Aviation Engines Part 16
You’re reading novel Aviation Engines Part 16 online at LightNovelFree.com. Please use the follow button to get notification about the latest chapter next time when you visit LightNovelFree.com. Use F11 button to read novel in full-screen(PC only). Drop by anytime you want to read free – fast – latest novel. It’s great if you could leave a comment, share your opinion about the new chapters, new novel with others on the internet. We’ll do our best to bring you the finest, latest novel everyday. Enjoy!
Among the advantages stated for direct air cooling, the greatest is the elimination of cooling water and its cooling auxiliaries, which is a factor of some moment, as it permits considerable reduction in horse-power-weight ratio of the engine, something very much to be desired. In the temperate zone, where the majority of airplanes are used, the weather conditions change in a very few months from the warm summer to the extreme cold winter, and when water-cooled systems are employed it is necessary to add some chemical substance to the water to prevent it from freezing. The substances commonly employed are glycerine, wood alcohol, or a saturated solution of calcium chloride.
Alcohol has the disadvantage in that it vaporizes readily and must be often renewed. Glycerine affects the rubber hose, while the calcium chloride solution crystallizes and deposits salt in the radiator and water pipes.
One of the disadvantages of an air-cooling method, as stated by those who do not favor this system, is that engines cooled by air cannot be operated for extended periods under constant load or at very high speed without heating up to such a point that premature ignition of the charge may result. The water-cooling systems, at the other hand, maintain the temperature of the engine more nearly constant than is possible with an air-cooled motor, and an engine cooled by water can be operated under conditions of inferior lubrication or poor mixture adjustment that would seriously interfere with proper and efficient cooling by air.
Air-cooled motors, as a rule, use less fuel than water-cooled engines, because the higher temperature of the cylinder does not permit of a full charge of gas being inspired on the intake stroke. As special care is needed in operating an air-cooled engine to obtain satisfactory results and because of the greater difficulty which obtains in providing proper lubrication and fuel mixtures which will not produce undue heating, the air-cooled system has but few adherents at the present time, and practically all airplanes, with but very few exceptions, are provided with water-cooled power plants. Those fitted with air-cooled engines are usually short-flight types where maximum lightness is desired in order to obtain high speed and quick climb. The water-cooled engines are best suited for airplanes intended for long flights. The Gnome, Le Rhone and Clerget engines are thoroughly practical and have been widely used in France and England. These are rotary radial cylinder types. The Anzani is a fixed cylinder engine used on training machines, while the Renault is a V-type engine made in eight- and twelve-cylinder V forms that has been used on reconnaissance and bombing airplanes with success. These types will be fully considered in proper sequence.
CHAPTER VIII
Methods of Cylinder Construction--Block Castings--Influence on Crank-Shaft Design--Combustion Chamber Design--Bore and Stroke Ratio--Meaning of Piston Speed--Advantage of Off-Set Cylinders-- Valve Location of Vital Import--Valve Installation Practice-- Valve Design and Construction--Valve Operation--Methods of Driving Cam-Shaft--Valve Springs--Valve Timing--Blowing Back-- Lead Given Exhaust Valve--Exhaust Closing, Inlet Opening-- Closing the Inlet Valve--Time of Ignition--How an Engine Is Timed--Gnome "Monosoupape" Valve Timing--Springless Valves--Four Valves per Cylinder.
The improvements noted in the modern internal combustion motors have been due to many conditions. The continual experimenting by leading mechanical minds could have but one ultimate result. The parts of the engines have been lightened and strengthened, and greater power has been obtained without increasing piston displacement. A careful study has been made of the many conditions which make for efficient motor action, and that the main principles are well recognized by all engineers is well shown by the standardization of design noted in modern power plants. There are many different methods of applying the same principle, and it will be the purpose of this chapter to define the ways in which the construction may be changed and still achieve the same results. The various components may exist in many different forms, and all have their advantages and disadvantages. That all methods are practical is best shown by the large number of successful engines which use radically different designs.
METHODS OF CYLINDER CONSTRUCTION
One of the most important parts of the gasoline engine and one that has material bearing upon its efficiency is the cylinder unit. The cylinders may be cast individually, or in pairs, and it is possible to make all cylinders a unit or block casting. Some typical methods of cylinder construction are shown in accompanying ill.u.s.trations. The appearance of individual cylinder castings may be ascertained by examination of the Hall-Scott airplane engine. Air-cooled engine cylinders are always of the individual pattern.
Considered from a purely theoretical point of view, the individual cylinder casting has much in its favor. It is advanced that more uniform cooling is possible than where the cylinders are cast either in pairs or three or four in one casting. More uniform cooling insures that the expansion or change of form due to heating will be more equal. This is an important condition because the cylinder bore must remain true under all conditions of operation. If the heating effect is not uniform, which condition is liable to obtain if metal is not evenly distributed, the cylinder may become distorted by heat and the bore be out of truth. When separate cylinders are used it is possible to make a uniform water s.p.a.ce and have the cooling liquid evenly distributed around the cylinder. In multiple cylinder castings this is not always the rule, as in many instances, especially in four-cylinder block motors where compactness is the main feature, there is but little s.p.a.ce between the cylinders for the pa.s.sage of water. Under such circ.u.mstances the cooling effect is not even, and the stresses which obtain because of unequal expansion may distort the cylinder to some extent. When steel cylinders are made from forgings, the water jackets are usually of copper or sheet steel attached to the forging by autogenous welding; in the case of the latter and, in some cases, the former may be electro-deposited on the cylinders.
BLOCK CASTINGS
[Ill.u.s.tration: Fig. 86.--Views of Four-Cylinder Duesenberg Airplane Engine Cylinder Block.]
The advantage of casting the cylinders in blocks is that a motor may be much shorter than it would be if individual castings were used. It is admitted that when the cylinders are cast together a more compact, rigid, and stronger power plant is obtained than when cast separately.
There is a disadvantage, however, in that if one cylinder becomes damaged it will be necessary to replace the entire unit, which means sc.r.a.pping three good cylinders because one of the four has failed. When the cylinders are cast separately one need only replace the one that has become damaged. The casting of four cylinders in one unit is made possible by improved foundry methods, and when proper provision is made for holding the cores when the metal is poured and the cylinder casts are good, the construction is one of distinct merit. It is sometimes the case that the proportion of sound castings is less when cylinders are cast in block, but if the proper precautions are observed in molding and the proper mixtures of cast iron used, the ratio of defective castings is no more than when cylinders are molded individually. As an example of the courage of engineers in departing from old-established rules, the cylinder casting shown at Fig. 86 may be considered typical. This is used on the Duesenberg four-cylinder sixteen-valve 4-3/4" 7" engine which has a piston displacement of 496 cu. in. At a speed of 2,000 r.p.m., corresponding to a piston speed of 2,325 ft. per min., the engine is guaranteed to develop 125 horse-power. The weight of the model engine without gear reduction is 436 lbs., but a number of refinements have been made in the design whereby it is expected to get the weight down to 390 lbs. The four cylinders are cast from semi-steel in a single block, with integral heads. The cylinder construction is the same as that which has always been used by Mr. Duesenberg, inlet and exhaust valves being arranged horizontally opposite each other in the head.
There are large openings in the water jacket at both sides and at the ends, which are closed by means of aluminum covers, water-tightness being secured by the use of gaskets. This results in a saving in weight because the aluminum covers can be made considerably lighter than it would be possible to cast the jacket walls, and, besides, it permits of obtaining a more nearly uniform thickness of cylinder wall, as the cores can be much better supported. The cooling water pa.s.ses completely around each cylinder, and there is a very considerable s.p.a.ce between the two central cylinders, this being made necessary in order to get the large bearing area desirable for the central bearing.
It is common practice to cast the water jackets integral with the cylinders, if cast iron or aluminum is used, and this is also the most economical method of applying it because it gives good results in practice. An important detail is that the water s.p.a.ces must be proportioned so that they are equal around the cylinders whether these members are cast individually, in pairs, threes or fours. When cylinders are cast in block form it is good practice to leave a large opening in the jacket wall which will a.s.sist in supporting the core and make for uniform water s.p.a.ce. It will be noticed that the casting shown at Fig.
86 has a large opening in the side of the cylinder block. These openings are closed after the interior of the casting is thoroughly cleaned of all sand, core wire, etc., by bra.s.s, cast iron or aluminum plates. These also have particular value in that they may be removed after the motor has been in use, thus permitting one to clean out the interior of the water jacket and dispose of the rust, sediment, and incrustation which are always present after the engine has been in active service for a time.
Among the advantages claimed for the practice of casting cylinders in blocks may be mentioned compactness, lightness, rigidity, simplicity of water piping, as well as permitting the use of simple forms of inlet and exhaust manifolds. The light weight is not only due to the reduction of the cylinder ma.s.s but because the block construction permits one to lighten the entire motor. The fact that all cylinders are cast together decreases vibration, and as the construction is very rigid, disalignment of working parts is practically eliminated. When inlet and exhaust manifolds are cored in the block casting, as is sometimes the case, but one joint is needed on each of these instead of the multiplicity of joints which obtain when the cylinders are individual castings. The water piping is also simplified. In the case of a four-cylinder block motor but two pipes are used; one for the water to enter the cylinder jacket, the other for the cooling liquid to discharge through.
INFLUENCE ON CRANK-SHAFT DESIGN
[Ill.u.s.tration: Fig. 87.--Twin-Cylinder Block of Sturtevant Airplane Engine is Cast of Aluminum, and Has Removable Cylinder Head.]
The method of casting the cylinders has a material influence on the design of the crank-shaft as will be shown in proper sequence. When four cylinders are combined in one block it is possible to use a two-bearing crank-shaft. Where cylinders are cast in pairs a three-bearing crank-shaft is commonly supplied, and when cylinders are cast as individual units it is thought necessary to supply a five-bearing crank-shaft, though sometimes shafts having but three journals are used successfully. Obviously the shafts must be stronger and stiffer to withstand the stresses imposed if two supporting bearings are used than if a larger number are employed. In this connection it may be stated that there is less difficulty in securing alignment with a lesser number of bearings and there is also less friction. On the other hand, the greater the number of points of support a crank-shaft has the lighter the webs can be made and still have requisite strength.
COMBUSTION CHAMBER DESIGN
[Ill.u.s.tration: Fig. 88.--Aluminum Cylinder Pair Casting of Thomas 150 Horse-Power Airplane Engine is of the L Head Type.]
Another point of importance in the design of the cylinder, and one which has considerable influence upon the power developed, is the shape of the combustion chamber. The endeavor of designers is to obtain maximum power from a cylinder of certain proportions, and the greater energy obtained without increasing piston displacement or fuel consumption the higher the efficiency of the motor. To prevent troubles due to pre-ignition it is necessary that the combustion chamber be made so that there will be no roughness, sharp corners, or edges of metal which may remain incandescent when heated or which will serve to collect carbon deposits by providing a point of anchorage. With the object of providing an absolutely clean combustion chamber some makers use a separable head unit to their twin cylinder castings, such as shown at Fig. 87 and Fig.
88. These permit one to machine the entire interior of the cylinder and combustion chamber. The relation of valve location and combustion chamber design will be considered in proper sequence. These cylinders are cast of aluminum, instead of cast iron, as is customary, and are provided with steel or cast iron cylinder liners forced in the soft metal casting bores.
BORE AND STROKE RATIO
A question that has been a vexed one and which has been the subject of considerable controversy is the proper proportion of the bore to the stroke. The early gas engines had a certain well-defined bore to stroke ratio, as it was usual at that time to make the stroke twice as long as the bore was wide, but this cannot be done when high speed is desired.
With the development of the present-day motor the stroke or piston travel has been gradually shortened so that the relative proportions of bore and stroke have become nearly equal. Of late there seems to be a tendency among designers to return to the proportions which formerly obtained, and the stroke is sometimes one and a half or one and three-quarter times the bore.
Engines designed for high speed should have the stroke not much longer than the diameter of the bore. The disadvantage of short-stroke engines is that they will not pull well at low speeds, though they run with great regularity and smoothness at high velocity. The long-stroke engine is much superior for slow speed work, and it will pull steadily and with increasing power at low speed. It was formerly thought that such engines should never turn more than a moderate number of revolutions, in order not to exceed the safe piston speed of 1,000 feet per minute. This old theory or rule of practice has been discarded in designing high efficiency automobile racing and aviation engines, and piston speeds from 2,500 to 3,000 feet per minute are sometimes used, though the average is around 2,000 feet per minute. While both short- and long-stroke motors have their advantages, it would seem desirable to average between the two. That is why a proportion of four to five or six seems to be more general than that of four to seven or eight, which would be a long-stroke ratio. Careful a.n.a.lysis of a number of foreign aviation motors shows that the average stroke is about 1.2 times the bore dimensions, though some instances were noted where it was as high as 1.7 times the bore.
MEANING OF PISTON SPEED
The factor which limits the stroke and makes the speed of rotation so dependent upon the travel of the piston is piston speed. Lubrication is the main factor which determines piston speed, and the higher the rate of piston travel the greater care must be taken to insure proper oiling.
Let us fully consider what is meant by piston speed.
a.s.sume that a motor has a piston travel or stroke of six inches, for the sake of ill.u.s.tration. It would take two strokes of the piston to cover one foot, or twelve inches, and as there are two strokes to a revolution it will be seen that this permits of a normal speed of 1,000 revolutions per minute for an engine with a six-inch stroke, if one does not exceed 1,000 feet per minute. If the stroke was only four inches, a normal speed of 1,500 revolutions per minute would be possible without exceeding the prescribed limit. The crank-shaft of a small engine, having three-inch stroke, could turn at a speed of 2,000 revolutions per minute without danger of exceeding the safe speed limit. It will be seen that the longer the stroke the slower the speed of the engine, if one desires to keep the piston speed within the bounds as recommended, but modern practice allows of greatly exceeding the speeds formerly thought best.
ADVANTAGES OF OFF-SET CYLINDERS
[Ill.u.s.tration: Fig. 90.--Cross Section of Austro-Daimler Engine, Showing Offset Cylinder Construction. Note Applied Water Jacket and Peculiar Valve Action.]
Another point upon which considerable difference of opinion exists relates to the method of placing the cylinder upon the crank-case--i.e., whether its center line should be placed directly over the center of the crank-shaft, or to one side of center. The motor shown at Fig. 90 is an off-set type, in that the center line of the cylinder is a little to one side of the center of the crank-shaft. Diagrams are presented at Fig. 91 which show the advantages of off-set crank-shaft construction.
The view at A is a section through a simple motor with the conventional cylinder placing, the center line of both crank-shaft and cylinder coinciding. The view at B shows the cylinder placed to one side of center so that its center line is distinct from that of the crank-shaft and at some distance from it. The amount of off-set allowed is a point of contention, the usual amount being from fifteen to twenty-five per cent. of the stroke. The advantages of the off-set are shown at Fig. 91, C. If the crank turns in direction of the arrow there is a certain resistance to motion which is proportional to the amount of energy exerted by the engine and the resistance offered by the load. There are two thrusts acting against the cylinder wall to be considered, that due to explosion or expansion of the gas, and that which resists the motion of the piston. These thrusts may be represented by arrows, one which acts directly in a vertical direction on the piston top, the other along a straight line through the center of the connecting rod. Between these two thrusts one can draw a line representing a resultant force which serves to bring the piston in forcible contact with one side of the cylinder wall, this being known as side thrust. As shown at C, the crank-shaft is at 90 degrees, or about one-half stroke, and the connecting rod is at 20 degrees angle. The shorter connecting rod would increase the diagonal resultant and side thrusts, while a longer one would reduce the angle of the connecting rod and the side thrust of the piston would be less. With the off-set construction, as shown at D, it will be noticed that with the same connecting-rod length as shown at C and with the crank-shaft at 90 degrees of the circle that the connecting-rod angle is 14 degrees and the side thrust is reduced proportionately.
[Ill.u.s.tration: Fig. 91.--Diagrams Demonstrating Advantages of Offset Crank-Shaft Construction.]
Another important advantage is that greater efficiency is obtained from the explosion with an off-set crank-shaft, because the crank is already inclined when the piston is at top center, and all the energy imparted to the piston by the burning mixture can be exerted directly into producing a useful turning effort. When a cylinder is placed directly on a line with the crank-shaft, as shown at A, it will be evident that some of the force produced by the expansion of the gas will be exerted in a direct line and until the crank moves the crank throw and connecting rod are practically a solid member. The pressure which might be employed in obtaining useful turning effort is wasted by causing a direct pressure upon the lower half of the main bearing and the upper half of the crank-pin bus.h.i.+ng.
Very good and easily understood ill.u.s.trations showing advantages of the off-set construction are shown at E and F. This is a bicycle crank-hanger. It is advanced that the effort of the rider is not as well applied when the crank is at position E as when it is at position F.
Position E corresponds to the position of the parts when the cylinder is placed directly over the crank-shaft center. Position F may be compared to the condition which is present when the off-set cylinder construction is used.
VALVE LOCATION OF VITAL IMPORT
It has often been said that a chain is no stronger than its weakest link, and this is as true of the explosive motor as it is of any other piece of mechanism. Many motors which appeared to be excellently designed and which were well constructed did not prove satisfactory because some minor detail or part had not been properly considered by the designer. A factor having material bearing upon the efficiency of the internal combustion motor is the location of the valves and the shape of the combustion chamber which is largely influenced by their placing. The fundamental consideration of valve design is that the gases be admitted and discharged from the cylinder as quickly as possible in order that the speed of gas flow will not be impeded and produce back pressure. This is imperative in obtaining satisfactory operation in any form of motor. If the inlet pa.s.sages are constricted the cylinder will not fill with explosive mixture promptly, whereas if the exhaust gases are not fully expelled the parts of the inert products of combustion retained dilute the fresh charge, making it slow burning and causing lost power and overheating. When an engine employs water as a cooling medium this substance will absorb the surplus heat readily, and the effects of overheating are not noticed as quickly as when air-cooled cylinders are employed. Valve sizes have a decided bearing upon the speed of motors and some valve locations permit the use of larger members than do other positions.
While piston velocity is an important factor in determinations of power output, it must be considered from the aspect of the wear produced upon the various parts of the motor. It is evident that engines which run very fast, especially of high power, must be under a greater strain than those operating at lower speeds. The valve-operating mechanism is especially susceptible to the influence of rapid movement, and the slower the engine the longer the parts will wear and the more reliable the valve action.
[Ill.u.s.tration: Fig. 92.--Diagram Showing Forms of Cylinder Demanded by Different Valve Placings. A--T Head Type, Valves on Opposite Sides. B--L Head Cylinder, Valves Side by Side. C--L Head Cylinder, One Valve in Head, Other in Pocket. D--Inlet Valve Over Exhaust Member, Both in Side Pocket. E--Valve-in-the-Head Type with Vertical Valves. F--Inclined Valves Placed to Open Directly into Combustion Chamber.]
As will be seen by reference to the accompanying ill.u.s.tration, Fig. 92, there are many ways in which valves may be placed in the cylinder. Each method outlined possesses some point of advantage, because all of the types ill.u.s.trated are used by reputable automobile manufacturers. The method outlined at Fig. 92, A, is widely used, and because of its shape the cylinder is known as the "T" form. It is approved for automobile use for several reasons, the most important being that large valves can be employed and a well-balanced and symmetrical cylinder casting obtained.
Two independent cam-shafts are needed, one operating the inlet valves, the other the exhaust members. The valve-operating mechanism can be very simple in form, consisting of a plunger actuated by the cam which transmits the cam motion to the valve-stem, raising the valve as the cam follower rides on the point of the cam. Piping may be placed without crowding, and larger manifolds can be fitted than in some other constructions. This has special value, as it permits the use of an adequate discharge pipe on the exhaust side with its obvious advantages.
This method of cylinder construction is never found on airplane engines because it does not permit of maximum power output.
On the other hand, if considered from a viewpoint of actual heat efficiency, it is theoretically the worst form of combustion chamber.
This disadvantage is probably compensated for by uniformity of expansion of the cylinder because of balanced design. The ignition spark-plug may be located directly over the inlet valve in the path of the incoming fresh gases, and both valves may be easily removed and inspected by uns.c.r.e.w.i.n.g the valve caps without taking off the manifolds.
Aviation Engines Part 16
You're reading novel Aviation Engines Part 16 online at LightNovelFree.com. You can use the follow function to bookmark your favorite novel ( Only for registered users ). If you find any errors ( broken links, can't load photos, etc.. ), Please let us know so we can fix it as soon as possible. And when you start a conversation or debate about a certain topic with other people, please do not offend them just because you don't like their opinions.
Aviation Engines Part 16 summary
You're reading Aviation Engines Part 16. This novel has been translated by Updating. Author: Victor Wilfred Page already has 718 views.
It's great if you read and follow any novel on our website. We promise you that we'll bring you the latest, hottest novel everyday and FREE.
LightNovelFree.com is a most smartest website for reading novel online, it can automatic resize images to fit your pc screen, even on your mobile. Experience now by using your smartphone and access to LightNovelFree.com
- Related chapter:
- Aviation Engines Part 15
- Aviation Engines Part 17
RECENTLY UPDATED NOVEL
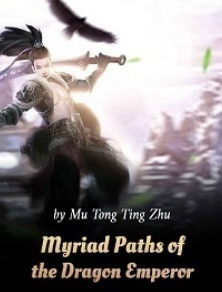
Myriad Paths of the Dragon Emperor
Myriad Paths of the Dragon Emperor Chapter 3091: Sinister intentions View : 1,659,797
The Grand Secretary's Pampered Wife
The Grand Secretary's Pampered Wife Chapter 763.1: Overbearing Robbery! View : 617,402
Madam's Identities Shocks The Entire City Again
Madam's Identities Shocks The Entire City Again Chapter 3489: A Sir Who Claims to Be From Continent M Is Looking For You View : 2,719,077