Aviation Engines Part 19
You’re reading novel Aviation Engines Part 19 online at LightNovelFree.com. Please use the follow button to get notification about the latest chapter next time when you visit LightNovelFree.com. Use F11 button to read novel in full-screen(PC only). Drop by anytime you want to read free – fast – latest novel. It’s great if you could leave a comment, share your opinion about the new chapters, new novel with others on the internet. We’ll do our best to bring you the finest, latest novel everyday. Enjoy!
CHAPTER IX
Constructional Details of Pistons--Aluminum Cylinders and Pistons--Piston Ring Construction--Leak Proof Piston Rings-- Keeping Oil Out of Combustion Chamber--Connecting Rod Forms-- Connecting Rods for Vee Engines--Cam-Shaft and Crank-Shaft Designs--Ball Bearing Crank-Shafts--Engine Base Construction.
CONSTRUCTIONAL DETAILS OF PISTONS
The piston is one of the most important parts of the gasoline motor inasmuch as it is the reciprocating member that receives the impact of the explosion and which transforms the power obtained by the combustion of gas to mechanical motion by means of the connecting rod to which it is attached. The piston is one of the simplest elements of the motor, and it is one component which does not vary much in form in different types of motors. The piston is a cylindrical member provided with a series of grooves in which packing rings are placed on the outside and two bosses which serve to hold the wrist pin in its interior. It is usually made of cast iron or aluminum, though in some motors where extreme lightness is desired, such as those used for aeronautic work, it may be made of steel. The use of the more resisting material enables the engineer to use lighter sections where it is important that the weight of this member be kept as low as possible consistent with strength.
[Ill.u.s.tration: Fig. 116.--Forms of Pistons Commonly Employed in Gasoline Engines. A--Dome Head Piston and Three Packing Rings. B--Flat Top Form Almost Universally Used. C--Concave Piston Utilized in Knight Motors and Some Having Overhead Valves. D--Two-Cycle Engine Member with Deflector Plate Cast Integrally. E--Differential of Two-Diameter Piston Used in Some Engines Operating on Two-Cycle Principle.]
A number of piston types are shown at Fig. 116. That at A has a round top and is provided with four split packing rings and two oil grooves. A piston of this type is generally employed in motors where the combustion chamber is large and where it is desired to obtain a higher degree of compression than would be possible with a flat top piston. This construction is also stronger because of the arched piston top. The most common form of piston is that shown at B, and it differs from that previously described only in that it has a flat top. The piston outlined in section at C is a type used on some of the sleeve-valve motors of the Knight pattern, and has a concave head instead of the convex form shown at A. The design shown at D in side and plan views is the conventional form employed in two-cycle engines. The deflector plate on the top of the cylinder is cast integral and is utilized to prevent the incoming fresh gases from flowing directly over the piston top and out of the exhaust port, which is usually opposite the inlet opening. On these types of two-cycle engines where a two-diameter cylinder is employed, the piston shown at E is used. This is known as a "differential piston," and has an enlarged portion at its lower end which fits the pumping cylinder. The usual form of deflector plate is provided at the top of the piston and one may consider it as two pistons in one.
[Ill.u.s.tration: Fig. 117.--Typical Methods of Piston Pin Retention Generally Used in Engines of American Design. A--Single Set Screw and Lock Nut. B--Set Screw and Check Nut Fitting Groove in Wrist Pin. C, D--Two Locking Screws Pa.s.sing Into Interior of Hollow Wrist Pin.
E--Split Ring Holds Pin in Place. F--Use of Taper Expanding Plugs Outlined. G--Spring Pressed Plunger Type. H--Piston Pin Pinned to Connecting Rod. I--Wrist Pin Clamped in Connecting Rod Small End by Bolt.]
[Ill.u.s.tration: Fig. 118.--Typical Piston and Connecting Rod a.s.sembly.]
[Ill.u.s.tration: Fig. 119.--Parts of Sturtevant Aviation Engine.
A--Cylinder Head Showing Valves. B--Connecting Rod. C--Piston and Rings.]
One of the important conditions in piston design is the method of securing the wrist pin which is used to connect the piston to the upper end of the connecting rod. Various methods have been devised to keep the pin in place, the most common of these being shown at Fig. 117. The wrist pin should be retained by some positive means which is not liable to become loose under the vibratory stresses which obtain at this point.
If the wrist pin was free to move it would work out of the bosses enough so that the end would bear against the cylinder wall. As it is usually made of steel, which is a harder material than cast iron used in cylinder construction, the rubbing action would tend to cut a groove in the cylinder wall which would make for loss of power because it would permit escape of gas. The wrist pin member is a simple cylindrical element that fits the bosses closely, and it may be either hollow or solid stock. A typical piston and connecting rod a.s.sembly which shows a piston in section also is given at Fig. 118. The piston of the Sturtevant aeronautical motor is shown at Fig. 119, the aluminum piston of the Thomas airplane motor with piston rings in place is shown at Fig.
120. A good view of the wrist pin and connecting rod are also given. The iron piston of the Gnome "Monosoupape" airplane engine and the unconventional connecting rod a.s.sembly are clearly depicted at Fig 121.
[Ill.u.s.tration: Fig. 120.--Aluminum Piston and Light But Strong Steel Connecting Rod and Wrist Pin of Thomas Aviation Engine.]
The method of retention shown at A is the simplest and consists of a set screw having a projecting portion pa.s.sing into the wrist pin and holding it in place. The screw is kept from turning or loosening by means of a check nut. The method outlined at B is similar to that shown at A, except that the wrist pin is solid and the point of the set screw engages an annular groove turned in the pin for its reception. A very positive method is shown at C. Here the retention screws pa.s.s into the wrist pin and are then locked by a piece of steel wire which pa.s.ses through suitable holes in the ends. The method outlined at D is sometimes employed, and it varies from that shown at C only in that the locking wire, which is made of spring steel, is pa.s.sed through the heads of the locking screws. Some designers machine a large groove around the piston at such a point that when the wrist pin is put in place a large packing ring may be sprung in the groove and utilized to hold the wrist pin in place.
[Ill.u.s.tration: Fig. 121.--Cast Iron Piston of "Monosoupape" Gnome Engine Installed On One of the Short Connecting Rods.]
The system shown at F is not so widely used as the simpler methods, because it is more costly and does not offer any greater security when the parts are new than the simple lock shown at A. In this a hollow wrist pin is used, having a tapered thread cut at each end. The wrist pin is slotted at three or four points, for a distance equal to the length of the boss, and when taper expansion plugs are screwed in place the ends of the wrist pin are expanded against the bosses. This method has the advantage of providing a certain degree of adjustment if the wrist pin should loosen up after it has been in use for some time. The taper plugs would be screwed in deeper and the ends of the wrist pin expanded proportionately to take up the loss motion. The method shown at G is an ingenious one. One of the piston bosses is provided with a projection which is drilled out to receive a plunger. The wrist pin is provided with a hole of sufficient size to receive the plunger, which is kept in place by means of a spring in back of it. This makes a very positive lock and one that can be easily loosened when it is desired to remove the wrist pin. To unlock, a piece of fine rod is thrust into the hole at the bottom of the boss which pushes the plunger back against the spring until the wrist pin can be pushed out of the piston.
Some engineers think it advisable to oscillate the wrist pin in the piston bosses, instead of in the connecting rod small end. It is argued that this construction gives more bearing surface at the wrist pin and also provides for more strength because of the longer bosses that can be used. When this system is followed the piston pin is held in place by locking it to the connecting rod by some means. At H the simplest method is outlined. This consisted of driving a taper pin through both rod and wrist pin and then preventing it from backing out by putting a split cotter through the small end of the tapered locking pin. Another method, which is depicted at I, consists of clamping the wrist pin by means of a suitable bolt which brings the slit connecting rod end together as shown.
ALUMINUM FOR CYLINDERS AND PISTONS
Aluminum pistons outlined at Fig. 122, have replaced cast iron members in many airplane engines, as these weigh about one-third as much as the cast iron forms of the same size, while the reduction in the inertia forces has made it possible to increase the engine speed without correspondingly stressing the connecting rods, crank-shaft and engine bearings.
[Ill.u.s.tration: Fig. 122.--Types of Aluminum Pistons Used In Aviation Engines.]
Aluminum has not only been used for pistons, but a number of motors will be built for the coming season that will use aluminum cylinder block castings as well. Of course, the aluminum alloy is too soft to be used as a bearing for the piston, and it will not withstand the hammering action of the valve. This makes the use of cast iron or steel imperative in all motors. When used in connection with an aluminum cylinder block the cast iron pieces are placed in the mould so that they act as cylinder liners and valve seats, and the molten metal is poured around them when the cylinder is cast. It is said that this construction results in an intimate bond between the cast iron and the surrounding aluminum metal. Steel liners may also be pressed into the aluminum cylinders after these are bored out to receive them. Aluminum has for a number of years been used in many motor car parts. Alloys have been developed that have greater strength than cast iron and that are not so brittle. Its use for manifolds and engine crank and gear cases has been general for a number of years.
At first thought it would seem as though aluminum would be entirely unsuited for use in those portions of internal combustion engines exposed to the heat of the explosion, on account of the low melting point of that metal and its disadvantageous quality of suddenly "wilting" when a critical point in the temperature is reached. Those who hesitated to use aluminum on account of this defect lost sight of the great heat conductivity of that metal, which is considerably more than that of cast iron. It was found in early experiments with aluminum pistons that this quality of quick radiation meant that aluminum pistons remained considerably cooler than cast iron ones in service, which was attested to by the reduced formation of carbon deposit thereon. The use of aluminum makes possible a marked reduction in power plant weight. A small four-cylinder engine which was not particularly heavy even with cast iron cylinders was found to weigh 100 pounds less when the cylinder block, pistons, and upper half of the crank-case had been made of aluminum instead of cast iron. Aluminum motors are no longer an experiment, as a considerable number of these have been in use on cars during the past year without the owners of the cars being apprised of the fact. Absolutely no complaint was made in any case of the aluminum motor and it was demonstrated, in addition to the saving in weight, that the motors cost no more to a.s.semble and cooled much more efficiently than the cast iron form. One of the drawbacks to the use of aluminum is its growing scarcity, which results in making it a "near precious"
metal.
PISTON RING CONSTRUCTION
As all pistons must be free to move up and down in the cylinder with minimum friction, they must be less in diameter than the bore of the cylinder. The amount of freedom or clearance provided varies with the construction of the engine and the material the piston is made of, as well as its size, but it is usual to provide from .005 to .010 of an inch to compensate for the expansion of the piston due to heat and also to leave sufficient clearance for the introduction of lubricant between the working surfaces. Obviously, if the piston were not provided with packing rings, this amount of clearance would enable a portion of the gases evolved when the charge is exploded to escape by it into the engine crank-case. The packing members or piston rings, as they are called, are split rings of cast iron, which are sprung into suitable grooves machined on the exterior of the piston, three or four of these being the usual number supplied. These have sufficient elasticity so that they bear tightly against the cylinder wall and thus make a gas-tight joint. Owing to the limited amount of surface in contact with the cylinder wall and the elasticity of the split rings the amount of friction resulting from the contact of properly fitted rings and the cylinder is not of enough moment to cause any damage and the piston is free to slide up and down in the cylinder bore.
[Ill.u.s.tration: Fig. 123.--Types of Piston Rings and Ring Joints.
A--Concentric Ring. B--Eccentrically Machined Form. C--Lap Joint Ring.
D--b.u.t.t Joint, Seldom Used. E--Diagonal Cut Member, a Popular Form.]
These rings are made in two forms, as outlined at Fig. 123. The design shown at A is termed a "concentric ring," because the inner circle is concentric with the outer one and the ring is of uniform thickness at all points. The ring shown at B is called an "eccentric ring," and it is thicker at one part than at others. It has theoretical advantages in that it will make a tighter joint than the other form, as it is claimed its expansion due to heat is more uniform. The piston rings must be split in order that they may be sprung in place in the grooves, and also to insure that they will have sufficient elasticity to take the form of the cylinder at the different points in their travel. If the cylinder bore varies by small amounts the rings will spring out at the points where the bore is larger than standard, and spring in at those portions where it is smaller than standard.
It is important that the joint should be as nearly gas-tight as possible, because if it were not a portion of the gases would escape through the slots in the piston rings. The joint shown at C is termed a "lap joint," because the ends of the ring are cut in such a manner that they overlap. This is the approved joint. The b.u.t.t joint shown at D is seldom used and is a very poor form, the only advantage being its cheapness. The diagonal cut shown at E is a compromise between the very good form shown at C and the poor joint depicted at D. It is also widely used, though most constructors prefer the lap joint, because it does not permit the leakage of gas as much as the other two types.
There seems to be some difference of opinion relative to the best piston ring type--some favoring the eccentric pattern, others the concentric form. The concentric ring has advantages from the lubricating engineer's point of view; as stated by the Platt & Washburn Company in their text-book on engine lubrication, the smaller clearance behind the ring possible with the ring of uniform section is advantageous.
Fig. 124, A, shows a concentric piston ring in its groove. Since the ring itself is concentric with the groove, very small clearance between the back of the ring and the bottom of its groove may be allowed. Small clearance leaves less s.p.a.ce for the acc.u.mulation of oil and carbon deposits. The gasket effect of this ring is uniform throughout the entire length of its edges, which is its marked advantage over the eccentric ring. This type of piston ring rarely burns fast in its groove. There are a large number of different concentric rings manufactured of different designs and of different efficiency.
[Ill.u.s.tration: Fig. 124.--Diagrams Showing Advantages of Concentric Piston Rings.]
Figs. 124, B and 124, C show eccentric rings a.s.sembled in the ring groove. It will be noted that there is a large s.p.a.ce between the thin ends of this ring and the bottom of the groove. This empty s.p.a.ce fills up with oil which in the case of the upper ring frequently is carbonized, restricting the action of the ring and nullifying its usefulness. The edges of the thin ends are not sufficiently wide to prevent rapid escape of gases past them. In a practical way this leakage means loss of compression and noticeable drop in power. When new and properly fitted, very little difference can be noted between the tightness of eccentric and concentric rings. Nevertheless, after several months' use, a more rapid leakage will always occur past the eccentric than past the concentric. If continuous trouble with the carbonization of cylinders, smoking and sooting of spark-plugs is experienced, it is a sure indication that mechanical defects exist in the engine, a.s.suming of course, that a suitable oil has been used. Such trouble can be greatly lessened, if not entirely eliminated, by the application of concentric rings (lap joint), of any good make, properly fitted into the grooves of the piston. Too much emphasis cannot be put upon this point.
If the oil used in the engine is of the correct viscosity, and serious carbon deposit, smoking, etc., still result, the only certain remedy then is to have the cylinders rebored and fitted with properly designed, oversized pistons and piston rings.
LEAK-PROOF PISTON RINGS
In order to reduce the compression loss and leakage of gas by the ordinary simple form of diagonal or lap joint one-piece piston ring a number of compound rings have been devised and are offered by their makers to use in making replacements. The leading forms are shown at Fig. 125. That shown at A is known as the "Stat.i.te" and consists of three rings, one carried inside while the other two are carried on the outside. The ring shown at B is a double ring and is known as the McCadden. This is composed of two thin concentric lap joint rings so disposed relative to each other that the opening in the inner ring comes opposite to the opening in the outer ring.
The form shown at C is known as the "Leekt.i.te," and is a single ring provided with a peculiar form of lap and dove tail joint. The ring shown at D is known as the "Dunham" and is of the double concentric type being composed of two rings with lap joints which are welded together at a point opposite the joint so that there is no pa.s.sage by which the gas can escape. The Burd high compression ring is shown at E. The joints of these rings are sealed by means of an H-shaped coupler of bronze which closes the opening. The ring ends are made with tongues which interlock with the coupling. The ring shown at F is called the "Evert.i.te" and is a three-piece ring composed of three members as shown in the sectional view below the ring. The main part or inner ring has a circ.u.mferential channel in which the two outer rings lock, the resulting cross-section being rectangular just the same as that of a regular pattern ring. All three rings are diagonally split and the joints are s.p.a.ced equally and the distances maintained by small pins. This results in each joint being sealed by the solid portion of the other rings.
[Ill.u.s.tration: Fig. 125.--Leak-Proof and Other Compound Piston Rings.]
The use of a number of light steel rings instead of one wide ring in the groove is found on a number of automobile power plants, but as far as known, this construction is not used in airplane power plants. It is contended that where a number of light rings is employed a more flexible packing means is obtained and the possibility of leakage is reduced.
Rings of this design are made of square section steel wire and are given a spring temper. Owing to the limited width the diagonal cut joint is generally employed instead of the lap joint which is so popular on wider rings.
KEEPING OIL OUT OF COMBUSTION CHAMBERS
An examination of the engine design that is economical in oil consumption discloses the use of tight piston rings, large centrifugal rings on the crank-shaft where it pa.s.ses through the case, ample cooling fins in the pistons, vents between the crank-case chamber and the valve enclosures, etc. Briefly put, cooling of the oil in this engine has been properly cared for and leakage reduced to a minimum. To be specific regarding details of design: Oil surplus can be kept out of the explosion chambers by leaving the lower edge of the piston skirt sharp and by the use of a shallow groove (C), Fig. 126, just below the lower piston ring. Small holes are bored through the piston walls at the base of this groove and communicate with the crank-case. The similarity of the sharp edges of piston skirt (D) and piston ring to a carpenter's plane bit, makes their operation plain.
[Ill.u.s.tration: Fig. 126.--Sectional View of Engine Showing Means of Preventing Oil Leakage By Piston Rings.]
The cooling of oil in the sump (A) can be accomplished most effectively by radiating fins on its outer surface. The lower crank-case should be fully exposed to the outer air. A settling basin for sediment (B) should be provided having a cubic content not less than one-tenth of the total oil capacity as outlined at Fig. 126. The depth of this basin should be at least 2-1/2 inches, and its walls vertical, as shown, to reduce the mixing of sediment with the oil in circulation. The inlet opening to the oil pump should be near the top of the sediment basin in order to prevent the entrance into the pump with the oil of any solid matter or water condensed from the products of combustion. This sediment basin should be drained after every five to seven hours air service of an airplane engine. Concerning filtering screens there is little to be said, save that their areas should be ample and the mesh coa.r.s.e enough (one-sixteenth of an inch) to offer no serious resistance to the free flow of cold or heavy oil through them; otherwise the oil in the crank-case may build up above them to an undesirable level. The necessary frequency of draining and flus.h.i.+ng out the oil sump differs greatly with the age (condition) of the engine and the suitability of the oil used. In broad terms, the oil sump of a new engine should be thoroughly drained and flushed with kerosene at the end of the first 200 miles, next at the end of 500 miles and thereafter every 1,000 miles. While these instructions apply specifically to automobile motors, it is very good practice to change the oil in airplane engines frequently. In many cases, the best results have been secured when the oil supply is completely replenished every five hours that the engine is in operation.
CONNECTING ROD FORMS
The connecting rod is the simple member that joins the piston to the crank-shaft and which transmits the power imparted to the piston by the explosion so that it may be usefully applied. It transforms the reciprocating movement of the piston to a rotary motion at the crank-shaft. A typical connecting rod and its wrist pin are shown at Fig. 120. It will be seen that it has two bearings, one at either end.
The small end is bored out to receive the wrist pin which joins it to the piston, while the large end has a hole of sufficient size to go on the crank-pin. The airplane and automobile engine connecting rod is invariably a steel forging, though in marine engines it is sometimes made a steel or high tensile strength bronze casting. In all cases it is desirable to have softer metals than the crank-shaft and wrist pin at the bearing point, and for this reason the connecting rod is usually provided with bus.h.i.+ngs of anti-friction or white metal at the lower end, and bronze at the upper. The upper end of the connecting rod may be one piece, because the wrist pin can be introduced after it is in place between the bosses of the piston. The lower bearing must be made in two parts in most cases, because the crank-shaft cannot be pa.s.sed through the bearing owing to its irregular form. The rods of the Gnome engine are all one piece types, as shown at Fig. 127, owing to the construction of the "mother" rod which receives the crank-pins. The complete connecting rod a.s.sembly is shown in Fig. 121, also at A, Fig. 127. The "mother" rod, with one of the other rods in place and one about to be inserted, is shown at Fig. 127, B. The built-up crank-shaft which makes this construction feasible is shown at Fig. 127, C.
[Ill.u.s.tration: Fig. 127.--Connecting Rod and Crank-Shaft Construction of Gnome "Monosoupape" Engine.]
Some of the various designs of connecting rods that have been used are shown at Fig. 128. That at A is a simple form often employed in single-cylinder motors, having built-up crank-shafts. Both ends of the connecting rod are bushed with a one-piece bearing, as it can be a.s.sembled in place before the crank-shaft a.s.sembly is built up. A built-up crank-shaft such as this type of connecting rod would be used with is shown at Fig. 106. The pattern shown at B is one that has been used to some extent on heavy work, and is known as the "marine type." It is made in three pieces, the main portion being a steel forging having a f.l.a.n.g.ed lower end to which the bronze boxes are secured by bolts. The modified marine type depicted at C is the form that has received the widest application in automobile and aviation engine construction. It consists of two pieces, the main member being a steel drop forging having the wrist-pin bearing and the upper crank-pin bearing formed integral, while the lower crank-pin bearing member is a separate forging secured to the connecting rod by bolts. In this construction bus.h.i.+ngs of anti-friction metal are used at the lower end, and a bronze bus.h.i.+ng is forced into the upper- or wrist-pin end. The rod shown at D has also been widely used. It is similar in construction to the form shown at C, except that the upper end is split in order to permit of a degree of adjustment of the wrist-pin bus.h.i.+ng, and the lower bearing cap is a hinged member which is retained by one bolt instead of two. When it is desired to a.s.semble it on the crank-shaft the lower cap is swung to one side and brought back into place when the connecting rod has been properly located. Sometimes the lower bearing member is split diagonally instead of horizontally, such a construction being outlined at E.
Aviation Engines Part 19
You're reading novel Aviation Engines Part 19 online at LightNovelFree.com. You can use the follow function to bookmark your favorite novel ( Only for registered users ). If you find any errors ( broken links, can't load photos, etc.. ), Please let us know so we can fix it as soon as possible. And when you start a conversation or debate about a certain topic with other people, please do not offend them just because you don't like their opinions.
Aviation Engines Part 19 summary
You're reading Aviation Engines Part 19. This novel has been translated by Updating. Author: Victor Wilfred Page already has 688 views.
It's great if you read and follow any novel on our website. We promise you that we'll bring you the latest, hottest novel everyday and FREE.
LightNovelFree.com is a most smartest website for reading novel online, it can automatic resize images to fit your pc screen, even on your mobile. Experience now by using your smartphone and access to LightNovelFree.com
- Related chapter:
- Aviation Engines Part 18
- Aviation Engines Part 20
RECENTLY UPDATED NOVEL
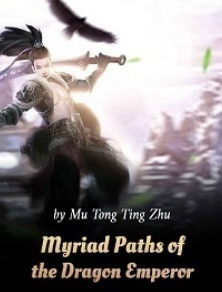
Myriad Paths of the Dragon Emperor
Myriad Paths of the Dragon Emperor Chapter 3091: Sinister intentions View : 1,659,797
The Grand Secretary's Pampered Wife
The Grand Secretary's Pampered Wife Chapter 763.1: Overbearing Robbery! View : 617,402
Madam's Identities Shocks The Entire City Again
Madam's Identities Shocks The Entire City Again Chapter 3489: A Sir Who Claims to Be From Continent M Is Looking For You View : 2,719,077