Textiles Part 2
You’re reading novel Textiles Part 2 online at LightNovelFree.com. Please use the follow button to get notification about the latest chapter next time when you visit LightNovelFree.com. Use F11 button to read novel in full-screen(PC only). Drop by anytime you want to read free – fast – latest novel. It’s great if you could leave a comment, share your opinion about the new chapters, new novel with others on the internet. We’ll do our best to bring you the finest, latest novel everyday. Enjoy!
=Grades of Wool.= In the grading of wool no set standard of quality exists. The same cla.s.sification may be applied in different years, or in different localities, to qualities of wool showing much variation, the best grade obtainable usually setting the standard for the lower grades. The highest quality of wool in the United States is found on full-blooded Merino sheep.
=Merino Wool.= The Merino sheep was bred for wool and not mutton. The fleece of this breed is fine, strong, elastic, and of good color; it also possesses a high felting power. Though naturally short, it is now grown to good length and the fleece is dense. The Merino sheep is a native of Spain, and Spain was for a long period the chief country of its production. It was also in past centuries extensively bred in England and English wool owes much to the Merino for the improvement it has effected in the fleeces of other breeds of English sheep. It was also introduced into Saxony and was highly bred there, and Saxony soon came to surpa.s.s Spanish wool in fineness, softness, and felting properties. The Merino was introduced into the United States at the beginning of the nineteenth century. By 1810, 5,000 Merino sheep had been imported and these 5,000 sheep formed the basis of most of the fine wool-producing flocks of our country to-day.
The terms half blood, three-eighths blood, and quarter blood refer to the full-blooded Merino standard. As the scale descends the wool becomes coa.r.s.er, the wool of a quarter blood usually being a comparatively coa.r.s.e fiber. The general cla.s.sifications of fine, medium, coa.r.s.e, and low, refer to the relative fineness of Merino combing wools. These distinctions naturally overlap according to the opinion of the parties in transactions. Picklock x.x.x and XX represent the highest grades of clothing wool, the grade next lower being X, and then Nos. 1 and 2. These again are used in connection with the locality from which the wool is grown, as Ohio XX, Michigan X, New York No. 1, etc.
=Difference Between Lamb's and Sheep's Wool.= One of the first points to be understood in wool sorting is the difference between the wool of lambs and one-year-old sheep, and that of sheep two or more years old.
Lamb's wool is naturally pointed at the end, because it has never been clipped. It is termed hog or hoggett wool, and is more valuable when longer, of about fourteen months' growth. It is finer in quality and possesses more waviness, which is a help in the process of spinning.
The wool of sheep two or more years old is known as wether. The ends of the fiber from such sheep are thick and blunted, on account of having been previously cut. It is necessary to be able to tell at once a hog fleece from a wether, and this can be done in two ways: by examining the ends of the fiber to see if they are pointed; or by pulling a staple out of the fleece. If it is wether, the staple will come out clean, without interfering to any extent with those around it; but if hog, some of the fibers will adhere to the one that is being pulled. Hog wool is generally more full of dirt, moss, straw, and other vegetable matter.
=Dead Wool= is wool obtained from the pelts of sheep that have died.
=Pulled Wool.= Pulled wool is wool from the pelts[10] as they come from the slaughter-houses of large packing plants. These pelts are thrown into vats of water and left to soak for twenty-four hours to loosen the dirt which has become matted into the wool. From these vats the pelts are taken to scrubbing machines from which the wool issues perfectly clean and white. The pelts are next freed from any particles of flesh or fat which may have adhered to them, and are then taken to the "painting" room. Here they are laid flesh side up and carefully painted with a preparation for loosening the roots of the wool. This preparation is allowed to remain on the pelts for twenty-four hours, when it is cleaned off and the pelts taken to the "pulling" room. Each wool puller stands before a small wooden framework over which the pelt is thrown, and the wool, being all thoroughly loosened by the "paint" preparation, is easily and quickly pulled out by the handful. As it is pulled it is thrown into barrels conveniently arranged according to grade and length.
When a barrel is filled, it is transferred to a large room across which are several rows of wire netting, raised about three feet from the floor. Each sheet of netting is about six feet wide. Here the wool is piled on the netting to a depth of several inches and hot air is forced underneath it by means of a blower. Meanwhile it is worked over by men with rakes, and soon dries. When thoroughly dry, it is raked up and taken to the storeroom, where it is dumped into bins. Here it usually remains open for inspection and sampling till it is sold, when it is bagged. The bags of wool ultimately find their way to the woolen mill or sampling house. Sometimes the fleece will retain its fleece form, but usually it breaks up. The wool contains lime and has to be specially treated by a scouring process to prevent lime from absorbing the cleansing substances used for scouring the wool.
=Delaine Wool= is a variety of fine, long combing wool.
=Cotty Wool=, or cotts, is wool from sheep that have been exposed to severe weather and lack of nourishment, and for these reasons have failed to throw off the yolk necessary to feed the wool. As a result it becomes matted or felted together, and is hard and brittle and almost worthless.
=Wool Sorter.= The sorter begins by placing the fleece upon his board or table, always arranging it so that he faces the north, as this gives the most constant light and no glare of the sun. The fleece thus spread out shows a definite dividing line through the center. The sorter parts the two halves and proceeds to a.n.a.lyze their different qualities. The number of sorts is determined by the requirements of the manufacturer who, in purchasing his wool, buys those grades that will produce the greatest bulk of the qualities for present use, and that leave in stock the smallest number of sorts and least weight for which he has no immediate use. The sorter then removes all extraneous matter adhering to the fleece, such as straw, twigs, and seeds, and cuts off the hard lumps of earth, tar, or paint, which, if not removed at this time, will dissolve in the scouring process and stain the wool. With these preliminaries finished, he proceeds to cast out the locks, according to quality, into baskets or skeps provided for that purpose. After skirting or taking off the outside edges of the fleece, usually known as brokes, and the legs and tail, known as breech, he separates the other portions from the better qualities.
[Ill.u.s.tration: SORTED WOOL IN PILES READY TO BE TRANSPORTED TO THE DEGREASING PLANT]
Picklock, prime, choice, super, head, downrights, seconds, breech, etc., are some of the terms used. Picklock comprises the choicest qualities; prime is similar to picklock, but slightly inferior; choice is true staple, but not as fine in fiber; super is similar to choice, but as a rule not as valuable; head includes the inferior sorts from this part of the sheep; downrights come from the lower parts of the sides; seconds consist of the best wool clipped from the throat and breast; breech, the short, coa.r.s.e fibers obtained from the skirting and edgings of the fleece.
In the worsted trade different names are used. The terms generally adopted are: blue, from the neck; fine, from the shoulders; neat, from the middle of the sides and back; brown-drawings, from the haunches; breech, from the tail and hind legs; cowtail, when the breech is very strong; brokes, from the lower part of the front legs and belly, which are cla.s.sed as super, middle, and common.
Fine, short wools are sorted according to the number of counts of yarn they are expected to spin, as 48's, 60's, 70's, and so on. Thus we see there are different methods of indicating qualities in different districts, and also of indicating differences of qualities between the woolen and worsted branches of the trade.
It may be noted that the quality of the wool varies in the same way as the quality of the flesh. The shoulder is finest in grain and most delicate, so the wool is finer in fiber. There is more wear and tear for the sheep at its haunches than at its shoulders, hence the wool is longer and stronger; about the neck the wool is short, to prevent the sheep from being weighted down while eating, etc.; the wool on the back becomes rough and thin, being most exposed to the rain. From the foregoing it will be readily seen that there is necessity for careful sorting, in order to insure obtaining an even running yarn, and subsequently a uniform quality of fabrics.
=Wool Was.h.i.+ng.= Fleece wool as it comes into the market is either in the "grease," that is, unwashed and with all the dirt which gathers on the surface of the greasy wool; or it is received as washed wool, the was.h.i.+ng being done as a preliminary step to the sheep shearing. Wool, unlike cotton, cannot be worked into yarn without being thoroughly cleansed of its impurities. These impurities consist of greasy and sweaty secretions, of the nature of a lubricant to the fiber. Combined with dirt, sand, etc., which adhere to the wool, these secretions form an encrusting compound, known as yolk, which acts as a natural preservative to the wool, keeping it soft and supple. This compound, with other extraneous matter, must be removed before the wool is in a workable condition. The amount of yolk varies, the greatest amount being found in fine, short wools from the warm climates. In long-staple wool the amount of yolk is comparatively small.
[Ill.u.s.tration: WAs.h.i.+NG ROOM]
Various methods of removing these impurities have been tried; one is the use of absorbent substances, such as fossil meal, alumina, etc., to withdraw the greasy matter, so that the remaining impurities can be easily removed by was.h.i.+ng. In other methods, naphtha or similar solvent liquids are used to dissolve the wool fats. This is followed by was.h.i.+ng in tepid water to dissolve the potash salts, leaving the dirt to fall away when the other substances are no longer present. To work this method with safety requires a costly and intricate plant with skilled supervision. The method which is practically in universal use is was.h.i.+ng the wool in alkaline solutions, properties of which combine with and reduce the impurities to a lathery emulsion which is easily washed off from the wool.
Great stress is laid upon the necessity of care in the was.h.i.+ng process, as the l.u.s.ter may be destroyed and a brownish-yellow tint given to the wool, the spinning properties very seriously injured, the softness destroyed, or the fiber dissolved. Some wools are easy to wash, requiring little soap and a reasonable temperature; other wools are cleansed with great difficulty. A note, therefore, should be made of any particular brand or cla.s.s of wool requiring special attention, to serve as a guide in the treatment of future lots. The danger lies in using unsuitable agents,--hard water, excessive temperatures, strong reagents, etc.
Caustic alkalies have a most destructive effect on wool as they eat into it and destroy its vitality. Carbonate alkalies are less severe.
Whatever cleansing substances are used, it is essential that they should be free from anything that is likely to injure the wool--that they remove the impurities and still preserve all the qualities in the wool. If the was.h.i.+ng is properly performed the alkaline portion of the yolk is removed, leaving only the colorless animal oil in the fiber.
If the work is not thoroughly done the wool pa.s.ses as "unmerchantable washed." "Tub washed" is the term applied to fleeces which are broken up and washed more or less by hand. Scoured wool is tub washed with warm water and soap, and then thoroughly rinsed in cold water until nothing remains but the clean fiber.
[Ill.u.s.tration: DEGREASING PLANT--REMOVING GREASE FROM WOOL]
An improved method of was.h.i.+ng wool by hand is to have a series of tanks with pressing rollers attached to each tank: the wool is agitated by means of forks, and then pa.s.sed to the pressing rollers and into each tank in succession. The tanks are usually five in number, and so arranged that the liquor can be run from the upper to the lower tank. Upon leaving the pressing rollers the excess of water is driven off in a hydro extractor[11] and the wool is beaten into a light, fluffy condition by means of a wooden fan or beater.
=Wool Drying.= The process of drying wool is not intended to be carried to such an extent that the wool will be in an absolutely dry state, for in such a condition it would be l.u.s.terless, brittle, and discolored. It is the nature of wool to retain a certain amount of moisture since it is hygroscopic, and to remove it entirely would result in partial disintegration of the fibers. Buyers and sellers have a recognized standard of moisture, 16 per cent. If, on the other hand, it is left too wet, the fibers will not stand the pulling strain in the succeeding operations, and if not broken, they are so unduly stretched that they have lost their elasticity.
The theory which underlies the drying process is that dry air is capable of absorbing moisture, hence by circulating currents of dry air in and around wet wool, the absorbing power of the air draws off the moisture. For continuous drying free circulation is a necessity, as otherwise the air would soon become saturated and incapable of taking up more moisture. Warming the air increases its capacity to absorb moisture; thus a higher temperature is capable of drying the wool much quicker than the same volume of air would at a low temperature. A free circulation of air at 75 to 100 degrees F., evenly distributed, and with ample provision for the escape of the saturated air, is essential for good work.
=Oiling.= After being scoured wool generally has to be oiled before it is ready for the processes of spinning, blending, etc. As delivered from the drying apparatus, the wool is bright and clean, but somewhat harsh and wiry to the touch, owing to the removal of the yolk which is its natural lubricant. To render it soft and elastic, and to improve its spinning qualities, the fiber is sprinkled with lard oil or olive oil. As the oil is a costly item, it is of consequence that it be equally distributed and used economically. To attain this end various forms of oiling apparatus have been invented, which sprinkle the oil in a fine spray over the wool, which is carried under the sprinkler by an endless cloth.
=Burring and Carbonizing.= After wool has been washed and scoured it frequently happens that it cannot be advanced to the succeeding operations of manufacture because it is mixed with burs, seeds, leaves, slivers, etc., which are picked up by the sheep in the pasture. These vegetable impurities injure the spinning qualities of the stock, for if a bur or other foreign substance becomes fastened in the strand of yarn while it is being spun, it either causes the thread to break or renders it bunchy and uneven. For removing burs, etc., from the wool two methods are pursued: the one purely mechanical, the other chemical, and known respectively as burring and carbonizing.
=Bur Picker.= For the mechanical removing of burs a machine called the bur picker is employed. In this machine the wool is first spread out into a thin lap or sheet; then light wooden blades, rotating rapidly, beat upon every part of the sheet and break the burs into pieces. The pieces fall down into the dust box or upon a grating beneath the machine, and are ejected together with a good deal of the wool adhering to them. Often the machine fails to beat out fine pieces and these are scattered through the stock.
=Process of Carbonizing.= For the complete removal of all foreign vegetable substances from wool the most effective process is carbonizing, in which the burs, etc., are burned out by means of acid and a high degree of heat. The method of procedure is as follows: The wool to be treated is immersed in a solution of sulphuric or hydrochloric acid for about twelve hours, the acid bath being placed in cement cisterns or in large lead-lined tubs and not made strong enough to injure the fiber of the wool. During the immersion the stock is frequently stirred. Next, the wool is dried and then placed in an enclosed chamber and subjected to a high temperature (75 degrees C.).
The result of this process is that all the vegetable matter contained in the wool is "carbonized" or burned to a crisp, and on being slightly beaten or shaken readily turns to dust. This dust is removed from the wool by various simple processes. The carbonizing process was first introduced in 1875, though it made but slight headway against the old burring method until after 1880.
=Blending.= Pure wool of but one quality is not often used in the production of woven fabrics, so, before the raw material is ready for spinning into yarn, or for other processes by which it is worked into useful forms, it is blended. Wools are blended for many reasons (among which cheapness figures prominently), the added materials consisting usually of shoddy, mungo, or extract fibers. Ordinarily, however, blending has for its object the securing of a desired quality or weight of cloth. The question of color, as well as quality, also determines blending operations, natural colored wools being frequently intermixed to obtain particular shades for dress goods, tweeds, knitting yarns, etc. Stock dyed wools are also blended for the production of mixed colors, as browns, grays, Oxfords, etc. There is practically no limit to the variety of shades and tints obtainable by mixing two or more colors of wool together. The various quant.i.ties of wool to be blended are spread out in due proportion in the form of thin layers, one on top of the other, and then pa.s.sed through a machine called the teaser. The teaser consists of a combination of large and small rollers, thickly studded with small pins, which open the wool, pull it apart, and thoroughly intermix it. A blast of air constantly plays upon the wool in the teaser and aids the spikes and pins in opening out the fibers. The material is subjected to this operation several times and is finally delivered in a soft, fleecy condition, ready to be spun into yarn.
FOOTNOTES:
[10] Skins.
[11] A wire cage enclosed in a metallic sh.e.l.l which revolves at a high speed causing sixty or seventy per cent of the moisture to be removed.
CHAPTER III
WOOL SUBSt.i.tUTES AND WASTE PRODUCTS
=Remanufactured= wool subst.i.tutes are extensively used in the manufacture of woolen and worsted goods. There is no need for the prejudice that is sometimes met regarding these reclaimed materials, for by their use millions of people are warmly and cheaply clothed. If the immense quant.i.ty of these materials were wasted, countless persons would be unable to afford proper clothing, as it is difficult to estimate what the price of wool would be; and it is also doubtful if a sufficient quant.i.ty could be produced to supply the need. In almost all instances the use of wool subst.i.tutes is for the special purpose of producing cloths at a much lower price.
The cloths made from waste products, such as noils, are not much inferior in quality to those produced from the wool from which the noils are obtained; but the great majority of cloths made from other waste products are much inferior. The following are the most important subst.i.tutes: noils, shoddy, mungo, extract-wool, and flocks.
=Noils= are the rejected fibers from the process of combing the different wools and hairs; thus, wool noils are from the sheep, mohair noils from the Angora goat, and alpaca noils from the Peruvian sheep.
Noils are divided into cla.s.ses, namely, long-wool noils, short or fine-wool noils, mohair noils, and alpaca noils. They are all obtained in the process of combing, that is, the process which separates the long from the short fibers; the former are known as the "top," and are used in worsted and in the production of mohair and alpaca yarns; while the latter are used to advantage in the production of many different kinds of woolen fabrics. With the exception of length, noils are practically of the same quality as the tops from which they are taken.
Long-wool noils are from the combings of such wools as Leicester and similar wools. These noils, like the wool from which they are obtained, are much coa.r.s.er in quality and fiber than the short-wool noils. Occasionally, when strength is required in the fabric, these noils are used, and they are also mixed with short-wool noils. Many of the cheviot fabrics are made exclusively of these noils. They are also mixed with shoddy and cotton in the production of dark-colored fabrics, and in medium and low-priced goods requiring a fibrous appearance they are extremely useful.
Short or fine-wool noils are the most valuable, and are obtained from combing Australian and other fine wools. The number and variety of uses to which they are put are innumerable. They are used to advantage in the plain and fancy woolen trade, in the manufacture of shawls and plain woolens of a soft nature, and are also suitable for mixing with cotton in the production of twist threads.
Mohair and alpaca noils are obtained by the combing of these materials. They are lacking in felting properties, but are l.u.s.trous and possess strength, and are most valuable in the manufacture of fabrics where strength and l.u.s.ter are required. These noils are used in the production of yarns for Kidderminster carpets, as yarns for these carpets must possess strength, brightness, and thickness of fiber. They are also used in combination with shoddy and cotton to produce weft or filling yarns for a lower quality of goods.
=Shoddy= and =Mungo= are in reality wool products, or wool fiber which has previously pa.s.sed through the processes of manufacture whereby its physical structure has been considerably mutilated. These were first produced about sixty years ago. Shoddy is higher in value than mungo.
The value and quality of the waste or rags from which it is made determine the quality or value of the material. Shoddy is derived from waste or rags of pure unmilled woolens, such as flannels, wraps, stockings, and all kinds of soft goods.
=Mungo= is made from rags of hard or milled character and is much shorter in fiber than shoddy. Its length, varying from one-quarter to three-quarters of an inch, can be regulated by the treatment the rags receive, and by the proper setting of the rollers in the grinding machine. Both shoddy and mungo may be divided into cla.s.ses. Mungo is divided into two cla.s.ses, namely, new and old mungo. New mungo is made from rags chiefly composed of tailor's clippings, unused pattern-room clippings, etc. Old mungo is made from cast-off garments, etc. By a careful selection of the rags previous to grinding, it is possible to make a large number of qualities, and a great variety of colors and shades without dyeing. Owing to their cheapness shoddy and mungo are used in cloths of low and medium qualities. Shoddies are utilized in fabrics of the cheviot cla.s.s and in the production of backing yarns.
Mungoes of the best quality are used in the low fancy tweed trade, in both warp and weft, but chiefly in union and backed fabrics.
=Method of Producing Shoddy and Mungo.= Before the fibrous mungo is obtained, the rags have to pa.s.s through the following necessary preliminary operations:
Textiles Part 2
You're reading novel Textiles Part 2 online at LightNovelFree.com. You can use the follow function to bookmark your favorite novel ( Only for registered users ). If you find any errors ( broken links, can't load photos, etc.. ), Please let us know so we can fix it as soon as possible. And when you start a conversation or debate about a certain topic with other people, please do not offend them just because you don't like their opinions.
Textiles Part 2 summary
You're reading Textiles Part 2. This novel has been translated by Updating. Author: William H. Dooley already has 660 views.
It's great if you read and follow any novel on our website. We promise you that we'll bring you the latest, hottest novel everyday and FREE.
LightNovelFree.com is a most smartest website for reading novel online, it can automatic resize images to fit your pc screen, even on your mobile. Experience now by using your smartphone and access to LightNovelFree.com
- Related chapter:
- Textiles Part 1
- Textiles Part 3
RECENTLY UPDATED NOVEL
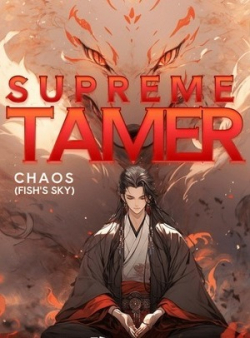
Supreme Tamer
Supreme Tamer Chapter 758: Chapter 628: Welcoming the Battle with Leopard Tribe Village (Part 2) View : 315,665
The Yun Family's Ninth Child Is An Imp!
The Yun Family's Ninth Child Is An Imp! Chapter 6374: what did it do wrong View : 2,263,863
Complete Martial Arts Attributes
Complete Martial Arts Attributes Chapter 2987: Nine Worlds Mixed Space Array! Teleportation! Space Annihilation! (2) View : 2,935,208
I Have A City In An Alternate World
I Have A City In An Alternate World Chapter 3867: The rabbit devoured the Tiger (1) View : 1,282,758
Raising My Children With My Personal Spatial Ability
Raising My Children With My Personal Spatial Ability Chapter 1843 Finally Came Back to See Mother View : 1,280,802
Maximum Comprehension: Taking Care of Swords In A Sword Pavilion
Maximum Comprehension: Taking Care of Swords In A Sword Pavilion Chapter 2247: 1003, the Sky-Treading Divine Beasts clan View : 864,439
Pampered Consort Of The Fragrant Orchard
Pampered Consort Of The Fragrant Orchard Chapter 111.5: A Family Outside the City (5) View : 560,178
Madam's Identities Shocks The Entire City Again
Madam's Identities Shocks The Entire City Again Chapter 3496: Only Sister Nian Can Have Master Wang Cook View : 2,726,006