottery, for Artists Craftsmen & Teachers Part 2
- Pottery, for Artists Craftsmen & Teachers Part 4
RECENTLY UPDATED NOVEL

Nine Star Hegemon Body Arts
Nine Star Hegemon Body Arts Chapter 5675: Ruler, Minister, Assistant, Envoy View : 8,873,355
The Great Mage Returns After 4000 Years
The Great Mage Returns After 4000 Years Book 2 Chapter 595 View : 526,674
I Love Destroying Worlds' Plot
I Love Destroying Worlds' Plot Chapter 1551 21.8 Fifth Violet Star - Xiu Mo View : 520,492
The Strongest War God
The Strongest War God Chapter 1394: This Path, Burying the Heaven's Favorites View : 540,672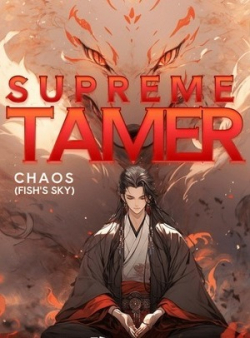
Supreme Tamer
Supreme Tamer Chapter 770: Chapter 640: Natural Disasters and Human Calamities, Crisis in Barbarian Valley View : 321,635
I'll Be the Male Leads Sister-in-Law
I'll Be the Male Leads Sister-in-Law Chapter 559 View : 191,558