Aviation Engines Part 20
You’re reading novel Aviation Engines Part 20 online at LightNovelFree.com. Please use the follow button to get notification about the latest chapter next time when you visit LightNovelFree.com. Use F11 button to read novel in full-screen(PC only). Drop by anytime you want to read free – fast – latest novel. It’s great if you could leave a comment, share your opinion about the new chapters, new novel with others on the internet. We’ll do our best to bring you the finest, latest novel everyday. Enjoy!
[Ill.u.s.tration: Fig. 128.--Connecting Rod Types Summarized.
A--Single Connecting Rod Made in One Piece, Usually Fitted in Small Single-Cylinder Engines Having Built-Up Crank-Shafts. B--Marine Type, a Popular Form on Heavy Engines. C--Conventional Automobile Type, a Modified Marine Form. D--Type Having Hinged Lower Cap and Split Wrist Pin Bus.h.i.+ng. E--Connecting Rod Having Diagonally Divided Big End.
F--Ball-Bearing Rod. G--Sections Showing Structural Shapes Commonly Employed in Connecting Rod Construction.]
In a number of instances, instead of plain bushed bearings anti-friction forms using ball or rollers have been used at the lower end. A ball-bearing connecting rod is shown at F. The big end may be made in one piece, because if it is possible to get the ball bearing on the crank-pins it will be easy to put the connecting rod in place. Ball bearings are not used very often on connecting rod big ends because of difficulty of installation, though when applied properly they give satisfactory service and reduce friction to a minimum. One of the advantages of the ball bearing is that it requires no adjustment, whereas the plain bus.h.i.+ngs depicted in the other connecting rods must be taken up from time to time to compensate for wear.
This can be done in forms shown at B, C, D, and E by bringing the lower bearing caps closer to the upper one and sc.r.a.ping out the bra.s.ses to fit the shaft. A number of liners or s.h.i.+ms of thin bra.s.s or copper stock, varying from .002 inch to .005 inch, are sometimes interposed between the halves of the bearings when it is first fitted to the crank-pin. As the bra.s.ses wear the s.h.i.+ms may be removed and the portions of the bearings brought close enough together to take up any lost motion that may exist, though in some motors no s.h.i.+ms are provided and depreciation can be remedied only by installing new bra.s.ses and sc.r.a.ping to fit.
[Ill.u.s.tration: Fig. 129.--Double Connecting Rod a.s.sembly For Use On Single Crank-Pin of Vee Engine.]
The various structural shapes in which connecting rods are formed are shown in section at G. Of these the I section is most widely used in airplane engines, because it is strong and a very easy shape to form by the drop-forging process or to machine out of the solid bar when extra good steel is used. Where extreme lightness is desired, as in small high-speed motors used for cycle propulsion, the section shown at the extreme left is often used. If the rod is a cast member as in some marine engines, the cross, hollow cylinder, or U sections are sometimes used. If the sections shown at the right are employed, advantage is often taken of the opportunity for pa.s.sing lubricant through the center of the hollow round section on vertical motors or at the bottom of the U section, which would be used on a horizontal cylinder power plant.
[Ill.u.s.tration: Fig. 130.--Another Type of Double Connecting Rod for Vee Engines.]
Connecting rods of Vee engines are made in two distinct styles. The forked or "scissors" joint rod a.s.sembly is employed when the cylinders are placed directly opposite each other. The "blade" rod, as shown at Fig. 129, fits between the lower ends of the forked rod, which oscillate on the bearing which encircles the crank-pin. The lower end of the "blade" rod is usually attached to the bearing bra.s.ses, the ends of the "forked" rod move on the outer surfaces of the bra.s.ses. Another form of rod devised for use under these conditions is shown at Fig. 130 and installed in an aviation engine at Fig. 132. In this construction the shorter rod is attached to a boss on the master rod by a short pin to form a hinge and to permit the short rod to oscillate as the conditions dictate. This form of rod can be easily adjusted when the bearing depreciates, a procedure that is difficult with the forked type rod. The best practice, in the writer's opinion, is to stagger the cylinders and use side-by-side rods as is done in the Curtiss engine. Each rod may be fitted independently of the other and perfect compensation for wear of the big ends is possible.
[Ill.u.s.tration: Fig. 131.--Part Sectional View of Wisconsin Aviation Engine, Showing Four-Bearing Crank-Shaft, Overhead Cam-Shaft, and Method of Combining Cylinders in Pairs.]
[Ill.u.s.tration: Fig. 132.--Part Sectional View of Renault Twelve-Cylinder Water-Cooled Engine, Showing Connecting Rod Construction and Other Important Internal Parts.]
CAM-SHAFT AND CRANK-SHAFT DESIGN
Before going extensively into the subject of crank-shaft construction it will be well to consider cam-shaft design, which is properly a part of the valve system and which has been considered in connection with the other elements which have to do directly with cylinder construction to some extent. Cam-shafts are usually simple members carried at the base of the cylinder in the engine case of Vee type motors by suitable bearings and having the cams employed to lift the valves attached at intervals. A typical cam-shaft design is shown at Fig. 133. Two main methods of cam-shaft construction are followed--that in which the cams are separate members, keyed and pinned to the shaft, and the other where the cams are formed integral, the latter being the most suitable for airplane engine requirements.
[Ill.u.s.tration: Fig. 133.--Typical Cam-Shaft, with Valve Lifting Cams and Gears to Operate Auxiliary Devices Forged Integrally.]
The cam-shafts shown at Figs. 133 and 134, B, are of the latter type, as the cams are machined integrally. In this case not only the cams but also the gears used in driving the auxiliary shafts are forged integral.
This is a more expensive construction, because of the high initial cost of forging dies as well as the greater expense of machining. It has the advantage over the other form in which the cams are keyed in place in that it is stronger, and as the cams are a part of the shaft they can never become loose, as might be possible where they are separately formed and a.s.sembled on a simple shaft.
[Ill.u.s.tration: Fig. 134.--Important Parts of Duesenberg Aviation Engine.
A--Three Main Bearing Crank-Shaft. B--Cam-Shaft with Integral Cams.
C--Piston and Connecting Rod a.s.sembly. D--Valve Rocker Group. E--Piston.
F--Main Bearing Bra.s.ses.]
The importance of the crank-shaft has been previously considered, and some of its forms have been shown in views of the motors presented in earlier portions of this work. The crank-shaft is one of the parts subjected to the greatest strain and extreme care is needed in its construction and design, because practically the entire duty of transmitting the power generated by the motor to the gea.r.s.et devolves upon it. Crank-shafts are usually made of high tensile strength steel of special composition. They may be made in four ways, the most common being from a drop or machine forging which is formed approximately to the shape of the finished shaft and in rare instances (experimental motors only) they may be steel castings. Sometimes they are made from machine forgings, where considerably more machine work is necessary than would be the case where the shaft is formed between dies. Some engineers favor blocking the shaft out of a solid slab of metal and then machining this rough blank to form. In some radial-cylinder motors of the Gnome and Le Rhone type the crank-shafts are built up of two pieces, held together by taper fastenings or bolts.
[Ill.u.s.tration: Fig. 135.--Showing Method of Making Crank-Shaft. A--The Rough Steel Forging Before Machining. B--The Finished Six-Throw, Seven-Bearing Crank-Shaft.]
The form of the shaft depends on the number of cylinders and the form has material influence on the method of construction. For instance, a four-cylinder crank-shaft could be made by either of the methods outlined. On the other hand, a three- or six-cylinder shaft is best made by the machine forging process, because if drop forged or cut from the blank it will have to be heated and the crank throws bent around so that the pins will lie in three planes one hundred and twenty degrees apart, while the other types described need no further attention, as the crank-pins lie in planes one hundred and eighty degrees apart. This can be better understood by referring to Fig. 135, which shows a six-cylinder shaft in the rough and finished stages. At A the appearance of the machine forging before any of the material is removed is shown, while at B the appearance of the finished crank-shaft is clearly depicted. The built-up crank-shaft is seldom used on multiple-cylinder motors, except in some cases where the crank-shafts revolve on ball bearings as in some automobile racing engines.
[Ill.u.s.tration: Fig. 136.--Showing Form of Crank-Shaft for Twin-Cylinder Opposed Power Plant.]
[Ill.u.s.tration: Fig. 137.--Crank-Shaft of Thomas-Morse Eight-Cylinder Vee Engine.]
Crank-shaft form will vary with a number of cylinders and it is possible to use a number of different arrangements of crank-pins and bearings for the same number of cylinders. The simplest form of crank-shaft is that used on simple radial cylinder motors as it would consist of but one crank-pin, two webs, and the crank-shaft. As the number of cylinders increase in Vee motors as a general rule more crank-pins are used. The crank-shaft that would be used on a two-cylinder opposed motor is shown at Fig. 136. This has two throws and the crank-pins are s.p.a.ced 180 degrees apart. The bearings are exceptionally long. Four-cylinder crank-shafts may have two, three or five main bearings and three or four crank-pins. In some forms of two-bearing crank-shafts, such as used when four-cylinders are cast in a block, or unit casting, two of the pistons are attached to one common crank-pin, so that in reality the crank-shaft has but three crank-pins. A typical three bearing, four-cylinder crank-shaft is shown at Fig. 134, A. The same type can be used for an eight-cylinder Vee engine, except for the greater length of crank-pins to permit of side by side rods as shown at Fig. 137. Six cylinder vertical tandem and twelve-cylinder Vee engine crank-shafts usually have four or seven main bearings depending upon the disposition of the crank-pins and arrangement of cylinders. At Fig. 138, A, the bottom view of a twelve-cylinder engine with bottom half of crank case removed is given. This ill.u.s.trates clearly the arrangement of main bearings when the crank-shaft is supported on four journals. The crank-shaft shown at Fig. 138, B, is a twelve-cylinder seven-bearing type.
[Ill.u.s.tration: Fig. 138.--Crank-Case and Crank-Shaft Construction for Twelve-Cylinder Motors. A--Duesenberg. B--Curtiss.]
[Ill.u.s.tration: Fig. 139.--Counterbalanced Crank-Shafts Reduce Engine Vibration and Permit of Higher Rotative Speeds.]
In some automobile engines, extremely good results have been secured in obtaining steady running with minimum vibration by counterbalancing the crank-shafts as outlined at Fig. 139. The shaft at A is a type suitable for a high speed four-cylinder vertical or an eight-cylinder Vee type.
That at B is for a six-cylinder vertical or a twelve-cylinder V with scissors joint rods. If counterbalancing crank-shafts helps in an automobile engine, it should have advantages of some moment in airplane engines, even though the crank-shaft weight is greater.
BALL-BEARING CRANK-SHAFTS
While crank-shafts are usually supported in plain journals there seems to be a growing tendency of late to use anti-friction bearings of the ball type for their support. This is especially noticeable on block motors where but two main bearings are utilized. When ball bearings are selected with proper relation to the load which obtains they will give very satisfactory service. They permit the crank-shaft to turn with minimum friction, and if properly selected will never need adjustment.
The front end is supported by a bearing which is clamped in such a manner that it will take a certain amount of load in a direction parallel to the axis of the shaft, while the rear end is so supported that the outer race of the bearing has a certain amount of axial freedom or "float." The inner race or cone of each bearing is firmly clamped against shoulders on the crank-shaft. At the front end of the crank-shaft timing gear and a suitable check nut are used, while at the back end the bearing is clamped by a threaded retention member between the fly-wheel and a shoulder on the crank-shaft. The fly-wheel is held in place by a taper and key retention. The ball bearings are carried in a light housing of bronze or malleable iron, which in turn are held in the crank-case by bolts. The Renault engine uses ball bearings at front and rear ends of the crank-shaft, but has plain bearings around intermediate crank-shaft journals. The rotary engines of the Gnome, Le Rhone and Clerget forms would not be practical if ball bearings were not used as the bearing friction and consequent depreciation would be very high.
ENGINE-BASE CONSTRUCTION
One of the important parts of the power plant is the substantial casing or bed member, which is employed to support the cylinders and crank-shaft and which is attached directly to the fuselage engine supporting members. This will vary widely in form, but as a general thing it is an approximately cylindrical member which may be divided either vertically or horizontally in two or more parts. Airplane engine crank-cases are usually made of aluminum, a material which has about the same strength as cast iron, but which only weighs a third as much. In rare cases cast iron is employed, but is not favored by most engineers because of its brittle nature, great weight and low resistance to tensile stresses. Where exceptional strength is needed alloys of bronze may be used, and in some cases where engines are produced in large quant.i.ties a portion of the crank-case may be a sheet steel or aluminum stamping.
[Ill.u.s.tration: Fig. 140.--View of Thomas 135 Horse-Power Aeromotor, Model 8, Showing Conventional Method of Crank-Case Construction.]
[Ill.u.s.tration: Fig. 141.--Views of Upper Half of Thomas Aeromotor Crank-Case.]
Crank-cases are always large enough to permit the crank-shaft and parts attached to it to turn inside and obviously its length is determined by the number of cylinders and their disposition. The crank-case of the radial cylinder or double-opposed cylinder engine would be substantially the same in length. That of a four-cylinder will vary in length with the method of casting the cylinder. When the four-cylinders are cast in one unit and a two-bearing crank-shaft is used, the crank-case is a very compact and short member. When a three-bearing crank-shaft is utilized and the cylinders are cast in pairs, the engine base is longer than it would be to support a block casting, but is shorter than one designed to sustain individual cylinder castings and a five-bearing crank-shaft. It is now common construction to cast an oil container integral with the bottom of the engine base and to draw the lubricating oil from it by means of a pump, as shown at Fig. 140. The arms by which the motor is supported in the fuselage are substantial-ribbed members cast integrally with the upper half.
[Ill.u.s.tration: Fig. 142.--Method of Constructing Eight-Cylinder Vee Engine, Possible if Aluminum Cylinder and Crank-Case Castings are Used.]
[Ill.u.s.tration: Fig. 143.--Simple and Compact Crank-Case, Possible When Radial Cylinder Engine Design is Followed.]
The approved method of crank-case construction favored by the majority of engineers is shown at the top of Fig. 141, bottom side up. The upper half not only forms a bed for the cylinder but is used to hold the crank-shaft as well. In the ill.u.s.tration, the three-bearing boxes form part of the case, while the lower bra.s.ses are in the form of separately cast caps retained by suitable bolts. In the construction outlined the bottom part of the case serves merely as an oil container and a protection for the interior mechanism of the motor. The cylinders are held down by means of studs screwed into the crank-case top, as shown at Fig. 141, lower view. If the aluminum cylinder motor has any future, the method of construction outlined at Fig. 142, which has been used in cast iron for an automobile motor, might be used for an eight-cylinder Vee engine for airplane use. The simplicity of the crank-case needed for a revolving cylinder motor and its small weight can be well understood by examination of the ill.u.s.tration at Fig. 143, which shows the engine crank-case for the nine-cylinder "Monosoupape" Gnome engine. This consists of two accurately machined forgings held together by bolts as clearly indicated.
CHAPTER X
Power Plant Installation--Curtiss OX-2 Engine Mounting and Operating Rules--Standard S. A. E. Engine Bed Dimensions-- Hall-Scott Engine Installation and Operation--Fuel System Rules --Ignition System--Water System--Preparations to Start Engine-- Mounting Radial and Rotary Engines--Practical Hints to Locate Engine Troubles--All Engine Troubles Summarized--Location of Engine Troubles Made Easy.
The proper installation of the airplane power plant is more important than is generally supposed, as while these engines are usually well balanced and run with little vibration, it is necessary that they be securely anch.o.r.ed and that various connections to the auxiliary parts be carefully made in order to prevent breakage from vibration and that attendant risk of motor stoppage while in the air. The type of motor to be installed determines the method of installation to be followed. As a general rule six-cylinder vertical engine and eight-cylinder Vee type are mounted in substantially the same way. The radial, fixed cylinder forms and the radial, rotary cylinder Gnome and Le Rhone rotary types require an entirely different method of mounting. Some unconventional mountings have been devised, notably that shown at Fig. 144, which is a six-cylinder German engine that is installed in just the opposite way to that commonly followed. The inverted cylinder construction is not generally followed because even with pressure feed, dry crank-case type lubricating system there is considerable danger of over-lubrication and of oil collecting and carbonizing in the combustion chamber and gumming up the valve action much quicker than would be the case if the engine was operated in the conventional upright position. The reason for mounting an engine in this way is to obtain a lower center of gravity and also to make for more perfect streamlining of the front end of the fuselage in some cases. It is rather doubtful if this slight advantage will compensate for the disadvantages introduced by this unusual construction. It is not used to any extent now but is presented merely to show one of the possible systems of installing an airplane engine.
[Ill.u.s.tration: Fig. 144.--Unconventional Mounting of German Inverted Cylinder Motor.]
[Ill.u.s.tration: Fig. 145.--How Curtiss Model OX-2 Motor is Installed in Fuselage of Curtiss Tractor Biplane. Note Similarity of Mounting to Automobile Power Plant.]
In a number of airplanes of the tractor-biplane type the power plant installation is not very much different than that which is found in automobile practice. The ill.u.s.tration at Fig. 145 is a very clear representation of the method of mounting the Curtiss eight-cylinder 90 H. P. or model OX-2 engine in the fuselage of the Curtiss JN-4 tractor biplane which is so generally used in the United States as a training machine. It will be observed that the fuel tank is mounted under a cowl directly behind the motor and that it feeds the carburetor by means of a flexible fuel pipe. As the tank is mounted higher than the carburetor, it will feed that member by gravity. The radiator is mounted at the front end of the fuselage and connected to the water piping on the motor by the usual rubber hose connections. An oil pan is placed under the engine and the top is covered with a hood just as in motor car practice. The panels of aluminum are attached to the sides of the fuselage and are supplied with doors which open and provide access to the carburetor, oil-gauge and other parts of the motor requiring inspection. The complete installation with the power plant enclosed is given at Fig. 146, and in this it will be observed that the exhaust pipes are connected to discharge members that lead the gases above the top plane. In the engine shown at Fig. 145 the exhaust flows directly into the air at the sides of the machine through short pipes bolted to the exhaust gas outlet ports. The installation of the radiator just back of the tractor screw insures that adequate cooling will be obtained because of the rapid air flow due to the propeller slip stream.
[Ill.u.s.tration: Fig. 146.--Latest Model of Curtiss JN-4 Training Machine, Showing Thorough Enclosure of Power Plant and Method of Disposing of the Exhaust Gases.]
INSTALLATION OF CURTISS OX-2 ENGINE
[Ill.u.s.tration: Fig. 147.--Front View of L. W. F. Tractor Biplane Fuselage, Showing Method of Installing Thomas Aeromotor and Method of Disposing of Exhaust Gases.]
Aviation Engines Part 20
You're reading novel Aviation Engines Part 20 online at LightNovelFree.com. You can use the follow function to bookmark your favorite novel ( Only for registered users ). If you find any errors ( broken links, can't load photos, etc.. ), Please let us know so we can fix it as soon as possible. And when you start a conversation or debate about a certain topic with other people, please do not offend them just because you don't like their opinions.
Aviation Engines Part 20 summary
You're reading Aviation Engines Part 20. This novel has been translated by Updating. Author: Victor Wilfred Page already has 679 views.
It's great if you read and follow any novel on our website. We promise you that we'll bring you the latest, hottest novel everyday and FREE.
LightNovelFree.com is a most smartest website for reading novel online, it can automatic resize images to fit your pc screen, even on your mobile. Experience now by using your smartphone and access to LightNovelFree.com
- Related chapter:
- Aviation Engines Part 19
- Aviation Engines Part 21
RECENTLY UPDATED NOVEL
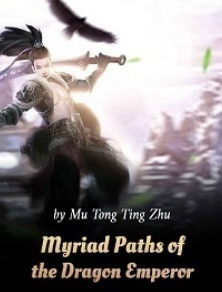
Myriad Paths of the Dragon Emperor
Myriad Paths of the Dragon Emperor Chapter 3091: Sinister intentions View : 1,659,780
The Grand Secretary's Pampered Wife
The Grand Secretary's Pampered Wife Chapter 763.1: Overbearing Robbery! View : 617,389
Madam's Identities Shocks The Entire City Again
Madam's Identities Shocks The Entire City Again Chapter 3489: A Sir Who Claims to Be From Continent M Is Looking For You View : 2,719,046