Pottery, for Artists Craftsmen & Teachers Part 7
You’re reading novel Pottery, for Artists Craftsmen & Teachers Part 7 online at LightNovelFree.com. Please use the follow button to get notification about the latest chapter next time when you visit LightNovelFree.com. Use F11 button to read novel in full-screen(PC only). Drop by anytime you want to read free – fast – latest novel. It’s great if you could leave a comment, share your opinion about the new chapters, new novel with others on the internet. We’ll do our best to bring you the finest, latest novel everyday. Enjoy!
[Ill.u.s.tration: FIG. 53--DIPPING.]
When glazing with a transparent glaze over under-glaze painting a thin coat is advisable. If it be thick and run, the painting is spoiled; but if, after firing, it appears thin, another light spray may be tried. But whole chapters of writing will never settle these points. Repeated trials on odd pieces of biscuit will elucidate more than many books. In packing a glost or glaze kiln stilts and spurs instead of saddles must be used to prevent the pots from sticking to the floor or shelves. (Figs. 49 and 54.) For the same reason the pots must not touch each other. With glazes requiring a high temperature the s.p.a.ce between pots of different colour should be considerable. An appreciable amount of glaze is liberated in the intense heat and a blue pot will often leave a distinct blue patch on any light pot placed too near. Soft glazes liable to run or drip should be placed on separate bats well flinted beneath. Any crack in the m.u.f.fle should be well stopped and lime may be used to neutralize the effects of any sulphur that may enter.
[Ill.u.s.tration: FIG. 54--STILTS, BITS AND SPURS.]
As the back is usually hotter than the front the hard glazes should be packed first, and by selecting suitable shapes a good _setter_ will pack a surprising amount into even a small kiln. The clamming should be done with care, as bits are liable to flake off and stick to the glaze. The top plug only need be left out and the lighting up proceeded with as before.
The gradual increase of heat is very essential in firing glaze, for any sudden jump or reduction will play all manner of games in a glost oven.
The slow start is not so important, there being no risk of _blowing_.
Indeed the glaze is best in a sharp quick fire.
Although cones should always be used and are excellent indicators, experience will soon show when a kiln is fired up. It may be advisable to go on a little after the cone is over until all looks fluxed so as to get rid of bubbles. These appear in some glazes until the last. They do not always go down on cooling, but those glazes that bubble through over-firing should be avoided. Possibly the trouble will arise from sulphur in the body which must be corrected. Trials are always useful but they must be small and easily hooked out, as constant poking about at the spy hole lowers the temperature of the m.u.f.fle at the front, just where it is most difficult to get it up.
When fired, a glost kiln should cool very slowly, for any sudden access of cold air is liable to stunt or crack the pots. When firing over glaze decoration where the glaze does not run, the packing is much simplified.
With low-firing l.u.s.tres the pots may even touch each other.
All this has been set out at great length but we shall find over and above this that each kiln has its own little ways which must be studied and humoured before the best results can be obtained.
The chief thing to avoid is a sudden flush or jump in the heat. The main thing to aim at is a slow start steadily increasing to a sharp finish. The state of the m.u.f.fle, a dry or a damp day, will modify each firing a little, but the above generalization will have a fairly wide application to the working of a small kiln.
Unpacking is a compound of despair and delight, and is best done slowly.
As the colour dies the clamming, if any, may be knocked away, and later on the spy plugs removed. When comparatively cold, the door may be opened slightly, and left so for one or two hours. Then the front pots can be extracted but those at the back should be allowed another half hour. Be very careful of the razor edges of broken stilts or glaze dips. A steel chisel should be used for chopping rough edges or removing refractory stilts. If necessary the bases may be ground on an emery wheel until the pot stands true.
CHAPTER XII
GLAZES AND l.u.s.tRES
"I began to think that if I should discover how to make enamels I could make earthen vessels and other things very prettily, because G.o.d had gifted me with some knowledge of drawing."
--PALISSY.
It is in this department of potting, with its surprises, difficulties, and disappointments, its rare but exciting successes, that for most potters the greatest interest lies. To those of a scientific bent it is perhaps the summit of the craft, but the artist groping amidst formulas and methods may take heart. The finest work in pottery was not produced by scientists alone and does not depend altogether upon the quality of its paste, its unique colour, or strange l.u.s.tre. The last word, the form, decoration, and craftsmans.h.i.+p, is with the artist.
It is beyond the scope of a book of this description to enter into a necessarily long and complicated account of the different processes concerned in the composition of glazes. It will be sufficient to indicate their leading characteristics plainly enough to enable the student to start experimenting. None can afford to miss opportunities for experiment, just as surely as none can afford to be always experimenting.
For a full description of materials and glazes and their manufacture such books as those of Drs. Shaw, Furnival, and Hainbach are recommended.
Putting aside salt glaze we find a countless number of both lead and leadless glazes. They range from the thin silicious coating of the ancients up to the rich alkaline glazes of the Persians and Chinese; from the raw galena of peasant pottery to the rich Majolicas and fine hard glazes of modern commerce. Salt glaze is obtained by the vaporizing of salt inside the kiln at a great heat. The sodium oxide so formed combines with the silicates in the clay to form a very thin coat of refractory gla.s.s, intimately connected with the body. Porcelain glazes, though not differing so much in composition from the ordinary _fine_ earthenware glazes, are extremely hard, being compounded of kaolin, felspar, and quartz, with possibly limestone and ground sherds. It has in common with the salt glaze the close union with the body, so that when fractured the line of demarcation between glaze and body is indeterminable.
With a few minor exceptions the following list comprises the ingredients of all colourless glazes:
Kaolin Quartz Cornish stone Felspar Fluorspar Flint Sand Barytes Bis.m.u.th Gypsum Limestone Nitre Borax Bone-ash White lead Red lead Zinc oxide Tin oxide Salt Soda Potash
These materials must be free from all trace of iron. They are pulverized and some are calcined or oxidized. Then they are mixed in varying quant.i.ties to form the glaze ma.s.s. This ma.s.s is easily fusible when lead or borax is present in large proportions, more infusible or harder the more silica it contains, and very refractory if alumina is present in any quant.i.ty. The silica forming the gla.s.sy part of the glaze is stiffened by the presence of alumina, which stops any tendency to run.
Lead is very largely used as a powerful flux at low temperatures but is unsuited to hard glazes. Borax and boracic acid are important const.i.tuents of leadless glazes. They are used to replace some of the silica, than which they are more fusible. Matt or non-reflective glazes are opaque and less vitreous than the gla.s.sy glazes. They do not flux or run.
All these minerals are finely ground before mixing. Then those insoluble are mixed and _fritted_; that is, fused in a crucible or fritting furnace to a greater or less degree, according to the hardness of the glaze. If fused into a gla.s.s, the melted ma.s.s is poured into water to facilitate the next process, which is its reduction to a fine powder by re-grinding. Then the completing ingredients are added and the ma.s.s coloured by the addition of metallic oxides. Of these the chief are:
Iron Copper Nickel Antimony Cobalt Chrome Manganese t.i.tanium
and the more precious metals, in various forms, as oxides, carbonates, sulphates, and nitrates soluble in the glaze at great heat.
These metals impart the many varied colours found in pottery. Zinc oxide is used to brighten a glaze or to stabilize colour. Tin oxide, which is insoluble at great heat but remains in suspension, gives opacity.
This is no more than a skeleton outline of the intricate processes often used in the fabrication of a glaze. The manifold minerals, metals, oxides, acids, and alkalies are used in a variety of ways by the modern chemical potter.
To all this seeming complication is added the question of pastes and bodies. There then arises the great problem of fitting one to the other.
Salt glaze and porcelain excepted, the finished pot presents three stratas. Outside is the glaze, next the body, then inside the glaze again.
If the coefficient of expansion of these three layers differs, in other words, if the glaze does not fit, the result is _crazing_, that bugbear of the potter.
This crazing, which has been followed up and developed into their delightful _crackle_ by the Chinese, may show itself at once or only after a lapse of months. It appears as a minute network of fine cracks over the entire surface of the pot. It is often not unsightly, but sooner or later it must cause devitrification. The glaze after a time a.s.sumes an evanescent iridescence followed by a dull smoky appearance; finally, perhaps not for many years, it decomposes and peels off.
With low-firing natural clays rich in silica and iron, the craze is not of much consequence. The body itself at a moderately high temperature becomes non-porous. With hard short bodies containing lime or chalk it may have quite disastrous consequences. Water placed inside will eventually percolate through leaving a network of grey lines all over the pot and completely spoiling its appearance.
It will be readily granted that, whether porous or non-porous, a craze is most undesirable on any piece of pottery that may be used for food or drink.
It is here that the commercial potter is such an admirable fellow. Many of the glazes on modern tablewares are perfect for their purposes. Sometimes only a little more fire is needed to stop the nuisance, but a bad craze usually needs more attention. The glaze requires stiffening, and the addition of ground flint or quartz, China stone or clay and felspar introduces alumina and silica and raises the fusing point. The subst.i.tution of borax for a portion of the silica can also be tried and will permit the use of slightly lower firing point.
If the glazes are bought ready mixed, the body must be altered instead.
Refractory China clays should be replaced by more fusible clays or some reduction made in the amount of infusible materials. The addition of ground sherds or flint will have a contrary effect should the glaze peel or crack at the edges, as it may do on a very silicious body. In working with natural clays on a moderate scale it will be found best to mix "fat"
or rich natural clays with those of a more porous or hard nature. A few graded mixtures submitted to a thorough trial should soon show when a sympathy has been established between the body and glaze.
The receipts given on pages 183 and 184 will make good colourless glazes without fritting if thoroughly ground in a mortar and pa.s.sed through a sieve. Numbers 3 and 7, when calcined, will give much more even results and they can be coloured by the addition of the oxides named. But simple as it sounds, the was.h.i.+ng, grinding, fritting, re-grinding, and sieving is a long and laborious process demanding machinery, and on that account is unsuited to schools or potters of moderate means. Glazes like Nos. 1 and 2 will do quite well for elementary work but unless the appliances are to hand the manufactured article will have to be relied on for more finished and ambitious work.
If, indeed, you are already in possession of a good receipt for a fine colour and glaze, one quite worth while, so much the better. Mix it and feel the joy of the Compleat Potter unafraid of spoiling his own good shapes with a faulty or unknown glaze.
Admittedly, to get anywhere in an original direction systematic research is essential. One must keep on experimenting, keep on hoping, and keep on taking notes; but at the start let us not be too impatient or independent if we wish to produce good pots.
There is often among young potters a false pride that prevents them using, and among old potters acknowledging the use of, the manufactured article.
Why this should be is a little difficult to understand. A painter might far more reasonably be ashamed to use modern tube colours or a stained-gla.s.s craftsman as logically insist on making his own gla.s.s, as a potter in the twentieth century refuse to avail himself of the wonderful range of glazes that modern research has placed at his disposal. These resources should be used intelligently, not mechanically, or by the book--artistically, inventively, secretly, if you will, but they should be used--until the mult.i.tudinous experiments have borne fruit and repeated trials convince you that at last you possess some gem of research worth, as well it may be, the months of patient toil engendered in its production.
The various receipts are given on pages 183 and 184 without a.n.a.lysis of the composition of the paste or body to which they were applied. The first group have been used on common earthenware clays with complete satisfaction. They are to be considered as points of departure for future experiments in which they may be modified at will, and not regarded as a contribution to the science of glaze making.
In colouring it will be found that combinations of cobalt, iron, and copper oxides give an interesting range of simple blues or greens; iron and manganese browns; and so forth. The colour ma.s.s or stain is ground fine and lawned, and from about 2 to 7 per cent mixed with the colourless glaze ma.s.s, according to the depth of colour required. The ordinary under-glaze colours may be used to stain glazes, the percentage being fixed by small trials. For the rare colours--turquoise, crimson, or purple--a more complicated process is necessary and only perfected after many trials. The ingredients of these fine colours are naturally kept secret by their fortunate possessors.
It must be noted that a glaze suited to one body may peel or run off an unsuitable one. Then a colourant is affected differently by a lead or an alkaline base in the glaze. Again, copper and iron oxides may help to flux a glaze, whilst cobalt or nickel will exert a contrary effect. Cobalt, being a strong colourant, will need a sparing use, whereas a similar percentage of iron will merely tinge the glaze ma.s.s. And so _ad infinitum_.
It is self-evident that any attempt to emulate the vast range of the modern ceramic chemist is doomed to failure. To a craftsman the fabrication of one fine individual glaze or l.u.s.tre is an achievement of which he may be proud, and for which he will find abundant and varied uses. In this connection it is encouraging to the craftsman to learn from so high an authority as W. Burton, Esq., F.C.S., that it is impossible to obtain with purified oxides the fine tones got by the Orientals with impure materials. Further, that the simple glaze of the Persians--a mixture of clean white sand with soda or wood ash or potash--is still the best for under-glaze painting. Although tastes differ so widely, invariably it will be found that more and more heat will be the cry.
Imperceptibly this leads to the desire for hard, cold, "fat" translucent glazes, neither matt nor glossy. And on the summit, far out of reach, stand the wonders of the Old Chinese.
l.u.s.tRES
There are several kinds of l.u.s.tres, but the true l.u.s.tres possess a pearly iridescence in addition to their colour. The copper and silver _l.u.s.tres_ of the eighteenth-century Staffords.h.i.+re potters were thin metallic films over the whole surface of the glaze. Gold or silver solutions were used.
Pottery, for Artists Craftsmen & Teachers Part 7
You're reading novel Pottery, for Artists Craftsmen & Teachers Part 7 online at LightNovelFree.com. You can use the follow function to bookmark your favorite novel ( Only for registered users ). If you find any errors ( broken links, can't load photos, etc.. ), Please let us know so we can fix it as soon as possible. And when you start a conversation or debate about a certain topic with other people, please do not offend them just because you don't like their opinions.
Pottery, for Artists Craftsmen & Teachers Part 7 summary
You're reading Pottery, for Artists Craftsmen & Teachers Part 7. This novel has been translated by Updating. Author: George J. Cox already has 658 views.
It's great if you read and follow any novel on our website. We promise you that we'll bring you the latest, hottest novel everyday and FREE.
LightNovelFree.com is a most smartest website for reading novel online, it can automatic resize images to fit your pc screen, even on your mobile. Experience now by using your smartphone and access to LightNovelFree.com
- Related chapter:
- Pottery, for Artists Craftsmen & Teachers Part 6
- Pottery, for Artists Craftsmen & Teachers Part 8
RECENTLY UPDATED NOVEL

Nine Star Hegemon Body Arts
Nine Star Hegemon Body Arts Chapter 5675: Ruler, Minister, Assistant, Envoy View : 8,873,355
The Great Mage Returns After 4000 Years
The Great Mage Returns After 4000 Years Book 2 Chapter 595 View : 526,674
I Love Destroying Worlds' Plot
I Love Destroying Worlds' Plot Chapter 1551 21.8 Fifth Violet Star - Xiu Mo View : 520,492
The Strongest War God
The Strongest War God Chapter 1394: This Path, Burying the Heaven's Favorites View : 540,672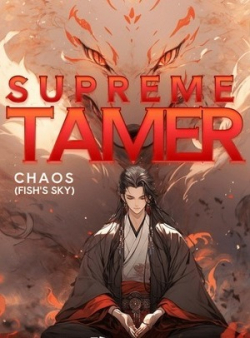
Supreme Tamer
Supreme Tamer Chapter 770: Chapter 640: Natural Disasters and Human Calamities, Crisis in Barbarian Valley View : 321,635
I'll Be the Male Leads Sister-in-Law
I'll Be the Male Leads Sister-in-Law Chapter 559 View : 191,558