De Re Metallica Part 41
You’re reading novel De Re Metallica Part 41 online at LightNovelFree.com. Please use the follow button to get notification about the latest chapter next time when you visit LightNovelFree.com. Use F11 button to read novel in full-screen(PC only). Drop by anytime you want to read free – fast – latest novel. It’s great if you could leave a comment, share your opinion about the new chapters, new novel with others on the internet. We’ll do our best to bring you the finest, latest novel everyday. Enjoy!
_Naevius_.--I should have thought it a crystal. _Bermannus_.--A fourth is a yellow colour, a fifth ash colour, a sixth blackish. Some are violet, some green, others gold-coloured. _Anton_.--What is the use of _fluores_? _Bermannus_.--They are wont to be made use of when metals are smelted, as they cause the material in the fire to be much more fluid, exactly like a kind of stone which we said is made from pyrites (matte); it is, indeed, made not far from here, at Breitenbrunn, which is near Schwarzenberg. Moreover, from _fluores_ they can make colours which artists use."
[16] _Stannum_. (_Interpretatio_,--_werck_, modern _werk_). This term has been rendered throughout as "silver-lead" or "silver-lead alloy." It was the argentiferous lead suitable for cupellation. Agricola, in using it in this sense, was no doubt following his interpretation of its use by Pliny. Further remarks upon this subject will be found in note 33, p.
473.
[17] _Expirare_,--to exhale or blow out.
[18] _Rhetos_. The ancient Rhaetia comprised not only the greater part of Tyrol, but also parts of Switzerland and Lombardy. The mining section was, however, in Tyrol.
[19] _Noric.u.m_ was a region south of the Danube, embracing not only modern Styria, but also parts of Austria, Salzberg, and Carinthia.
[20] One _drachma_ of gold to a _centumpondium_ would be (if we a.s.sume these were Roman weights) 3 ozs. 1 dwt. Troy per short ton. One-half _uncia_ of silver would be 12 ozs. 3 dwts. per short ton.
[21] For discussion of these fluxes see note page 232.
[22] _Carni_. Probably the people of modern Austrian Carniola, which lies south of Styria and west of Croatia.
[23] HISTORICAL NOTE ON SMELTING LEAD AND SILVER.--The history of lead and silver smelting is by no means a sequent array of exact facts. With one possible exception, lead does not appear upon the historical horizon until long after silver, and yet their metallurgy is so inextricably mixed that neither can be considered wholly by itself. As silver does not occur native in any such quant.i.ties as would have supplied the amounts possessed by the Ancients, we must, therefore, a.s.sume its reduction by either (1) intricate chemical processes, (2) amalgamation, (3) reduction with copper, (4) reduction with lead. It is impossible to conceive of the first with the ancient knowledge of chemistry; the second (see note 12, p. 297) does not appear to have been known until after Roman times; in any event, quicksilver appears only at about 400 B.C. The third was impossible, as the parting of silver from copper without lead involves metallurgy only possible during the last century.
Therefore, one is driven to the conclusion that the fourth case obtained, and that the lead must have been known practically contemporaneously with silver. There is a leaden figure exhibited in the British Museum among the articles recovered from the Temple of Osiris at Abydos, and considered to be of the Archaic period--prior to 3800 B.C.
The earliest known Egyptian silver appears to be a necklace of beads, supposed to be of the XII. Dynasty (2400 B.C.), which is described in the 17th Memoir, Egyptian Exploration Fund (London, 1898, p. 22). With this exception of the above-mentioned lead specimen, silver articles antedate positive evidence of lead by nearly a millennium, and if we a.s.sume lead as a necessary factor in silver production, we must conclude it was known long prior to any direct (except the above solitary possibility) evidence of lead itself. Further, if we are to conclude its necessary a.s.sociation with silver, we must a.s.sume a knowledge of cupellation for the parting of the two metals. Lead is mentioned in 1500 B.C. among the spoil captured by Thotmes III. Leaden objects have frequently been found in Egyptian tombs as early as Rameses III. (1200 B.C.). The statement is made by Pulsifer (Notes for a History of Lead, New York 1888, p. 146) that Egyptian pottery was glazed with lead. We have been unable to find any confirmation of this. It may be noted, incidentally, that lead is not included in the metals of the "Tribute of Yu" in the Shoo King (The Chinese Cla.s.sics, 2500 B.C.?), although silver is so included.
After 1200 or 1300 B.C. evidences of the use of lead become frequent.
Moses (Numbers x.x.xI, 22-23) directs the Israelites with regard to their plunder from the Midianites (1300 B.C.): "Only the gold and the silver, the bra.s.s [_sic_], the iron, the tin, and the lead. Everything that may abide the fire, ye shall make it go through the fire, and it shall be clean; nevertheless, it shall be purified with the water of separation, and all that abideth not the fire ye shall make go through the water."
Numerous other references occur in the Scriptures (Psalms XII, 6; Proverbs XVII, 3; XXV, 4; etc.), one of the most pointed from a metallurgical point of view being that of Jeremiah (600 B.C.), who says (VI, 29-30): "The bellows are burned, the lead is consumed of the fire; the founder melteth in vain; for the wicked are not plucked away.
Reprobate silver shall men call them because the Lord hath rejected them." From the number of his metaphors in metallurgical terms we may well conclude that Jeremiah was of considerable metallurgical experience, which may account for his critical tenor of mind. These Biblical references all point to a knowledge of separating silver and lead. Homer mentions lead (Iliad XXIV, 109), and it has been found in the remains of ancient Troy and Mycenae (H. Schliemann, "Troy and its Remains," London, 1875, and "Mycenae," New York, 1877). Both Herodotus (I, 186) and Diodorus (II, 1) speak of the lead used to fix iron clamps in the stone bridge of Nitocris (600 B.C.) at Babylon.
Our best evidence of ancient lead-silver metallurgy is the result of the studies at Mt. Laurion by Edouard Ardaillon (_Mines du Laurion dans l'Antiquite_, Paris, 1897). Here the very extensive old workings and the slag heaps testify to the greatest activity. The re-opening of the mines in recent years by a French Company has well demonstrated their technical character, and the frequent mention in Greek History easily determines their date. These deposits of argentiferous galena were extensively worked before 500 B.C. and while the evidence of concentration methods is ample, there is but little remaining of the ancient smelters. Enough, however, remains to demonstrate that the galena was smelted in small furnaces at low heat, with forced draught, and that it was subsequently cupelled. In order to reduce the sulphides the ancient smelters apparently depended upon partial roasting in the furnace at a preliminary period in reduction, or else upon the ferruginous character of the ore, or upon both. See notes p. 27 and p.
265. Theognis (6th century B.C.) and Hippocrates (5th century B.C.) are frequently referred to as mentioning the refining of gold with lead; an inspection of the pa.s.sages fails to corroborate the importance which has been laid upon them. Among literary evidences upon lead metallurgy of later date, Theophrastus (300 B.C.) describes the making of white-lead with lead plates and vinegar. Diodorus Siculus (1st century B.C.), in his well-known quotation from Agatharchides (2nd century B.C.) with regard to gold mining and treatment in Egypt, describes the refining of gold with lead. (See note 8, p. 279.) Strabo (63 B.C.-24 A.D.) says (III, 2, 8): "The furnaces for silver are constructed lofty in order that the vapour, which is dense and pestilent, may be raised and carried off." And again (III, 2, 10), in quoting from Polybius (204-125 B.C.): "Polybius, speaking of the silver mines of New Carthage, tells us that they are extremely large, distant from the city about 20 stadia, and occupy a circuit of 400 stadia; that there are 40,000 men regularly engaged in them, and that they yield daily to the Roman people (a revenue of) 25,000 drachmae. The rest of the process I pa.s.s over, as it is too long; but as for the silver ore collected, he tells us that it is broken up and sifted through sieves over water; that what remains is to be again broken, and the water having been strained off it is to be sifted and broken a third time. The dregs which remain after the fifth time are to be melted, and the lead being poured off, the silver is obtained pure. These silver mines still exist; however, they are no longer the property of the State, neither these nor those elsewhere, but are possessed by private individuals. The gold mines, on the contrary, nearly all belong to the State. Both at Castlon and other places there are singular lead mines worked. They contain a small proportion of silver, but not sufficient to pay for the expense of refining"
(Hamilton's Trans.). Dioscorides (1st century A.D.), among his medicines, describes several varieties of litharge, their origin, and the manner of making white-lead (see on pp. 465, 440), but he gives no very tangible information on lead smelting. Pliny, at the same period in speaking of silver, (x.x.xIII, 31), says: "After this we speak of silver, the next folly. Silver is only found in shafts, there being no indications like s.h.i.+ning particles as in the case of gold. This earth is sometimes red, sometimes of an ashy colour. It is impossible to melt it except with lead ore (_vena plumbi_), called _galena_, which is generally found next to silver veins. And this the same agency of fire separates part into lead, which floats on the silver like oil on water."
(We have transferred lead and silver in this last sentence, otherwise it means nothing.) Also (x.x.xIV, 47) he says: "There are two different sources of lead, it being smelted from its own ore, whence it comes without the admixture of any other substance, or else from an ore which contains it in common with silver. The metal, which flows liquid at the first melting in the furnace, is called _stannum_ that at the second melting is silver; that which remains in the furnace is _galena_, which is added to a third part of the ore. This being again melted, produces lead with a deduction of two-ninths." We have, despite some grammatical objections, rendered this pa.s.sage quite differently from other translators, none of whom have apparently had any knowledge of metallurgy; and we will not, therefore, take the several pages of s.p.a.ce necessary to refute their extraordinary and unnecessary hypotheses. From a metallurgical point of view, two facts must be kept in mind,--first, that _galena_ in this instance was the same substance as _molybdaena_, and they were both either a variety of litharge or of lead carbonates; second, that the _stannum_ of the Ancients was silver-lead alloy.
Therefore, the metallurgy of this paragraph becomes a simple melting of an argentiferous lead ore, its subsequent cupellation, with a return of the litharge to the furnace. Pliny goes into considerable detail as to varieties of litharge, for further notes upon which see p. 466. The Romans were most active lead-silver miners, not only in Spain, but also in Britain. There are scores of lead pigs of the Roman era in various English museums, many marked "_ex argent_." Bruce (The Roman Wall, London, 1852, p. 432) describes some Roman lead furnaces in c.u.mberland where the draught was secured by driving a tapering tunnel into the hills. The Roman lead slag ran high in metal, and formed a basis for quite an industry in England in the early 18th century (Hunt, British Mining, London, 1887, p. 26, etc.). There is nothing in mediaeval literature which carries us further with lead metallurgy than the knowledge displayed by Pliny, until we arrive at Agricola's period. The history of cupellation is specially dealt with in note on p. 465.
[25] _Cadmia_. In the German Translation this is given as _kobelt_. It would be of uncertain character, but no doubt partially furnace calamine. (See note on p. 112.)
[26] _Pompholyx_. (_Interpretatio_ gives the German as _Weisser hutten rauch als ober dem garherde und ober dem kupfer ofen_). This was the impure protoxide of zinc deposited in the furnace outlets, and is modern "tutty." The ancient products, no doubt, contained a.r.s.enical oxides as well. It was well known to the Ancients, and used extensively for medicinal purposes, they dividing it into two species--_pompholyx_ and _spodos_. The first adequate description is by Dioscorides (V, 46): "_Pompholyx_ differs from _spodos_ in species, not in genus. For _spodos_ is blacker, and is often heavier, full of straws and hairs, like the refuse that is swept from the floors of copper smelters. But _pompholyx_ is fatty, unctuous, white and light enough to fly in the air. Of this there are two kinds--the one inclines to sky blue and is unctuous; the other is exceedingly white, and is extremely light. White _pompholyx_ is made every time that the artificer, in the preparation and perfecting of copper (bra.s.s?) sprinkles powdered _cadmia_ upon it to make it more perfect, for the soot which rises being very fine becomes _pompholyx_. Other _pompholyx_ is made, not only in working copper (bra.s.s?), but is also made from _cadmia_ by continually blowing with bellows. The manner of doing it is as follows:--The furnace is constructed in a two-storied building, and there is a medium-sized aperture opening to the upper chamber; the building wall nearest the furnace is pierced with a small opening to admit the nozzle of the bellows. The building must have a fair-sized door for the artificer to pa.s.s in and out. Another small building must adjoin this, in which are the bellows and the man who works them. Then the charcoal in the furnace is lighted, and the artificer continually throws broken bits of _cadmia_ from the place above the furnace, whilst his a.s.sistant, who is below, throws in charcoals, until all of the _cadmia_ inside is consumed. By this means the finest and lightest part of the stuff flies up with the smoke to the upper chamber, and adheres to the walls of the roof. The substance which is thus formed has at first the appearance of bubbles on water, afterward increasing in size, it looks like skeins of wool. The heaviest parts settle in the bottom, while some fall over and around the furnaces, and some lie on the floor of the building. This latter part is considered inferior, as it contains a lot of earth and becomes full of dirt."
Pliny (x.x.xIV, 33) appears somewhat confused as to the difference between the two species: "That which is called _pompholyx_ and _spodos_ is found in the copper-smelting furnaces, the difference between them being that _pompholyx_ is separated by was.h.i.+ng, while _spodos_ is not washed. Some have called that which is white and very light _pompholyx_, and it is the soot of copper and _cadmia_; whereas _spodos_ is darker and heavier.
It is sc.r.a.ped from the walls of the furnace, and is mixed with particles of metal, and sometimes with charcoal." (x.x.xIV, 34.) "The Cyprian _spodos_ is the best. It is formed by fusing _cadmia_ with copper ore.
This being the lightest part of the metal, it flies up in the fumes from the furnace, and adheres to the roof, being distinguished from the soot by its whiteness. That which is less white is immature from the furnace, and it is this which some call '_pompholyx_.'" Agricola (_De Natura Fossilium_, p. 350) traverses much the same ground as the authors previously quoted, and especially recommends the _pompholyx_ produced when making bra.s.s by melting alternate layers of copper and calamine (_cadmia fossilis_).
[27] _Oleo, ex fece vini sicca confecto_. This oil, made from argol, is probably the same substance mentioned a few lines further on as "wine,"
distilled by heating argol in a retort. Still further on, salt made from argol is mentioned. It must be borne in mind that this argol was crude tartrates from wine vats, and probably contained a good deal of organic matter. Heating argol sufficiently would form potash, but that the distillation product could be anything effective it is difficult to see.
[28] _Aqua valens_. No doubt mainly nitric acid, the preparation of which is explained at length in Book X, p. 439.
[29] _Quod c.u.m ignis consumit non modo una c.u.m eo, quae ipsius stibii vis est, aliqua auri particula, sed etiam argenti, si c.u.m auro fuerit permistum, consumitur._ The meaning is by no means clear. On p. 451 is set out the old method of parting silver from gold with antimony sulphide, of which this may be a variation. The silver combines with sulphur, and the reduced antimony forms an alloy with the gold. The added iron and copper would also combine with the sulphur from the antimony sulphide, and no doubt a.s.sist by increasing the amount of free collecting agent and by increasing the volume of the matte. (See note 17, p. 451.)
[30] There follow eight different methods of treating crude bullion or rich concentrates. In a general way three methods are involved,--1st, reduction with lead or antimony, and cupellation; 2nd, reduction with silver, and separation with nitric acid; 3rd, reduction with lead and silver, followed by cupellation and parting with nitric acid. The use of sulphur or antimony sulphide would tend to part out a certain amount of silver, and thus obtain fairly pure bullion upon cupellation. But the introduction of copper could only result deleteriously, except that it is usually accompanied by sulphur in some form, and would thus probably pa.s.s off harmlessly as a matte carrying silver. (See note 33 below.)
[31] It is not very clear where this lead comes from. Should it be antimony? The German translation gives this as "silver."
[32] These powders are described in Book VII., p. 236. It is difficult to say which the second really is. There are numbers of such recipes in the _Probierbuchlein_ (see Appendix B), with which a portion of these are identical.
[33] A variety of methods are involved in this paragraph: 1st, crude gold ore is smelted direct; 2nd, gold concentrates are smelted in a lead bath with some addition of iron--which would simply matte off--the lead bullion being cupelled; 3rd, roasted and unroasted pyrites and _cadmia_ (probably blende, cobalt, a.r.s.enic, etc.) are melted into a matte; this matte is repeatedly roasted, and then re-melted in a lead bath; 4th, if the material "flies out of the furnace" it is briquetted with iron ore and lime, and the briquettes smelted with copper matte. Three products result: (_a_) slag; (_b_) matte; (_c_) copper-gold-silver alloy. The matte is roasted, re-smelted with lead, and no doubt a b.u.t.ton obtained, and further matte. The process from this point is not clear. It appears that the copper bullion is melted with lead, and normally this product would be taken to the liquation furnace, but from the text it would appear that the lead-copper bullion was melted again with iron ore and pyrites, in which case some of the copper would be turned into the matte, and the lead alloy would be richer in gold and silver.
HISTORICAL NOTE ON GOLD.--There is ample evidence of gold being used for ornamental purposes prior to any human record. The occurrence of large quant.i.ties of gold in native form, and the possibility of working it cold, did not necessitate any particular metallurgical ingenuity. The earliest indications of metallurgical work are, of course, among the Egyptians, the method of was.h.i.+ng being figured as early as the monuments of the IV Dynasty (prior to 3800 B.C.). There are in the British Museum two stelae of the XII Dynasty (2400 B.C.) (144 Bay 1 and 145 Bay 6) relating to officers who had to do with gold mining in Nubia, and upon one there are references to working what appears to be ore. If this be true, it is the earliest reference to this subject. The Papyrus map (1500 B.C.) of a gold mine, in the Turin Museum (see note 16, p. 129), probably refers to a quartz mine. Of literary evidences there is frequent mention of refining gold and pa.s.sing it through the fire in the Books of Moses, arts no doubt learned from the Egyptians. As to working gold, ore as distinguished from alluvial, we have nothing very tangible, unless it be the stelae above, until the description of Egyptian gold mining by Agatharchides (see note 8, p. 279). This geographer, of about the 2nd century B.C., describes very clearly indeed the mining, crus.h.i.+ng, and concentration of ore and the refining of the concentrates in crucibles with lead, salt, and barley bran. We may mention in pa.s.sing that Theognis (6th Century B.C.) is often quoted as mentioning the refining of gold with lead, but we do not believe that the pa.s.sage in question (1101): "But having been put to the test and being rubbed beside (or against) lead as being refined gold, you will be fair," etc.; or much the same statement again (418) will stand much metallurgical interpretation. In any event, the myriads of metaphorical references to fining and purity of gold in the earliest shreds of literature do not carry us much further than do those of Shakespeare or Milton. Vitruvius and Pliny mention the recovery or refining of gold with mercury (see note 12, p. 297 on Amalgamation); and it appears to us that gold was parted from silver by cementation with salt prior to the Christian era.
We first find mention of parting with sulphur in the 12th century, with nitric acid prior to the 14th century, by antimony sulphide prior to the 15th century, and by cementation with nitre by Agricola. (See historical note on parting gold and silver, p. 458.) The first mention of parting gold from copper occurs in the early 16th century (see note 24, p. 462).
The first comprehensive description of gold metallurgy in all its branches is in _De Re Metallica_.
[34] _Rudis_ silver comprised all fairly pure silver ores, such as silver sulphides, chlorides, a.r.s.enides, etc. This is more fully discussed in note 6, p. 108.
[35] _Evolent_,--volatilize?
[36] _Lapidis plumbarii facile liquescentis_. The German Translation gives _glantz_, _i.e._, Galena, and the _Interpretatio_ also gives _glantz_ for _lapis plumbarius_. We are, however, uncertain whether this "easily melting" material is galena or some other lead ore.
[37] _Molybdaena_ is usually hearth-lead in _De Re Metallica_, but the German translation in this instance uses _pleyertz_, lead ore. From the context it would not appear to mean hearth-lead--saturated bottoms of cupellation furnaces--for such material would not contain appreciable silver. Agricola does confuse what are obviously lead carbonates with his other _molybdaena_ (see note 37, p. 476).
[38] The term _cadmia_ is used in this paragraph without the usual definition. Whether it was _cadmia fornacis_ (furnace accretions) or _cadmia metallica_ (cobalt-a.r.s.enic-blende mixture) is uncertain. We believe it to be the former.
[39] _Ramentum si lotura ex argento rudi_. This expression is generally used by the author to indicate concentrates, but it is possible that in this sentence it means the tailings after was.h.i.+ng rich silver minerals, because the treatment of the _rudis_ silver has been already discussed above.
[40] _Ustum_. This might be rendered "burnt." In any event, it seems that the material is sintered.
[41] _Aes purum sive proprius ei color insederit, sive chrysocolla vel caeruleo fuerit tinctum, et rude plumbei coloris, aut fusci, aut nigri._ There are six copper minerals mentioned in this sentence, and from our study of Agricola's _De Natura Fossilium_ we hazard the following:--_Proprius ei color insederit_,--"its own colour,"--probably cuprite or "ruby copper." _Tinctum chrysocolla_--partly the modern mineral of that name and partly malachite. _Tinctum caeruleo_, partly azurite and partly other blue copper minerals. _Rude plumbei coloris_,--"lead coloured,"--was certainly chalcocite (copper glance).
We are uncertain of _fusci aut nigri_, but they were probably alteration products. For further discussion see note on p. 109.
[42] HISTORICAL NOTE ON COPPER SMELTING.--The discoverer of the reduction of copper by fusion, and his method, like the discoverer of tin and iron, will never be known, because he lived long before humanity began to make records of its discoveries and doings. Moreover, as different races pa.s.sed independently and at different times through the so-called "Bronze Age," there may have been several independent discoverers. Upon the metallurgy of pre-historic man we have some evidence in the many "founders' h.o.a.rds" or "smelters' h.o.a.rds" of the Bronze Age which have been found, and they indicate a simple shallow pit in the ground into which the ore was placed, underlaid with charcoal.
Rude round copper cakes eight to ten inches in diameter resulted from the cooling of the metal in the bottom of the pit. a.n.a.lyses of such Bronze Age copper by Professor Gowland and others show a small percentage of sulphur, and this is possible only by smelting oxidized ores. Copper objects appear in the pre-historic remains in Egypt, are common throughout the first three dynasties, and bronze articles have been found as early as the IV Dynasty (from 3800 to 4700 B.C., according to the authority adopted). The question of the origin of this bronze, whether from ores containing copper and tin or by alloying the two metals, is one of wide difference of opinion, and we further discuss the question in note 53, p. 411, under Tin. It is also interesting to note that the crucible is the emblem of copper in the hieroglyphics. The earliest source of Egyptian copper was probably the Sinai Peninsula, where there are reliefs as early as Seneferu (about 3700 B.C.), indicating that he worked the copper mines. Various other evidences exist of active copper mining prior to 2500 B.C. (Petrie, Researches in Sinai, London, 1906, p. 51, etc.). The finding of crucibles here would indicate some form of refining. Our knowledge of Egyptian copper metallurgy is limited to deductions from their products, to a few pictures of crude furnaces and bellows, and to the minor remains on the Sinai Peninsula; none of the pictures were, so far as we are aware, prior to 2300 B.C., but they indicate a considerable advance over the crude hearth, for they depict small furnaces with forced draught--first a blow-pipe, and in the XVIII Dynasty (about 1500 B.C.) the bellows appear. Many copper articles have been found scattered over the Eastern Mediterranean and Asia Minor of pre-Mycenaean Age, some probably as early as 3000 B.C. This metal is mentioned in the "Tribute of Yu" in the Shoo King (2500 B.C.?); but even less is known of early Chinese metallurgy than of the Egyptian. The remains of Mycenaean, Phoenician, Babylonian, and a.s.syrian civilizations, stretching over the period from 1800 to 500 B.C., have yielded endless copper and bronze objects, the former of considerable purity, and the latter a fairly constant proportion of from 10% to 14% tin. The copper supply of the pre-Roman world seems to have come largely, first from Sinai, and later from Cyprus, and from the latter comes our word copper, by way of the Romans shortening _aes cyprium_ (Cyprian copper) to _cuprum_. Research in this island shows that it produced copper from 3000 B.C., and largely because of its copper it pa.s.sed successively under the domination of the Egyptians, a.s.syrians, Phoenicians, Greeks, Persians, and Romans. The bronze objects found in Cyprus show 2% to 10% of tin, although tin does not, so far as modern research goes, occur on that island. There can be no doubt that the Greeks obtained their metallurgy from the Egyptians, either direct or second-hand--possibly through Mycenae or Phoenicia.
Their metallurgical G.o.ds and the tradition of Cadmus indicate this much.
By way of literary evidences, the following lines from Homer (Iliad, XVIII.) have interest as being the first preserved description in any language of a metallurgical work. Hephaestus was much interrupted by Thetis, who came to secure a s.h.i.+eld for Achilles, and whose general conversation we therefore largely omit. We adopt Pope's translation:--
There the lame architect the G.o.ddess found Obscure in smoke, his forges flaming round, While bathed in sweat from fire to fire he flew; And puffing loud the roaring bellows blew.
In moulds prepared, the glowing ore (metal?) he pours.
"Vouchsafe, oh Thetis! at our board to share The genial rites and hospitable fare; While I the labours of the forge forego, And bid the roaring bellows cease to blow."
Then from his anvil the lame artist rose; Wide with distorted legs oblique he goes, And stills the bellows, and (in order laid) Locks in their chests his instruments of trade; Then with a sponge, the sooty workman dress'd His brawny arms embrown'd and hairy breast.
Thus having said, the father of the fires To the black labours of his forge retires.
Soon as he bade them blow the bellows turn'd Their iron mouths; and where the furnace burn'd Resounding breathed: at once the blast expires, And twenty forges catch at once the fires; Just as the G.o.d directs, now loud, now low, They raise a tempest, or they gently blow; In hissing flames huge silver bars are roll'd, And stubborn bra.s.s (copper?) and tin, and solid gold; Before, deep fixed, the eternal anvils stand.
The ponderous hammer loads his better hand; His left with tongs turns the vex'd metal round.
And thick, strong strokes, the doubling vaults rebound Then first he formed the immense and solid s.h.i.+eld;
Even if we place the siege of Troy at any of the various dates from 1350 to 1100 B.C., it does not follow that the epic received its final form for many centuries later, probably 900-800 B.C.; and the experience of the race in metallurgy at a much later period than Troy may have been drawn upon to fill in details. It is possible to fill a volume with indirect allusion to metallurgical facts and to the origins of the art, from Greek mythology, from Greek poetry, from the works of the grammarians, and from the Bible. But they are of no more technical value than the metaphors from our own tongue. Greek literature in general is singularly lacking in metallurgical description of technical value, and it is not until Dioscorides (1st Century A.D.) that anything of much importance can be adduced. Aristotle, however, does make an interesting reference to what may be bra.s.s (see note on p. 410), and there can be no doubt that if we had the lost work of Aristotle's successor, Theophrastus (372-288 B.C.), on metals we should be in possession of the first adequate work on metallurgy. As it is, we find the green and blue copper minerals from Cyprus mentioned in his "Stones." And this is the first mention of any particular copper ore. He also mentions (XIX.) pyrites "which melt," but whether it was a copper variety cannot be determined. Theophrastus further describes the making of verdigris (see note 4, p. 440). From Dioscorides we get a good deal of light on copper treatment, but as his objective was to describe medicinal preparations, the information is very indirect. He states (V, 100) that "pyrites is a stone from which copper is made." He mentions _chalcitis_ (copper sulphide, see note on, p. 573); while his _misy_, _sory_, _melanteria_, _caeruleum_, and _chrysocolla_ were all oxidation copper or iron minerals. (See notes on p. 573.) In giving a method of securing _pompholyx_ (zinc oxide), "the soot flies up when the copper refiners sprinkle powdered _cadmia_ over the molten metal" (see note 26, p. 394); he indirectly gives us the first definite indication of making bra.s.s, and further gives some details as to the furnaces there employed, which embraced bellows and dust chambers. In describing the making of flowers of copper (see note 26, p. 538) he states that in refining copper, when the "molten metal flows through its tube into a receptacle, the workmen pour cold water on it, the copper spits and throws off the flowers." He gives the first description of vitriol (see note 11, p. 572), and describes the pieces as "shaped like dice which stick together in bunches like grapes." Altogether, from Dioscorides we learn for the first time of copper made from sulphide ores, and of the recovery of zinc oxides from furnace fumes; and he gives us the first certain description of making bra.s.s, and finally the first notice of blue vitriol.
The next author we have who gives any technical detail of copper work is Pliny (23-79 A.D.), and while his statements carry us a little further than Dioscorides, they are not as complete as the same number of words could have afforded had he ever had practical contact with the subject, and one is driven to the conclusion that he was not himself much of a metallurgist. Pliny indicates that copper ores were obtained from veins by underground mining. He gives the same minerals as Dioscorides, but is a good deal confused over _chrysocolla_ and _chalcitis_. He gives no description of the shapes of furnaces, but frequently mentions the bellows, and speaks of the _cadmia_ and _pompholyx_ which adhered to the walls and arches of the furnaces. He has nothing to say as to whether fluxes are used or not. As to fuel, he says (x.x.xIII, 30) that "for smelting copper and iron pine wood is the best." The following (x.x.xIV, 20) is of the greatest interest on the subject:--"Cyprian copper is known as _coronarium_ and _regulare_; both are ductile.... In other mines are made that known as _regulare_ and _caldarium_. These differ, because the _caldarium_ is only melted, and is brittle to the hammer; whereas the _regulare_ is malleable or ductile. All Cyprian copper is this latter kind. But in other mines with care the difference can be eliminated from _caldarium_, the impurities being carefully purged away by smelting with fire, it is made into _regulare_. Among the remaining kinds of copper the best is that of Campania, which is most esteemed for vessels and utensils. This kind is made in several ways. At Capua it is melted with wood, not with charcoal, after which it is sprinkled with water and washed through an oak sieve. After it is melted a number of times Spanish _plumb.u.m argentum_ (probably pewter) is added to it in proportion of ten pounds of the lead to one hundred pounds of copper, and thereby it is made pliable and a.s.sumes that pleasing colour which in other kinds of copper is effected by oil and the sun. In many parts of the Italian provinces they make a similar kind of metal; but there they add eight pounds of lead, and it is re-melted over charcoal because of the scarcity of wood. Very different is the method carried on in Gaul, particularly where the ore is smelted between red hot stones, for this burns the metal and renders it black and brittle. Moreover, it is re-melted only a single time, whereas the oftener this operation is repeated the better the quality becomes. It is well to remark that all copper fuses best when the weather is intensely cold." The red hot stones in Gaul were probably as much figments of imagination as was the a.s.sumption of one commentator that they were a reverberatory furnace.
Apart from the above, Pliny says nothing very direct on refining copper.
It is obvious that more than one melting was practised, but that anything was known of the nature of oxidation by a blast and reduction by poling is uncertain. We produce the three following statements in connection with some bye-products used for medicinal purposes, which at least indicate operations subsequent to the original melting. As to whether they represent this species of refining or not, we leave it to the metallurgical profession (x.x.xIV, 24):--"The flowers of copper are used in medicine; they are made by fusing copper and moving it to another furnace, where the rapid blast separates it into a thousand particles, which are called flowers. These scales are also made when the copper cakes are cooled in water (x.x.xIV, 35). _Smega_ is prepared in the copper works; when the metal is melted and thoroughly smelted charcoal is added to it and gradually kindled; after this, being blown upon by a powerful bellows, it spits out, as it were, copper chaff (x.x.xIV, 37).
There is another product of these works easily distinguished from _smega_, which the Greeks call _diphrygum_. This substance has three different origins.... A third way of making it is from the residues which fall to the bottom in copper furnaces. The difference between the different substances (in the furnace) is that the copper itself flows into a receiver; the slag makes its escape from the furnace; the flowers float on the top (of the copper?), and the _diphrygum_ remains behind.
De Re Metallica Part 41
You're reading novel De Re Metallica Part 41 online at LightNovelFree.com. You can use the follow function to bookmark your favorite novel ( Only for registered users ). If you find any errors ( broken links, can't load photos, etc.. ), Please let us know so we can fix it as soon as possible. And when you start a conversation or debate about a certain topic with other people, please do not offend them just because you don't like their opinions.
De Re Metallica Part 41 summary
You're reading De Re Metallica Part 41. This novel has been translated by Updating. Author: Georgius Agricola already has 690 views.
It's great if you read and follow any novel on our website. We promise you that we'll bring you the latest, hottest novel everyday and FREE.
LightNovelFree.com is a most smartest website for reading novel online, it can automatic resize images to fit your pc screen, even on your mobile. Experience now by using your smartphone and access to LightNovelFree.com
- Related chapter:
- De Re Metallica Part 40
- De Re Metallica Part 42
RECENTLY UPDATED NOVEL

The King of Hell's Genius Pampered Wife
The King of Hell's Genius Pampered Wife Chapter 1928: Accepted! View : 2,732,510
A Demon Lord's Tale: Dungeons, Monster Girls, and Heartwarming Bliss
A Demon Lord's Tale: Dungeons, Monster Girls, and Heartwarming Bliss Chapter 574 View : 1,365,615
Eternal Life Begins with Taking a Wife
Eternal Life Begins with Taking a Wife Chapter 1153: Mysterious Exotic Beast (1) View : 410,703
Cultivation: Start From Simplifying Martial Arts Techniques
Cultivation: Start From Simplifying Martial Arts Techniques Chapter 1092: Chapter 1048 Stepping Stone View : 621,173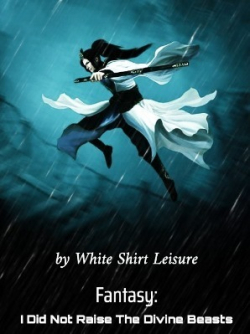
Fantasy: I Did Not Raise The Divine Beasts
Fantasy: I Did Not Raise The Divine Beasts Chapter 1111: These Are All Trash (1) View : 387,915