Textiles Part 3
You’re reading novel Textiles Part 3 online at LightNovelFree.com. Please use the follow button to get notification about the latest chapter next time when you visit LightNovelFree.com. Use F11 button to read novel in full-screen(PC only). Drop by anytime you want to read free – fast – latest novel. It’s great if you could leave a comment, share your opinion about the new chapters, new novel with others on the internet. We’ll do our best to bring you the finest, latest novel everyday. Enjoy!
_A. Dusting._ This is carried on in a shaking machine, which consists of a cylinder possessing long and strong spikes, which are enclosed, having underneath a grating to allow the dust to pa.s.s through. The dust is then driven by a fan into a receptacle provided for that purpose.
_B. Sorting._ All rags, both old and new, must be sorted, and considerable care must be exercised in this operation, as on this work alone depends the obtaining of different qualities and shades, as well as the securing of the production of a regular and uniform product.
_C. Seaming._ This is only necessary with the rags procured from garments. It is simply removing the cotton threads from the seams, and any metallic or hard substances from the rags.
_D. Oiling._ The rags are oiled to soften them and make them more pliable, and thus to facilitate the grinding.
_E. Grinding._ This is the princ.i.p.al operation, and the rags are made fibrous in this process. The machine by which this is effected is made up of the following parts: feed ap.r.o.n, fluted rollers, swift, and a funnel for conveying the material out of the machine. The princ.i.p.al features of the machine are the swift and its speed. The swift is enclosed in a framework, and is about forty-two inches in diameter and eighteen inches wide, thus possessing a surface area of 2,376 square inches, containing from 12,000 to 14,000 fine strong iron spikes. The speed of the swift may be from 600 to 800 revolutions per minute. The rags are fed by placing them on the traveling feed ap.r.o.n, and are thus conveyed to the fluted rollers. As they emerge from the rollers they are presented to the swift, and by strong iron teeth, moving with exceedingly high surface velocity, they are torn thread from thread and fiber from fiber. The fluted rollers run very slowly, and the rags are held while the swift carries out this operation. By means of the strong current of air created by the high speed of the swift, the mungo is expelled from the machine through the funnel into a specially arranged receptacle. If by any chance the machine should be overcharged, that is, if too many rags are pa.s.sing through the rollers, the top fluted roller is raised up, and the rags are simply carried, or thrown by the swift, over into a box on the opposite side of the machine without being subjected to the tearing process. The top roller is weighted by levers with weights attached to keep it in position, thus bringing downward pressure to bear upon it, as it is driven simply by friction. By the adjustment of the feed rollers in relation to the swift, the length of the fiber may be varied to a small degree.
=Extract Wool.= This is obtained from union cloths, that is, from cloths having a wool weft and warp of cotton, etc., also from cloths having the same material for warp, but possessing a woolen or mungo warp or filling, etc. It is the wool fiber that is required. Therefore the vegetable matter (cotton) must be extracted from it by the process of carbonizing. To effect this, the tissue or rags are steeped in a solution of sulphuric acid and water and then subjected to heat in an enclosed room. The water is evaporated, leaving the acid in a concentrated form, which acts upon the cotton, converting it into powder. The powder readily becomes separated, and thus the cotton is eliminated. The material that is left is well washed to remove all acid, dried, and then pa.s.sed through a miniature carder, to impart to it the appearance of a woolly and a softer fabric.
=Flocks.= These are of three kinds, and are waste products of the milling, cropping, and raising operations. The most valuable are those derived from the fulling mill, being clean and of a bright color. They are chiefly used by sail spinners, and in the manufacture of low grade cloths of a cheviot cla.s.s. White flocks are suitable for blending with wool, and as a rule command a fair price. Raising flocks are those obtained from the dressing or raising gigs, and are applied to purposes similar to those for which fulling flocks are used. Cutting or cropping flocks are the short fibers which are removed from the cloths in this operation. They are practically of no value to the textile manufacturer, being unfit for yarn production, but are used chiefly by wall-paper manufacturers in producing "flock-papers," which are papers with raised figures resembling cloth, made of poor wool, and attached with a gluey varnish.
[Ill.u.s.tration: CARD ROOM
1. Automatic Feed.
2. Bur Guards.
3. Bur Tray.
4. 1st Top Divider.
5. 2d Top Divider.
6. Workers.
7. Strippers.
8. Doffer Cylinder.
9. Main Cylinders.
10. Main Card Drive on 2d Main Cylinder Shaft.
11. 1st Lickerin.
12. 2d Lickerin.
13. 3d Lickerin.
14. 4th Lickerin.
15. Fancy Hood.]
CHAPTER IV
WORSTED YARNS
=Carding.= After the wool is washed it undergoes a number of operations before it is finished into worsted or woolen yarn.[12] The first step in the manufacturing of worsted yarn is to pa.s.s the washed wool through a worsted card which consists of a number of cylinders covered with fine wire teeth mounted on a frame. The effect of these cylinders on the wool is to disengage the wool fibers, make them straight, and form a "sliver" or strand. It is now ready for the combing machine.
=Combing.= The process of combing consists of subjecting the card sliver to the operations of the automatic wool comber, which straightens the fibers and removes all short and tufted pieces of wool. Combing is a guarantee that every fiber of the wool lies perfectly straight, and that all fibers follow one after the other in regular order.
=Comb.= A comb is a complicated machine. The princ.i.p.al feature is a large metal ring with rows of fine steel pins (pin circles), which is made to revolve horizontally within the machine. By various devices the wool is fed into the teeth of the ring in the form of tufts. The fibers of the tufts by an intricate process are separated into long and short lengths, and a set of rollers draws each out separately and winds it into a continuous strand called "tops." On leaving the comber, the wool is free from short fibers, specks, and foreign substances, and presents a fine, flowing, and l.u.s.trous appearance. The short combed-out wool is called noils, and is used in making carpet yarns, ground up into shoddy stock, or utilized in spinning fancy yarns.
=Worsted Tops.= American textile manufacturers are finding it advantageous to have their combing done by those who make the work a specialty rather than to do it themselves. In the manufacture of tops all varieties of combing wools are used: Australian, Merino, and Crossbred wools, South American Merino and Crossbred wools, Cape Merino wools, Merino and Crossbred wools grown in the United States, the l.u.s.trous wools of pure English blood, Mohair from Asiatic Turkey, and Alpaca from the Andes. Tops are sold to worsted spinneries.[13]
Many mills or worsted spinneries send their wools, either sorted or unsorted as they may desire, to a combing mill, where the wool is put into top at a lower price than that at which most spinneries can do their own combing. By means of the naphtha process a larger amount of top from a given amount of wool can be secured than by any other process, and in addition, a top in better condition for drawing and spinning.
[Ill.u.s.tration: COMB ROOM
1. Driving pulley on horizontal shaft (2).
3. Boxes containing bevel gears.
4. Pillars.
5. Driving pulley for dabbing motion.
6. Boxes containing dabbing-brush mechanism.
7. Dabbing brushes.
8. Star or stroker wheels.
9. Large circle containing rows of pins.
10. Drawing-off ap.r.o.n and rollers for large circle.
11. Bra.s.s boxes or conductors.
12. Guides for comb ball ends.
13. Comb b.a.l.l.s (4 ends each).
14. Fluted wooden rollers on which comb b.a.l.l.s rest.
15. Comb leg (4 in number).
16. Foundation plate.]
In a strand of combed wool, called top, no single fiber lies across the strand; all lie in the direction of the length. This order is preserved until the fibers have been converted into yarn, which is accomplished by pa.s.sing through "gill boxes." These gill boxes are machines with bars of iron having upon their surface two rows of minute steel pins, by this means kept perfectly straight. The bars on which they are placed are worked on screws between two sets of rollers. The wool enters between the first set of rollers, and, as it pa.s.ses through, is caught by one of these gills that is raised up for the purpose, being succeeded by others as the rollers revolve. These gills are moved forward on screws in the direction of the other set of rollers, and the pins in the gills always keep the fiber perfectly straight. The second set of rollers is termed the draught rollers, since by them the wool, after pa.s.sing through the front rollers, is drawn out and reduced in thickness. This is accomplished because the second rollers revolve at a higher rate of speed than the first rollers, the speed being regulated according to the length of the wool, and the thickness of the yarn to be produced. These gills are used in the production of worsted yarn until the size of the rope of wool has been so reduced and twisted that there is no chance of any fiber getting crossed or out of the order of straightness. A worsted yarn is, consequently, a straight yarn, or a yarn produced from perfectly straight fibers.
[Ill.u.s.tration: GILLING
1. Cans containing Comb Ends or Sliver.
2. Balling Head.
3. Stock from Balling Head No. 2.
4. Screws for applying pressure to Back Rollers.
5. Screws for applying pressure to Front Rollers.
6. Faller Screws situated between No. 4 and No. 5.
7. Guard for covering gears which drive Back Rollers.
8. Guard covering gears which drive Balling Head.
9. Balling Head.]
The combing of wool may be dispensed with in some cases, although such a yarn is not in common use. When combing is dispensed with, the gills, in connection with the draught of the rollers, make the fibers straight, and produce a worsted yarn, although such a yarn has a tendency to be uneven and knotty.
Before the wool can be spun it must be made into roving of a suitable thickness. This is done by pa.s.sing it, after being combed, through a series of operations termed drawing, whose functions are to produce a gradual reduction in thickness at each stage. Although the number of machines varies according to the kind of wool to be treated, still the same principle applies to all.
=Spinning.= The process of spinning is the last in the formation of yarn or thread, the subsequent operations having for their object the strengthening of the yarn by combining two or more strands and afterward arranging them for weaving or for the purpose for which the yarn is required. It is also the last time that the fibers are mechanically drawn over each other or drafted, and this is invariably done from a single roving. The humidity and temperature of the spinning room must be adjusted to conditions. Each spinner is provided with a wet and dry thermometer so that the best temperature can be ascertained. The most suitable heat and humidity can only be obtained by comparison and observation. A dry and warm atmosphere causes the wool to become charged with electricity and then the fibers repel each other.
[Ill.u.s.tration: WORSTED SPINNING. "BRADFORD SYSTEM"
1. Bobbins containing Worsted Yarn.
2. Conical shape caps placed on top of spindles.
3. Tin Wings fastened to Eyeboard.
4. Eyeboard containing pot eyes, through which yarn pa.s.ses to the bobbin.
5. Scratch fluted front rollers.
6. Leather covered Pressing Rollers for No. 5 Rollers.
7. Smooth metal Pressing Rollers for Back Rollers.
8. Large Front Roller Gear.
9. Pulley for driving Twist gear.
10. Spools of Roving held by a series of pegs.
Textiles Part 3
You're reading novel Textiles Part 3 online at LightNovelFree.com. You can use the follow function to bookmark your favorite novel ( Only for registered users ). If you find any errors ( broken links, can't load photos, etc.. ), Please let us know so we can fix it as soon as possible. And when you start a conversation or debate about a certain topic with other people, please do not offend them just because you don't like their opinions.
Textiles Part 3 summary
You're reading Textiles Part 3. This novel has been translated by Updating. Author: William H. Dooley already has 680 views.
It's great if you read and follow any novel on our website. We promise you that we'll bring you the latest, hottest novel everyday and FREE.
LightNovelFree.com is a most smartest website for reading novel online, it can automatic resize images to fit your pc screen, even on your mobile. Experience now by using your smartphone and access to LightNovelFree.com
- Related chapter:
- Textiles Part 2
- Textiles Part 4
RECENTLY UPDATED NOVEL
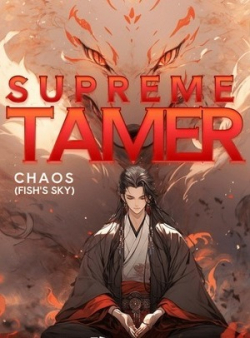
Supreme Tamer
Supreme Tamer Chapter 758: Chapter 628: Welcoming the Battle with Leopard Tribe Village (Part 2) View : 315,546
The Yun Family's Ninth Child Is An Imp!
The Yun Family's Ninth Child Is An Imp! Chapter 6374: what did it do wrong View : 2,263,805
Complete Martial Arts Attributes
Complete Martial Arts Attributes Chapter 2987: Nine Worlds Mixed Space Array! Teleportation! Space Annihilation! (2) View : 2,935,168
I Have A City In An Alternate World
I Have A City In An Alternate World Chapter 3867: The rabbit devoured the Tiger (1) View : 1,282,710
Raising My Children With My Personal Spatial Ability
Raising My Children With My Personal Spatial Ability Chapter 1843 Finally Came Back to See Mother View : 1,280,768
Maximum Comprehension: Taking Care of Swords In A Sword Pavilion
Maximum Comprehension: Taking Care of Swords In A Sword Pavilion Chapter 2247: 1003, the Sky-Treading Divine Beasts clan View : 864,421
Pampered Consort Of The Fragrant Orchard
Pampered Consort Of The Fragrant Orchard Chapter 111.5: A Family Outside the City (5) View : 560,174
Madam's Identities Shocks The Entire City Again
Madam's Identities Shocks The Entire City Again Chapter 3496: Only Sister Nian Can Have Master Wang Cook View : 2,725,979