The Handbook of Soap Manufacture Part 13
You’re reading novel The Handbook of Soap Manufacture Part 13 online at LightNovelFree.com. Please use the follow button to get notification about the latest chapter next time when you visit LightNovelFree.com. Use F11 button to read novel in full-screen(PC only). Drop by anytime you want to read free – fast – latest novel. It’s great if you could leave a comment, share your opinion about the new chapters, new novel with others on the internet. We’ll do our best to bring you the finest, latest novel everyday. Enjoy!
CHAPTER VII.
TOILET, TEXTILE AND MISCELLANEOUS SOAPS.
_Toilet Soaps--Cold Process Soaps--Settled Boiled Soaps--Remelted Soaps--Milled Soaps--Drying--Milling and Incorporating Colour, Perfume, or Medicament--Perfume--Colouring Matter--Neutralising and Superfatting Material--Compressing--Cutting--Stamping--Medicated Soaps--Ether Soap--Floating Soaps--Shaving Soaps--Textile Soaps--Soaps for Woollen, Cotton and Silk Industries--Patent Textile Soaps--Miscellaneous Soaps._
_Toilet Soaps._--By the term "toilet soap" is inferred a soap specially adapted for toilet use by reason not only of its good detergent and lathering qualities, but also on account of its freedom from caustic alkali and any other ingredient likely to cause irritation or injury to the skin.
Toilet soaps may be simply cla.s.sified according to their method of preparation into the following four cla.s.ses:--
(1) Cold process soaps.
(2) Settled boiled soaps.
(3) Remelted soaps.
(4) Milled soaps.
Soaps of the first cla.s.s are of comparatively trifling importance, having been superseded by the other qualities. Details of the "cold process" have already been given on page 46; it is only necessary to add the desired perfume and colouring matter to the soap.
The second cla.s.s consists of good quality settled soaps, direct from the copper, to which have been added, prior to framing, suitable perfume and colouring matter, also, if necessary, dealkalising materials.
The third cla.s.s is represented by soaps made by the old English method of remelting, which are often termed "perfumers'," or "little pan"
soaps. The soap-base or mixture of various kinds of soap is remelted in a steam-jacketed pan, or pan provided with steam coils, and agitated.
The agitation must not be too vigorous or lengthy, or the soap will become aerated. When all the soap is molten, additions of pearl ash solution are made to give it a finer and smoother texture, render it more transparent, and increase its lathering properties. The necessary colour, in a soluble form, is well incorporated, and lastly the perfume.
Owing to volatilisation, much of the perfume is lost when added to hot soap, and it is necessary to add a large quant.i.ty to get the desired odour; hence the cheaper essential oils have to be used, so that the perfume of this cla.s.s of soap is not so delicate as that of milled soaps, although it is quite possible to produce remelted soaps as free from uncombined alkali as a milled toilet soap.
Palm-oil soap often forms the basis for yellow and brown toilet soaps of this cla.s.s. The old-fas.h.i.+oned Brown Windsor soap was originally a curd soap that with age and frequent remelting had acquired a brown tint by oxidation of the fatty acids--the oftener remelted the better the resultant soap.
Medicaments are sometimes added to these soaps, _e.g._, camphor, borax, coal-tar, or carbolic. Oatmeal and bran have been recommended in combination with soap for toilet purposes, and a patent (Eng. Pat.
26,396, 1896) has been granted for the use of these substances together with wood-fibre impregnated with boric acid.
After cooling in small frames, the soap is slabbed, and cut into blocks, and finally into portions suitable for stamping in a press (hand or steam driven) with a design or lettering on each side.
_Milled Toilet Soaps._--Practically all high-cla.s.s soaps now on the market pa.s.s through the French or milling process. This treatment, as its name implies, was first practised by the French who introduced it to this country, and consists briefly of (i.) drying, (ii.) milling and incorporating colour, perfume or medicament, (iii.) compressing, and (iv.) cutting and stamping.
The advantages of milled soap over toilet soap produced by other methods are that the former, containing less water and more actual soap, is more economical in use, possesses a better appearance, and more elegant finish, does not shrink or lose its shape, is more uniform in composition, and essential oils and delicate perfumes may be incorporated without fear of loss or deterioration.
Only soap made from best quality fats is usually milled, a suitable base being that obtained by saponifying a blend of the finest white tallow with a proportion, not exceeding 25 per cent., of cocoa-nut oil, and prepared as described in Chapter V.
The first essential of a milling base is that the saponification should be thorough and complete; if this is not ensured, rancidity is liable to occur and a satisfactory toilet soap cannot be produced. The soap must not be short in texture or brittle and liable to split, but of a firm and somewhat plastic consistency.
(i.) _Drying._--The milling-base, after solidification in the frames, contains almost invariably from 28 to 30 per cent. of water, and this quant.i.ty must be reduced to rather less than half before the soap can be satisfactorily milled. Cutting the soap into bars or strips and open piling greatly facilitates the drying, which is usually effected by chipping the soap and exposing it on trays to a current of hot air at 95-105 F. (35-40 C.).
There are several forms of drying chambers in which the trays of chips are placed upon a series of racks one above another, and warm air circulated through, and Fig. 21 shows a soap drying apparatus with fan made by W. J. Fraser & Co., Ltd., London.
The older method of heating the air by allowing it to pa.s.s over a pipe or flue through which the products of combustion from a c.o.ke or coal fire are proceeding under the floor of the drying chamber to a small shaft, has been superseded by steam heat. The air is either drawn or forced by means of quickly revolving fans through a cylinder placed in a horizontal position and containing steam coils, or pa.s.sed over steam-pipes laid under the iron grating forming the floor of the chamber.
[Ill.u.s.tration: FIG. 21.--Soap-drying apparatus.]
It will be readily understood that in the case of a bad conductor of heat, like soap-chippings, it is difficult to evaporate moisture without constantly moving them and exposing fresh surfaces to the action of heat.
In the Cressonnieres' system, where the shavings of chilled soap are dried by being carried through a heated chamber upon a series of endless bands (the first discharging the contents on to a lower belt which projects at the end, and is moving in the opposite direction, and so on), this is performed by intercepting milling rollers in the system of belts (Eng. Pat. 4,916, 1898) whereby the surfaces exposed to the drying are altered, and it is claimed that the formation of hardened crust is prevented.
In the ordinary methods of drying, the chips are frequently moved by hand to a.s.sist uniform evaporation.
The degree of saturation of the air with moisture must be taken into consideration in regulating the temperature and flow of air through the drying chamber, and for this purpose the use of a hygrometer is advantageous.
It is very important that the correct amount of moisture should be left in the soap, not too much, nor too little; the exact point can only be determined by judgment and experience, and depends to a considerable extent upon the nature of the soap, and also on the amount of perfume or medicament to be added, but speaking generally, a range of 11 to 14 per cent. gives good results. If the soap contains less than this amount it is liable to crumble during the milling, will not compress satisfactorily, and the finished tablet may have a tendency to crack and contain gritty particles so objectionable in use. If, on the other hand, the soap is left too moist, it is apt to stick to the rollers and mill with difficulty, and during compression the surface a.s.sumes a blistered and sticky appearance.
(ii.) _Milling and Incorporation of Colour, Perfume or Medicament._--The object of milling is to render the soap perfectly h.o.m.ogeneous, and to reduce it to a state in which colour, perfume, or any necessary neutralising material or other substance may be thoroughly incorporated.
The milling machine consists of smooth granite rollers, fitted with suitable gearing and working in an iron framework (Fig. 22). The rollers are connected in such a manner that they rotate at different speeds, and this increases the efficiency of the milling, and ensures that the action of the rollers is one of rubbing rather than crus.h.i.+ng.
By means of suitably arranged screws the pressure of the rollers on one another can be adjusted to give the issuing soap any desired thickness; care should be taken that the sheets of soap are not unnecessarily thick or the colour and odour will not be uniform.
The soap, in the form of chips, is introduced on to the rollers through a hopper, and after one pa.s.sage through the mill, from bottom to top, one of the serrated knife edges is applied and the ribbons of the soap are delivered into the top of the hopper where the colour, perfume, and any other desired admixture is added, and the milling operation repeated three or four times. When the incorporation is complete the other sc.r.a.per is fixed against the top roller and the soap ribbon pa.s.sed into the receptacle from which it is conveyed to the compressor. A better plan, however, especially in the case of the best grade soaps, where the perfumes added are necessarily more delicate and costly, is to make the addition of the perfume when the colour has been thoroughly mixed throughout the ma.s.s. Another method is to mill once and transfer the ma.s.s to a rotary mixing machine, fitted with internal blades, of a peculiar form, which revolve in opposite directions one within the other as the mixer is rotated. The perfume, colouring matter, etc., are added and the mixer closed and set in motion, when, after a short time, the soap is reduced to a fine granular condition, with the colour and perfume evenly distributed throughout the whole. By the use of such machines, the loss of perfume by evaporation, which during milling is quite appreciable, is reduced to a minimum, and the delicacy of the aroma is preserved unimpaired.
[Ill.u.s.tration: FIG. 22.--Milling machine.]
Prolonged milling, especially with a suitable soap base, tends to produce a semi-transparent appearance, which is admired by some, but the increased cost of production by the repeated milling is not accompanied by any real improvement in the soap.
_Perfume._--The materials used in perfuming soap will be dealt with fully in the next chapter. The quant.i.ty necessary to be added varies considerably with the nature of the essential oils, and also the price at which the soap is intended to be sold. In the cheaper grades of milled soaps the quant.i.ty will range from 10-30 fluid ozs. per cwt., and but rarely exceeds 18-20 ozs., whereas in more costly soaps as much as 40-50 fluid ozs. are sometimes added to the cwt.
_Colouring Matter._--During recent years an outcry has been made against highly coloured soaps, and the highest cla.s.s soaps have been manufactured either colourless or at the most with only a very delicate tint. It is obvious that a white soap guarantees the use of only the highest grade oils and fats, and excludes the introduction of any rosin, and, so far, the desire for a white soap is doubtless justified. Many perfumes, however, tend to quickly discolour a soap, hence the advantage of giving it a slight tint. For this purpose a vegetable colouring matter is preferable, and chlorophyll is very suitable.
[Ill.u.s.tration: FIG. 23.--Compressor.]
A demand still exists for brightly coloured soaps, and this is usually met by the use of coal-tar dyes. The quant.i.ty required is of course extremely small, so that no harm or disagreeable result could possibly arise from their use.
_Neutralising and Superfatting Material._--If desired, the final neutralisation of free alkali can be carried out during the milling process, any superfatting material being added at the same time. The chief neutralising reagents have already been mentioned in Chapter VI.
With regard to superfatting material, the quant.i.ty of this should be very small, not exceeding 6-8 ozs. per cwt: The most suitable materials are vaseline, lanoline, or spermaceti.
[Ill.u.s.tration: FIG. 24--Hand soap-stamping press.]
(iii.) _Compressing._--The next stage is the compression and binding of the soap ribbons into a solid bar suitable for stamping, and the plant used (Fig. 23) for this purpose is substantially the same in all factories. The soap is fed through a hopper into a strong metal conical-shaped tube like a cannon, which tapers towards the nozzle, and in which a single or twin screw is moving, and the soap is thereby forced through a perforated metallic disc, subjected to great pressure, and compressed. The screws must be kept uniformly covered with shavings during compression to obviate air bubbles in the soap.
[Ill.u.s.tration: FIG. 25.--Screw press.]
The soap finally emerges through the nozzle (to which is attached a cutter of suitable shape and size according to the form it is intended the final tablet to take) as a long, polished, solid bar, which is cut with a knife or wire into lengths of 2 or 3 feet, and if of satisfactory appearance, is ready for cutting and stamping. The nozzle of the plodder is heated by means of a Bunsen burner to about 120 or 130 F. (49-55 C.) to allow the soap to be easily forced out, and this also imparts a good gloss and finish to the ejected bar--if the nozzle is too hot, however, the soap will be blistered, whereas insufficient heat will result in streaky soap of a poor and dull appearance.
(iv.) _Cutting and Stamping._--In cutting the soap into sections for stamping, the cutter should shape it somewhat similar to the required finished tablet.
Many manufacturers cut the soap into sections having concave ends, and in stamping, the corners are forced into the concavity, with the result that unsightly markings are produced at each end of the tablet. It is preferable to have a cutter with convex ends, and if the stamping is to be done in a pin mould the shape should be a trifle larger than the exact size of the desired tablet.
[Ill.u.s.tration: FIG. 26--Pin mould.]
The stamping may be performed by a hand stamper (Fig. 24), a screw press (Fig. 25), or by a steam stamper. The screw press works very satisfactorily for toilet soaps.
There are two kinds of moulds in use for milled soaps:--
The Handbook of Soap Manufacture Part 13
You're reading novel The Handbook of Soap Manufacture Part 13 online at LightNovelFree.com. You can use the follow function to bookmark your favorite novel ( Only for registered users ). If you find any errors ( broken links, can't load photos, etc.. ), Please let us know so we can fix it as soon as possible. And when you start a conversation or debate about a certain topic with other people, please do not offend them just because you don't like their opinions.
The Handbook of Soap Manufacture Part 13 summary
You're reading The Handbook of Soap Manufacture Part 13. This novel has been translated by Updating. Author: H. A. Appleton and W. H. Simmons already has 587 views.
It's great if you read and follow any novel on our website. We promise you that we'll bring you the latest, hottest novel everyday and FREE.
LightNovelFree.com is a most smartest website for reading novel online, it can automatic resize images to fit your pc screen, even on your mobile. Experience now by using your smartphone and access to LightNovelFree.com
RECENTLY UPDATED NOVEL

Global Lord: 100% Drop Rate
Global Lord: 100% Drop Rate Chapter 1717 Killing The Void Emperor! (1) View : 1,041,287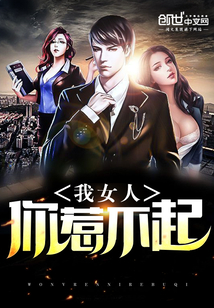