Aviation Engines Part 18
You’re reading novel Aviation Engines Part 18 online at LightNovelFree.com. Please use the follow button to get notification about the latest chapter next time when you visit LightNovelFree.com. Use F11 button to read novel in full-screen(PC only). Drop by anytime you want to read free – fast – latest novel. It’s great if you could leave a comment, share your opinion about the new chapters, new novel with others on the internet. We’ll do our best to bring you the finest, latest novel everyday. Enjoy!
BLOWING BACK
When the factor of r.e.t.a.r.ded opening is considered without reckoning the inertia of the gases, it would appear that if the valve were allowed to remain open after center had pa.s.sed, say, on the closing of the inlet, the piston, having reversed its motion, would have the effect of expelling part of the fresh charge through the still open valve as it pa.s.sed inward at its compression stroke. This effect is called blowing back, and is often noted with motors where the valve settings are not absolutely correct, or where the valve-springs or seats are defective and prevent proper closing.
This factor is not of as much import as might appear, as on closer consideration it will be seen that the movement of the piston as the crank reaches either end of the stroke is less per degree of angular movement than it is when the angle of the connecting rod is greater.
Then, again, a certain length of time is required for the reversal of motion of the piston, during which time the crank is in motion but the piston practically at a standstill. If the valves are allowed to remain open during this period, the pa.s.sage of the gas in or out of the cylinder will be by its own momentum.
LEAD GIVEN EXHAUST VALVE
The faster a motor turns, all other things being equal, the greater the amount of lead or advance it is necessary to give the opening of the exhaust valve. It is self-evident truth that if the speed of a motor is doubled it travels twice as many degrees in the time necessary to lower the pressure. As most designers are cognizant of this fact, the valves are proportioned accordingly. It is well to consider in this respect that the cam profile has much to do with the manner in which the valve is opened; that is, the lift may be abrupt and the gas allowed to escape in a body, or the opening may be gradual, the gas issuing from the cylinder in thin streams. An a.n.a.logy may be made with the opening of any bottle which contains liquid highly carbonated. If the cork is removed suddenly the gas escapes with a loud pop, but, on the other hand, if the bottle is uncorked gradually, the gas escapes from the receptacle in thin streams around the cork, and pa.s.sage of the gases to the air is accomplished without noise. While the second plan is not harsh, it is slower than the former, as must be evident.
EXHAUST CLOSING, INLET OPENING
A point which has been much discussed by engineers is the proper relation of the closing of the exhaust valve and the opening of the inlet. Theoretically they should succeed each other, the exhaust closing at upper dead center and the inlet opening immediately afterward. The reason why a certain amount of lag is given the exhaust closing in practice is that the piston cannot drive the gases out of the cylinder unless they are compressed to a degree in excess of that existing in the manifold or pa.s.sages, and while toward the end of the stroke this pressure may be feeble, it is nevertheless indispensable. At the end of the piston's stroke, as marked by the upper dead center, this compression still exists, no matter how little it may be, so that if the exhaust valve is closed and the inlet opened immediately afterward, the pressure which exists in the cylinder may r.e.t.a.r.d the entrance of the fresh gas and a certain portion of the inert gas may penetrate into the manifold. As the piston immediately begins to aspirate, this may not be serious, but as these gases are drawn back into the cylinder the fresh charge will be diluted and weakened in value. If the spark-plug is in a pocket, the points may be surrounded by this weak gas, and the explosion will not be nearly as energetic as when the ignition spark takes place in pure mixture.
It is a well-known fact that the exhaust valve should close after dead center and that a certain amount of lag should be given to opening of the inlet. The lag given the closing of the exhaust valve should not be as great as that given the closing of the inlet valve. a.s.suming that the excess pressure of the exhaust will equal the depression during aspiration, the time necessary to complete the emptying of the cylinder will be proportional to the volume of the gas within it. At the end of the suction stroke the volume of gas contained in the cylinder is equal to the cylindrical volume plus the s.p.a.ce of the combustion chamber. At the end of the exhaust stroke the volume is but that of the dead s.p.a.ce, and from one-third to one-fifth its volume before compression. While it is natural to a.s.sume that this excess of burned gas will escape faster than the fresh gas will enter the cylinder, it will be seen that if the inlet valve were allowed to lag twenty degrees, the exhaust valve lag need not be more than five degrees, providing that the capacity of the combustion chamber was such that the gases occupied one-quarter of their former volume.
It is evident that no absolute rule can be given, as back pressure will vary with the design of the valve pa.s.sages, the manifolds, and the construction of the m.u.f.fler. The more direct the opening, the sooner the valve can be closed and the better the cylinder cleared. Ten degrees represent an appreciable angle of the crank, and the time required for the crank to cover this angular motion is not inconsiderable and an important quant.i.ty of the exhaust may escape, but the piston is very close to the dead center after the distance has been covered.
Before the inlet valve opens there should be a certain depression in the cylinder, and considerable lag may be allowed before the depression is appreciable. So far as the volume of fresh gas introduced during the admission stroke is concerned, this is determined by the displacement of the piston between the point where the inlet valve opens and the point of closing, a.s.suming that sufficient gas has been inspired so that an equilibrium of pressure has been established between the interior of the cylinder and the outer air. The point of inlet opening varies with different motors. It would appear that a fair amount of lag would be fifteen degrees past top center for the inlet opening, as a certain depression will exist in the cylinder, a.s.suming that the exhaust valve has closed five or ten degrees after center, and at the same time the piston has not gone down far enough on its stroke to materially decrease the amount of gas which will be taken into the cylinder.
CLOSING THE INLET VALVE
As in the case with the other points of opening and closing, there is a wide diversity of practice as relates to closing the inlet valve. Some of the designers close this exactly at bottom center, but this practice cannot be commended, as there is a considerable portion of time, at least ten or fifteen degrees angular motion of the crank, before the piston will commence to travel to any extent on its compression stroke.
The gases rus.h.i.+ng into the cylinder have considerable velocity, and unless an equilibrium is obtained between the pressure inside and that of the atmosphere outside, they will continue to rush into the cylinder even after the piston ceases to exert any suction effect.
For this reason, if the valve is closed exactly on center, a full charge may not be inspired into the cylinder, though if the time of closing is delayed, this momentum or inertia of the gas will be enough to insure that a maximum charge is taken into the cylinder. The writer considers that nothing will be gained if the valve is allowed to remain open longer than twenty degrees, and an a.n.a.lysis of practice in this respect would seem to confirm this opinion. From that point in the crank movement the piston travel increases and the compressive effect is appreciable, and it would appear that a considerable proportion of the charge might be exhausted into the manifold and carburetor if the valve were allowed to remain open beyond a point corresponding to twenty degrees angular movement of the crank.
TIME OF IGNITION
In this country engineers unite in providing a variable time of ignition, though abroad some difference of opinion is noted on this point. The practice of advancing the time of ignition, when affected electrically, was severely condemned by early makers, these maintaining that it was necessary because of insufficient heat and volume of the spark, and it was thought that advancing ignition was injurious. The engineers of to-day appreciate the fact that the heat of the electric spark, especially when from a mechanical generator of electrical energy, is the only means by which we can obtain practically instantaneous explosion, as required by the operation of motors at high speeds, and for the combustion of large volumes of gas.
[Ill.u.s.tration: Fig. 108.--Diagrams Explaining Valve and Ignition Timing of Hall-Scott Aviation Engine.]
It is apparent that a motor with a fixed point of ignition is not as desirable, in every way, as one in which the ignition can be advanced to best meet different requirements, and the writer does not readily perceive any advantage outside of simplicity of control in establis.h.i.+ng a fixed point of ignition. In fact, there seems to be some difference of opinion among those designers who favor fixed ignition, and in one case this is located forty-three degrees ahead of center, and in another motor the point is fixed at twenty degrees, so that it may be said that this will vary as much as one hundred per cent. in various forms. This point will vary with different methods of ignition, as well as the location of the spark-plug or igniter. For the sake of simplicity, most airplane engines use set spark; if an advancing and r.e.t.a.r.ding mechanism is fitted, it is only to facilitate starting, as the spark is kept advanced while in flight, and control is by throttle alone.
[Ill.u.s.tration: Fig. 109.--Timing Diagram of Typical Six-Cylinder Engine.]
It is obvious by consideration of the foregoing that there can be no arbitrary rules established for timing, because of the many conditions which determine the best times for opening and closing the valves. It is customary to try various settings when a new motor is designed until the most satisfactory points are determined, and the setting which will be very suitable for one motor is not always right for one of different design. The timing diagram shown at Fig. 108 applies to the Hall-Scott engine, and may be considered typical. It should be easily followed in view of the very complete explanation given in preceding pages. Another six-cylinder engine diagram is shown at Fig. 109, and an eight-cylinder timing diagram is shown at Fig. 110. In timing automobile engines no trouble is experienced, because timing marks are always indicated on the engine fly-wheel register with an indicating trammel on the crank-case. To time an airplane engine accurately, as is necessary to test for a suspected cam-shaft defect, a timing disc of aluminum is attached to the crank-shaft which has the timing marks indicated thereon. If the disc is made 10 or 12 inches in diameter, it may be divided into degrees without difficulty.
[Ill.u.s.tration: Fig. 110.--Timing Diagram of Typical Eight-Cylinder V Engine.]
HOW AN ENGINE IS TIMED
In timing a motor from the marks on the timing disc rim it is necessary to regulate the valves of but one cylinder at a time. a.s.suming that the disc is revolving in the direction of engine rotation, and that the firing order of the cylinders is 1-3-4-2, the operation of timing would be carried on as follows: The crank-shaft would be revolved until the line marked "Exhaust opens 1 and 4" registered with the trammel on the motor bed. At this point the exhaust-valve of either cylinder No. 1 or No. 4 should begin to open. This can be easily determined by noting which of these cylinders holds the compressed charge ready for ignition.
a.s.suming that the spark has occurred in cylinder No. 1, then when the fly-wheel is turned from the position to that in which the line marked "Exhaust opens 1 and 4" coincides with the trammel point, the valve-plunger under the exhaust-valve of cylinder No. 1 should be adjusted in such a way that there is no clearance between it and the valve stem. Further movement of the wheel in the same direction should produce a lift of the exhaust valve. The disc is turned about two hundred and twenty-five degrees, or a little less than three-quarters of a revolution; then the line marked "Exhaust closes 1 and 4" will register with the trammel point. At this period the valve-plunger and the valve-stem should separate and a certain amount of clearance obtain between them. The next cylinder to time would be No. 3. The crank-shaft is rotated until mark "Exhaust opens 2 and 3" comes in line with the trammel. At this point the exhaust valve of cylinder No. 3 should be just about opening. The closing is determined by rotating the shaft until the line "Exhaust closes 2 and 3" comes under the trammel.
This operation is carried on with all the cylinders, it being well to remember that but one cylinder is working at a time and that a half-revolution of the fly-wheel corresponds to a full working stroke of all the cylinders, and that while one is exhausting the others are respectively taking in a new charge, compressing and exploding. For instance, if cylinder No. 1 has just completed its power-stroke, the piston in cylinder No. 3 has reached the point where the gas may be ignited to advantage. The piston of cylinder No. 4, which is next to fire, is at the bottom of its stroke and will have inspired a charge, while cylinder No. 2, which is the last to fire, will have just finished expelling a charge of burned gas, and will be starting the intake stroke. This timing relates to a four-cylinder engine in order to simplify the explanation. The timing instructions given apply only to the conventional motor types. Rotary cylinder engines, especially the Gnome "monosoupape," have a distinctive valve timing on account of the peculiarities of design.
GNOME "MONOSOUPAPE" VALVE TIMING
In the present design of the Gnome motor, a cycle of operations somewhat different from that employed in the ordinary four-cycle engine is made use of, says a writer in "The Automobile," in describing the action of this power-plant. This cycle does away with the need for the usual inlet valve and makes the engine operable with only a single valve, hence the name _monosoupape_, or "single-valve." The cycle is as follows: A charge being compressed in the outer end of the cylinder or combustion chamber, it is ignited by a spark produced by the spark-plug located in the side of this chamber, and the burning charge expands as the piston moves down in the cylinder while the latter revolves around the crank-shaft. When the piston is about half-way down on the power stroke, the exhaust valve, which is located in the center of the cylinder-head, is mechanically opened, and during the following upstroke of the piston the burnt gases are expelled from the cylinder through the exhaust valve directly into the atmosphere.
Instead of closing at the end of the exhaust stroke, or a few degrees thereafter, the exhaust valve is held open for about two-thirds of the following inlet stroke of the piston, with the result that fresh air is drawn through the exhaust valve into the cylinder. When the cylinder is still 65 degrees from the end of the inlet half-revolution, the exhaust valve closes. As no more air can get into the cylinder, and as the piston continues to move inwardly, it is obvious that a partial vacuum is formed.
When the cylinder approaches within 20 degrees of the end of the inlet half-revolution a series of small inlet ports all around the circ.u.mference of the cylinder wall is uncovered by the top edge of the piston, whereby the combustion chamber is placed in communication with the crank chamber. As the pressure in the crank chamber is substantially atmospheric and that in the combustion chamber is below atmospheric, there results a suction effect which causes the air from the crank chamber to flow into the combustion chamber. The air in the crank chamber is heavily charged with gasoline vapor, which is due to the fact that a spray nozzle connected with the gasoline supply tank is located inside the chamber. The proportion of gasoline vapor in the air in the crank chamber is several times as great as in the ordinary combustible mixture drawn from a carburetor into the cylinder. This extra-rich mixture is diluted in the combustion chamber with the air which entered it through the exhaust valve during the first part of the inlet stroke, thus forming a mixture of the proper proportion for complete combustion.
The inlet ports in the cylinder wall remain open until 20 degrees of the compression half-revolution has been completed, and from that moment to near the end of the compression stroke the gases are compressed in the cylinder. Near the end of the stroke ignition takes place and this completes the cycle.
The exact timing of the different phases of the cycle is shown in the diagram at Fig. 111. It will be seen that ignition occurs substantially 20 degrees ahead of the outer dead center, and expansion of the burning gases continues until 85 degrees past the outer dead center, when the piston is a little past half-stroke. Then the exhaust-valve opens and remains open for somewhat more than a complete revolution of the cylinders, or, to be exact, for 390 degrees of cylinder travel, until 115 degrees past the top dead center on the second revolution. Then for 45 degrees of travel the charge within the cylinder is expanded, whereupon the inlet ports are uncovered and remain open for 40 degrees of cylinder travel, 20 degrees on each side of the inward dead center position.
SPRINGLESS VALVES
Springless valves are the latest development on French racing car engines, and it is possible that the positively-operated types will be introduced on aviation engines also. Two makes of positively-actuated valves are shown at Fig. 112. The positive-valve motor differs from the conventional form by having no necessity for valve-springs, as a cam not only a.s.sures the opening of the valve, but also causes it to return to the valve-seat. In this respect it is much like the sleeve-valve motor, where the uncovering of the ports is absolutely positive. The cars equipped with these valves were a success in long-distance auto races.
Claims made for this type of valve mechanism include the possibility of a higher number of revolutions and consequently greater engine power.
With the spring-controlled, single-cam operated valve a point is reached where the spring is not capable of returning the valve to its seat before the cam has again begun its opening movement. It is possible to extend the limits considerably by using a light valve on a strong spring, but the valve still remains a limiting factor in the speed of the motor.
[Ill.u.s.tration: Fig. 111.--Timing Diagram Showing Peculiar Valve Timing of Gnome "Monosoupape" Rotary Motor.]
A part sectional view through a cylinder of an engine designed by G.
Michaux is shown at Fig. 112, A. There are two valves per cylinder, inclined at about ten degrees from the vertical. The valve-stems are of large diameter, as owing to positive control, there is no necessity of lightening this part in an unusual degree. A single overhead cam-shaft has eight pairs of cams, which are shown in detail at B. For each valve there is a three-armed rocker, one arm of which is connected to the stem of the valve and the two others are in contact respectively with the opening and closing cams. The connection to the end of the valve-stem is made by a short connecting link, which is screwed on to the end of the valve-stem and locked in position. This allows some adjustment to be made between the valves and the actuating rocker. It will be evident that one cam and one rocker arm produce the opening of the valve and that the corresponding rocker arm and cam result in the closing of the valve. If the opening cam has the usual convex profile, the closing cam has a correspondingly concave profile. It will be noticed that a light valve-spring is shown in drawing. This is provided to give a final seating to its valve after it has been closed by the cam. This is not absolutely necessary, as an engine has been run successfully without these springs. The whole mechanism is contained within an overhead aluminum cover.
[Ill.u.s.tration: Fig. 112.--Two Methods of Operating Valves by Positive Cam Mechanism Which Closes as Well as Opens Them.]
The positive-valve system used on the De Lage motor is shown at D. In this the valves are actuated as shown in sectional views D and E. The valve system is unique in that four valves are provided per cylinder, two for exhaust and two for intake. The valves are mounted side by side, as shown at E, so the double actuator member may be operated by a single set of cams. The valve-operating member consists of a yoke having guide bars at the top and bottom. The actuating cam works inside of this yoke.
The usual form of cam acts on the lower portion of the yoke to open the valve, while the concave cam acts on the upper part to close the valves.
In this design provision is made for expansion of the valve-stems due to heat, and these are not positively connected to the actuating member. As shown at E, the valves are held against the seat by short coil springs at the upper end of the stem. These are very stiff and are only intended to provide for expansion. A slight s.p.a.ce is left between the top of the valve-stem and the portion of the operating member that bears against them when the regular profile cam exerts its pressure on the bottom of the valve-operating mechanism. Another novelty in this motor design is that the cam-shafts and the valve-operating members are carried in casing attached above the motor by housing supports in the form of small steel pillars. The overhead cam-shafts are operated by means of bevel gearing.
FOUR VALVES PER CYLINDER
[Ill.u.s.tration: Fig. 113.--Diagram Comparing Two Large Valves and Four Small Ones of Practically the Same Area. Note How Easily Small Valves are Installed to Open Directly Into the Cylinder.]
Mention has been previously made of the sixteen-valve four-cylinder Duesenberg motor and its great power output for the piston displacement.
This is made possible by the superior volumetric efficiency of a motor provided with four valves in each cylinder instead of but two. This principle was thoroughly tried out in racing automobile motors, and is especially valuable in permitting of greater speed and power output from simple four- and six-cylinder engines. On eight- and twelve-cylinder types, it is doubtful if the resulting complication due to using a very large number of valves would be worth while. When extremely large valves are used, as shown in diagram at Fig. 113, it is difficult to have them open directly into the cylinder, and pockets are sometimes necessary. A large valve would weigh more than two smaller valves having an area slightly larger in the aggregate; it would require a stiffer valve spring on account of its greater weight. A certain amount of metal in the valve-head is necessary to prevent warping; therefore, the inertia forces will be greater in the large valve than in the two smaller valves. As a greater port area is obtained by the use of two valves, the gases will be drawn into the cylinder or expelled faster than with a lesser area. Even if the areas are practically the same as in the diagram at Fig. 113, the smaller valves may have a greater lift without imposing greater stresses on the valve-operating mechanism and quicker gas intake and exhaust obtained. The smaller valves are not affected by heat as much as larger ones are. The quicker gas movements made possible, as well as reduction of inertia forces, permits of higher rotative speed, and, consequently, greater power output for a given piston displacement. The drawings at Fig. 114 show a sixteen-valve motor of the four-cylinder type that has been designed for automobile racing purposes, and it is apparent that very slight modifications would make it suitable for aviation purposes. Part of the efficiency is due to the reduction of bearing friction by the use of ball bearings, but the multiple-valve feature is primarily responsible for the excellent performance.
[Ill.u.s.tration: Fig. 114.--Sectional Views of Sixteen-Valve Four-Cylinder Automobile Racing Engine That May Have Possibilities for Aviation Service.]
[Ill.u.s.tration: Fig. 115.--Front View of Curtiss OX-3 Aviation Motor, Showing Unconventional Valve Action by Concentric Push Rod and Pull Tube.]
Aviation Engines Part 18
You're reading novel Aviation Engines Part 18 online at LightNovelFree.com. You can use the follow function to bookmark your favorite novel ( Only for registered users ). If you find any errors ( broken links, can't load photos, etc.. ), Please let us know so we can fix it as soon as possible. And when you start a conversation or debate about a certain topic with other people, please do not offend them just because you don't like their opinions.
Aviation Engines Part 18 summary
You're reading Aviation Engines Part 18. This novel has been translated by Updating. Author: Victor Wilfred Page already has 709 views.
It's great if you read and follow any novel on our website. We promise you that we'll bring you the latest, hottest novel everyday and FREE.
LightNovelFree.com is a most smartest website for reading novel online, it can automatic resize images to fit your pc screen, even on your mobile. Experience now by using your smartphone and access to LightNovelFree.com
- Related chapter:
- Aviation Engines Part 17
- Aviation Engines Part 19
RECENTLY UPDATED NOVEL
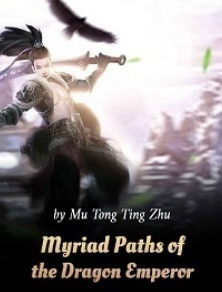
Myriad Paths of the Dragon Emperor
Myriad Paths of the Dragon Emperor Chapter 3091: Sinister intentions View : 1,659,780
The Grand Secretary's Pampered Wife
The Grand Secretary's Pampered Wife Chapter 763.1: Overbearing Robbery! View : 617,389
Madam's Identities Shocks The Entire City Again
Madam's Identities Shocks The Entire City Again Chapter 3489: A Sir Who Claims to Be From Continent M Is Looking For You View : 2,719,046