De Re Metallica Part 42
You’re reading novel De Re Metallica Part 42 online at LightNovelFree.com. Please use the follow button to get notification about the latest chapter next time when you visit LightNovelFree.com. Use F11 button to read novel in full-screen(PC only). Drop by anytime you want to read free – fast – latest novel. It’s great if you could leave a comment, share your opinion about the new chapters, new novel with others on the internet. We’ll do our best to bring you the finest, latest novel everyday. Enjoy!
Some say that in the furnace there are certain ma.s.ses of stone which, being smelted, become soldered together, and that the copper fuses around it, the ma.s.s not becoming liquid unless it is transferred to another furnace. It thus forms a sort of knot, as it were, in the metal."
Pliny is a good deal confused over the copper alloys, failing to recognise _aurichalc.u.m_ as the same product as that made by mixing _cadmia_ and molten copper. Further, there is always the difficulty in translation arising from the fact that the Latin _aes_ was indiscriminately copper, bra.s.s, and bronze. He does not, except in one instance (x.x.xIV., 2), directly describe the mixture of _cadmia_ and copper. "Next to Livian (copper) this kind (_corduban_, from Spain) most readily absorbs _cadmia_, and becomes almost as excellent as _aurichalc.u.m_ for making _sesterces_." As to bronze, there is no very definite statement; but the _argentatium_ given in the quotation above from x.x.xIV, 20, is stated in x.x.xIV, 48, to be a mixture of tin and lead.
The Romans carried on most extensive copper mining in various parts of their empire; these activities extended from Egypt through Cyprus, Central Europe, the Spanish Peninsula, and Britain. The activity of such works is abundantly evidenced in the mines, but very little remains upon the surface to indicate the equipment; thus, while mining methods are clear enough, the metallurgy receives little help from these sources. At Rio Tinto there still remain enormous slag heaps from the Romans, and the Phoenician miners before them. Professor W. A. Carlyle informs us that the ore worked must have been almost exclusively sulphides, as only negligible quant.i.ties of carbonates exist in the deposits; they probably mixed basic and siliceous ores. There is some evidence of roasting, and the slags run from .2 to .6%. They must have run down mattes, but as to how they ultimately arrived at metallic copper there is no evidence to show.
The special processes for separating other metals from copper by liquation and matting, or of refining by poling, etc., are none of them clearly indicated in records or remains until we reach the 12th century.
Here we find very adequate descriptions of copper smelting and refining by the Monk Theophilus (see Appendix B). We reproduce two paragraphs of interest from Hendrie's excellent translation (p. 305 and 313): "Copper is engendered in the earth. When a vein of which is found, it is acquired with the greatest labour by digging and breaking. It is a stone of a green colour and most hard, and naturally mixed with lead. This stone, dug up in abundance, is placed upon a pile and burned after the manner of chalk, nor does it change colour, but yet loses its hardness, so that it can be broken up. Then, being bruised small, it is placed in the furnace; coals and the bellows being applied, it is incessantly forged by day and night. This should be done carefully and with caution; that is, at first coals are placed in, then small pieces of stone are distributed over them, and again coals, and then stone anew, and it is thus arranged until it is sufficient for the size of the furnace. And when the stone has commenced to liquefy, the lead flows out through some small cavities, and the copper remains within. (313) Of the purification of copper. Take an iron dish of the size you wish, and line it inside and out with clay strongly beaten and mixed, and it is carefully dried.
Then place it before a forge upon the coals, so that when the bellows act upon it the wind may issue partly within and partly above it, and not below it. And very small coals being placed round it, place copper in it equally, and add over it a heap of coals. When, by blowing a long time, this has become melted, uncover it and cast immediately fine ashes of coals over it, and stir it with a thin and dry piece of wood as if mixing it, and you will directly see the burnt lead adhere to these ashes like a glue. Which being cast out again superpose coals, and blowing for a long time, as at first, again uncover it, and then do as you did before. You do this until at length, by cooking it, you can withdraw the lead entirely. Then pour it over the mould which you have prepared for this, and you will thus prove if it be pure. Hold it with pincers, glowing as it is, before it has become cold, and strike it with a large hammer strongly over the anvil, and if it be broken or split you must liquefy it anew as before."
The next writer of importance was Biringuccio, who was contemporaneous with Agricola, but whose book precedes _De Re Metallica_ by 15 years.
That author (III, 2) is the first to describe particularly the furnace used in Saxony and the roasting prior to smelting, and the first to mention fluxes in detail. He, however, describes nothing of matte smelting; in copper refining he gives the whole process of poling, but omits the pole. It is not until we reach _De Re Metallica_ that we find adequate descriptions of the copper minerals, roasting, matte smelting, liquation, and refining, with a wealth of detail which eliminates the necessity for a large amount of conjecture regarding technical methods of the time.
[43] _Cadmia metallica fossilis_ (see note on p. 112). This was undoubtedly the complex cobalt-a.r.s.enic-zinc minerals found in Saxony. In the German translation, however, this is given as _Kalmey_, calamine, which is unlikely from the a.s.sociation with pyrites.
[44] The Roman _modius_ (_modulus_?) held about 550 cubic inches, the English peck holding 535 cubic inches. Then, perhaps, his seven _moduli_ would be roughly, 1 bushel 3 pecks, and 18 vessels full would be about 31 bushels--say, roughly, 5,400 lbs. of ore.
[45] Exhausted liquation cakes (_panes aerei fathiscentes_). This is the copper sponge resulting from the first liquation of lead, and still contains a considerable amount of lead. The liquation process is discussed in great detail in Book XI.
[46] The method of this paragraph involves two main objectives--first, the gradual enrichment of matte to blister copper; and, second, the creation of large cakes of copper-lead-silver alloy of suitable size and ratio of metals for liquation. This latter process is described in detail in Book XI. The following groupings show the circuit of the various products, the "lbs." being Roman _librae_:--
CHARGE. PRODUCTS.
{ Crude ore 5,400 lbs. } Primary matte (1) 600 lbs.
{ Lead slags 3 cartloads } 1st { Schist 1 cartload } Silver-copper alloy (A) 50 "
{ Flux 20 lbs. } { Concentrates from } Slags (B) { slags & accretions Small quant.i.ty }
{ Primary matte (1) 1,800 lbs. } Secondary matte (2) 1,800 lbs.
{ Hearth-lead & litharge 1,200 " } { Lead ore 300 " } Silver-copper-lead 2nd { Rich hard cakes (A_{4}) 500 " } alloy (liquation { Liquated cakes 200 " } cakes) (A_{2}) 1,200 "
{ Slags (B) } { Concentrates from } Slags (B_{2}) { accretions }
{ Secondary matte (2) 1,800 lbs. } Tertiary matte (3) 1,300 lbs.
{ Hearth-lead & litharge 1,200 " } Silver-copper-lead { Lead ore 300 " } alloy (liquation 3rd { Rich hard cakes (A_{4}) 500 " } cakes) (A_{3}) 1,100 "
{ Slags (B_{2}) } Slags (B_{3}) { Concentrates from } { accretions }
{ Tertiary matte (3) 11 cartloads } Quaternary hard cakes { Poor hard cakes (A_{5}) 3 " } matte (4) 2,000 lbs.
4th { Slags (B_{3}) } Rich hard cakes of { Concentrates from } matte (A_{4}) 1,500 "
{ accretions }
{ Roasted quartz } Poor hard cakes of 5th { Matte (4) (three } matte (A_{5}) 1,500 lbs.
{ times roasted) 11 cartloads } Final cakes of matte (5)
6th Final matte three times roasted is smelted to blister copper.
The following would be a rough approximation of the value of the various products:--
(1.) Primary matte = 158 ounces troy per short ton.
(2.) Secondary matte = 85 " " "
(3.) Tertiary matte = 60 " " "
(4.) Quaternary matte = Indeterminate.
A. Copper-silver alloy = 388 ounces Troy per short ton.
A_{2} Copper-silver-lead alloy = 145 " " "
A_{3} " " " = 109 " " "
A_{4} Rich hard cakes = 97 " " "
A_{5} Poor hard cakes = Indeterminate.
Final blister copper = 12 ozs. Troy per short ton.
[47] This expression is usually used for hearth-lead, but in this case the author is apparently confining himself to lead ore, and apparently refers to lead carbonates. The German Translation gives _pleyschweiss_.
The pyrites mentioned in this paragraph may mean galena, as pyrites was to Agricola a sort of genera.
[48] (_Excoquitur_) ... "_si ver pyrites, prim e fornace, ut Goselariae videre licet, in catinum defluit liquor quidam candidus, argento inimicus et nocivus; id enim comburit: quo circa recrementis, quae supernatant, detractis effunditur: vel induratus conto uncinato extrahitur: eundem liquorem parietes fornacis exudant._" In the Glossary the following statement appears: "_Liquor candidus primo e fornace defluens c.u.m Goselariae excoquitur pyrites,--kobelt; quem parietes fornacis exudant,--conterfei._" In this latter statement Agricola apparently recognised that there were two different substances, _i.e._, that the substance found in the furnace walls--_conterfei_--was not the same substance as that which first flowed from the furnace--_kobelt_. We are at no difficulty in recognizing _conterfei_ as metallic zinc; it was long known by that term, and this accidental occurrence is repeatedly mentioned by other authors after Agricola. The substance which first flowed into the forehearth presents greater difficulties; it certainly was not zinc. In _De Natura Fossilium_ (p. 347), Agricola says that at Goslar the lead has a certain white slag floating upon it, the "colour derived from the pyrites (_pyriten argenteum_) from which it was produced." _Pyriten argenteum_ was either marcasite or mispickel, neither of which offers much suggestion; nor are we able to hazard an explanation of value.
HISTORICAL NOTE ON ZINC. The history of zinc metallurgy falls into two distinct lines--first, that of the metal, and second, that of zinc ore, for the latter was known and used to make bra.s.s by cementation with copper and to yield oxides by sublimation for medicinal purposes, nearly 2,000 years before the metal became generally known and used in Europe.
There is some reason to believe that metallic zinc was known to the Ancients, for bracelets made of it, found in the ruins of Cameros (prior to 500 B.C.), may have been of that age (Raoul Jagnaux, _Traite de Chimie Generale_, 1887, II, 385); and further, a pa.s.sage in Strabo (63 B.C.-24 A.D.) is of much interest. He states: (XIII, 1, 56) "There is found at Andeira a stone which when burnt becomes iron. It is then put into a furnace, together with some kind of earth, when it distils a mock silver (_pseudargyrum_), or with the addition of copper it becomes the compound called _orichalc.u.m_. There is found a mock silver near Tismolu also." (Hamilton's Trans., II, p. 381). About the Christian era the terms _orichalc.u.m_ or _aurichalc.u.m_ undoubtedly refer to bra.s.s, but whether these terms as used by earlier Greek writers do not refer to bronze only, is a matter of considerable doubt. Beyond these slight references we are without information until the 16th Century. If the metal was known to the Ancients it must have been locally, for by its greater adaptability to bra.s.s-making it would probably have supplanted the crude melting of copper with zinc minerals.
It appears that the metal may have been known in the Far East prior to such knowledge in Europe; metallic zinc was imported in considerable quant.i.ties from the East as early as the 16th and 17th centuries under such terms as _tuteneque_, _tuttanego_, _calaem_, and _spiauter_--the latter, of course, being the progenitor of our term spelter. The localities of Eastern production have never been adequately investigated. W. Hommel (Engineering and Mining Journal, June 15, 1912) gives a very satisfactory review of the Eastern literature upon the subject, and considers that the origin of manufacture was in India, although the most of the 16th and 17th Century product came from China.
The earliest certain description seems to be some recipes for manufacture quoted by Praphulla Chandra Ray (A History of Hindu Chemistry, London, 1902, p. 39) dating from the 11th to the 14th Centuries. There does not appear to be any satisfactory description of the Chinese method until that of Sir George Staunton (Journal Asiatique Paris, 1835, p. 141.) We may add that spelter was produced in India by crude distillation of calamine in clay pots in the early part of the 19th Century (Brooke, Jour. Asiatic Soc. of Bengal, vol. XIX, 1850, p.
212), and the remains of such smelting in Rajputana are supposed to be very ancient.
The discovery of zinc in Europe seems to have been quite independent of the East, but precisely where and when is clouded with much uncertainty.
The _marchasita aurea_ of Albertus Magnus has been called upon to serve as metallic zinc, but such belief requires a hypothesis based upon a great deal of a.s.sumption. Further, the statement is frequently made that zinc is mentioned in Basil Valentine's Triumphant Chariot of Antimony (the only one of the works attributed to this author which may date prior to the 17th Century), but we have been unable to find any such reference. The first certain mention of metallic zinc is generally accredited to Paracelsus (1493-1541), who states (_Liber Mineralium_ II.): "Moreover there is another metal generally unknown called _zinken_. It is of peculiar nature and origin; many other metals adulterate it. It can be melted, for it is generated from three fluid principles; it is not malleable. Its colour is different from other metals and does not resemble others in its growth. Its ultimate matter (_ultima materia_) is not to me yet fully known. It admits of no mixture and does not permit of the _fabricationes_ of other metals. It stands alone entirely to itself." We do not believe that this book was published until after Agricola's works. Agricola introduced the following statements into his revised edition of _Bermannus_ (p. 431), published in 1558: "It (a variety of pyrites) is almost the colour of galena, but of entirely different components. From it there is made gold and silver, and a great quant.i.ty is dug in Reichenstein, which is in Silesia, as was recently reported to me. Much more is found at Raurici, which they call _zinc.u.m_, which species differs from pyrites, for the latter contains more silver than gold, the former only gold or hardly any silver." In _De Natura Fossilium_ (p. 368): "For this _cadmia_ is put, in the same way as quicksilver, in a suitable vessel so that the heat of the fire will cause it to sublime, and from it is made a black or brown or grey body which the Alchemists call _cadmia sublimata_. This possesses corrosive properties to the highest degree. Cognate with this _cadmia_ and pyrites is a compound which the Noricans and Rhetians call _zinc.u.m_." We leave it to readers to decide how near this comes to metallic zinc; in any event, he apparently did not recognise his _conterfei_ from the furnaces as the same substance as the _zinc.u.m_ from Silesia. The first correlation of these substances was apparently by Lohneys, in 1617, who says (_Vom Bergwerk_, p. 83-4): "When the people in the smelting works are smelting, there is made under the furnace and in the cracks in the walls among the badly plastered stones, a metal which is called _zinc_ or _counterfeht_, and when the wall is sc.r.a.ped it falls into a vessel placed to receive it. This metal greatly resembles tin, but it is harder and less malleable.... The Alchemists have a great desire for this _zinc_ or bis.m.u.th." That this metal originated from blende or calamine was not recognised until long after, and Libavis (_Alchymia_, Frankfort, 1606), in describing specimens which came from the East, did not so identify it, this office being performed by Glauber, who says (_De Prosperitate Germanias_, Amsterdam, 1656): "Zink is a volatile mineral or half-ripe metal when it is extracted from its ore. It is more brilliant than tin and not so fusible or malleable ...
it turns (copper) into bra.s.s, as does _lapis calaminaris_, for indeed this stone is nothing but infusible zinc, and this zinc might be called a fusible _lapis calaminaris_, inasmuch as both of them partake of the same nature.... It sublimates itself up into the cracks of the furnace, whereupon the smelters frequently break it out." The systematic distillation of zinc from calamine was not discovered in Europe until the 18th Century. Henkel is generally accredited with the first statement to that effect. In a contribution published as an Appendix to his other works, of which we have had access only to a French translation (_Pyritologie_, Paris, 1760, p. 494), he concludes that zinc is a half-metal of which the best ore is calamine, but believes it is always a.s.sociated with lead, and mentions that an Englishman lately arrived from Bristol had seen it being obtained from calamine in his own country. He further mentions that it can be obtained by heating calamine and lead ore mixed with coal in a thick earthen vessel. The Bristol works were apparently those of John Champion, established about 1740.
The art of distillation was probably learned in the East.
Definite information as to the zinc minerals goes back to but a little before the Christian Era, unless we accept nebular references to _aurichalc.u.m_ by the poets, or what is possibly zinc ore in the "earth"
mentioned by Aristotle (_De Mirabilibus_, 62): "Men say that the copper of the Mossynoeci is very brilliant and white, no tin being mixed with it; but there is a kind of earth there which is melted with it." This might quite well be an a.r.s.enical mineral. But whether we can accept the poets or Aristotle or the remark of Strabo given above, as sufficient evidence or not, there is no difficulty with the description of _cadmia_ and _pompholyx_ and _spodos_ of Dioscorides (1st Century), parts of which we reproduce in note 26, p. 394. His _cadmia_ is described as rising from the copper furnaces and clinging to the iron bars, but he continues: "_Cadmia_ is also prepared by burning the stone called pyrites, which is found near Mt. Soloi in Cyprus.... Some say that _cadmia_ may also be found in stone quarries, but they are deceived by stones having a resemblance to _cadmia_." _Pompholyx_ and _spodos_ are evidently furnace calamine. From reading the quotation given on p. 394, there can be no doubt that these materials, natural or artificial, were used to make bra.s.s, for he states (V, 46): "White _pompholyx_ is made every time that the artificer in the working and perfecting of the copper sprinkles powdered _cadmia_ upon it to make it more perfect, the soot arising from this ... is _pompholyx_." Pliny is confused between the mineral _cadmia_ and furnace _calamine_, and none of his statements are very direct on the subject of bra.s.s making. His most pointed statement is (x.x.xIV, 2): "... Next to Livian (copper) this kind best absorbs _cadmia_, and is almost as good as _aurichalc.u.m_ for making sesterces and double a.s.ses." As stated above, there can be little doubt that the _aurichalc.u.m_ of the Christian Era was bra.s.s, and further, we do know of bra.s.s sesterces of this period. Other Roman writers of this and later periods refer to earth used with copper for making bra.s.s.
Apart from these evidences, however, there is the evidence of a.n.a.lyses of coins and objects, the earliest of which appears to be a large bra.s.s of the Ca.s.sia family of 20 B.C., a.n.a.lyzed by Phillips, who found 17.3% zinc (Records of Mining and Metallurgy, London, 1857, p. 13). Numerous a.n.a.lyses of coins and other objects dating during the following century corroborate the general use of bra.s.s. Professor Gowland (Presidential Address, Inst. of Metals, 1912) rightly considers the Romans were the first to make bra.s.s, and at about the above period, for there appears to be no certainty of any earlier production. The first adequate technical description of bra.s.s making is in about 1200 A.D. being that of Theophilus, who describes (Hendrie's Trans., p. 307) calcining _calamina_ and mixing it with finely divided copper in glowing crucibles. The process was repeated by adding more calamine and copper until the pots were full of molten metal. This method is repeatedly described with minor variations by Biringuccio, Agricola (_De Nat.
Fos._), and others, down to the 18th Century. For discussion of the zinc minerals see note on p. 112.
[49] "_... non raro, ut nonnulli pyritae sunt, candida...._" This is apparently the unknown substance mentioned above.
[50] One _drachma_ is about 3 ounces Troy per short ton. Three _unciae_ are about 72 ounces 6 dwts. Troy per short ton.
[51] In this section, which treats of the metallurgy of _plumb.u.m candidum_, "tin," the word _candidum_ is very often omitted in the Latin, leaving only _plumb.u.m_, which is confusing at times with lead.
The black tin-stone, _lapilli nigri_ has been treated in a similar manner, _lapilli_ (small stones) constantly occurring alone in the Latin. This has been rendered as "tin-stone" throughout, and the material prior to extraction of the _lapilli nigri_ has been rendered "tin-stuff," after the Cornish.
[52] "_... ex saxis vilibus, quae natura de diversa materia composuit._"
The Glossary gives _grindstein_. Granite (?).
[53] HISTORICAL NOTES ON TIN METALLURGY. The first appearance of tin lies in the ancient bronzes. And while much is written upon the "Bronze Age" by archaeologists, we seriously doubt whether or not a large part of so-called bronze is not copper. In any event, this period varied with each race, and for instance, in Britain may have been much later than Egyptian historic times. The bronze articles of the IV Dynasty (from 3800 to 4700 B.C. depending on the authority) place us on certain ground of antiquity. Professor Gowland (Presidential Address, Inst. of Metals, London, 1912) maintains that the early bronzes were the result of direct smelting of stanniferous copper ores, and while this may be partially true for Western Europe, the distribution and nature of the copper deposits do not warrant this a.s.sumption for the earlier scenes of human activity--Asia Minor, Egypt, and India. Further, the lumps of rough tin and also of copper found by Borlase (Tin Mining in Spain, Past and Present, London, 1897, p. 25) in Cornwall, mixed with bronze celts under conditions certainly indicating the Bronze Age, is in itself of considerable evidence of independent melting. To our mind the vast majority of ancient bronzes must have been made from copper and tin mined and smelted independently. As to the source of supply of ancient tin, we are on clear ground only with the advent of the Phoenicians, 1500-1000 B.C., who, as is well known, distributed to the ancient world a supply from Spain and Britain. What the source may have been prior to this time has been subject to much discussion, and while some slender threads indicate the East, we believe that a more local supply to Egypt, etc., is not impossible. The discovery of large tin fields in Central Africa and the native-made tin ornaments in circulation among the negroes, made possible the entrance of the metal into Egypt along the trade routes. Further, we see no reason why alluvial tin may not have existed within easy reach and have become exhausted. How quickly such a source of metal supply can be forgotten and no evidence remain, is indicated by the seldom remembered alluvial gold supply from Ireland.
However, be these conjectures as they may, the East has long been the scene of tin production and of transportation activity. Among the slender evidences that point in this direction is that the Sanskrit term for tin is _kastira_, a term also employed by the Chaldeans, and represented in Arabic by _kasdir_, and it may have been the progenitor of the Greek _ca.s.siteros_. There can be no doubt that the Phoenicians also traded with Malacca, etc., but beyond these threads there is little to prove the pre-western source. The strained argument of Beckmann (Hist. of Inventions, vol. II., p. 207) that the _ca.s.siteros_ of Homer and the _bedil_ of the Hebrews was possibly not tin, and that tin was unknown at this time, falls to the ground in the face of the vast amount of tin which must have been in circulation to account for the bronze used over a period 2,000 years prior to those peoples. Tin is early mentioned in the Scriptures (Numbers x.x.xI, 22), being enumerated among the spoil of the Midianites (1200 B.C.?), also Ezekiel (600 B.C., XXVII, 12) speaks of tin from Tars.h.i.+sh (the Phoenician settlement on the coast of Spain). According to Homer tin played considerable part in Vulcan's metallurgical stores. Even approximately at what period the Phoenicians began their distribution from Spain and Britain cannot be determined. They apparently established their settlements at Gades (Cadiz) in Tars.h.i.+sh, beyond Gibraltar, about 1100 B.C. The remains of tin mining in the Spanish peninsula prior to the Christian Era indicate most extensive production by the Phoenicians, but there is little evidence as to either mining or smelting methods. Generally as to the technical methods of mining and smelting tin, we are practically without any satisfactory statement down to Agricola. However, such sc.r.a.ps of information as are available are those in Homer (see note on p. 402), Diodorus, and Pliny.
Diodorus says (V, 2) regarding tin in Spain: "They dig it up, and melt it down in the same way as they do gold and silver;" and again, speaking of the tin in Britain, he says: "These people make tin, which they dig up with a great deal of care and labour; being rocky, the metal is mixed with earth, out of which they melt the metal, and then refine it." Pliny (x.x.xIV, 47), in the well-known and much-disputed pa.s.sage: "Next to be considered are the characteristics of lead, which is of two kinds, black and white. The most valuable is the white; the Greeks called it _ca.s.siteros_, and there is a fabulous story of its being searched for and carried from the islands of Atlantis in barks covered with hides.
Certainly it is obtained in Lusitania and Gallaecia on the surface of the earth from black-coloured sand. It is discovered by its great weight, and it is mixed with small pebbles in the dried beds of torrents. The miners wash these sands, and that which settles they heat in the furnace. It is also found in gold mines, which are called _alutiae_. A stream of water pa.s.sing through detaches small black pebbles variegated with white spots, the weight of which is the same as gold. Hence it is that they remain in the baskets of the gold collectors with the gold; afterward, they are separated in a _camillum_ and when melted become white lead."
There is practically no reference to the methods of Cornish tin-working over the whole period of 2,000 years that mining operations were carried on there prior to the Norman occupation. From then until Agricola's time, a period of some four centuries, there are occasional references in Stannary Court proceedings, Charters, and such-like official doc.u.ments which give little metallurgical insight. From a letter of William de Wrotham, Lord Warden of the Stannaries, in 1198, setting out the regulations for the impost on tin, it is evident that the black tin was smelted once at the mines and that a second smelting or refining was carried out in specified towns under the observation of the Crown Officials. In many other official doc.u.ments there are repeated references to the right to dig turfs and cut wood for smelting the tin.
Under note 8, p. 282, we give some further information on tin concentration, and the relation of Cornish and German tin miners.
Biringuccio (1540) gives very little information on tin metallurgy, and we are brought to _De Re Metallica_ for the first clear exposition.
As to the description on these pages it must be remembered that the tin-stone has been already roasted, thus removing some volatile impurities and oxidizing others, as described on page 348. The furnaces and the methods of working the tin, here described, are almost identical with those in use in Saxony to-day. In general, since Agricola's time tin has not seen the mechanical and metallurgical development of the other metals. The comparatively small quant.i.ties to be dealt with; the necessity of maintaining a strong reducing atmosphere, and consequently a mild cold blast; and the comparatively low temperature demanded, gave little impetus to other than crude appliances until very modern times.
De Re Metallica Part 42
You're reading novel De Re Metallica Part 42 online at LightNovelFree.com. You can use the follow function to bookmark your favorite novel ( Only for registered users ). If you find any errors ( broken links, can't load photos, etc.. ), Please let us know so we can fix it as soon as possible. And when you start a conversation or debate about a certain topic with other people, please do not offend them just because you don't like their opinions.
De Re Metallica Part 42 summary
You're reading De Re Metallica Part 42. This novel has been translated by Updating. Author: Georgius Agricola already has 666 views.
It's great if you read and follow any novel on our website. We promise you that we'll bring you the latest, hottest novel everyday and FREE.
LightNovelFree.com is a most smartest website for reading novel online, it can automatic resize images to fit your pc screen, even on your mobile. Experience now by using your smartphone and access to LightNovelFree.com
- Related chapter:
- De Re Metallica Part 41
- De Re Metallica Part 43
RECENTLY UPDATED NOVEL

The King of Hell's Genius Pampered Wife
The King of Hell's Genius Pampered Wife Chapter 1928: Accepted! View : 2,732,510
A Demon Lord's Tale: Dungeons, Monster Girls, and Heartwarming Bliss
A Demon Lord's Tale: Dungeons, Monster Girls, and Heartwarming Bliss Chapter 574 View : 1,365,615
Eternal Life Begins with Taking a Wife
Eternal Life Begins with Taking a Wife Chapter 1153: Mysterious Exotic Beast (1) View : 410,703
Cultivation: Start From Simplifying Martial Arts Techniques
Cultivation: Start From Simplifying Martial Arts Techniques Chapter 1092: Chapter 1048 Stepping Stone View : 621,173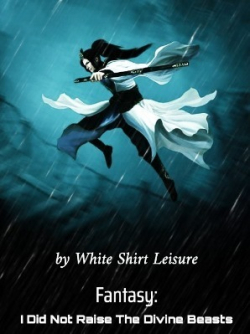
Fantasy: I Did Not Raise The Divine Beasts
Fantasy: I Did Not Raise The Divine Beasts Chapter 1111: These Are All Trash (1) View : 387,915